McDonnell Douglas DC-10-10
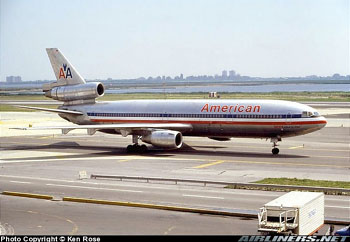
Photo Copyright Ken Rose - used with permission
American Airlines Flight 191, N110AA
Chicago, Illinois
May 25, 1979
During takeoff rotation, the left engine and strut assembly separated from the wing, and traveled over the wing, severing hydraulic lines in the associated area of the wing. Damage to the hydraulic lines caused a loss of hydraulic pressure and subsequent retraction of the outboard leading edge slats on the left wing. The flight crew reacted to the engine separation as if it were an engine failure, and they followed procedures consistent with that type of event. In decelerating to the procedurally required V2 speed, the left wing stalled, as the prescribed speed was below the stall speed of the reconfigured wing. The resulting lift asymmetry caused an uncontrollable left roll and loss of control of the airplane. The airplane crashed inverted, killing all 271 passengers and crew. The National Transportation Safety Board (NTSB) determined that the probable cause of the accident was the asymmetric stall and ensuing roll following the uncommanded retraction of the left wing outboard leading edge-slats.
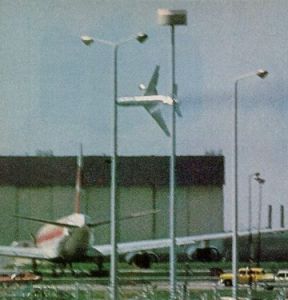
History of Flight
American Airlines Flight 191, a DC-10, experienced a number 1 (left wing) engine/strut failure, and subsequent engine and strut separation, on takeoff from Chicago, O'Hare Airport on May 25, 1979. During rotation, the left engine and strut assembly, and about three feet of wing leading edge, separated from the wing as a single unit, went over the top of the wing, and fell to the runway. The takeoff continued, the pilots assuming that they had experienced an engine failure, unaware that the left engine and pylon assembly had separated and fallen off the airplane. Compounding the developing problems, the pylon separation also severed hydraulic lines, causing a loss of associated hydraulic pressure and retraction of all slats outboard of the left engine.
The separation of the left engine also caused the loss of electrical power provided by that engine's electrical generator. This resulted in the loss of many aircraft systems and instruments, including the captain's flight instruments, the left stall warning computer, the stickshaker (stall warning) motor, number 1 engine instruments, the slat disagree warning system, and parts of the flight control indicating system.
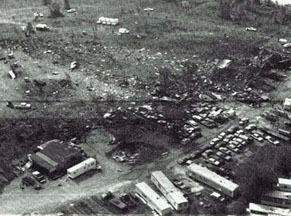
The airplane climbed to approximately 300 feet with wings level, then began to turn and roll left, with bank angle increasing to approximately 90 degrees. During the roll, the nose also pitched down, and the airplane began to descend. The airplane continued to roll (112 degrees of roll at impact) and crashed in a trailer park near the airport. All 271 passengers and flight crew and two persons on the ground were killed. Additionally, two persons on the ground received serious injuries.
Flight Path
Approximately one second prior to liftoff, the left engine and strut assembly separated from the airplane. The airplane had accelerated through the engine-out climb speed, V2, a speed normally achieved at approximately 35 feet above the ground, while still on the ground, and lifted off at V2 + 6 knots. The airplane lifted off slightly left wing down, and was corrected back to wings-level flight via appropriate flight control inputs. The airplane continued to climb wings level, and about nine seconds after liftoff, the airplane had accelerated to 172 knots and reached 140 feet of altitude. As the climb continued, the airplane began to decelerate at a rate of about one knot per second, and at 20 seconds after liftoff, and an altitude of 325 feet, airspeed had been reduced to 159 knots. At this point, the airplane began to roll to the left, countered by rudder and aileron inputs. The airplane continued to roll until impact, 31 seconds after liftoff, and in a 112-degree left roll, and 21-degree nose down pitch attitude.
Click on this link to view an aerial photograph of O'Hare Airport and surrounding areas. The crash site is in the upper right portion of the photograph, between the green area north of the runway and the fuel tank farm at upper center.
