McDonnell Douglas DC-10-10
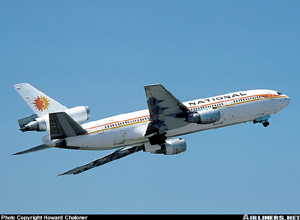
Photo copyright Howard Chaloner - used with permission
National Airlines Flight 27, N60NA
Albuquerque, New Mexico
November 3, 1973
On November 3, 1973, while National Airlines DC-10 Flight 27, from Miami to San Francisco, was cruising at 39,000 feet, the number 3 engine fan assembly completely disintegrated. The number 3 inlet and fan case separated simultaneously with fan blade liberation, allowing the blades to impact the airplane at high speed. The liberated blades struck the fuselage, right wing, engines number 1 and 2, and caused a cabin window to fail. This resulted in the expulsion of one passenger through the opening during the rapid decompression. Many passenger oxygen masks failed to deploy, causing a panic among the remaining passengers.
At the time of the number 3 fan failure, the pilot and flight engineer were experimenting with the relationship between the engine's fan speed (N1) signals and the automatic flight control systems. After the crew heard an explosion and cabin decompression, they declared an emergency and executed an emergency descent. There was an uneventful landing at Albuquerque, New Mexico.
The National Transportation Safety Board (NTSB) determined that the probable cause of this accident was the disintegration of the number 3 engine fan assembly as a result of interaction between the fan blade tips and the fan case. The precise cause of the engine failure was not completely identified during the course of the investigation. Subsequent research by the engine and airframe manufacturers determined that the engine fan and fan case exhibited a vibratory coupling phenomenon that later became known as the "interactive mode."
History of Flight
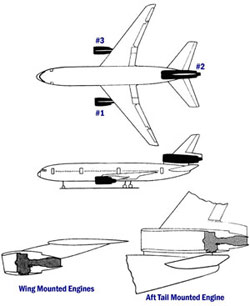
View Larger
On November 3, 1973, while National Airlines DC-10 Flight 27 from Miami to San Francisco was cruising at 39,000 feet, the number 3 engine fan assembly completely disintegrated.
The number 3 inlet and fan case separated simultaneously with fan blade liberation, allowing the blades to impact the airplane at high speed. The liberated blades struck the fuselage, right wing, engines number 1 and 2, and caused a cabin window to fail. This resulted in the expulsion of one passenger through the opening during rapid decompression. Many passenger oxygen masks failed to deploy, causing a panic among the remaining passengers. The engine debris also caused damage to two of the aircraft's three hydraulic systems resulting in loss of all hydraulic fluid for both systems.
At the time of the number 3 fan failure, the pilot and flight engineer were "experimenting" with the relationship between the engine's fan speed (N1) signals and the automatic flight control systems. The pilot and flight engineer appeared to be curious as to where the autopilot/auto throttle received its engine speed signal (i.e., N1 gauge or N1 tachometer generator). The crew reported that their "experiment" was conducted as follows:
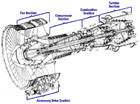
View Larger
- Autopilot selected in airspeed mode - 257 Knots-Indicated Air Speed (KIAS)
- Flight engineer pulled circuit breakers for N1 tachometers on engine numbers 1, 2, and 3
- Target airspeed reduced by five knots
- When throttles retarded, pilot disengaged auto throttle
- Crew then heard explosion and cabin decompression
Photos of damage to aircraft:
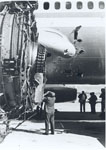
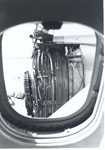
The crew declared an emergency and executed an emergency descent. There was an uneventful landing at Albuquerque, New Mexico.
The oil tank in the number 1 engine had been penetrated by fan blade debris and upon landing had lost all oil, and the number 1 engine constant speed drive generator line was severed. Engine number 2 ingested fan debris and sustained minor foreign object damage. The failure of a substantial number of oxygen masks to deploy appeared to result from multiple electrical failures.
Analysis of cockpit voice recorder data shows that the number 3 engine accelerated from 97% N1 to 100% N1, fluctuated for a few seconds and failed at 100%. The flight data recorder was inoperative. Engines number 1 and 2 also accelerated from 97% N1 to a maximum of 107% N1.
