McDonnell Douglas DC-10-10
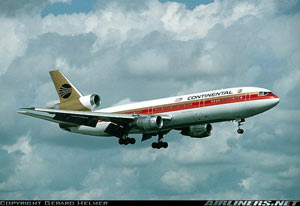
Photo copyright Gerard Helmer - used with permission
Continental Airlines Flight 603, N68045
Los Angeles, California
March 1, 1978
At approximately 0925 Pacific Standard Time on March 1, 1978, Continental Airlines Flight 603, a McDonnell Douglas Model DC-10-10 airplane, overran the departure end of Runway 6R at Los Angeles International Airport, California following a rejected takeoff. As the airplane departed the wet, load-bearing surface of the runway, the left main landing gear collapsed, and fire erupted from the wing area. The airplane slid to a stop approximately 664 feet beyond the departure end of the runway. The left side of the airplane was destroyed. Of the 184 passengers, two infants, and 14 crewmembers on board, two passengers were killed, and 28 passengers and three crewmembers were seriously injured during the evacuation of the airplane.
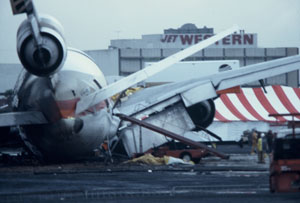
On March 1, 1978, a Continental Airlines McDonnell-Douglas DC-10, operating as Flight 603, overran the runway at Los Angeles International Airport (LAX) during an attempted rejected takeoff (RTO). At the time of the accident, the runway surface was wet, although the surface is also grooved to aid in wet runway braking. During the takeoff acceleration the Nos. 1 and 2 tires failed, nearly simultaneously, leading to RTO initiation just prior to reaching V1. The airplane departed the runway surface, collapsing the left main landing gear. Gear Failure led to a fuel leak, and fire, which consumed the left side of the airplane (landing gear configuration).
The National Transportation Safety Board (NTSB) determined that the probable cause of the accident was the sequential failure of two tires on the left main landing gear and the resultant failure of another tire on the same landing gear at a critical time during the takeoff roll. These failures resulted in the captain's decision to reject the takeoff. Contributing factors to the accident were 1) the cumulative effect of the partial loss of airplane braking because of the failed tires and 2) the reduced braking friction achievable on the wet runway surface which increased the accelerate-stop distance to a value greater than the available runway length. These factors prevented the captain from stopping the airplane within the runway confines.
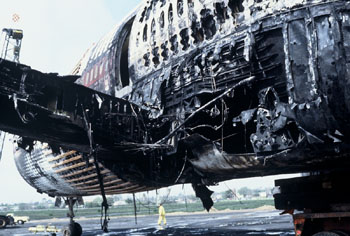
The digital flight data recorder (DFDR) showed that the tires failed just before the airplane accelerated through 152 knots, about four knots below the calculated takeoff decision (V1) speed. The DFDR further showed that the captain reacted promptly to the tire failures and began rejected takeoff procedures. However, he was not able to stop the airplane within the remaining runway distance.
Post investigation of the failed tires showed that the accident was initiated by the nearly simultaneous carcass failures of the two tires mounted in the No. 1 and No. 2 positions. Since these tires were mounted on the same axle, the 97,920 lb. load on the axle was distributed between the two tires.
The first tire failed at the No. 2 tire position approximately 6,300 ft. from the departure end of Runway 6R. The tire failed because of a thrown tread. The carcass blew about 4,520 ft. from the departure end of the runway.
The second tire failed at the No. 1 tire position about 4,480 ft. from the departure end of Runway 6R after the No. 2 tire carcass blew out. Fatigue in the ply structure may have been caused by long-term overload since the tire was mounted on an axle with a tire of a different brand that had less sidewall stiffness. The tire blew out because of an overload.
The third tire failed at the No. 5 tire position about 3,400 ft. from the departure end of Runway 6R. Pieces of the wheel rim from either the No. 1 or the No. 2 wheel hit the tire and caused it to blow out. This blowout further affected the airplane's braking capability. Also, the left main landing gear might not have collapsed if the No. 5 tire had been available to distribute load on the overrun area.
