Boeing 777-236ER
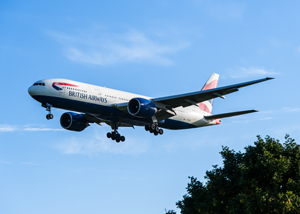
Photo copyright Jason Wood - used with permission
British Airways Flight 38, G-YMMM
London, England
January 17, 2008
On January 17, 2008, a British Airways 777-236ER equipped with Rolls Royce RB211 Trent 800 engines, landed short of runway 27L at Heathrow International Airport. The airplane was operating as Flight 38 from Beijing to London with 136 passengers and 16 crew members on board. The airplane impacted the ground short of the runway, skidded in the grassy area and came to rest at the end of the runway. This resulted in substantial structural damage but there was no fire. The airplane was successfully evacuated with one passenger receiving serious injuries, and all others only minor injuries.
Analysis of the Flight Data Recorder and the Quick Access Recorder data showed that there were no anomalies until final approach. As the airplane approached the runway, recorded data showed a thrust increase commanded by the autothrottles. The engines initially responded, but at an altitude of 720 feet, right engine thrust dropped below the commanded thrust. Approximately 7 seconds later left engine thrust also dropped below the commanded thrust. Both engines continued to produce thrust, at an engine speed above flight idle, but less than the commanded thrust, and lower than the thrust necessary to reach the runway.
The British Air Accidents Investigation Board (AAIB) determined that the most likely cause of the accident was a fuel flow restriction on both engines, resulting in a significant thrust loss during final approach. The fuel flow restriction was concluded to have been the result of an accumulation of ice in the fuel system which released in a short time period, collected on, and restricted fuel flow through the Fuel-Oil Heat Exchanger. The associated thrust loss resulted in a reduction in airplane performance, and a deterioration in the flight path such that landing on the runway was not possible.
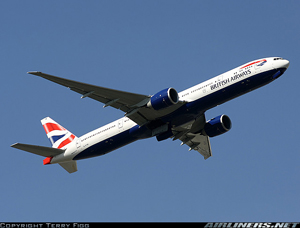
History of Flight
British Airways flight 38 was a scheduled return flight from Beijing, China to London Heathrow, and departed on 0209 on January 17th, 2008. At Beijing, the aircraft was fueled with 71,401 kg of Jet A-1, at a temperature of 5 degrees Celsius (C), 30 minutes before engine start. The total fuel load at the start of the flight was 79,000 kg and the temperature recorded in the left main tank was -2 degrees C. The flight crew obtained an initial cruise altitude of 10,600 m (flight level (FL) 348) with estimated temperatures at altitude of approximately -65C, which was expected to result in a total air temperature (TAT) of -37C. The flight crew was informed of the potential to encounter extreme cold temperatures near the border of China and Mongolia, and as a result the crew briefed that they would monitor the fuel temperature. The concern was that the fuel would cool below its freeze point and prevent fuel from being pumped to the engines. Once enroute, the minimum fuel temperature encountered was -34C. The fuel had not, at any time during the flight, cooled to a temperature at which it would form fuel wax or gel. An article printed in the Boeing Airliner Magazine on polar operations explains the operational concerns associated with operations in regions where extremely low temperatures may be encountered during cruise flight: (Polar Route Operations).
After exiting the enroute region of extreme cold temperatures, the flight crew initiated step climbs to FL400 using the Vertical Speed (VS) mode of the auto flight system. Investigators established that until approach at Heathrow, due to the relatively low passenger load, and therefore low airplane weight, low thrust settings, and associated low fuel flows were used throughout the flight. Once on approach, with the airplane reconfigured (flaps down) for approach, the higher drag and need to maintain a specific flight path required higher fuel flows. Due to cold soaking at altitude, fuel temperatures remained low, which was later shown by the investigation to be a major contributing factor in the accident.