The photo to the right is the number 1 engine cowl showing impact damage from the number 3 engine debris. Engine debris penetrated the oil tank resulting in total loss of engine oil upon landing.
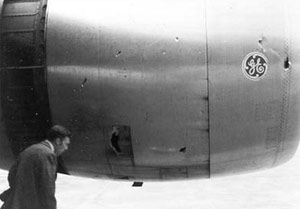
Engine Failure Scenario
The initial triggering event was not completely understood during the course of the investigation, due to the complex nature of the vibratory phenomena later identified. The investigation centered on vibratory characteristics of the fan blades and fan case. All parties did not agree on the initiating event. The question remained, "Did the inlet failure cause tip rub?" or "Did tip rub cause the inlet failure?" There was general agreement that the failure mechanism somehow involved a fan case 6th order wave mode traveling at one half the fan speed in the direction of fan rotation.
It was also agreed that the fan blade assembly fore and aft rocking vibratory mode was a contributor to the failure mechanism. This rocking mode also involved a 6th order traveling wave shape at one half fan speed in an opposite direction to the fan.
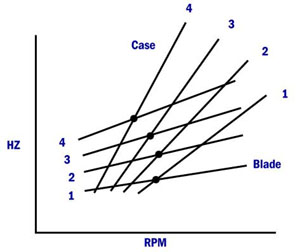
It was also agreed that the fan blade assembly fore and aft rocking vibratory mode was a contributor to the failure mechanism. This rocking mode also involved a 6th order traveling wave shape at one half fan speed in an opposite direction to the fan.
The investigators concluded that both conditions had to be present for a massive engine failure such as this to result:
- A coincident and coupled fan case wave and blade "rocking" wave mode, and
- Fan blade tip rub.
Note: All large, high bypass, fan engines commonly experience fan tip rubs, especially early in service. High "g" aircraft maneuvers, high physical fan speeds, and other operating conditions where tip clearances are reduced due to component deflections can result in minor abrasion of tip shroud material, or "tip rubs". This "wearing in" of fan and inlet components is an expected condition, and is intended, in order to establish "final" tip clearances between the blades and fan case. This clearance is also very significant in establishing installed engine thrust.
The concept of sympathetic vibratory modes is illustrated in this diagram, known as a Campbell Diagram, showing the vibratory frequencies of various components plotted in overlay - in this case, a fan case and fan blades, and their vibratory modes up to 4th order. The components have various vibratory frequencies that are generally independent of each other. However, where the lines intersect, the modes are sympathetic, and if fan blades and fan case come in contact, a divergent feedback process results in a catastrophic energy release. In this accident, the fan blades and fan case were vibrating in sympathy with one another, each at 6th order, and their contact caused the destruction of the forward section of the engine.
View CF-6 Vibratory Characteristics Animation below:
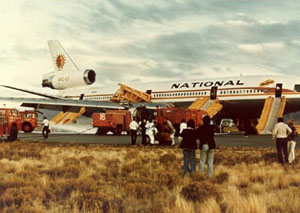
During this accident, the maximum speed of the fan rotor on the number 3 engine when it failed was determined to be approximately 100% which is below the maximum red line speed of 111%. Had the number 3 engine not failed on the National Airlines flight, it was believed that eventually a similar vibratory condition would have been experienced in service with similar catastrophic results.
Although the flight crew was experimenting with the aircraft systems and not following an approved procedure, the root cause of the failure was not the improper flight crew actions in the cockpit, but a design problem with the engine fan, fan case and inlet combination.
The NTSB determined that the probable cause of this accident was the disintegration of the number 3 engine fan assembly as a result of interaction between the fan blade tips and the fan case. The fan-tip rub condition was caused by the acceleration of the engine to a fan speed which resulted in the fan tip and fan case making physical contact (i.e., "tip rub"). This physical contact permitted vibratory coupling to exist between the fan blades and fan case, resulting in very high energy being exchanged between the two components and the eventual fan blade liberation from the fan hub.