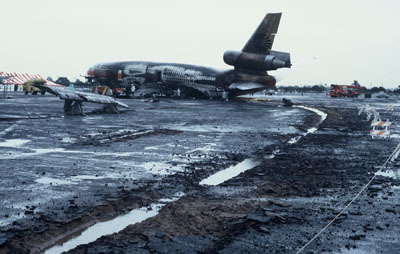
The tires on the airplane may have been operated in an over-deflected condition, since the average inflation pressure was less than the optimum pressure for maximum gross weight.
Both the No. 1 and No. 2 tires were on their third retread cycle, a limit which was set by the airline based upon prior experience with unscheduled removal of tires on Model DC-10-10 airplanes. The two tires had been manufactured by different companies and had different design characteristics. Both, however, met all specifications set forth in FAA regulations for certification. Tire No. 2 had been subjected to more total landings than tire No. 1 and its tread was worn about 40 percent more. The pressure of both tires had been checked three hours before the accident, and the NTSB has no evidence to indicate that either tire was inflated below the limits allowed by the operator during the taxi and takeoff roll immediately preceding the accident. However, the No. 2 tire had the lower pressure of the pair, which shifted load to the No. 1 tire.
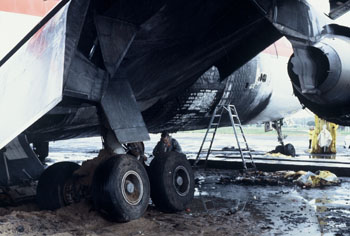
Tests conducted at the Department of Transportation's (DOT) Tire Laboratory did not disclose evidence of defects in the retread manufacturing process that could have explained the separation of tread from the No. 2 tire carcass. Examination of the tire did show that repair patches had been installed on the tire's liner when the tire was originally manufactured. The NTSB believed that these patches may have lost their sealing capability either just before or during the accident sequence. If so, either of two possibilities could explain the tread separation. First, the leakage of air under the tread was sufficient to cause the tread to separate without being sufficient to detect during checks, or second, the tire liner had lost its integrity and external leakage was causing over-deflected operation during the takeoff roll. Over-deflection could have produced a standing wave behind the footprint that led to tread separation.
Another possible tire failure sequence may have been that the No. 1 tire became under inflated during the taxi/takeoff cycle for some undetermined reason. The selection of tires for an airplane is based upon the assumption that each tire will carry its share of the load. Further, it is assumed that the load will be equally distributed between the tires mounted on the same axle. The tires' rated loads, as established by the tire manufacturer, must therefore equal half of the maximum calculated static load carried by the axle. Thus, when one of the two tires fails, the remaining tire must support the entire axle load, which can be nearly double the tire's rated load. Although the tire is probably capable of supporting this load, statically, it will be seriously over-deflected and dynamic operation will cause a rapid temperature rise in the sidewall.
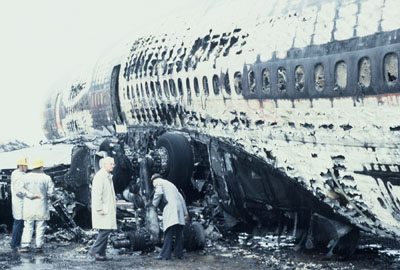
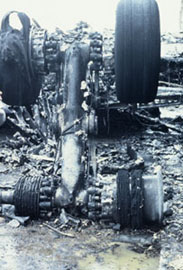
In this instance, the No. 2 tire would have then been overloaded and over-deflected which could result in tread loss followed by carcass blowout. Failure of the No. 2 tire alone probably would not have affected the airplane's accelerate-stop performance to the extent that an accident was inevitable. The NTSB believed that had the No. 1 tire not suffered previous degradation, it would have been capable of operating for a longer period than evident in this accident. The examination of the tire's carcass disclosed advanced fatigue in the ply structure. In addition, there was evidence of severe cord overheating near the sidewall bead area, and several other areas of the sidewall showed evidence of very high temperatures. Such conditions are typical of those produced by overload or over-deflected operation for a prolonged period of time.
