Douglas DC-9-31
Southern Airways Inc., Flight 242, N1335U
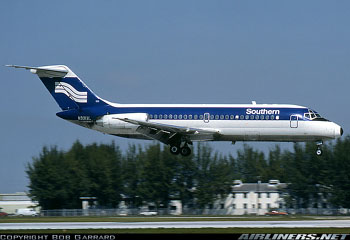
Photo copyright Bob Gerrard - used with permission
New Hope, Georgia
April 4, 1977
At approximately 4:19 PM Eastern Standard Time, on April 4, 1977, a Southern Airways DC-9 airplane, Flight 242, entered a severe thunderstorm at an altitude of between 14,000 and 17,000 feet near Rome, Georgia en route from Huntsville, Alabama to Atlanta, Georgia. Both engines were damaged, and all thrust was lost. The engines could not be restarted. The crew attempted an emergency landing on a highway in New Hope, Georgia but the airplane crashed. Of the eighty-five (85) persons on board the flight, sixty-two (62) were killed, twenty-two (22) were seriously injured and one was slightly injured. Eight persons on the ground were killed and one person was seriously injured; one person died about one month later.
History of Flight
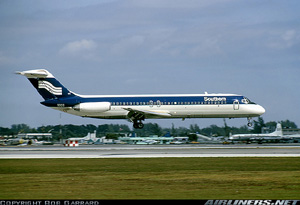
Photo copyright Bob Garrard - used with permission
At approximately 3:54 p.m. Flight 242 departed Huntsville, Alabama on an instrument flight rules (IFR) plan for the Hartsfield-Atlanta International Airport. The flight's route was direct to the Rome VOR (Very High Frequency Omni-range navigational aid) located approximately 72 nautical miles east-southeast of Huntsville and 46 nautical miles northwest of the Atlanta airport. The estimated time en route was 25 minutes and requested en route altitude was 17,000 feet (above sea level).
At approximately 3:55 the flight crew established communications with Huntsville departure control and was cleared to climb to 17,000 feet and proceed directly to the Rome VOR. According to the cockpit voice recorder (CVR), at approximately 3:56, the captain, in reference to the severe weather depicted on the weather radar commented, "Well, the radar is full of it, take your pick." Also at 3:56 the air traffic controller told Flight 242 that his radar was showing heavy precipitation about five nautical miles ahead of the flight. Flight 242 responded, "Okay...we're in the rain right now...it doesn't look much heavier than what we're in, does it?" The controller then said, "...I got weather cutting devices on which is cutting out the precip that you're in now... however, it's not a solid mass, it...appears to be a little bit heavier than what you're in right now." The flight crew responded, "Okay, thank you."
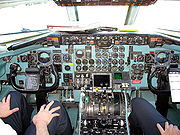
From 3:56 until approximately 4:04, flight deck conversation consisted primarily of a discussion regarding the severity of the weather ahead of the airplane and a strategy for penetrating and safely transiting that weather. At 4:04 the cockpit voice recorder recorded the sounds of rain and hail, and the flight informed the air traffic controller that it was reducing speed. At 4:06, flight 242 was cleared to descend to 14,000 feet, and simultaneous with acknowledging the clearance, the CVR recorded the sounds of heavy hail or rain. At 4:06:57 the CVR stopped recording for 36 seconds, and when it began recording again, the sound of heavy rain continued for another 40 seconds.
At 4:09:15 Flight 242 announced to the controller that the windshield had broken and that the left engine had failed. For the next 45 seconds, flight deck conversation focused on restarting the failed engine; however, at 4:10:05 the crew announced that the right engine had also failed. At 4:10:56 the CVR failed for two minutes and four seconds. During this same time period, radio transmissions to the flight went unacknowledged.