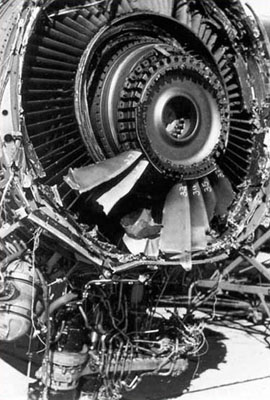
The precise reason or reasons for the acceleration and the onset of the destructive vibration could not be conclusively determined during the course of the investigation. Subsequent to the investigation, extensive research identified the precise
causes of the vibratory responses of the engine components and identified effective solutions to mitigate other occurrences.
The NTSB identified 14 findings for this accident in report NTSB-AAR-75-2. The findings addressed:
- Certification, qualification and maintenance of the crew and the aircraft
- Actions by the crew in relation to the N1 tachometer circuit breaker and the engine operating above normal conditions
- Damage to the aircraft caused by the liberation of 32 of the 38 fan blades
- Damage to the wiring and loss of electrical power
Select this link to view the detailed NTSB Findings. Select this link to view the entire NTSB Report.
The NTSB issued nine safety recommendations to the FAA. Select the link to view the detailed NTSB Safety Recommendations and corresponding FAA responses.
Three of the recommendations (A-73-116, -117, and -118) pertain to the inspection and maintenance of digital flight data recorders. During the accident investigation, the digital flight data recorder from the National Airlines airplane was found to be defective and no meaningful data could be retrieved.
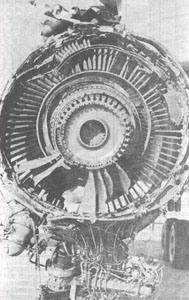
Five recommendations (A-74-7 thru A-74-11) concern the passenger and portable oxygen systems installed in the DC-10. The accident revealed deficiencies relative to the installation of the cabin oxygen generating units, functionality of the system and accessibility of portable oxygen units in the cabin. In addition, it addressed the possibility that separate pressure losses of different magnitudes may occur on the DC-10 and the need of separate aneroid devices.
One final recommendation pertains to the assessment of aircraft damage by flight crews during in-flight emergencies. The NTSB investigation identified that National Airlines did not have a procedure for crew members to assess the damage to the airplane in an emergency situation. After the emergency was under initial control, the cockpit crew did not assess the extent of damage to the airplane or the condition in the cabin.
Immediately following the accident, the FAA issued a telegraphic Airworthiness Directive (AD) that applied to all DC-10 aircraft. The AD required inspection of the engine nose cowl mounting integrity and correction of any possible deficiencies. Also, it was recognized early that fan-tip rub was a necessary condition in the sequence of events that brought about the loss of the fan blades.
As a preventive measure against the recurrence of this type of condition, the fan blade tip-to-shroud clearances were increased. As backup for the possibility of blade-tip rub even after the tip clearance was modified, an extensive development, testing, and production program was established to increase the capabilities of the blade retention devices. The blade retention devices were redesigned with increased capability of more than three times the original configuration. These modified blade retention devices were incorporated in all revenue service engines.
In the accident report, the NTSB addressed the flight crew performance of an experiment with the auto-throttle/speed control system. The NTSB stressed that the operator and the pilot in command should be fully cognizant of their operational responsibilities to conduct the flight in a professional manner and not to conduct experiments with aircraft systems in which they have not received specific training or instruction.
The following Federal Aviation Regulations were pertinent to the DC-10 design and certification:
14 CFR 25.1447 - Equipment Standards for Oxygen Dispensing Units
14 CFR 25.903 (d)(1) - Minimize hazards to the airplane from engine rotor failure
14 CFR 25.1585 (a)(4) - Operating Procedures
14 CFR 33.94 - Blade Containment and Rotor Imbalance Test
The following Air Carrier Operations regulations were pertinent:
121.343(a)(1),(2) - Flight Recorders
At the time of the accident, the McDonnell-Douglas Model DC-10 was relatively new in airline service. The airplane design also incorporated relatively new technology in many systems with which flight crews were unfamiliar. Just prior to the fan separation event, the flight crew was discussing the autothrottle system, and where the engine rotor speed signals for the autothrottle originated. This discussion led to a quickly organized experiment to determine the signal source. The experiment resulted in all three engines accelerating to speeds which had not been commanded by the flight crew and had the immediate effect of initiating the interactive mode on the number 3 engine and the rapid separation of the inlet and fan.