Although the NTSB could not determine when such damage was inflicted, it was concerned that the airframe and tire design, as well as operational and maintenance procedures, could have combined to cause prolonged operation of tires in an over-deflected or overloaded condition. Normal differences between two tires on the same axle, particularly if they are of different designs, could preclude them from carrying equal loads. The NTSB believed that the preexisting damage in the No. 1 tire was a factor in causing it to ultimately fail almost immediately after the No. 2 tire failed, and thus, the preexisting damage may have been a causal factor.
Rejected Takeoff Performance
DC-10 LAX - Rejected Takeoff Scenarios Animation:
Although the flight crew rejected the takeoff before V1 was attained, and used all of the available deceleration devices, the airplane overran the end of the wet, grooved 10,285-foot runway at 68 knots.
The NTSB believed that this accident illustrated a number of shortcomings in the certification of airplanes and in the training of flight crews to effectively accomplish rejected takeoffs (RTO) under the most critical conditions of speed, weight, runway condition, and the reasons for initiating RTOs.
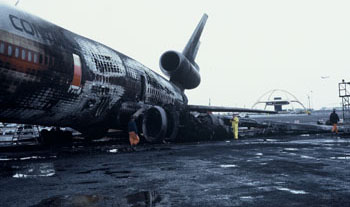
Part 25, "Airworthiness Standards: Transport Category Airplanes" (14 CFR part 25), defines the certification requirements for normal takeoffs and RTOs. The associated takeoff speeds, and accelerate-stop distances, are predicated on recognition of an engine failure not later than V1, on a smooth, dry, hard-surfaced runway. Certification/operational criteria have generally considered an engine failure at V1 to be the most critical situation with regard to stopping the airplane within the confines of the runway surface. Newer regulatory amendments require the consideration of wet runways for accelerate-stop performance. Certification requirements at the time of the accident did not (and still do not) address the cumulative effects of failed tires and wet runway surfaces, each of which may add a considerable stopping distance increment to that presently required to demonstrate stopping distance requirements.
In contrast to 14 CFR part 25 certification requirements, 14 CFR 121, "Operating Requirements: Domestic, Flag, and Supplemental Operations," prior to the accident, provided an operational safety-stopping margin for landings on wet runways. A landing airplane is required to stop on a dry runway within 60 percent of the effective runway length. The runway length used for this calculation is increased by 15 percent for wet or slippery conditions. In effect, 14 CFR part 121 establishes a wet runway length that is approximately twice the distance demonstrated for stopping the airplane during dry runway certification tests. However, even though 14 CFR Part 121 includes corrections to takeoff weights, stopping distances, and flight paths to account for the effects of density altitude, wind, and runway slope during normal and rejected takeoffs, it does not require similar adjustments to RTO stopping performance on wet or slippery runways.
In FAA report "Jet Transport Rejected Takeoffs, Final Report, February 1977, Flight Standards Services", the FAA indicates that 87 percent of RTOs were caused by some failure or malfunction of tires, wheels, and brakes, and that engine failures have not been the dominant cause. Airplane stopping distances significantly increase as a result of tire, wheel, or brake failure because the ability to develop or transmit braking torque to the runway surface is reduced. Despite causing 87 percent of RTOs, the effects of these failures were not considered in calculating stopping distance. The FAA report "Trans World Airlines, Inc., B-707, N69TW, Fiumicino Airport, Rome, Italy, November 23, 1970," cites wet or slippery runway involvement in three major RTO accidents between 1964 and 1975. The FAA report recommends that "The increased accelerate-stop distance required on wet, slippery runways be taken into account in takeoff calculations and the necessary changes to airplane flight manuals, procedures, and regulations be incorporated to accommodate this." The NTSB determined that no FAA actions had been taken before the Flight 603 accident concerning this recommendation.
A "Pilot Guide To Takeoff Safety" training guide was published in 1992 as a result of a combined industry and FAA team effort. This training guide, used as an industry standard aid to train pilots at several major U.S. airlines, points out some of the lessons that have been learned through the RTO experiences of other airline flight crews over the past 30 years and recommends ways of avoiding similar experiences by the pilots of today's airline fleet. The training guide cites poor pilot decision making and understanding of the go/no-go decision process as contributing factors to numerous unnecessary RTOs.
