Embraer EMB-120RT
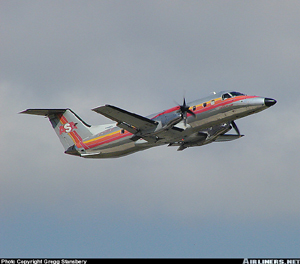
Photo copyright Greg Stansbery - used with permission
Atlantic Southeast Flight 529, N256AS
Carrollton, Georgia
August 21, 1995
Approximately 30 minutes after departing from the Atlanta Hartsfield International Airport, Atlanta, Georgia, an Embraer EMB-120RT airplane, operated as Flight 529 by Atlantic Southeast Airlines Inc., experienced the loss of a blade from the left engine propeller while climbing through 18,100 feet. The airplane crashed near West Georgia Regional Airport, Carrollton, Georgia while attempting an emergency landing. The crash killed seven passengers and the captain.
The in-flight separation of the propeller blade resulted in failure of the left engine mount, displacing the propeller and gearbox to the left side of the wing. This resulted in excessive drag, loss of wing lift, and reduced directional control of the airplane. The NTSB determined that the propeller blade fracture was caused by a fatigue crack originating from multiple corrosion pits that, due to ineffective maintenance procedures, had not been discovered.
The accident blade had initially been removed from service after failing an on-wing ultrasonic inspection. However, the accident investigation determined that the inspection procedure used to detect cracks and corrosion in the taper bore surface of the blade spar was inadequate. Additionally, inadequate training of maintenance personnel, and poor communication by the propeller manufacturer led to misapplication of the propeller repair procedure, allowing the accident blade to be returned to service with an undetected crack.
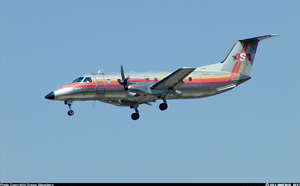
Photo copyright Gregg Stansbery - used with permission
History of Flight
On August 21, 1995, an Embraer EMB-120RT airplane operated by Atlantic Southeast Airlines Inc. (ASA) as ASE flight 529 experienced an engine failure due to the in-flight loss of a propeller blade on the left engine. The in-flight separation of the blade caused the propeller, with its gearbox to become displaced, causing damage to the left engine nacelle, resulting in loss of wing lift, and reduced directional control of the airplane. The airplane crash landed near Carrollton, GA while attempting an emergency landing. Seven passengers and the captain were fatally injured.
ASE Flight 529 was a scheduled passenger flight from Atlanta Hartsfield International Airport (ATL), Atlanta, Georgia to Gulfport, Mississippi (GPT). There were 26 passengers and three crew members on board. According to the NTSB accident report, while climbing to 18,000 feet at 160 knots, several loud sounds were heard and the airplane started to roll to the left. The crew also noticed that the torque from the left engine decreased to zero. Some passengers reported that the propeller blades from the left engine were wedged against the leading edge of the wing.
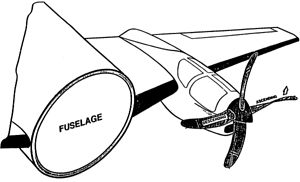
After declaring an emergency, the flight crew attempted to stabilize the airplane and return to ATL. However, they were unable to maintain altitude and were directed toward West Georgia Regional Airport (CTJ), Carrollton, GA for an emergency landing. During approach, unable to maintain airspeed and a stable altitude, the airplane impacted the ground approximately 30 minutes after departure, and 10 minutes after experiencing the in-flight blade loss.
Flight 529 Crash Site
According to the NTSB accident report, the airplane came to rest at the northwest end of an 850 foot wreckage trail that was aligned on a heading of about 330 degrees magnetic on unimproved farmland with trees. A trajectory from the ground impact pointed to the tree line revealed that the airplane was descending at an angle of about 20 degrees, and a left-wing-down attitude of 15 to 40 degrees. Ground scars were observed to be consistent with separation of the left wing root from the fuselage.
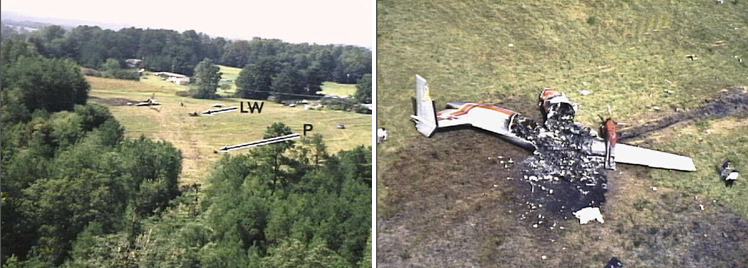
Aerial photo of Atlantic SE Flight 529 crash site (right)
Photos provided by NTSB
An area of grass leading up to and surrounding the main wreckage was burned out to a radius of about 30 feet due to post-crash fire. Portions of two of the right engine propeller blades remained attached to the propeller hub and engine and the remaining two blades of the right engine/propeller assembly were located nearby. The left engine propeller and reduction gear box (RGB) assembly were located approximately 160 feet past the tree line. The propeller hub and blade assembly contained three complete propeller blades with the inboard piece of a fourth blade protruding about 1 foot from the hub. The outboard piece was found three weeks later.