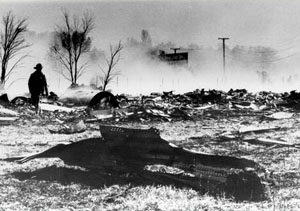
The NTSB concluded that the airplane was being flown in accordance with American Airline's engine failure procedures. Immediately after liftoff, a pitch attitude of 14 degrees was attained and maintained, indicating use of the flight director for pitch guidance. It was also subsequently determined that the captain's flight director was inoperative, implying that the first officer was flying the takeoff. American Airlines procedures required that, following an engine failure, the airplane should be accelerated to V2, and climbed to 800 feet at that speed. No differences in the procedure were specified if an engine failure occurred after reaching V2, and in fact, the specific scenario was not addressed by the airline's procedures. Following the accident, American Airlines modified this procedure to either maintain the speed at the time of engine failure, if between V2 and V2 + 10, and to maintain not less than V2 + 10 if the failure occurred after reaching V2 + 10. The revised procedure also instructed crews to disregard the flight director pitch command (which provided guidance to achieve V2) and to maintain at least V2+10.
It was clear to the NTSB that the airplane was being decelerated from 172 knots toward V2 in an attempt to follow the engine-out climb procedure (and reacquire V2) when the left wing stalled at 159 knots. The stall resulted in the left roll and ensuing loss of control.
As the engine/pylon assembly separated from the airplane, four hydraulic lines in the vicinity of the engine pylon were severed, resulting in the loss of hydraulic pressure to the slat actuators outboard of the engine location. This loss of pressure allowed several left wing leading edge slats to retract. The hydraulic actuators did not include an alternate locking system to prevent inadvertent slat retraction in the event of hydraulic system pressure loss. The slat system was designed such that when the slats achieve the commanded position, the hydraulic system provides a "lock" that uses hydraulic pressure to maintain slat position. (view diagram of the slat actuation system) When the engine/pylon assembly separated from the wing, hydraulic fluid was pumped through the broken lines, draining the system and depleting the hydraulic locking pressure. Upon loss of this pressure, aerodynamic loads caused the retraction of the slats on the outboard portion of the left wing. With the slats retracted, the stall speed for the wing is higher than with slats extended. View Animation of the engine separation sequence during the takeoff roll and see an illustration of the effects of slat retraction on the wing's ability to generate lift and the crew's capability to control the airplane.
Strut Failure and Associated Maintenance Procedures
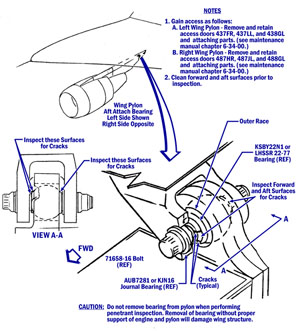
View Larger
Strut failure was determined to have been caused by unintended structural damage which occurred during engine/pylon reinstallation using a forklift. The engine/pylon removal and reinstallation were being conducted to implement two DC-10 Service Bulletins, one of which called for replacement of the aft attach spherical bearings on engines 1 and 3 (McDonnell Douglas Service Bulletin 54-48), and the other called for lubrication/replacement of the forward attach monoball bearings for engines 1 and 3 (McDonnell Douglas Service Bulletin 54-59).
Service Bulletin 54-48 superseded but did not cancel an earlier Service Bulletin (54-45), which required inspection/replacement of the aft attach bearing. Both Service Bulletins 54-48 and 54-59 required that the pylons be removed, and recommended that this be accomplished with the engines removed. The Service Bulletin instructions assumed that engines and pylons would be removed separately, and did not provide instructions to remove the engine and pylon as a unit. Additionally, removal of the engines and pylons as a unit was not an approved Maintenance Manual procedure.
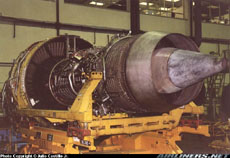
Photo Copyright Julio Castillo - used with permission
The DC-10 engine strut and pylon access doors are illustrated below. This figure identifies the inspection panels and access points. If inspection per the service bulletin(s) revealed damaged parts, then removal of the engine and pylon was necessary.