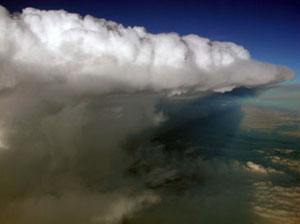
At 4:13 the CVR resumed operation, and discussion in the flight deck, and with air traffic control, centered on finding an alternate airport for landing. At 4:14:02 the flight crew announced that both engines had failed, the flight was at 5,800 feet and descending, and discussions ensued regarding finding a suitable landing site, including clear fields or straight sections of highway.
At 4:18:02 the flight crew's last radio transmission was, "...we're putting it on the highway, we're down to nothing." From 4:18:36 to 4:18:43 crash sounds were recorded on the CVR.
The NTSB report indicated that the aircraft's outboard, left wing section first contacted two trees near Highway 92 in the community of New Hope, Georgia. About 0.8 miles farther north-northeast, the left wing again contacted a tree along the highway within the community of New Hope. The left and right wings continued to strike trees and utility poles on both sides of the highway, and 570 feet after striking the first tree, the aircraft's left main gear contacted the highway to the left of the centerline. Almost simultaneously, the outer structure of the left wing struck an embankment, and the aircraft veered to the left and off the highway. The aircraft traveled another 1,260 feet before it came to rest. The total wreckage area was about 1,900 feet long and 295 feet wide; the area was oriented on a magnetic heading of about 25°.
The investigation concluded - based on examination of wreckage, review of radar and air traffic data, interviews with other flight crews in the area, and statements made by survivors - that the engines were essentially overwhelmed by massive quantities of water and hail. This resulted in compressor stall, leading to turbine over-temperature and failure, and a complete loss of thrust on both engines. The combination of engine damage and continued high rates of rain/hail ingestion prevented restarting of the engines, leading to an emergency landing and the accident.
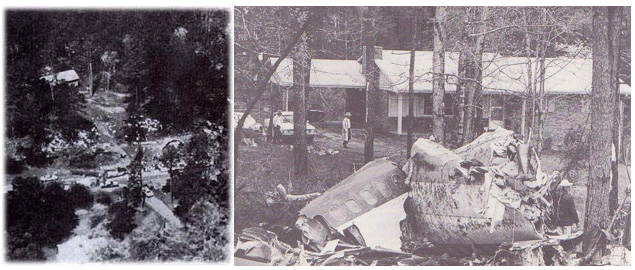
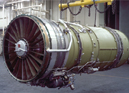
Photo copyright Pratt & Whitney
- used with permission
Engine Description
The JT8D is an axial-flow, front turbofan engine incorporating dual-spool design. There are two coaxially-mounted independently rotating assemblies. The first is a rotating assembly for the low pressure compressor (LPC), which consists of the first six stages (i.e. six pairs of rotating and stator blades, including the first two stages which are for the bypass turbofan), driven by the second (downstream) turbine (which consists of three stages). The second is a rotating assembly for the high-pressure compressor (HPC) section and has seven stages. The high-pressure compressor is driven by the first (upstream) turbine, which has a single stage.
The engine compressor inlet incorporates a non-rotating inlet guide vane (IGV) assembly, intended to redirect inlet air flow into rotating compressor elements. The front-mounted bypass fan has two stages. The annular discharge duct for the bypass fan runs along the full length of the engine, so that both the fan air and exhaust gases can exit through the same nozzle. This arrangement allows some noise attenuation in that the still-hot fast-moving turbine exhaust is shrouded in much-cooler and slower-moving air (from the bypass duct) before interacting with ambient air. Thus the JT8D noise levels were significantly reduced from previous non-turbofan engines, although the low bypass ratio meant that relatively high noise levels were still produced.
Eight models comprise the JT8D standard engine family, covering the thrust range from 12,250 to 17,400 pounds-force (62 to 77 kN) and powering 727, 737-100/200, and DC-9 aircraft. More than 14,000 JT8D engines have been produced, totaling more than one-half billion hours of service with more than 350 operators, making it the most popular of all low-bypass turbofan engines ever produced.
Within the fan inlet case, there are anti-icing air bosses and probes to sense the inlet pressure and temperature. Similar units exist throughout the engine to check temperatures and pressures.