Embraer EMB-120RT Airplane
The Embraer EMB-120RT is a twin turboprop commuter airliner incorporating Pratt & Whitney PW118 engines, and Hamilton Standard 14RF propeller blades. During certification of the airplane, the ability to safely complete a flight following the failure of a propeller was addressed by the damage tolerance objectives of 14 CFR 25.571(e)(2). However, it had been established that the state of the art in airplane design could not accommodate the level of structural damage due to impact of the propeller that might result. It was widely regarded that compliance with the rule was impractical, and the rule itself was eventually modified to remove the requirement relative to propellers. A failure of this type was considered catastrophic. Because of the impracticality of the rule, and the associated rule change, several turboprop airplane designs of the era, including the EMB-120 was granted an exemption from compliance with the propeller impact requirements of 14 CFR 25.571(e)(2). In 1990, new requirements were developed, specific to propellers, in 14 CFR 25.905(d), which required that the hazards related to propeller failures, including structural damage to the airplane, be minimized.
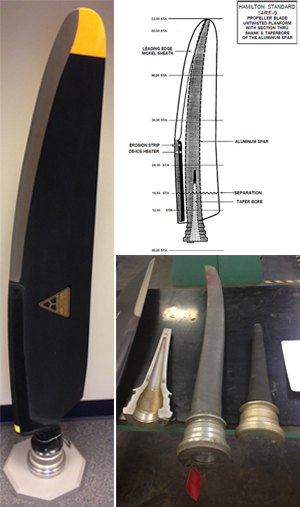
Hamilton Standard 14RF-9 Propeller Blade
The Hamilton Standard 14RF-9 propeller blade is part of a family of composite propeller blades designed for turboprop commuter airplanes. It has a solid, forged 7075-T73 aluminum alloy spar which is the main load carrying structure. The airfoil is formed by glass fiber-filled epoxy and foam adhesively bonded to the spar. For weight reduction and balance weight installation, the spar incorporates a taper bore. During early production of the blades, the taper bores underwent a shotpeen surface treatment process in order to improve their resistance to surface cracking. This process was later deemed unnecessary by Hamilton Standard and was discontinued. The Hamilton Standard fleet was therefore comprised of earlier production blades that had been shotpeended, and later production blades which had not, leaving a mixture blades in the fleet.The accident blade taper bore was of a later production series, and had not been shotpeened.
As long as the propellers, and blades, were maintained in accordance with Hamilton Standard maintenance instructions, it was able to be operated with no life limits. This is typical of nearly all propeller designs. Prior to installation, the 14RF-9 blade was balanced by inserting lead wool into the taper bore, followed by installation of a cork to prevent the lead wool from moving within the taper bore.
Preceding Blade Failure Events
Approximately one year prior to this accident, two propeller blade failure events occurred, one on a Hamilton Standard 14RF series, and a second on a 14SF series blade, These failures were determined to be the result of the development of cracks inside the taper bore of the blade. The first event was on an Inter-Canadien Aerospatiale-Aeritalia ATR 42 that occurred on March 13, 1994. The second event happened two weeks later on a Nordeste EMB-120. Since propeller blade failures are generally considered to be catastrophic events, these two failures were viewed as extremely serious, and urgent fleetwide corrective action was undertaken.
In these two events, blade failures occurred at different blade locations, resulting in different levels of damage to the engine installation. In the ATR 42 event, the 14SF blade separated near its root, resulting in a high level of imbalance, completely releasing the gearbox and propeller hub. The blade failure resulted in a single engine landing with drag levels similar to that of a feathered propeller. The released blade also struck the aircraft's fuselage, causing loss of pressurization and damage to a passenger seat.
In the second event, the 14RF blade failure occurred at a location further from the root than in the previous blade failure, and resulted in lower imbalance forces. The resulting imbalance caused failure of the gearbox attachment lugs. The propeller automatically feathered, and the engine cowlings detached from the engine nacelle. The crew successfully performed a single-engine landing.
Hamilton Standard Blade Inspection and Repair Procedure PS960A
In response to the two blade failure events that had occurred prior to this accident, Hamilton Standard developed a series of service bulletins intended to address problems related to crack origination inside the taper bore. Approximately one week after the second March 1994 blade failure event, Hamilton Standard began a program to conduct ultrasonic inspections on all in-service 14RF and 14-RS series blades. Blades with ultrasonic indications that might potentially be due to cracks were removed from service, and returned to Hamilton Standard. Removed blades were then inspected using a borescope to determine if cracks had actually formed.