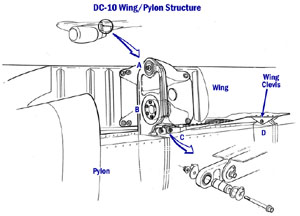
View Larger
For removal of the engine and pylon, the illustrated attachment points would be successively accessed and detached per maintenance manual instructions, first removing the engine and then the pylon.
The Maintenance Manual did not provide instructions for removal of the engine and pylon as an integral unit. To facilitate the time required for bearing replacement, American Airlines developed a procedure using a forklift to remove, support, and replace the engine/pylon assembly.
The airline's engine change procedure removed the engine and pylon as a unit. A forklift with an attached engine stand was used to support the engine while the forward and rear pylon/wing attachments were removed. American Airlines developed the forklift procedure for removing the engine without concurrence from McDonnell Douglas. The airline had evaluated and validated portions of the procedure, but the NTSB concluded that the procedure had not been sufficiently evaluated, and appropriate consideration had not been given to the potential for inducing damage.
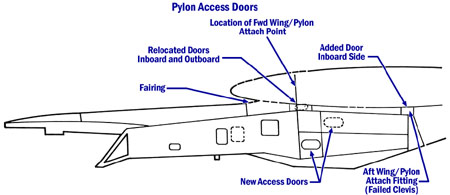
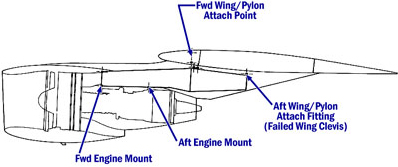
The lack of precision associated with the use of the forklift, essentially an inability to perform the fine manipulations necessary to accomplish reinstallation of the engine/strut assembly, in combination with the tight clearances between the pylon flange and the wing clevis resulted in damage to the same part that had just been inspected. View animation illustrating how the damage to aft pylon attach fitting occurred.
Shown is an illustration of the pylon/wing attachments. In American Airlines' procedure, the forward and aft fittings were the only fittings that were detached in order to separate the engine and pylon from the wing as a unit. The failure, which allowed the engine and pylon to separate from the wing and cause the accident, occurred at the aft attachment point, the pylon aft bulkhead.
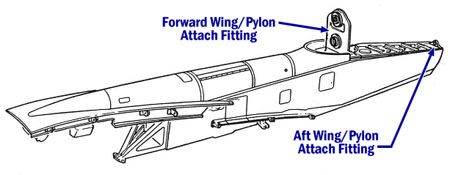
A detailed cutaway view of the pylon attachment structure illustrates the complexity of the surrounding area and relative difficulty in inspecting and/or working in the area without removing the pylon from the wing.
During reinstallation of the engine/pylon assembly, replacement of the forward pylon/wing fitting bolt (prior to replacement of the aft fitting) allowed the engine/pylon assembly to pivot around the forward pylon bulkhead fitting. This rotation of the engine/pylon assembly around the forward fitting resulted in rear mount contact with the wing clevis. The forces imparted by this contact resulted in cracking of the pylon aft bulkhead and the subsequent failure of the fitting during a takeoff.
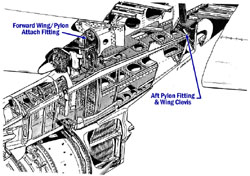
View Larger
Inspections of other DC-10 pylon mounts following the accident resulted in nine additional cracked mounts being identified. As a result, citing the possibility that the DC-10 "...may not meet the requirements of Section 603(a) of the Federal Aviation Act for a Type Certificate..." FAA Administrator Bond revoked the DC-10 type certificate for 37 days while the investigation proceeded.
The NTSB was highly critical of the FAA's lack of involvement in overseeing and approving important maintenance tasks such as engine change procedures. As a result of this accident, Type Certification Processes now formally address certain "vital" maintenance tasks. Prior to this, aircraft certification and maintenance were treated as separate, somewhat unrelated issues.
During the investigation, Aviation Week & Space Technology published a series of articles concerning various aspects of this accident and the early investigation. These articles can be viewed by clicking on the titles:
- Crash to Boost FAA Scrutiny, AW&ST, June 4, 1979, Page 12
- DC-10 type Certificate Lifted, AW&ST, June 11, 1979, Page 47
- Pylon Related Bulletins Issued Earlier, AW&ST June 11, 1979, Page 57
- FAA Probe Turns to DC-10 Slat System, AW&ST July 9, 1979, Page 30
Accident Memorial

Photo copyright Jason Rice – used with permission
In October 2011, a memorial was dedicated to the passengers and crew of Flight 191. The memorial is near the crash site, and consists of a decorative garden, bordered by a brick wall. The bricks in the wall are engraved with the names of persons who perished in the accident.