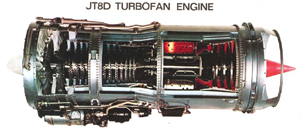
At the thirteenth (i.e. the final) compressor stage, bleed air is extracted and used for engine and airframe anti-icing. The amount is controlled by the Pressure Ratio Bleed Control (PRBC) sense signal. The diffuser case at the aft end of the compressor houses the thirteenth stage. Its increasing cross-sectional area allows the compressed air to slow down before entering one of the engine's nine burner cans. Again, there are two bosses to extract thirteenth stage air for anti-icing, de-icing of fuel, and airframe (cabin pressurization) use. Not all the compressed air enters the burner cans at the fuel-ignition point; some bypasses the can completely and cools the first turbine stage, and some is gradually introduced into the burner can's perimeter in such a way that the burning fuel is held near the can's centerline.
There are nine combustion chambers positioned in a can-annular arrangement. Each chamber has three air inlet hole sizes: the smallest is for cooling, the medium is for burning, and the large is for forming an air blanket.
Scoop Factor
Scoop factor is a term describing the relative behavior of the columns of air/water being ingested by the engine compared to the air/water "disturbed" by the airplane's forward motion. This factor has been described in Aerospace Industries Association (AIA) Report PC338 as:
"The column of air in front of the engine is captured, to a greater or lesser extent, by the engine. When flying in rain, this column is, in effect, two columns; one of air particles and the other of water particles. The amount of air ingested by the engine depends on airplane and engine speed. At high airplane speeds and low engine RPM, more air is intercepted by the inlet than the engine requires. Thus air is spilled around the inlet, effectively reducing the cross section of the column of air being ingested. The water droplets, having greater momentum, are not spilled around the inlet and the column of water particles thus remains essentially the same size as the inlet projected area. This 'scoop factor' can increase the water/air ratio by as much as 200 percent at the inlet plane."
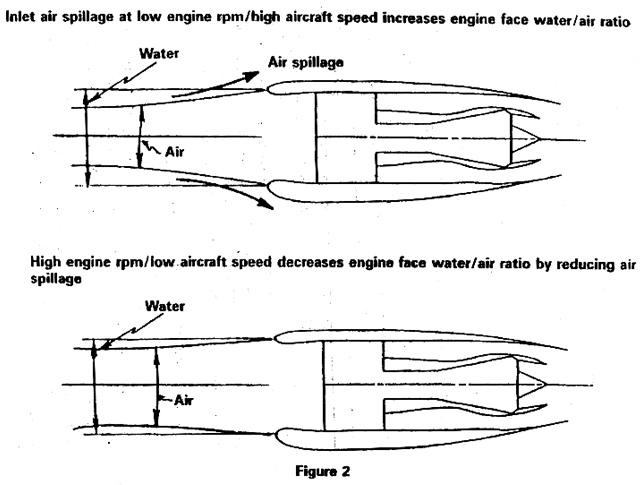
Effect of Water Ingestion On Turbine Engines
An animation illustrating the effects of water ingestion on JT8D engine operation is available below:
As a result of inclement weather-related incidents and accidents involving other turbofan engines subsequent to this accident, a comprehensive review of the general subject of inclement-related power loss was undertaken. The product of this extensive review was documented in AIA Report PC338-1, "Investigation of Engine Power Loss and Instability In Inclement Weather."
Pertinent excerpts from this report state:
"There have been several known events in which engines have experienced complete thrust loss during an encounter with heavy rain and hail. In most cases, the thrust losses occurred as the airplane encountered heavy precipitation and moderate turbulence during descent. Engine thrust was most likely near or at idle setting; however, thrust lever excursions may have been made during the event."
"Ingestion of water in liquid or solid form will affect engine operation because of the higher specific heat of water and the latent heat associated with evaporation."