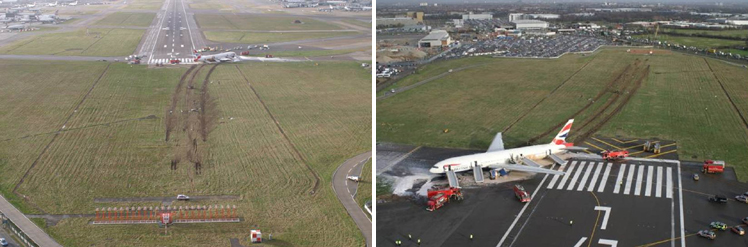
During the final approach to LHR, the first officer was the pilot flying, and took control of the aircraft at 800 feet, planning to disconnect the autopilot at 600 feet for a manual landing. Shortly after taking control of the aircraft the autothrottles commanded an increase in thrust from both engines. The engines initially responded but, 57 seconds before touchdown, thrust on the right engine reduced, and 7 seconds later thrust on the left engine reduced. The engines did not shut down and continued to produce thrust above flight idle, but less than the commanded thrust. Due to the thrust loss, and pilot attempts to extend the deteriorating flight path to the runway, airspeed decayed to 115 knots, and an "airspeed low" warning was annunciated along with a master caution aural warning. The airspeed stabilized for a short period, and in an attempt to reduce drag the captain, who was the pilot monitoring, retracted the flaps from 30 degrees to 25 degrees. Airspeed continued to decrease, and at 200 feet had deteriorated to 108 knots. Ten seconds before touchdown the stick shaker activated, indicating that the aircraft was nearing a stall. In response, the pilot flying pushed the control column forward, which resulted in autopilot disconnect and a reduction in pitch. The aircraft struck the ground approximately 330 meters short of the paved surface of Runway 27L. During the approach, surface temperature at Heathrow was 10C, and the fuel temperature at the time of the thrust reduction was -22C.
Investigators concluded that the most likely cause of the accident was an accumulation, and subsequent release of a large quantity of ice that had formed within the fuel system. This accumulated ice released, probably as a result of the demand for increased fuel flows, and collected on the face of the fuel oil heat exchanger (FOHE). The accumulation of ice on the FOHE face caused the uncommanded reduction in fuel flow, and resultant thrust loss, deterioration in the flight path, and touchdown short of the runway. Fuel system laboratory testing conducted after the accident led investigators to conclude that the many hours spent at low fuel flows and cold fuel temperatures contributed to larger than normal amounts of ice accumulation in the fuel feed system. High fuel flows, such as those typically encountered during an approach can flush the accumulated ice, resulting in an "avalanche" of slush and snow traveling through the fuel feed system. This "avalanche" is what collected on the face of the FOHE, restricting the fuel flow, and causing the loss of thrust.
Airplane and Engine Fuel System
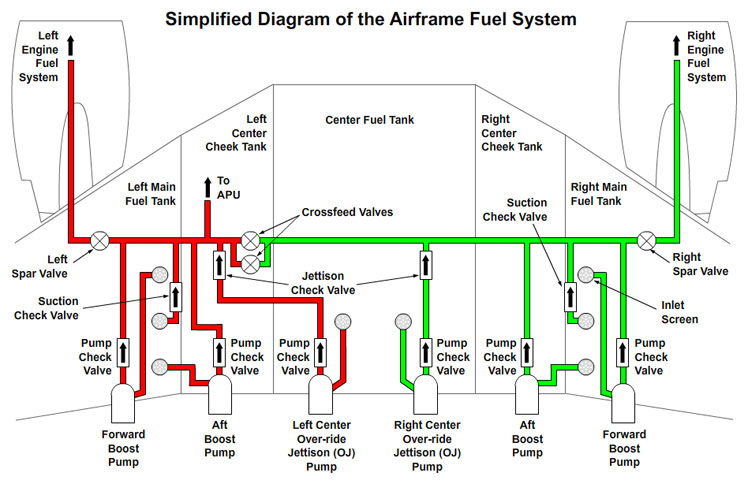
The Boeing 777 series airplane stores fuel in three fuel tanks, a center tank, a left main tank and a right main tank. Each fuel tank contains two fuel boost pumps that have inlets equipped with a ¼ inch mesh screen intended to provide protection for the pump inlet. A check valve fitted in the discharge port prevents fuel in the fuel feed manifold flowing back through the pump. A pressure switch mounted between the pump impeller and the check valve, monitors fuel pressure and triggers an advisory warning on the flight deck if the pressure rise across the pump drops below threshold pressure.