The NTSB determined that the probable cause of this accident was "...the asymmetrical stall and the ensuing roll of the aircraft because of the uncommanded retraction of the left wing outboard leading-edge slats and the loss of stall warning and slat disagreement indication systems." This resulted from maintenance-induced damage leading to the separation of the number 1 engine and pylon assembly at a critical point during takeoff. The separation resulted from damage by improper maintenance procedures, which led to failure of the pylon structure.
The NTSB issued 23 findings regarding this accident. The findings dealt variously with the:
- Separation of the engine pylon from the wing
- Loss of electrical and hydraulic power to flight controls
- Flight crew procedures
- Performance of improper maintenance procedures
- Lack of redundancy in the stall warning system
- Lack of mechanical locks in the high lift system
Select this link to view the detailed NTSB findings. Select this link to view the entire NTSB report.
The NTSB issued 11 recommendations. The subject areas covered include:
- Issuing Airworthiness Directives (AD) to inspect all DC-10 aircraft for engine pylon damage
- Issuing alert maintenance bulletins to discontinue improper maintenance techniques
- Changing type certification procedures to consider factors that affect maintainability, and to address possibilities of multiple failures that can result from damage to a primary structure through which essential systems are routed
- Ensuring that the design of transport category airplanes protects against asymmetry of high-lift devices
- Initiating strict manufacturer quality control programs and service difficulty and service information collection
- Instructions for Maintenance Review Boards
- Instructions for air carrier maintenance facilities and designated repair stations
- Proposed revision to 14 CFR 121.707 to more clearly define major and minor repair categories
- Instructions for revisions of operational procedures and instrumentation to increase stall margin during secondary emergencies
Select here to view the detailed NTSB recommendations.
The following Federal Aviation Regulations were pertinent to the DC-10 design and certification:
14 CFR 25.207 - Stall Warning
14 CFR 25.571 - Fatigue Evaluation of Flight Structure
14 CFR 25.671 - Control Systems - General
14 CFR 25.675 - Control Systems - Stops
14 CFR 25.685 - Control System Details
14 CFR 25.689 - Cable Systems
14 CFR 25.701 - Flap Interconnection
14 CFR 25.1309 - Equipment Systems and Installations
14 CFR 25.1435 - Hydraulic Systems
14 CFR 25.1529 - Maintenance Manual
The following Air Carrier Operations regulations were pertinent:
14 CFR 121.379 - Authority to Perform and Approve Maintenance, Preventive Maintenance, and Alterations
14 CFR 121.703 - Service Difficulty Reports
14 CFR 121.707 - Alteration and Repair Reports
The following reporting requirement is also relevant:
14 CFR 21.3 - Reporting of Failures, Malfunctions, and Defects
Airlines and manufacturers have historically communicated with each other regarding operational and/or maintenance difficulties. Manufacturer's service bulletins are a typical method of notifying air carriers of a need to perform specific maintenance in order to maintain the integrity of a design (usually detailing inspection processes), or to improve certain aspects of the design (periodic maintenance tasks, etc.) Further, these service bulletins may provide specific instructions for the service bulletin task or inspection or provide references to manufacturer documents where the instructions may be found. The manufacturer generally creates the service bulletins and associated task instructions based on the manufacturer's knowledge of the design, the manufacturer's knowledge of best practices to accomplish a specific task, and a means by which to accomplish the task in the least invasive but still safest (from a design integrity standpoint) methods. The manufacturer may also make assumptions about how the task would be accomplished by a carrier, and designs accomplishment instructions based on those assumptions.
In the case of the inspections associated with the two DC-10 service bulletins, McDonnell-Douglas referred to the DC-10 Maintenance Manual, which provided specific instructions for removing and replacing the wing-mounted engines and pylons. The maintenance manual instructed that engine and pylon removal be conducted as two separate activities, and McDonnell-Douglas assumed, when creating the service bulletins, that the engine and pylon would not be removed as a single unit.