"The ingestion of heavy amounts of water in the gas path causes the compressor to assume new operating conditions. The reason for this compressor rematching is that when the water is vaporized within the engine, it absorbs about 1,000 BTU per pound of evaporated water from the air passing through the engine, effectively reducing the air temperature in the downstream stages of the compressor and in the combustion chamber."..."The degree of compressor rematch is, of course, a function of the water/air ratio and the compressor design."
The compressor rematch moves the high pressure compressor operating line toward the surge line, causing the compressor to be more susceptible to surge.
The relevant sections of this report are available at the following links:
AIA PC 338-1 Project - Operational Factors
AIA PC 338-1 Project - Environmental Definition
A short video illustration of engine water ingestion testing is available below. The subject video was extracted from video documentation of a Pratt & Whitney high bypass turbofan engine that was not a JT8D, and is representative of current water ingestion tests.
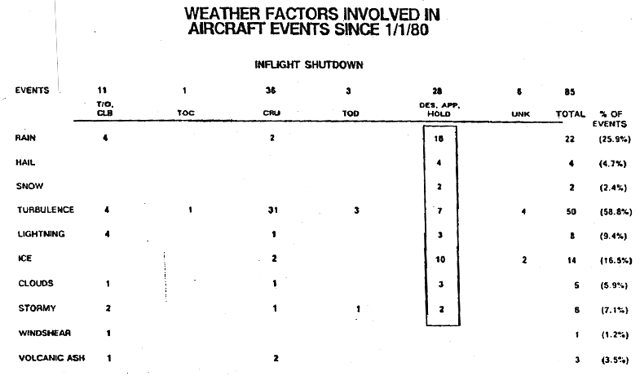
The National Transportation Safety Board issued 25 findings, most significantly concerning engine operation in severe weather, inclement weather, adequacy of weather monitoring, and air traffic control. The complete text of the findings is available at the following link: (NTSB Findings)
The complete NTSB accident report can be viewed at the following link: (Accident Report)
The probable cause was determined to be:
"....the total and unique loss of thrust from both engines while the aircraft was penetrating an area of severe thunderstorms. The loss of thrust was caused by the ingestion of massive amounts of water and hail which in combination with thrust lever movement induced severe stalling in and major damage to the engine compressors."
Contributing factors were listed as:
".... the failure of the companies dispatching system to provide the flight crew with up-to-date severe weather information pertaining to the airplane's intended route of flight, the captains reliance on airborne weather radar for penetration of thunderstorm areas and limitations in the Federal Aviation Administration's air traffic control system which precluded the timely dissemination of real-time hazardous weather information to the flight crew."
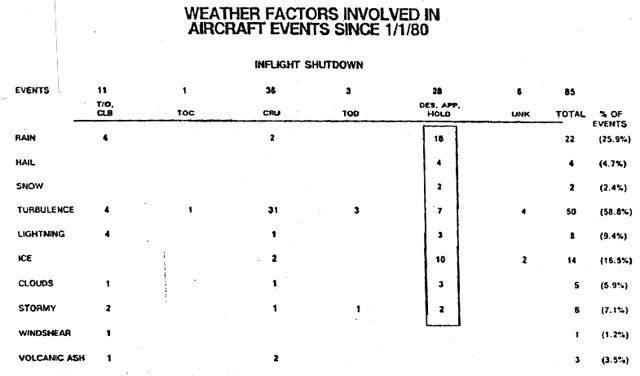
The NTSB issued a number of recommendations related primarily to the forecasting and dissemination of information regarding severe weather, and a means to classify severe weather, to advise flight crews of location, and enhance their ability to avoid potentially dangerous weather phenomena.
The complete text of the recommendations is available at the following link: (NTSB Recommendations)
The certification basis for the Pratt & Whitney JT8D, as installed on the DC-9, was Civil Air Regulations (CAR) 13 through Amendment 5. CAR 13 was first effective in 1956, and, through Amendment 5, there were no turbine engine water ingestion requirements, nor were any tests relative to water ingestion conducted during the certification of the JT8D engine. It was not until the inception of 14 CFR part 33 that water ingestion standards were first introduced into turbine engine certification.