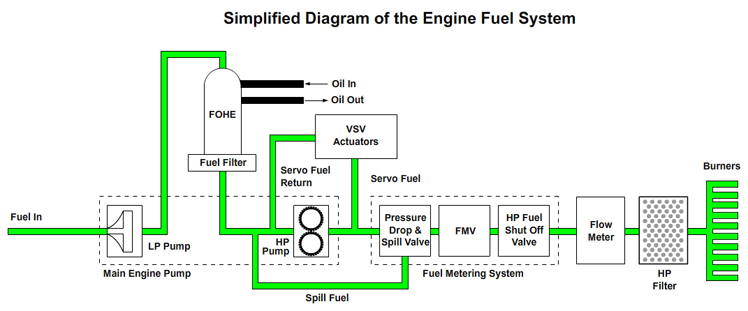
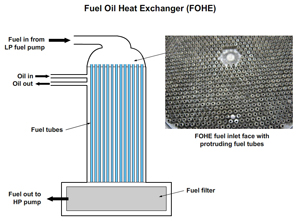
View Larger
Each fuel tank is equipped with a water scavenge system that is intended to prevent water from settling on the bottom of the fuel tanks. A jet pump, operated by motive flow from the boost pumps, draws fluid from the lowest section of each tank and injects it close to the inlet of a boost pump.
The airframe fuel system supplies fuel to the Low Pressure (LP) engine-driven pump, which forms part of the main engine fuel pump. When fuel flows through the LP pump, fuel pressure is increased (and fuel temperature, slightly). Fuel is then pumped through a Fuel/Oil Heat Exchanger (FOHE). The FOHE serves the dual purpose of cooling the engine oil, and raising the temperature of the fuel so that ice does not affect the downstream components, including the LP filter and the Fuel Metering Unit (FMU). The FOHE is a cross-flow/counter-flow design that includes a matrix of fine tubes. The fuel enters the top of the FOHE and passes through the tubes. Hot oil enters the FOHE main body and passes around the fuel tubes.
Turbine Fuel/Water Properties
Aviation turbine fuel is composed of a mixture of different hydrocarbon molecules. Depending on the hydrocarbon mix, properties such as specific heat and freezing point can vary between batches of fuel. Aviation turbine fuel is manufactured at the refinery to a specification that defines 30 properties that the fuel must meet. Fuel is manufactured to exceed the specifications, so it is typical that the freezing point may be lower than the -47C (for Jet A-1) freezing point specification. Fuel on board G-YMMM was tested and had a -57C freeze point.
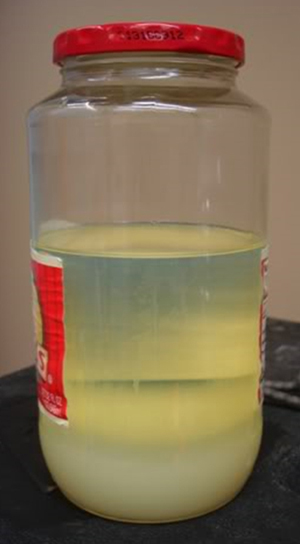
Fuel freezing point is the temperature at which wax crystals form in the fuel as it is cooled, and completely disappear when warmed. This should not be confused with the fuel becoming cloudy upon cooling, which is typically a result of the freezing of entrained water.
Water is normally present in aviation fuel and aircraft fuel systems. When fuel temperatures approach 0C, "entrained" water will freeze and form ice crystals which will turn the fuel cloudy. Water can also be introduced during refueling, or through the fuel tank vent system when descending in humid air.
Water in turbine fuel can take 3 forms:
1. Dissolved Water
Water molecules attach to the fuel hydrocarbons and can be compared to humidity. As fuel cools, the dissolved water is released and takes the form of either entrained or free water. This form of water will not result in ice since it is chemically bonded to the fuel as part of the molecule.
2. Entrained (Suspended) Water
Water suspended in fuel as droplets, and may be visible to the naked eye in concentrations below 30 ppm. At higher concentrations, entrained water will appear cloudy. As a general rule, under static conditions, entrained water will settle at a rate of about one foot per hour, however is unlikely that on an in-service aircraft all of the entrained water will settle out.