American Airlines was authorized by the FAA to perform their own maintenance, including development and approval of maintenance processes. In an effort to accomplish the inspections required by the referenced McDonnell-Douglas service bulletins in a more time-efficient manner, American Airlines developed a procedure which removed the engine and pylon as a single unit. In contrast to the DC-9, a smaller McDonnell-Douglas aircraft, an engine change took approximately four hours. On the DC-10, an engine change required approximately 24 hours. The cost associated with any work involving an engine removal and reinstallation therefore cost the airline more time and money and kept the subject airplane out of service for a significantly longer period. This airline therefore felt a time pressure to be as efficient as possible in performing engine removals and reinstallations, and the elimination of the maintenance procedures associated with separate removal of the engine and pylon would have provided a significant time savings. American Airlines performed an evaluation of the proposed procedure and determined that it could be accomplished efficiently and safely. The factor that was not sufficiently addressed was the intricate and precise movements of the forklift that were required to maneuver the engine/pylon assembly into position for reinstallation and the subsequent inability to thoroughly inspect the attachment fittings following the reinstallation. The damage caused during the reinstallation process was not discovered, and consequently allowed the inflight failure of the pylon, and separation from the wing.
Three key safety issues were identified:
- There was structural damage to the wing/pylon aft attachment resulting from the use of a forklift during the maintenance procedure.
- The flight crew had no means to determine that the left wing had stalled. With the loss of the left engine and its associated electrical power generation, electrical power to the left outboard slat position sensor, the stick shaker motor, the slat disagree warning light system, and the left stall warning computer was lost. Even though there were two (left and right) stall warning systems, there was no crossover information between the two systems to provide appropriate (slats retracted) stall warning information to the flight crew. Loss of the single stick shaker motor would have prevented warning, even with the existence of crossover information.
- The leading-edge device hydraulic actuators did not have an alternate means to lock the slats in place in the event of loss of hydraulic pressure to the system, which allowed the slats to retract.
- It was assumed that a forklift was safe to use in removing/reinstalling the pylon and engine. American Airlines thought they had developed a procedure employing a forklift to lower the engine and pylon as a unit that would be safe and efficient. In retrospect, it produced an unforeseen, difficult to detect problem that damaged the airplane and led directly to the crash.
- McDonnell-Douglas incorrectly assumed that the leading-edge slats would always retract symmetrically. They may also have assumed that a full leading-edge asymmetry was always controllable. They didn't address what would happen if a wing stalled due to the asymmetry, and they were not required to examine the effect of an asymmetry in the takeoff region of the flight envelope.
- It was assumed that slat asymmetry due to loss of hydraulics would not occur. McDonnell-Douglas thought they had provided sufficient system isolation to preclude loss of all hydraulic systems, and thereby prevent slat retraction. They did not foresee loss of hydraulics to the leading-edge slats as the result of an engine/pylon separation. The slat system was reliant on the retention of hydraulic pressure to maintain slat position. There was no alternate locking system to prevent retraction of the slats on loss of hydraulics to the slat system.
- V2 assumes that only the thrust from a single engine is lost. The weight of the engine, and the wing's ability to generate lift, will be unaffected.
Continental Airlines, in implementing service bulletin related maintenance, had independently developed a procedure similar to that employed by American Airlines. In two prior instances on Continental DC-10 airplanes in December 1978 and February 1979, engine/pylon assembly reinstallation had resulted in damage nearly identical to that incurred on the accident airplane. In both events at Continental, the sound of the flange fracturing was heard by maintenance personnel. Both Continental events were attributed to maintenance error by the carrier and were not reported to McDonnell Douglas or the FAA. The NTSB concluded that these two events should have been viewed as an indication that the alternate installation procedure was inappropriate.
Unclear guidance concerning proper techniques for changing engines or executing certain critical maintenance tasks, and a lack of regulatory oversight led to the revision of 14 CFR 25.1529, Instructions for Continued Airworthiness, and companion requirements in 14 CFR parts 23, 27, and 29.
The actual requirements of 14 CFR 25.1529 are contained in 14 CFR Part 25 Appendix H.
Additionally, 14 CFR 43.16 and 14 CFR 91.403(c) were amended by Amendments 43-20 and 91-267 as companion requirements to the part 25 requirements.