An analysis of 74 RTO accidents and incidents suggests that in approximately 55 percent of the events, the airplane was capable of continuing the takeoff and either landing at the departure airport or diverting to an alternate location. Approximately 80 percent of the RTO accidents and incidents were potentially avoidable through appropriate operational practices. Since the issuance of the 1977 report, the FAA indicates that the incidence of RTOs for these same causes has been reduced to approximately 23 percent.
In 1962 the British Civil Aviation Authority (CAA) changed the British Civil Airworthiness Requirements (BCAR), counterpart of 14 CFR part 25, to account for the increased accelerate-stop distance necessitated by wet runways during engine-out conditions. The BCARs defined a wet runway reference surface to be used during landing and RTO certification testing. This standard represents an average wet, well-soaked surface that typifies the condition of Runway 6R at the time of the Flight 603 accident. There was no FAA counterpart to the BCAR wet runway standard, although U.S. manufacturers were testing under the BCAR wet requirements in order to certificate airplanes in foreign countries. The V1 data for wet runway conditions are determined from these tests and provided to non-US flight crews. The BCAR procedures reduce the dry runway V1 decision speeds so that an RTO initiated at the lower wet V1 speed will allow the airplane to stop on the wet runway as long as the actual surface condition is no worse than the reference surface. The BCAR also reduced the wet runway screen height requirement from 35 feet, the FAA standard, to 15 feet. The BCAR, however, retained the requirement for the 35-foot screen height for takeoffs on dry runways. The screen height is the vertical distance above the runway where the takeoff safety airspeed (V2) is reached with a failed engine. This reduction in screen height for the Model DC-10 imposes no weight penalty on the operator. The NTSB did not attempt to evaluate the adequacy of the British CAA approach but recognized that lower V1 speeds or lower takeoff weights, or both, for wet runway conditions will improve airplane stopping performance.
During the investigation of the Flight 603 accident, the NTSB learned that one Model DC-10 operator at Los Angeles had routinely and voluntarily accounted for the added wet runway stopping distance for over five years by reducing V1 speeds and takeoff weights for its Model DC-10 airplanes. The reduction in weight is required because of the current FAA 35-foot screen height standard. For the Flight 603 accident, the wet V1 speed would have been 149 knots, 7 knots lower than the dry V1 speed (156 knots), and the takeoff weight would have been reduced by about 10,000 pounds. Under these conditions, a successful takeoff or RTO by the Flight 603 might have been possible.
The NTSB's investigation of flight crew training practices regarding RTOs revealed that most training is given in simulators under unrealistic conditions. For example, most simulated RTOs are not initiated at maximum takeoff weights and associated V1 speeds, and few simulators have the capacity to measure the flight crew's braking efficiency. In the latter respect, a simulation test conducted by NASA and Douglas Aircraft Company demonstrated that air carrier pilots who were told to apply maximum braking during simulated RTOs actually achieved this only 60 percent of the time.
The FAA acceptance standards for airplane simulators used in pilot training are set forth in Advisory Circular (AC) 121-14, "Aircraft Simulator Evaluation and Approval." This AC contains accuracy criteria for takeoff performance characteristics, but it does not contain deceleration criteria for dry, wet, or slippery runways. Additionally, it does not provide a measurement of pilot braking response time, or the amount of braking effort required when attempting to stop airplane during high-energy RTOs on critical length runways.
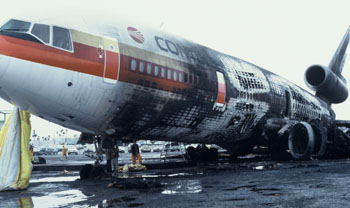
Pilot training in actual RTOs requiring maximum energy stops is by necessity limited to discussion and simulation. In some cases, simulator training may provide a false sense of security to the pilot by reflecting airplane performance in excess of that actually available for stopping on wet runways. The NTSB believed that when simulators are used for such training, they should demonstrate the actual performance, particularly where the simulator provides visual and acceleration cues. Furthermore, all simulators should be equipped with sufficient instrumentation to enable instructors to evaluate the pilot's performance in executing an RTO, particularly the response times in activating stopping devices and the level of brake application to ensure that such performance is compatible with a minimum-distance stop.