It is important to note, however, that in spite of the lack of water ingestion standards for the early turbine engines, the service experience of this family of Pratt & Whitney JT8D engines while operating in inclement weather, including rain, was quite good during its almost half billion hours of operation.
Evolution of Water Ingestion Standards
Turbine engine tolerance to inclement weather was not a consideration prior to 1974. However, the early service history of turbine engines in inclement weather did not indicate that operational vulnerabilities existed. It was not until the development of higher bypass, higher pressure ratio engines that difficulties during operation in inclement weather began to identify themselves, and the need to revise the engine certification standards became apparent.
Improved Airplane Aerodynamics
At the time of this accident, aerodynamics of airplanes powered by the JT8D engine (DC-9, 727, 737-200) were such that typical operation resulted in relatively high engine rotational speeds, and use of higher power settings for most phases of flight than are required by the current airline fleet. This contrast in power setting is most pronounced during descent and approach. Airplanes such as the DC-9 commonly used power settings substantially above idle for these flight phases. In today's higher efficiency airframes, i.e., Boeing 777, 737NG, Airbus A330/340, etc., engine power during descent is commonly set at idle for long periods of time. Since the operational "run lines" for the engine's compressor tend to be closer to the surge line at lower operational engine speeds, a heightened awareness of engine capabilities while operating in inclement weather is now necessary.
Weather Radar Capability
The onboard weather radars in common use at the time of this accident had functional limitations when operating in heavy precipitation and hail. The presence of high-water content, especially near to the airplane, could result in attenuation of the radar signal and loss of indication of significant weather in front of the airplane. The NTSB report commented on the attenuation as a function of the heavy rainfall that the accident airplane had penetrated and noted that the radar may not have been capable of properly displaying the highest intensity of the rainfall that the airplane was about to transit. This capability limitation was known by the radar manufacturer and was included in the airline's training material. The investigators concluded that the accident airplane had penetrated an area of especially intense precipitation, and the radar display may have been unable to accurately identify the area of highest water concentration.
Operation into severe weather, including high precipitation rates, leading to a dual-engine failure.
- Weather detection systems in use at the time were adequate.
- Turbine engine regulatory requirements were adequate for engine rain ingestion.
- Flight crews would consistently avoid extreme weather.
At the time of this accident, no significant service experience had identified difficulties related to operation of JT8D engines in high rainfall rates.
At the time of this accident, CAR 13 had been replaced by 14 CFR part 33 as the applicable regulatory standard for engine certification. 14 CFR 33.77 Amendment 6, in 1974, introduced the first requirement for water ingestion capability for turbine engines. This rule provided the initial requirements for foreign object ingestion capability, including birds, ice, hail, and water. This rule was later revised by separating the foreign objects into 14 CFR 33.76 (birds), 33.77 (ice), 33.78 (rain and hail). The original water ingestion requirement contained in amendment 6 specified a water concentration of 4% of engine airflow, by weight. This concentration equates to a rainfall rate of approximately 30 inches per hour, a very severe storm.
Appendix B to 14 CFR part 33 was added in 1998 and provided a table of rain concentration requirements verses altitude for turbine engine water ingestion standards. Appendix B is referenced by 14 CFR 33.78.
14 CFR 33.78, Rain and Hail Ingestion
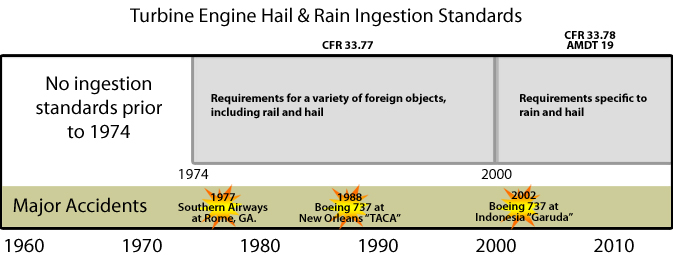
Current regulations require gas turbine engines to be water ingestion tested.