The DC-10 Type Certificate was suspended via an Emergency Order, signed by FAA Administrator Langhorne Bond, and issued on June 6, 1979. The type certificate was reinstated on July 13, 1979, after an assessment of the airplane certification process.
The following airworthiness directives (ADs) were issued as a result of this accident:
- AD 79-15-04 R1 required, prior to further flight, inspection of leading-edge slat drive components, and reporting of any discrepancies to the FAA.
- AD 79-15-05 required, prior to further flight, installation of two auto-throttle/speed control computers to provide stall warning based on both right and left angle of attack sensors and wing slat positions, and to modify the stall warning system to provide the required sensor information. Further, it required a new Flight Manual limitation relative to the slat function of the takeoff warning system and its operability for takeoff.
- AD 79-18-08 required, prior to further flight, inspection for and replacement of cracked barrel nuts in the aft engine mounts.
- AD 79-20-01 R1 required, prior to further flight, inspection, and if necessary, replacement of the four main aft mount pylon bulkhead bolts.
- AD 80-03-10 required, within 210 days of the effective date of the AD, installation of two auto-throttle/speed control computers, each of which receives information from the positions of both outboard wing slat groups, in addition to other previously required inputs, and installation of a stick shaker at the first officer's position, in addition to that previously required at the captain's position, with both stick shakers actuated by either auto-throttle/speed control computer.
- AD 80-11-05 R1 required removal and reinstallation of the engine and pylon separately, and required certain inspections, prior to further flight, following reinstallation of the pylon.
Airplane Life Cycle:
- Design / Manufacturing
- Maintenance / Repair / Alteration
Accident Threat Categories:
- Structural Failure
- Lack of System Isolation / Segregation
- Flight Deck Layout / Avionics Confusion
Groupings:
- Loss of Control
- Automation
Accident Common Themes:
- Organizational Lapses
- Human Error
- Flawed Assumptions
- Pre-existing Failures
- Unintended Effects
Organizational Lapses
Prior to the failure at American Airlines, Continental Airlines had developed a similar procedure for removal of the engine and pylon as a unit, in order to conduct the inspections required by the McDonnell-Douglas service bulletin. Twice, during service bulletin-related maintenance, Continental caused failures in the aft bulkhead, but discovered them prior to completion of the procedure. The failures were successfully repaired, and Continental attributed the failures to maintenance errors. As a result, they did not inform McDonnell-Douglas, or the FAA, and information was not disseminated outside Continental Airlines. Had the disposition and reporting process been more robust, American Airlines could possibly have learned of the failures at Continental and taken measures to prevent similar failures on their own DC-10 fleet.
Human Error
As stated by the NTSB in the official accident report, "A minor mistake by the forklift operator while adjusting the load could easily damage the aft bulkhead and its upper flange." ".... maintenance personnel had to be extremely cautious while they detached and attached the pylon." A seemingly minor error could result in the pylon attach fittings impacting the wing attachment structure and could cause damage to the pylon aft bulkhead sufficient to cause the failure of the fitting, and separation of the engine/pylon when subjected to flight loads.
Flawed Assumptions
Airplane Design - McDonnell-Douglas, designed the DC-10 leading edge slat system to be hydraulically locked when extended, and did not provide a mechanical means to lock the system in the extended position. It was assumed that sufficient hydraulic isolation had been provided to prevent the asymmetric retraction of the leading-edge slats.
Airplane Maintenance - American Airlines assumed that it would be safe to employ a forklift in conducting service bulletin-related maintenance, and that it was safe to remove the engine and pylon as a single unit, contrary to maintenance manual procedures. Damage to the just-inspected structure was the primary cause of the accident.
Preexisting Failures
This accident was a direct result of a failure that occurred and was undiscovered during maintenance. The preexisting failure of the wing/pylon attachment structure led to the separation of the engine and pylon during a takeoff.
Unintended Effects
The McDonnell-Douglas service bulletins were intended to improve the safety of the fleet. American Airlines developed a service bulletin related maintenance procedure in order to reduce the time associated with removing and inspecting the engine pylon attachment structure. The procedure resulted in damage to, and the ultimate failure of, the part that had just been inspected. The ultimate result was to negate the safety improvement intended by the service bulletins, and actually reduce the safety of the DC-10 fleet.