Experimentation of this type, while not authorized, has been noted during the course of other investigations involving new aircraft and/or technologies. Knowledge of system interactions and basic system function is important for a flight crew and fundamental to the proper conduct of flight operations. However, it is more appropriately conducted during initial aircraft evaluation and dedicated flight testing, not revenue service. This flight crew, while exercising their normal curiosity about their airplane, inadvertently triggered an unexpected event that led to the destruction of one engine and the accident sequence of events.
The key safety issues identified as a result of this accident are:
- The destructive "interactive" fan blade and fan case vibration mode within the engine operating envelope.
- The number 3 engine failure resulted in a large number of complete fan blades (nearly every blade) being released from the fan disk at high speed coincident with the fan containment case separating from the engine. This reduced its effectiveness in containing the engine debris and minimizing the hazard to the aircraft. High energy uncontained engine debris caused damage to the aircraft.
- Not all passenger masks were presented at the same time, some taking as long as three minutes to deploy after the decompression. In addition, three oxygen canisters were improperly mounted. As a result, the canisters fell in the passenger seat cushions, burning the fingers of a crew member when she tried to remove them and severely scorching the seat upholstery.
- Portable oxygen bottle storage and availability was inadequate and resulted in two flight attendants losing consciousness.
- Separate pressure losses of different magnitudes occurred throughout the airplane and the aneroid device - which detects unacceptable cabin pressure altitude and deploys the oxygen masks - was only located in the forward passenger cabin. This prevented supplemental oxygen from being available to the occupants in the lower galley.
The following design and safety assumptions are relevant to this accident:
- There were no harmful interacting vibratory modes existing within the engine operating range
No. 3 engine and punctured fuselage - Based on the engine's design and certification standards, the engine structure would contain damage resulting from a single rotor blade failure at the outermost retention groove
- Per oxygen dispensing unit regulations, oxygen would be immediately and easy accessible to all passengers and crew members
- Portable oxygen bottles would be immediately accessible for each cabin attendant
- Pressure loss would be of equal magnitude throughout the airplane. The aneroid would detect unacceptable cabin pressure throughout the entire airplane equally
On November 15, 1972, American Airlines experienced a CF6 engine failure during test cell operation. The bellmouth and exhaust cone separated, and all fan blades were liberated. The failure investigation focused on the cause of the failure as being the improper installation of the bellmouth to the engine, specifically the installation of the bolts by American Airlines. It was eventually determined that the bellmouth had been properly installed, and the failure had been a result of the interactive mode.
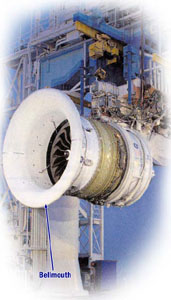
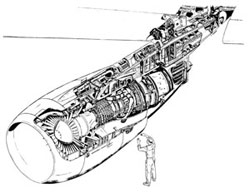
View Larger
On January 12, 1973, GE Aircraft Engines (GEAE) experienced a similar failure of a highly instrumented CF6 engine (engineering test) during test cell operation. This failure was initiated by the rubbing between the fan rotor and casing and resulted in damage similar to the other occurrences. The engine test cell was substantially damaged.
The GEAE engine was instrumented and was undergoing engineering tests in part as a result of the previous American Airlines test cell failure. At the time, these failures were not fully understood and the risk for a repeat event to a revenue service engine was not recognized.
No specific regulatory changes resulted directly from this accident; however some design changes were made, and industry practices were modified as follows:
Engine/Airplane Design Changes:
The number of inlet cowl brackets was increased from 12 to 21.
Blade axial retention was increased from 18,000 to 60,000 pounds-force ultimate.
Fan blade/case tip clearances were increased.
GE Service Bulletin 72-396 was incorporated prior to the accident and complemented the service bulletin that increased the fan blade/case tip clearance.
GEAE Design Practice:
GEAE engine design practice was updated to incorporate lessons learned regarding fan rotor and case harmful interactive vibratory modes.
Advisory Material:
This accident provided data and information relative to engine fragment spread angles that were used for development of FAA Order 8110.11, titled "Design Considerations for Minimizing Damage Caused by Uncontained Aircraft Turbine Engine Rotor Failures," dated November 19, 1975.
The information in this order was subsequently revised and issued in AC 20-128A, including Appendix 1.