Entrained water in fuel will freeze and form snow-like ice crystals at fuel temperatures between -1C and -3 C and will turn the fuel cloudy. The formed ice flakes travel through the fuel system and begin to stick to their surroundings, and each other, at temperatures between -5C and -20C which is considered the "sticky range" defined in Society of Automotive Engineers (SAE) Aerospace Recommended Practice (ARP) 1401.
Cold fuel laboratory testing conducted by the investigation, and using high concentrations of water and ice entrained in the fuel, demonstrated that a slushy ice formed within the fuel feed system pipes.
3. Free water
Water which is neither dissolved nor entrained, and has a higher density than fuel. Free water takes the form of droplets or puddles at the low point in the fuel tank. The aircraft water scavenge system as well as the sump drain are designed to remove this water.
Airplane Fuel System Ice Accumulation
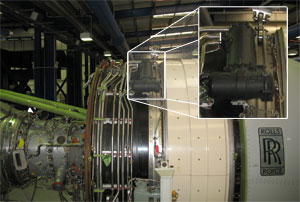
View Larger
Fuel samples were taken from the accident airplane, which showed no evidence of excessive water or other contaminants. Fuel samples taken from the accident aircraft were tested and shown to have a freeze point of -57C. This testing further confirmed to investigators that extreme cold fuel temperatures were not a factor in the fuel system restriction.
Based on the temperatures during refueling, investigators estimated that 3.0 liters of dissolved water (40 ppm) were uploaded onto the airplane, and a maximum of 2 liters (30 ppm) of entrained water. Additionally, it is estimated that as much as .14 liters of water could have been drawn through the fuel tank vent system enroute to Heathrow. These quantities were considered normal for aviation turbine fuel.
Based on evaluation of the flight data recorder and fuel system hardware, investigators concluded that ice accumulated in the airplane fuel system (fuel lines, piping) over a long period of operation at low fuel flows and low fuel temperatures. After a commanded fuel flow increase on approach, the ice released from the insides of pipes and tubes, causing an “avalanche” effect, resulting in a restriction at the fuel-oil heat exchanger (FOHE).
An animation of the blockage mechanism is available below:
The investigation concluded, based on the following evidence that the fuel flow reduction had been the result of an ice flushing event:
- The fuel metering valve showed that both engines experienced restrictions in the fuel delivery system.
- The left and right high pressure (HP) pumps had signs of fresh cavitation, indicating that the restriction was upstream of these pumps.
- The aircraft boost pumps had no low-pressure indications.
- The spar (fuel shutoff) valves were fully opened throughout the flight and there was no indication of uncommanded movement.
- The flight data recorder showed that the fuel flow restrictions on both engines occurred seconds after a commanded fuel flow increase.
- Laboratory testing duplicated the scenario, showing that the increase in fuel flow flushes the accumulated ice and creates an “avalanche” effect in the fuel feed system.
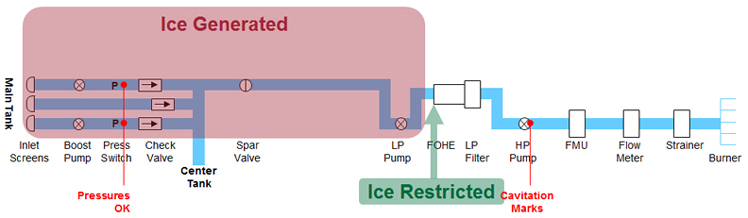
A video of the “avalanche” affect, recorded during post accident testing conducted at Boeing is available below:
Investigative findings confirmed that fuel flow was restricted at the FOHE and resulted from the release of accumulated ice in the airplane fuel feed system. Post-accident laboratory testing demonstrated that restrictions occurred at the inlet to the FOHE.
Fuel/Water/Ice Laboratory Testing
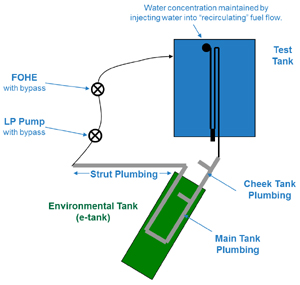
View Larger
As part of the investigation, a fuel icing test rig was constructed to simulate the 777-fuel feed system. Laboratory testing showed that ice forms in fuel feed lines with normal concentrations of dissolved and entrained water present. The testing was performed to establish how much ice accumulates in the fuel feed system over long periods of time. The test conditions represented long range flights operating in the critical temperature ranges. The fuel contained water concentrations at levels intended to simulate the most critical condition for fuel system icing.