China Airlines 747-200F, December 29, 1991
Ten minutes after takeoff from Taipei, Taiwan, at an altitude of 5,000 feet, the number 3 engine strut failed, causing separation of the number 3 engine, which subsequently struck and caused the separation of the number 4 engine. A loss of roll control resulted, and the airplane crashed in the Taiwan Strait.
El-Al 747-200F, October 4, 1992
Following departure from Schipol Airport in Amsterdam, The Netherlands, at an altitude of 6,000 feet, the number 3 engine separated and struck engine number 4, which subsequently separated. During an attempted to return to the airport, roll control was lost and the airplane crashed into an apartment complex.
See accident module
Technical Related Lessons:
Engine separation can result in catastrophic damage. (Threat Category: Lack of System Isolation/Segregation and Structural Failure)
- Especially inflight, an engine separation is a highly uncontrolled event, and the engine trajectory following separation can be somewhat random, based on a number of factors (e.g., thrust at time of separation, nature of failure, aircraft normal load factor, residual structural strength and failure progressions, etc). Some manufacturers have designed for limited engine mount fuse capability for specific on-ground events such as high landing loads, but it is not intended that engine separations occur in flight. In this accident, the separation of the engine and pylon resulted in collateral damage to the hydraulic systems routed through the leading edge of the wing. While hydraulic redundancy existed for extension and retraction of the leading-edge slats, the design did not consider the loss of all hydraulics to the outboard leading-edge slats, or the resulting asymmetry and its effect on flight characteristics.
Designs for safety critical components or systems should consider all foreseeable failure modes and strive to design such that when these failures do occur, they result in a safe configuration. (Threat Category: Lack of System Isolation/Segregation)
- Loss of the hydraulic system associated with the actuation of the outboard leading-edge slats on the left wing allowed the retraction of the slats, and development of a lift asymmetry that became uncontrollable. The design of the leading-edge system did not consider the loss of a single hydraulic system leading to an asymmetric leading-edge configuration. What proved to be the vulnerability of this design was its inability to accommodate a single failure (loss of hydraulic pressure to the leading-edge slats on one wing) during a critical phase of flight. Following the accident, the alleviation to this single failure vulnerability was a redesign to require hydraulic pressure to drive the leading-edge slats in either the extend or retract direction.
Airplane warning/alerting systems should be designed with sufficient redundancy that failure of a component will not result in an unsafe condition or configuration. (Threat Category: Flight Deck Layout/Avionics Confusion)
- The loss of the Number 1 engine, and its associated electrical generator, resulted in the failure of a number of safety and warning systems, including the stick shaker, and slat asymmetry indication system, as well as many of the captain's instruments. With the loss of these safety indicating systems, the flight crew was unaware that a leading-edge asymmetry had occurred and had no means to determine that the left wing had stalled.
Common Theme Related Lessons:
Accident precursor recognition and timely intervention are dependent upon both a knowledgeable safety management workforce and effective information sharing throughout the industry. (Common theme: Organizational Lapses)
- Prior to the failure during reassembly at American Airlines, Continental Airlines had experienced similar failures while using a forklift engine/strut change procedure to comply with the same service bulletins. Had this information been shared with either the manufacturer, or with other airlines performing the same maintenance, the accident could possibly have been avoided.
Maintenance procedures, especially those associated with airworthiness directives and service bulletins, must consider the complexity of tasks being required, and not become so complex that they create new problems or difficulties. (Common Theme: Unintended Effects)
- In this accident, the service bulletin-related maintenance was difficult and time consuming to accomplish. American Airlines developed an alternate procedure to save time. The procedure was not properly validated and resulted in unintended damage to the areas that had just been inspected. According to the NTSB, proper validation of the procedure would have made apparent the difficulty in manipulating the engine/pylon assembly and the potential for damage to the wing/pylon attachment structure.
Flawed safety assumptions made during design phases can have unintended, catastrophic consequences. (Common Theme: Flawed Assumptions)
- The wing leading edge slat system was designed without an alternate means to lock the slats in the extended position. McDonnell-Douglas assumed that the slats would always retract symmetrically. Further, with loss of the number one electrical generator, the stall warning stick shaker motor and slat asymmetry indications were deactivated, making it impossible for the flight crew to determine that the leading-edge asymmetry had occurred and that the left wing had stalled.