The RTO procedures in the Continental DC-10 airplane flight manual specified that brakes should be applied "as required" after retarding the throttles to idle. Reverse thrust was to be applied "as required" following brake application. These procedures were applied universally, regardless of takeoff gross weights or airplane speed during an RTO. In contrast to the Continental procedures, a Douglas DC-10 newsletter issued in August 1977 discussed the urgency of the situation when RTOs were initiated near V1 speed. The newsletter recommended using maximum brake pedal deflection and applying full reverse thrust simultaneously and as soon as possible.
The Flight 603 flight crew stated that the airplane acceleration was normal and that all engine instruments were in the normal range during takeoff. As the airspeed approached the V1 speed of 156 knots, the captain heard a loud "metallic bang" which was followed immediately by "a kind of quivering of the plane." The flight crew noticed that the left wing dropped slightly.
An RTO was begun immediately; however, according to the DFDR, the airspeed continued to increase to about 159 knots as the RTO procedures were begun. The captain stated that he applied full brake pressure while simultaneously bringing the thrust levers back to idle power. Reverse thrust levers were actuated and full reverse thrust was used. The flight crew stated that they noted good reverse thrust.
The airplane moved to the left of the runway centerline and appeared to the flight crew to be decelerating normally. With about 2,000 feet of runway remaining, the flight crew became aware that the rate of deceleration had decreased, and they believed that the airplane would not be able to stop on the runway surface. The captain stated that he maintained maximum brake pedal force and full reverse thrust as he steered the airplane to the right of the runway centerline in an effort "to go beside the stanchions holding the runway lights" immediately off of the departure end of Runway 6R. He stated further that he encountered no problems with directional control of the airplane throughout the RTO maneuver.
Fuel Tank Rupture and Fire
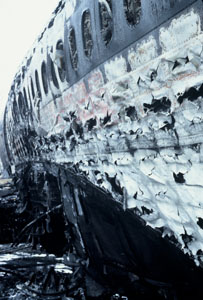
DC-10 Flight 603 fire damage
Shortly after the airplane ran off the departure end of the runway, the left main landing gear broke through the macadam surface of the overrun area and failed. The increased footprint pressure exerted by the No. 6 tire and the load from the No. 1 and No. 2 wheels was beyond the macadam's support capability.
When the Model DC-10 was certificated, the FAA required that the landing gear attachment be designed so that, if it failed because of up and aft overload, no part of the landing gear structure could puncture any part of the fuel system. The manufacturer, McDonnell-Douglas, satisfied this requirement. In four other accidents, the landing gear on the Model DC-10 had failed with no wing fuel tank rupture; however, in this case, the loads imposed upon the left main landing gear exceeded design loads. As a result, some of the landing gear attachment structure failed in an unusual mode and a large hole was torn in the aft web of the rear spar in the left wing at the juncture of the two main fuel tanks in the left wing. The fuel that was released through this rupture was the major contributor to the extensive post-crash fire.
The NTSB was not able to determine conclusively where or when the fire started. Statements of some passengers and flight attendants indicated that fire may have been present in the area of the left main landing gear wheels before the airplane left the runway surface. The escape of hydraulic fluid and the friction heat developed from rubber and metal contact with the runway surface could have ignited a fire. Fire engulfed the left side of the airplane immediately after the left main landing gear failed. This fire continued until extinguished by the Los Angeles Airport Fire Department.
Evacuation Slides
Because of the intense fire on the left side of the airplane, passengers exited from the right side. All cabin exit doors were opened and all slide/rafts, except the left forward (1L) exit, were deployed. Apparently, the door at exit 1L was opened in the emergency mode with the slide deployment mechanism disarmed. When the captain and a male passenger attempted to attach the slide/raft, it was pulled from its door container and fell to the ground.