An animation of the accident sequence, and illustration of the blade inspection procedure is available below:
Early in the inspection process, Hamilton Standard determined that some blades were being rejected due to ultrasonic indications that were not from cracks, but rather from mechanical damage. An investigation by Hamilton Standard engineers determined that the mechanical damage was the result of tools and techniques employed to insert and remove lead wool used to balance the propeller blades. Although no cracks were found on these blades, the manufacturer believed that the visible damage was beyond acceptable limits, and a repair procedure to correct the mechanical damage disseminated via Hamilton Standard repair procedure PS960.
Once a blade was returned to Hamilton Standard based on ultrasonic inspection results, PS960 required a visual inspection of the taper bore, and provided instructions for repairing any detected mechanical damage. Mechanical damage was blended per instructions in the procedure. No unblended mechanical damage was allowed to remain. Following repair, the taper bore was inspected with a borescope, and if visual inspection results were acceptable, another ultrasonic inspection was conducted. If ultrasonic inspections results were within limits, the blade could be returned to service.
As part of the investigation into crack formation in the taper bore, it was determined that the cork used to retain the lead balance wool in the taper bore contained a chlorine residue that could cause corrosion in the taper bore. Within 10 days of its initial issuance, PS960 was revised to become PS960A, and included procedures to eliminate the cork, and replace it with a sealant.
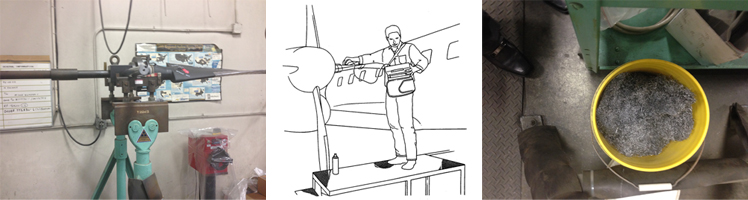
Concurrent with the development of PS960A, and in response to the two March 1994 propeller failure events, Hamilton Standard developed a series of alert service bulletins to address the formation of cracks within the taper bore. The bulletins called for an on-wing ultrasonic inspection, to be performed by an inspector qualified in non-destructive testing (NDT). Blades rejected during this inspection were to be returned to Hamilton Standard customer support centers where a borescope inspection was performed, and repairs initiated, if the blade was repairable. The FAA issued Airworthiness directive (AD) 94-09-06, which required that blades with ultrasonic indications above 50% were to be removed from service. The accident blade yielded inspection results of over 50%, and was removed from service on May 19, 1994. In total, 490 blades, including the accident blade were sent to Hamilton Standard for evaluation and possible repair.
Returned blades were ultrasonically inspected to verify the on-wing inspection results, and taper bores were cleaned and borescope inspected for visible anomalies such as cracks, corrsosion, pitting, or other flaws. None of the returned blades were found to be cracked, but corrosion was noted in 13% of the returned blades. None of the blades with visible corrosion were returned to service.
During the inspection process, Hamilton Standard discovered that a small percentage of returned blades did not have observable anomalies in the taper bore. This subset of blades had shotpeened taper bores, and Hamilton Standard concluded that the surface roughness inherent with shotpeening could produce an ultrasonic indication that would result in rejection of the blade. Hamilton Standard concluded that the blending procedures of PS960A to blend areas of mechanical damage could also be used to locally blend the shotpeened surface in areas where ultrasonic indications had occurred, and potentially eliminate the ultrasonic indications. Hamilton Standard issued a memo containing information that the repair procedure specified in PS960A could be extended to include blending of local areas in the taper bores of shotpeened blades.
During the accident investigation, the National Transportation Safety Board (NTSB) evaluated PS960A and had no technical objection to the decision to apply the procedure to remove ultrasonic indications caused by shotpeened impressions. However, the Board determined that the method in which it was communicated within Hamilton Standard, and to field technicians, was inadequate and confusing, and led to the procedure being employed to blend areas of ultrasonic indications on non-shotpeened blades, including the accident blade.
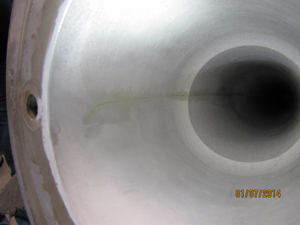
Failure to Detect an Existing Crack
The accident blade was first removed from service as a result of ultrasonic indicationsabove the limits allowed during the on wing ultrasonic inspection. In accordance with the PS960A repair procedure, it was then subjected to a borescope inspection to identify evidence of cracks or corrosion. The inspection result on the accident blade revealed no visible cracks or evidence of corrosion.