During the laboratory testing, observations were made of the formation and mobility of ice produced by a number of different methods. It appeared that ice would more readily stick to other ice crystals and surrounding surfaces when the fuel temperature range was between -5- and -20-degrees C. Below -20C, ice crystals appeared to have a more crystalline appearance and did not readily adhere to their surroundings or other ice crystals.
Testing results revealed:
- Ice forms in the fuel feed system when fuel temperatures are between -5C and -20C, and when warm fuel (5C) flows through cold pipes.
- Ice does not form at fuel temperatures of -35C or below.
- The accumulated ice is typically soft and mobile.
- Increasing fuel flow can cause accumulated ice to release.
- Ice generation and accumulation in fuel systems is often random.
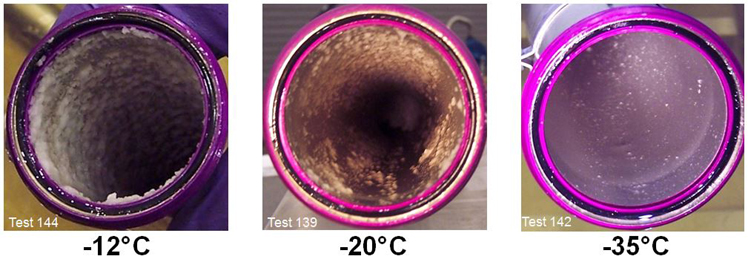
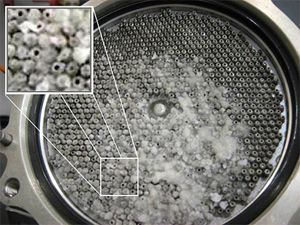
Fuel Oil Heat Exchanger Testing
Laboratory testing conducted by the investigation also demonstrated that at fuel temperatures below -15C, using as little as 50 ml water at high concentrations, an “avalanche” type event can result in a fuel flow restriction at the FOHE.
The FOHE matrix consists of over 1000 small tubes that are crimped at various locations along their length to improve thermal transfer efficiency. The crimp at the inlet of the tubes is a slightly smaller diameter than the remainder of the crimps to prevent small debris from becoming lodged in the matrix. The tubes protrude approximately 4 mm from the matrix top plate, which separates the fuel from the oil, and extends into the fuel inlet chamber. Laboratory testing determined that eliminating the protrusions from the tubes increased the FOHE's capability to withstand an avalanche of snow at fuel temperatures as low as -44C. The testing demonstrated that the FOHE with flush tubes could withstand high concentrations of slushy ice, eliminating the potential for a fuel flow restriction.
The FAA published AD 2010-07-01 which required replacement of the Fuel Oil heat exchanger (FOHE) on the Rolls-Royce RB211- Trent 500, 700, Trent 800 and Trent 900 Series Turbofan Engines.
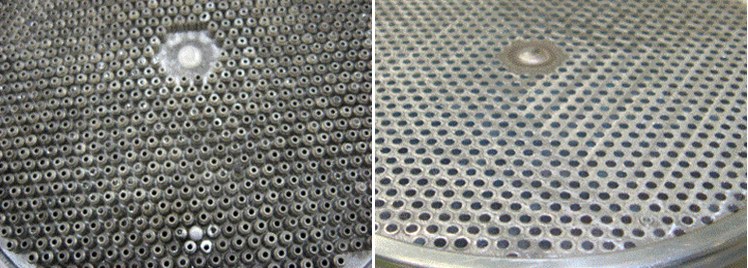
The AAIB issued 115 findings, covering the conduct of the flight, evacuation and survivability, crashworthiness, restriction to fuel flow, engine and fuel system testing, engine rollback, and other subjects.
The probable cause of the accident was a fuel flow restriction, resulting in a significant thrust loss during final approach. The fuel flow restriction was concluded to have been the result of an accumulation of ice in the fuel system which released in a short time period, which collected on, and restricted fuel flow through the Fuel-Oil Heat Exchanger. The associated thrust loss resulted in a reduction in airplane performance, and a deterioration in the flight path such that landing on the runway was not possible.