The following airworthiness directives were issued as a result of this event:
Engine:
No airworthiness directives were issued on the engine.
Airplane:
Telegraphic AD issued November 7, 1973, that applies to DC-10-10, -30, -30F series aircraft. The AD required inspection of nose cowl bolts on DC-10 wing-mounted engines. AD 73-26-04 became effective on December 19, 1973, and incorporates the requirements of the telegraphic AD.
AD 75-04-03 became effective on February 14, 1975, and required improvements to the DC-10 cabin oxygen mask deployment system. Before the National Airlines accident, the FAA was working with McDonnell Douglas on improving the DC-10 cabin oxygen mask deployment system. This accident resulted in the higher prioritization of this activity and contributed to the issuance of AD 75-04-03.
McDonnell Douglas Service Bulletins referenced in AD 75-04-03:
Douglas All Operators Letter No. 10-742
Douglas Service Bulletin No. 25-163
Douglas Service Bulletin No. 35-12
Douglas Service Bulletin No. 35-16
Airplane Life Cycle:
- Design / Manufacturing
Accident Threat Categories:
- Pressurization / Decompression Failures
- Cabin Safety / Hazardous Cargo
- Uncontained Engine Failure
Groupings:
- Automation
Accident Common Themes:
- Organizational Lapses
Organizational Lapses
Prior to this accident, there were two incidents during engine ground tests that were precursors for the inflight event. General Electric and McDonnell-Douglas each began work to identify and resolve what, at the time, was believed to be a single failure mode. It wasn't until after the National Airlines accident that the interdependent nature of the failure was understood, and a "coupled" solution was applied that involved changes to both engine and airplane hardware.
Prior to this accident, there was no record of a similar failure condition involving the "interactive mode" on any turbofan or turbojet installation.
Technical Related Lessons:
Large high bypass engines can exhibit hazardous mechanical interaction between vibratory modes of the fan blades and fan case, with the potential for catastrophic uncontained engine failure. (Threat Category: Uncontained Engine Failure)
- In this accident, harmful vibratory modes between the fan blades and fan case, within the engine operating envelope, resulted in the engine inlet bolts failing and a number of fan blades being released, striking the airplane. Although all large high bypass engines have fan case and fan blade vibratory modes, it is important that they do not exhibit a common vibratory frequency and order (e.g., fifth order, sixth order, etc.) at a fan speed within the operating range of the engine.
Hazardous deterioration of pressure anywhere in the passenger cabin should be rapidly detected and result in timely deployment of all passenger oxygen masks. (Threat Category: Cabin Safety/Hazardous Cargo and Pressurization/Decompression Failure)
- During the rapid decompression, many passenger oxygen masks were delayed in deploying or failed to deploy, causing panic among the passengers. The delay was caused by the severe damage to the number 3 nacelle which contained the number 3 electrical buses. This partial loss of power affected the depressurization warning system and some of the masks in the automatic oxygen deployment system.
- One liberated blade struck a cabin window which caused it to fail and the cabin to experience a rapid decompression, resulting in a pressure differential between the main cabin and the lower galley. This made the decompression profile steeper for the lower galley, and it decompressed faster. The single aneroid device, which detects unacceptable cabin pressure altitude and deploys the oxygen masks, was located in the forward passenger cabin. This prevented the supplemental oxygen from being immediately available to the occupants in lower galley.
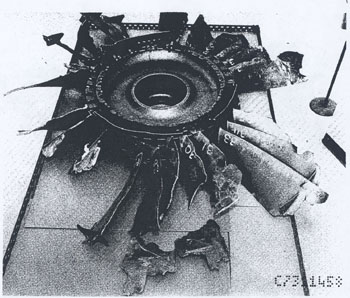
Common Themes Related Lessons:
It is essential that major service incidents are understood and resolved in a timely manner in order to avoid an additional incident or accident due to this same condition. (Common Theme: Organizational Lapses)
- Prior to this accident, two CF6 engine fan failures had occurred due to this same vibratory condition, both resulting in fan assembly disintegration identical to the National Airlines accident. Although both occurred during test cell testing, understanding their failure modes, recognizing the potential for similar failures during flight, and implementing timely and effective intervention, is critical in order to avoid in-service failures which could lead to an accident.