The investigation determined that it was widely understood that the PS960A repair procedure could be used to repair areas of the taper bore surface that had "unexplained ultrasonic indications" for both shotpeened and unshotpeened blades. However, the procedure was applicable to both types of surface finishes only to repair visible mechanical damage, and was not applicable to ultrasonic indications on blades that had not been shotpeened. The investigation determined that , since the accident blade had not been shotpeened, the repair procedure should not have been employed in the case of the unexplained ultrasonic indication. However, based on the misunderstanding regarding the applicability of the repair procedure, PS960A was applied to the accident blade. The local surface that had yielded the out of tolerance inspection result was blended, and the ultrasonic indication was significantly reduced. Based on ultrasonic indications that were reduced below the AD mandated threshold after repair, the blade was deemed airworthy, and returned to service with an existing, but undetected crack.
The investigation noted that the borescope inspection method lacked several critical steps which contributed to the failure to detect the existing crack. The inspection was conducted without indirect lighting which could have aided in outlining changes in taper bore surface depth. In addition, there was no means to ensure complete borescope coverage of the inner surface.
According to the investigation, the entire inspection process relied heavily on an assumption that the borescope inspection method was effective at detecting a crack. However, once a blade had been inspected and determined to be crack free, no repeat inspections were required for the remainder of the blade's service life.
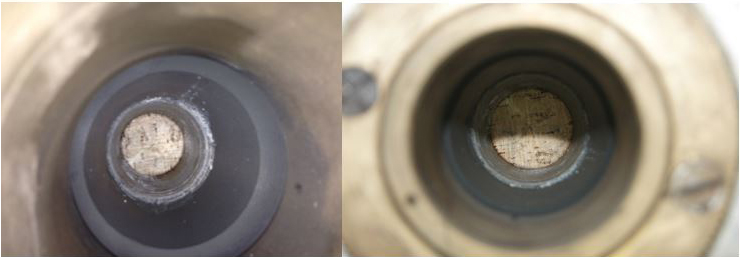
Accident Blade Failure Mechanism
The crack progressed through about 75% of the spar cross section before spar failure. The spar broke at blade station 16.6 which is about 13.2 inches outboard of the blade pin platform.
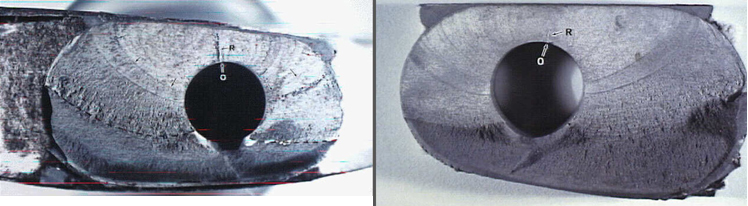
Photos of the fractured areas of the propeller spar show where the crack originated, and how it propagated through the spar. The arrow labeled "O" indicates the origin area, arrow "R" indicates a ratchet mark, which is a result of multiple fatigue origins. Unlabeled arrowheads indicate fatigue propagation direction, and the dashed lines indicate the extent of the fatigue crack.
A magnified view of the origin area on the inboard piece of the blade shows the initiation areas ("01" and "02"). Lead deposits ("L") can be seen around the fracture surface damage ("D"), the ratchet mark ("R"), and the location of a corrosion area ("P").
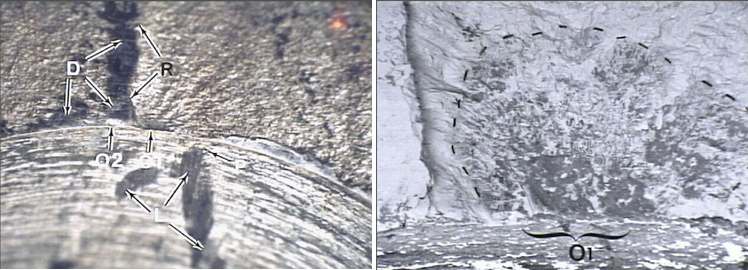
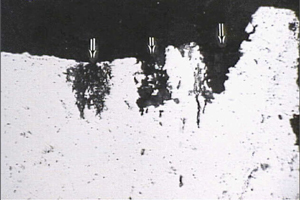
- NTSB Docket Photo
Pitting Corrosion
Laboratory examination of the fractured blade determined that a fatigue crack originated from several corrosion pits in the taper bore surface of the blade spar and propagated toward the outside of the blade. These pits were found in a line about 0.07 inches long, with a maximum depth of nearly 0.006 inches below the taper bore surface.