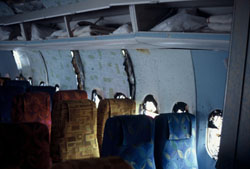
The slide/rafts that were deployed from the four right side emergency exits were exposed to fire and radiant heat. All of these slide/rafts failed before the evacuation was completed. Passengers and crewmembers that were still in the airplane when all slide/rafts had failed either jumped to the ground or slid down the escape rope from the first officer's side window in the cockpit.
The primary purpose of an emergency evacuation system is to provide for rapid passenger and crew egress from an airplane under emergency conditions. However, the investigation disclosed that when these slide/rafts were certificated as a part of the Model DC-10 airplane, no consideration was given to the slide/rafts serviceability when exposed to radiant heat.
The girt fabric on the right rear exit (4R) slide/raft tore loose and failed because of an apparent overload when passengers went onto the slide/raft faster than those at the bottom of the slide/raft could leave it. This unusual passenger flow resulted from the combined effects of 1) the shallow deployment angle of the slide/raft, and 2) a design feature inherent with the slide/raft concept.
For the slide/raft to function as a raft, the sides and ends must be raised above the level of the slide/raft floor. Therefore, the unit is constructed with inflatable tubes along both sides and across both ends. The slide surface and raft floor is attached inside this inflatable, rectangular framework. The surface that the evacuee slides on slopes from atop the inflated tube at the head end (airplane end) down to the center section of the unit. This center section that serves a dual purpose (raft floor and slide surface) is attached near the bottom of the sidewall inflatable tubes. A few feet from the tail end (outboard end) of the unit, the sliding surface slopes upward from this center section to the top of the inflatable tube that crosses the tail end of the unit. Thus, when the slide/raft is deployed from a normal doorsill height, the sloped section at the tail end of the slide surface acts to decelerate the evacuee. However, when the slide/raft is used from a lower-than-normal sill height, as was the case in this accident, the sloped surface becomes an obstacle that must be climbed over by the evacuee.
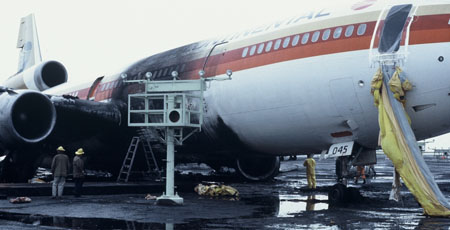
The 26-foot slide/rafts were fabricated with side sections that allow increased seating capacity when used as a raft. Passengers' shoes and other personal articles were found in these side sections indicating that some passengers exited the slide/raft via the side. The girt width of the 26-foot-long slide/raft was about 42 in. The slide width was about 172 in. Extreme asymmetrical loading of the girt was therefore possible if passengers attempted to exit via one side of the slide/raft.
The NTSB believed that the success of the emergency evacuation of the passengers, most of whom were elderly, was the direct result of the efforts of the entire flight crew and cabin crew and that of a Continental Boeing Model 727 captain who was on board as a passenger. Their immediate response and their initiative in seeking alternate escape routes when the normal routes were rendered useless undoubtedly saved lives and decreased the number of injuries.
The NTSB issued 36 findings ranging from the accident event sequence to runway surface conditions and the failure of the main landing gear. The complete text of the findings, including the NTSB’s identification of probable cause, is available at the following link: (NTSB findings)
The complete text of the NTSB accident report is available at the following link: (Accident Report)
On September 6, 1978, the NTSB issued eight initial recommendations to the FAA. These recommendations concerned tire rating criteria, in terms of compatibility of tire, airframe, and intended operation to assure that adequate margins are provided for all normal conditions. Other tire recommendations included upgrading the Technical Standard Order (TSO-62b) to reflect current engineering practices and operational conditions in both performance and certification requirements. Improve retread tire requirements and inspections, operator maintenance and operational practices. Finally, prohibit different model tires or tires manufactured by different manufacturers from being mounted on the same axle.