The complete text of the findings, including the probable cause, is available at the following link: (AAIB Findings).
The complete accident report is available at the following link: (AAIB Accident Report).
The AAIB issued 20 recommendations in total. One was issued a month after the accident, 8 were issued in interim reports, and the remainder were issued with the final accident report.
Early Recommendation (Issued February 18, 2008)
2008-009: Was a recommendation relative to the proper shutdown of engines using the CUTOFF switches in coordination with the engine fire handles.
Recommendations made in Interim Report published on September 15, 2008
2008-047: Recommended the introduction of interim measures to reduce the risks associated with ice formation in fuel feed systems.
2008-048: Recommended immediate action to consider the implications of the published AAIB findings on other airframe/engine combinations.
2008-049: Recommended a review of certification requirements to ensure that fuel systems are tolerant to potential ice buildup and sudden release in fuel feed systems.
Recommendations made in Interim Report 2, published on March 12, 2009
2009-028: Recommended a design review of engine and aircraft fuel systems and development of changes to prevent ice from causing a fuel flow restriction at the FOHE.
2009-029: Recommendation to airworthiness authorities to mandate design changes resulting from recommendations 2009-028.
2009-030: Recommended a study to consider the expanded use of fuel anti-ice additives.
2009-031: Recommended research into ice formation in aviation turbine fuels.
2009-032: Recommended research into ice accumulation and subsequent release within aircraft and engine fuel systems.
Recommendations made in Final Accident Report
2009-091 and 092: Recommended that EASA and the FAA introduce requirements to record the operational position of each fuel metering device on digital flight data recorders.
2009-093 through 2009-100: Included various recommendations relative to the crashworthiness of the airplane, and various cabin safety aspects in survivable accidents. These recommendations did not directly address the determined accident cause but recommended improvements relative to survivable accidents.
The complete text of the recommendations is available at the following link: (AAIB Recommendations)
The History of Fuel System Icing
Fuel system icing has been a concern since the 1950s and significant amounts of research have been accomplished. Early research showed ice from dissolved water can form in aviation turbine fuel and block filters and small orifices. Early research, which was confirmed by this investigation, determined that ice formation is dependent on a number of factors including the rate of cooling, water droplet size, and the agitation of fuel. Variation in fuel composition between batches of fuel affects the concentration and size of water droplets and amount of subsequent icing.
Two documents produced by the Society of Automotive Engineers (SAE), AIR 790, originated in 1964, and Aerospace Recommended Practice (ARP) 1401 discuss the phenomenon. Research from the 1950s identified the problem of ice formation from dissolved water in fuel systems but did not identify the scenario of accumulated ice release and subsequent restriction to fuel flow.
Fuel heaters were utilized on the first generation of jet aircraft to prevent fuel filter icing. Manufactures later developed a fuel oil heat exchanger to prevent icing of the engine’s critical components. It is common for large turbofan engines to incorporate fuel oil heat exchangers to automatically control fuel temperature.
- FOHE design feature that collected ice and led to a fuel flow restriction when ice was shed within the system.
- Fuel system design features would prevent formation of ice in quantities that could adversely affect engine operation.
On February 11, 1958, a Boeing B-52D crashed in South Dakota due to fuel icing. During a go around, engines 1, 2, and 5 experienced an uncommanded reduction in engine power. During the subsequent approach, power was gradually lost from all the engines when full thrust was commanded. The aircraft struck the ground 3500 feet short of the runway fatally injuring three of the crew. In spite of a significant post-crash fire, ice was discovered within the fuel system.
A subsequent inquiry attributed the engine power loss to icing of the engine fuel pump screens, causing a restricted fuel flow to the engines. Excess water/ice in the fuel tanks and no bypass on the fuel pump screen were listed as contributing factors.
Redesign of FOHE
A feature of the original FOHE design was fuel tubes that projected approximately 4 millimeters beyond the face of the FOHE. The investigation discovered that these tube extensions led to an inefficient heat exchange at the FOHE face, allowing ice to accumulate. This ice accumulation could lead to fuel flow restrictions at times of high fuel flow demand, and adversely affect flight safety. To correct this problem, the FOHE was redesigned to eliminate the tube extensions, making the fuel tubes flush with the FOHE face. Testing of this redesigned feature demonstrated its effectiveness at temperatures much lower than are expected to be encountered in flight.