Corrosion is the deterioration of metal due to its chemical reaction with the surrounding environment. It can take many different forms, and characteristics vary depending on the operating environment. Pitting corrosion is a localized form of corrosion and occurs in the presence of an aggressive chemical such as chloride. Pitting usually occurs on active-passive metals in environments containing aggressive ions, such as chlorides. Pit growth is encouraged by concentration of the corrosive in the pit and an unfavorable anode-cathode ratio. Aluminum alloys and stainless steels are especially susceptible to chloride pitting. Investigators determined that in the case of the accident blade, pitting was the result of chlorine that originated from the taper bore cork. As part of the manufacturing process, the cork had been bleached prior to being used to retain the lead wool inside the taper bore.
Pitting Corrosion on Aluminum Alloy
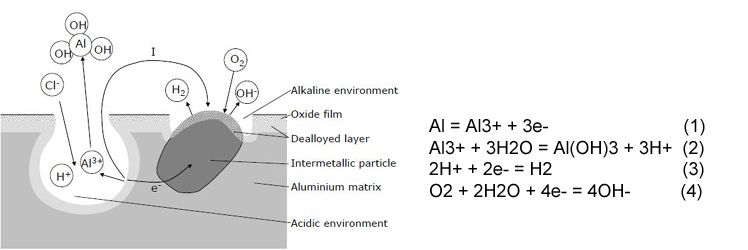
Pits are initiated by "chloride attack" at weak sites in the oxide.
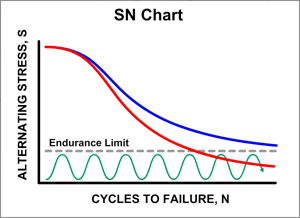
As a pit propagates, the environment inside the pit (anode) changes, and the pH of the pitted material will decrease. To balance the positive charge produced, chloride ions will migrate into the pit. The resulting formation of hydrochloric acid inside the pit causes accelerated pit propagation.
Propeller blades are designed to operate within their endurance limit to ensure safe operation. When corrosion pits, such as those discovered in the accident blade are inadvertently introduced, a stress concentration results, which reduces the fatigue life of the metal. If undetected, cracks can develop, which can eventually lead to a catastrophic failure of the blade.
Accident Memorial
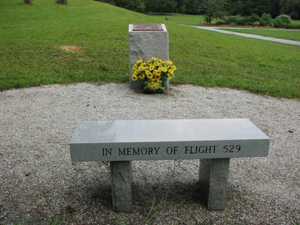
The memorial site for this accident is located at The Shiloh Methodist Church in Carroll County, GA. It was dedicated on August 21, 2000.
The NTSB issued 23 recommendations, addressing the nature of the propeller failure, effect of the failure on airplane performance, propeller maintenance and inspection procedures, and various aspects of the conduct of the accident flight. The complete text of the recommendations is available at the following link (NTSB Findings).
The complete accident report is available at the following link: (NTSB Report).
The NTSB issued 8 recommendations addressing propeller corrosion, propeller inspection, maintenance and repairs, FAA guidance material relative to propeller maintenance, and industry communication. The complete text of the recommendations is available at the following link: (NTSB Recommendations).
The regulations listed here are those that were in effect at the time of certification of the airplane and/or propeller. The list may include applicable guidance material as well.
14 CFR 25.571 Damage tolerance and fatigue evaluation of structure
14 CFR 25.905 Propellers
14 CFR 25.907 Propeller vibration
14 CFR 35.15 Design features
14 CFR 35.37 Fatigue limit tests
14 CFR 35.39 Endurance test
FAA Advisory Circular (AC) 20-66 Vibration Evaluation of Aircraft Propellers
The investigation cited several communication gaps within Hamilton Standard that contributed to this accident. Following the two 1994 propeller failures, Hamilton Standard had initially issued repair procedure PS960 to address the repair of visible mechanical damage on the taper bore surface. When it was learned that taper bore corks contained chlorine residue that could cause corrosion, the procedure was revised as PS960A to include removal of the cork, and replacement with a sealant.
During inspections related to the two 1994 events, Hamilton Standard further concluded that the surface finish of shotpeened taper bores could result in ultrasonic indications that were not related to mechanical damage and was causing large numbers of undamaged blades to be unnecessarily removed from service. As a result, PS960A was expanded to include local blending repair of areas where ultrasonic inspections of shotpeened taper bores had shown anomalies. However, while the expansion of the procedure was intended to include only shotpeened blades, investigators concluded that this information had been poorly communicated throughout Hamilton Standard, and to field organizations.
The change in scope was documented and distributed via internal memo and failed to clarify that the expansion was applicable only to shotpeened taper bores. Investigators believed that if the modified instructions had been properly communicated to field organizations, more blades would have been rejected due to inspection results, and in particular, the accident blade would have been rejected, and not returned to service.
- The taper bore cork contained chlorine which reacted with moisture in the taper bore and created corrosion pits.
- Failure to detect a fatigue crack that originated from multiple corrosion pits in the taper bore allowed it to reach its critical size and led to blade failure.