Airplane Life Cycle:
- Design / Manufacturing
Accident Threat Categories:
- Inclement Weather / Icing
Groupings:
- N/A
Accident Common Themes:
- Flawed Assumptions
Flawed Assumptions
In the 1950's and 1960's, with the introduction of the first turbine engines into the commercial fleet, foreign object ingestion standards did not exist. Also, during this period, these engines, including the JT8D, demonstrated satisfactory operational experience throughout a wide range of inclement weather conditions. Based on the satisfactory operational experience, and a lack of demonstrated engine vulnerabilities, it was assumed that water ingestion standards were therefore not necessary. In the 1970's it was recognized that foreign object ingestion standards needed to be developed and incorporated into the certification bases of turbine engines.
TACA International Airlines Flight 110, Boeing Model 737-300, N75356, New Orleans, Louisiana
On May 24, 1988, a Boeing Model 737-300, N75356, owned by Polaris Aircraft Leasing Corp. and operated by TACA International Airlines as Flight 110 from San Salvador, El Salvador with a stop in Belize City, Belize, made a forced landing on a levee near New Orleans, Louisiana, following a dual engine failure. The airplane had encountered extremely severe rain and hail at approximately 16,500 feet during descent.
See accident module
Garuda 737-300, Solo City, Indonesia
On January 16, 2002, a Garuda Boeing 737-300 experienced a dual-engine failure at 18,400 feet in intense rain/hail near Solo City, Indonesia. The flight crew was unable to restart the engines. The aircraft ditched in a river, resulting in one fatality.
Technical Related Lessons
Turbine engines must be capable of operation in a wide range of atmospheric conditions, including severe hail and rain. (Threat Category: Inclement Weather/Icing)
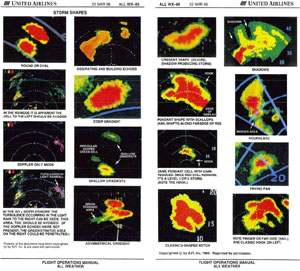
Photo copyright Ajt, Inc - used with permission
- Up to the time of this accident, the JT8D family of turbofan engines had a very satisfactory service history, having operated for millions of hours throughout a wide range of inclement weather conditions. Investigators concluded that this accident was due to attempted penetration of an extremely severe thunderstorm with rarely seen, exceptionally high precipitation rates, including both rain and hail. Examination of the wreckage showed that hail had caused the windshield to fail and had caused damage to wing leading edges and engine inlets. Even though the JT8D engine had failed in this accident, investigators believed that the probable cause for the accident was severe weather, rather than engine vulnerability.
There are some natural phenomena that must be detected and avoided, as their severity can be such that they will exceed the performance capability of any pilot or airplane. (Threat Category: Inclement Weather/Icing)
- This flight encountered a storm of extremely high liquid water content such that the capability of the engines to continue running was overwhelmed, and failure of both engines occurred. The NTSB concluded that the flight crew was unable to adequately establish the severity of the weather, based on limitations of the installed weather radar, prior to entering. Had they been able to establish the severity of the storm they were about to enter; they would have had an opportunity to change or reverse course.
Common Theme Related Lessons
Safety standards must be found to be consistent with the actual threat environment that will be experienced, including accounting for the actual conditions prevalent during the threat encounter. Assumptions are only valid if the related threat environment is properly defined. (Common Theme: Flawed Assumption)
- At the time of the JT8D development and certification, there were no water ingestion standards, nor was there service evidence that standards were necessary. Subsequent to the introduction of the JT8D into service, other turbofan engine designs exhibited inclement weather vulnerabilities, and drove introduction of engine water ingestion requirements. This accident underscored the need to have a robust water ingestion capability, and that the standards that were introduced in 1974 were intended to accomplish this objective.