Interim Actions
AD 2008-19-04
This AD mandated Approved Flight Manual (AFM) limitations to clear ice buildup in the fuel feed system and provide flight crew procedures to restore commanded thrust in the event of a fuel flow restriction resulting from ice blockage at the inlet to the FOHE.
This AD superseded AD 2008-19-04 to include the knowledge gained from a November 2008 Delta Airlines fuel icing event. This AD also included a restatement of the requirements of AD 2008-19-04.
Terminating Action
This AD required operators to remove and replace the fuel oil heat exchangers with a redesigned version. Since incorporation of the redesigned FOHE, no further events have occurred in the 777/Rolls-Royce Fleet.
Airplane Life Cycle:
- Design / Manufacturing
Accident Threat Categories:
- Lack of System Isolation / Segregation
Groupings:
- N/A
Accident Common Themes:
- Flawed Assumptions
- Unintended Effects
Flawed Assumptions
Prior to this accident, it was widely believed that fuel system icing, and its effects, would manifest themselves at temperatures at or near the freezing point of the fuel. Regulatory requirements focused on a reasonable level of water contamination in the fuel but assumed that critical effects would occur at the coldest fuel temperatures. This accident revealed a previously unknown critical condition, identified as the "sticky range", associated with fuel temperatures between -5C and -20C. In this range, turbine fuel, containing normal amounts of water, will form a soft form of ice and accumulate on internal surfaces of fuel tubing. Cruise conditions typically utilize lower throttle setting and fuel flows than takeoff or landing, and also tend to dwell at power settings, accommodating the formation of ice during cruise. On this accident, normal throttle usage on final approach required a fuel flow increase, causing a "flushing" of accumulated ice, and clogged the face of the FOHE.
Delta Airlines Boeing 777-200ER
On November 26, 2008, Delta Airlines 777-200ER N862DA experienced a single engine thrust rollback during cruise at 39,000 feet. The flight crew reduced engine power to idle (per AD mandated flight manual procedures) which caused ice blocking the face of the FOHE to melt. The flight crew was able to restore the commanded thrust, and the flight continued uneventfully. Data collected from this event were incorporated into FAA AD 2009-05-11.
Airbus Industrie A330
A330 aircraft equipped with Rolls-Royce Trent 700 engines experienced two separate thrust rollback events that were a result ice buildup on the inlet of the FOHE face, resulting in a fuel flow restriction.
Technical Related Lessons
Operation with turbine engine fuel containing normal amounts of entrained water results in ice accretion inside airplane fuel system tubing during long range flights. In order to maintain propulsion system separation and isolation requirements, the airplane and engine fuel feed systems must be capable of continued operation following release of accumulated ice from fuel feed system internal surfaces. (Threat Category: System Isolation/Segregation)
- This accident revealed that fuel temperatures in ranges above the fuel freezing point, and with concentrations of water that are normally expected to be encountered can lead to fuel system ice that can severely restrict fuel flow. On approach, having flown nearly 14 hours, engine thrust modulations typical of this phase of flight caused ice that had accumulated in the fuel feed lines to break free, and clog the FOHE face, resulting in a fuel flow restriction, and prevented the engines from producing normal thrust. This restriction was of sufficient duration that the airplane could not maintain flight and impacted just short of the approach end of the runway.
Common Theme Related Lessons
Turbine fuel temperatures in the range of -5C to -20C represent the "sticky range" where ice can accumulate in fuel tubing and will lead to flushing and potential fuel system restrictions. (Common Theme: Flawed Assumptions)
- Historical assumptions about turbine fuel icing, and regulatory requirements assumed that critical operating conditions occurred when the fuel was near its freezing point. This accident revealed that there is a fuel temperature range (the so-called sticky range), which is above the freezing point of the fuel, and can have severe consequences, up to and including blockage of fuel flow. This particular icing phenomenon can occur with water concentrations that are considered "normal" for turbine fuels and can be expected to be encountered whenever fuel temperature is inside the sticky range.