- The ultrasonic inspection procedure of PS960A would be effective at detecting cracks initiating in the taper bore.
- The borescope inspection required by PS960A was assumed to be adequate to detect any evidence of corrosion pits or cracks developed in the taper bore.
Inter-Canadien Aerospatiale-Aeritalia ATR 42, March 13, 1994
This accident, an inflight blade failure and subsequent separation was the result of cracks that originated inside the taper bore of a Model 14SF blade. The Transportation Safety Board of Canada (TSB) conducted an investigation and concluded that forces induced from the rotation of the three remaining blades resulted in propeller imbalance and loads on the forward engine mounts that exceeded the ultimate limits. This resulted in separation of the propeller and the reduction gearbox assembly from the airplane. The reduction gearbox with the propeller hub, three complete blades, and the retained portion of the fourth blade fell onto an ice-covered lake and was recovered during the investigation. The separated blade had passed through the fuselage and caused depressurization of the cabin. There were no injuries, and the flight crew accomplished a safe landing.
Nordeste Embraer EMB 120, March 30, 1994
This accident also involved a blade separation. The Aircraft Accident Prevention and Investigation Center of Brazil (CENIPA) investigated the Nordeste occurrence. CENIPA did not publish a formal report; however, it provided documentation contained in a technical report by Embraer that affirmed causal findings similar to the Inter-Canadien blade separation. Embraer's report indicated that during the Nordeste event, the imbalance forces from the rotation of the three remaining blades resulted in damage to the reduction gearbox. The remaining three blades and fourth blade stub were found moved toward the feathered position (resulting in minimum aerodynamic drag); and the propeller and reduction gearbox assembly remained within the nacelle area and were partially attached to the airframe. There were no injuries, and this flight crew also accomplished a safe landing.
14 CFR 35.37 Fatigue limits and evaluation
This regulation was revised to address composite materials more effectively. Requirements were expanded to all materials and components (including controls system components, if applicable) whose failure would cause a hazardous propeller effect. It also added environmental effects to the factors that must be considered when establishing fatigue limits. The revised regulation also required a fatigue evaluation of the propeller to show that hazardous propeller effects due to fatigue will be avoided throughout the intended operational life of the propeller.
14 CFR 25.907 Propeller vibration and fatigue
This regulation was revised to require propeller fatigue evaluation to show that failure due to fatigue will be avoided throughout the operational life of the propeller.
FAA Advisory Circular AC 20-66A Vibration Evaluation of Aircraft Propellers
In 2011, this AC was revised to AC 20-66B
After the accident, a stress survey was conducted to reexamine the effect of vibratory modes on the propeller blades. As a result, the FAA issued AD 95-25-11 which modified the EMB-120 Airplane Flight Manual and Maintenance Manual Limitations Sections to reduce the maximum propeller speed (Np) limit during ground operation from 65 to 60 percent to reduce propeller exposure to known high vibratory stresses during ground operation.
Hamilton Standard also performed a risk analysis using results from a NASA-developed fracture mechanics FASTRAN program which found that the 1,250-cycle inspection interval using the original ultrasonic technique provided insufficient safety margins for the detection of taper bore cracks. As a result, The FAA issued AD 96-01-01, effective on January 19, 1996, which required an improved ultrasonic inspection technique and mandated and reduced the 1,250-cycle inspection interval to 500 cycles.
In addition, the Component Maintenance Manual (CMM) for all Hamilton Standard model 14FR, 14SF, and 6/5500F airplane propellers was amended to include a recurring inspection of the taper bore.
AD T95-18-51 - Required ultrasonic shear wave inspections to detect cracks in the taper bore, and that the inspection be repeated every 1,250 flight cycles. If a crack was discovered on a blade, that blade was required to be removed from service. This AD cancelled ADs 94-09-06, and 95-05-03 (which superseded 94-09-06), issued following the March 1994 blade failures. The inspection processes of those two ADs had been deemed ineffective, hence the issuance of this emergency AD.
AD 95-18-06 - Required removal from service of certain serial 14RF-9 blades installed on EMB-120s that had been shear wave tested per ADs 94-09-06 or 95-05-03, repaired and returned to service. Also required shear wave testing of other model 14RF blades, and removal from service if crack indications were present. Imposed a repeat inspection interval of 1,250 cycles, and prohibited return to service of any blades with crack indications per the inspections specified by the AD.
AD 96-01-01 - Required reinspection of blades that had been inspected per previous ADs and required a new test method that was deemed more effective at detecting blade cracks. Also reduced the 1,250 cycles repeat interval to 500 cycles.
AD 96-08-02 - Superseded AD 96-01-01 and mandated a repair procedure (removal of a layer of taper bore material per a reaming procedure, followed by eddy current inspection, dye penetrant inspection, removal of a second layer of material, a wall thickness check, shotpeening, and the application of a corrosion protective coating, Finally, all blades were subject to a repeated inspection every 9500 flight hours.
Airplane Life Cycle:
- Maintenance / Repair / Alteration
Accident Threat Categories:
- Structural Failure
Groupings:
-
N/A
Accident Common Themes:
- Organizational Lapses
- Flawed Assumptions
Organizational Lapses
The decision to expand the PS960A procedure to cover local areas of ultrasonic indications on shotpeened blades was authorized during a Hamilton Standard engineering conference call and issued without FAA or DER's approval. It was documented using an internal memo. The memo failed to clarify that expansion was only applicable to shotpeened taper bores. As a result, the intent of the procedure was misunderstood to be applicable to all taper bores, independent of the type of surface finish. Investigators believed that had the procedure been properly applied, the ultrasonic indication on the accident blade would have resulted in its rejection and would have prevented its return to service with an existing crack.
Flawed Assumptions
Hamilton Standard procedure PS960A was originally intended as an inspection and repair procedure for mechanical damage (tool marks, etc.) found inside the taper bore. Upon learning that taper bores with shotpeened finishes could produce ultrasonic inspection results simply due to the inherent surface roughness, the procedure was expanded in scope to address indications found during inspection of shotpeened taper bores.
Following ultrasonic inspection, if results indicated an anomaly, the next step was to perform a borescope inspection to determine that there was no mechanical damage. In the case of a shotpeened taper bore, the procedure allowed local blending to remove the ultrasonic indication. The intent of the procedure was misunderstood by technicians and was also applied to the smoother finish of unshotpeened taper bores that should not have had any surface finish related anomalies. It was assumed that the associated borescope inspection would reveal any damage, which could then be repaired.
The investigation noted several shortcomings in the borescope procedure related to identifying cracks and deemed it inadequate to determine the airworthiness of a non-shotpeened blade. Because the procedure was inadequate, cracks were not identified in the accident blade, and subsequent repairs reduced the ultrasonic indications (by having blended out a portion of the existing crack) to levels that would have been acceptable for a repair to mechanical damage. This allowed a blade to be returned to service with an existing, but undiscovered, crack, and led to its eventual failure.
Boeing Model 377 Stratocruiser propeller failures
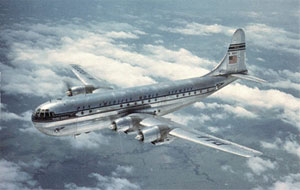
The Boeing model 377 Stratocruiser was a large four engine airliner that entered service in 1949. It was powered by four Pratt & Whitney R-4360 engines which drove four 17-foot diameter Hamilton Standard hollow steel blade propellers. Fifty-six aircraft entered service over a one-year time period and continued in service with several of the world’s major airlines until 1960. Soon after entry into service a series of incidents and accidents occurred resulting from propeller blade failures. The blade design was susceptible to fatigue cracking which led to failure and liberation of a portion of the blade. Resulting propeller imbalance could lead to loss of the propeller and engine from the aircraft, making the aircraft uncontrollable.
January 24, 1950, a Boeing 377 Stratocruiser, operated by Pan American World Airways (PAWA) on a flight to Tokyo, Japan experienced the failure of the number 4 engine due to in-flight loss of a propeller blade. A day later, on a Northwest Airline flight from Minneapolis to New York, a section of the number one propeller of the Boeing Stratocruiser broke off and entered the main cabin. Both aircraft landed safely despite suffering from substantial structural damage.
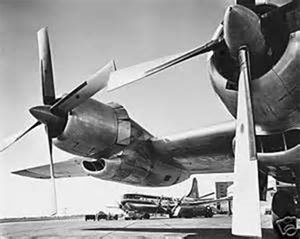
March 29, 1951, on descent through 3000 ft for landing at Idlewild airport, New York, a PAWA B377 Stratocruiser experienced a propeller blade failure on the number one engine. The propeller was feathered, and the airplane landed six minutes later. The number one engine and propeller were found drooped in the nacelle with three of the six mount ring lugs broken.
April 29, 1952, a PAWA B377 Stratocruiser crashed near Carolina, Brazil while en route from Rio de Janeiro to Port of Spain. All 50 persons on board were killed. The probable cause of the accident was determined to be the separation of the number 2 engine and propeller from the aircraft.
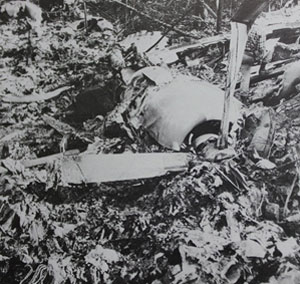
July 28, 1952, while on a ferry flight between Rio de Janeiro and Port of Spain, a Boeing 377 Stratocruiser experienced extreme roughness, requiring a propeller to be feathered. Follow on investigation found transverse fatigue cracks across the midsection of a propeller blade.
December 6, 1953, another PAWA B377 Stratocruiser departed from Honolulu and was about midway to the next stop on Wake Island when the number four engine and propeller separated from the aircraft. After regaining control of the aircraft, an emergency landing was made at Johnston Island. The Civil Aeronautics Board concluded that the accident was due to a propeller blade failure based on similarity to earlier investigations.
March 26, 1955, during a flight from Portland to Honolulu, a PAWA B377 Stratocruiser experienced severe vibration which lasted from five to eight seconds before the engine and propeller departed from the aircraft. The pilots had limited control of the aircraft before ditching it in the Pacific Ocean about 35 miles off of the Oregon coast. There were four fatalities among the 23 persons on board.
Fokker F27 Friendship
On October 26th, 2013, a Fokker F-27-500 operated by Miniliner experienced the failure and departure of the number one propeller and gearbox while climbing through 1000 feet out of Paris Charles de Gaulle Airport. The propeller separated from the engine and punctured the fuselage creating a large hole. The crew was able to land the aircraft safely. The cause of the propeller failure was determined to have been the result of fatigue.
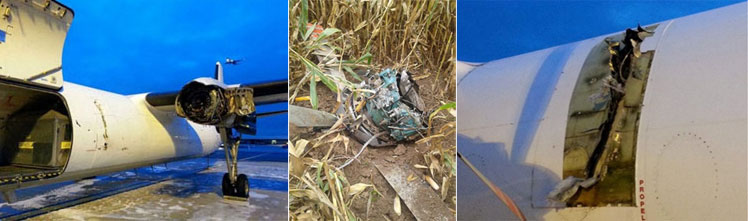
Technical Related Lessons
A propeller blade structural failure results in a massive out-of-balance condition that far exceeds the structural retention capability of the propeller mount and/or engine mount system. Cascading structural failures, damage from debris impact, or loss of airplane control can have catastrophic effects. (Threat Category: Structural Failure).
- During the certification of the Embraer EMB-120RT, the effect on safe flight of a failed or released propeller was addressed in 14 CFR 25.571(e)(2). However, it was later determined that the airplane could not survive the structural damage that occurs as a result of a failed propeller blade impact. Such failure was considered catastrophic, and Embraer was granted an exemption from compliance with 14 CFR 25.571(e)(2). The 14RF-9 propeller was certified by the FAA and was approved for unlimited life when maintained in accordance with FAA-accepted Hamilton Standard maintenance instructions; however, the fatigue life of the accident blade was reduced significantly due to a crack that originated from multiple corrosions pits. Corrosion pitting was the result of the reaction between the aluminum of the taper bore, and chlorine contained in the taper bore cork installed during the propeller balancing process. Following the accident, this type of event was further addressed by the additional requirements of 14 CFR 25.905(d).
Common Theme Related Lessons
The use of a borescope as a tool to find/identify small cracks has substantial limitations. Robust non-destructive evaluation methods should ensure that inspected components are returned to service free of defects that can result in hazardous failure events. (Common Theme: Flawed Assumptions).
- The NTSB report noted that the borescope inspection method lacked several critical steps which contributed to the failure to detect the existing crack. The inspection was done without any indirect lighting which could help to outline changes in surface depth of the taper bore. Furthermore, there was no standard procedure to ensure that the entire inner surface was covered by the borescope. It was controlled by hands, so the effectiveness of each inspection was dependent upon each technician's level of experience. The entire inspection process relied heavily on an assumption that the borescope inspection method was adequate and that any evidence of cracks would be detected.
Propellers present a unique safety challenge for transport airplanes due to the potential catastrophic nature of certain types of structural and control system failures. As such, every detail of the propeller design must be clearly identified, and rigorous configuration control maintained throughout the manufacturing, assembly, and repair processes such that no propeller failures are expected to occur in the life of the propeller fleet. (Common Theme: Organizational Lapse)
- This accident was the result of the failure and subsequent separation of a propeller blade, leading to a loss of control of the airplane. Investigators determined that the blade failure occurred as a result of corrosion pitting and subsequent cracking in the taper bore of the propeller. The source of the corrosion pitting was determined to have been chlorine contained in the taper bore cork. The cork was inserted during the blade balancing process to retain the lead wool balancing weight. The chlorine, in the presence of moisture, reacted with the aluminum of the propeller bore and initiated corrosion pitting, leading to the development of a crack that was not detected during propeller inspections. It was concluded by investigators that the presence of the chlorine was not known or detected prior to use of the cork in the taper bore. Configuration control methods should have identified components and substances which would be compatible with the propeller materials, and not result in unintended damage.