On November 17, 1978, the NTSB issued six additional recommendations to the FAA. These recommendations concerned revising the accelerate-stop criteria required to be demonstrated during aircraft certification to include the effects of wet runway conditions and worn brakes. Pilot training were also to include appropriate information regarding optimum rejected takeoff procedures at maximum weights, on wet and dry runways, at speeds near V1.
These recommendations were followed up with five additional NTSB recommendations on May 1, 1979. These additional recommendations required:
- Improvements to evacuation slide/rafts material to withstand radiant heat
- Increase slide/raft girt fabric material strength
- Require dual lane to increase passenger evacuation rate
- Include slide/raft devises and requirements in TSO
- Require a secondary means of escape at all floor level cabin exits that have evacuation slide/rafts
The complete text of the recommendations, excerpted from the NTSB report are included at the following link: (NTSB recommendations, Slide raft NTSB recommendations).
Accelerate-Stop Distance
Section 91.605, "Transport category civil airplane weight limitations," (14 CFR 91.605)
Section 25.101, "General," (14 CFR 25.101)
Section 25.105, "Takeoff," (14 CFR 25.105)
Section 25.109, "Accelerate-stop distance," (14 CFR 25.109)
Section 25.113, "Takeoff distance and takeoff run," (14 CFR 25.113)
Section 25.115, "Takeoff flight path," (14 CFR 25.115)
Section 25.733, "Tires," (14 CFR 25.733)
Section 25.735, "Brakes," (14 CFR 25.735)
Section 25.1587, "Performance information," (14 CFR 25.1587)
Amendment 25-42, Issued on January 9, 1978 (14 CFR part 25)
The McDonnell-Douglas DC-10-10 was not required to comply with amendment 25-42 to the 14 CFR 25, which was issued on January 9, 1978, and only affected airplanes certified after March 1, 1978. The amendment revised the takeoff performance standards on part 25 transport category airplanes making them more restrictive.
Before a takeoff may be started with a turbine-powered transport category airplane, the operator must determine that the length of the runway to be used, plus any "stopway" and "clearway" that may be available, is adequate to either safely continue the takeoff from a defined go/no-go decision point in the takeoff roll or reject the takeoff from that point and bring the airplane to a complete stop. The go/no-go decision point occurs during the takeoff roll when the airplane reaches a speed known as the "takeoff decision speed," or " V1 speed."
To assure that there is adequate runway to continue the takeoff from the go/no-go decision point, the runway plus any clearway at the end must be long enough for the airplane to first accelerate to the V1 speed and then to continue takeoff to a height of 35 feet, even if a total loss of power from the most critical engine occurs just before reaching the V1 speed. This distance for the airplane to reach a height of 35 feet following a total loss of power from the most critical engine is defined as the "takeoff distance."
To provide for a possible need to reject the takeoff, the runway plus any stopway area must also be long enough to accelerate the airplane to V1 speed and then bring the airplane to a complete stop. This distance to reject a takeoff is called the "accelerate-stop" distance. A "balanced field length" exists when V1 is selected such that the accelerate-stop distance is equal to the takeoff distance. In general, the balanced field length is the minimum runway length required for takeoff.
The V1 speed selected for any takeoff depends on several variables, including the airplane's takeoff weight and configuration (flap setting), the runway length, the air temperature, the runway surface elevation (airport altitude), etc. The takeoff performance and limitation charts in the AFM are developed in accordance with the FAA airworthiness standards in subpart B of 14 CFR part 25 -"Airworthiness Standards: Transport Category Airplanes," using data gathered during comprehensive flight tests completed as a part of the FAA's approval of the airplane's type design.
14 CFR part 25, subpart B, also prescribes the FAA airworthiness standards for determining the length of runway required for safe landing under various airplane and atmospheric conditions. Landing performance charts are also published in the AFM, to be used by the operator to determine whether a particular runway is long enough for landing.
The general operating rules contained in 14 CFR parts 91, 121, and 135 require operators to plan takeoffs and landings using the appropriate performance and limitation charts published in the AFM.
14 CFR part 1 defines terms and explains abbreviations used in parts 25, 91, 121, and 135. This nomenclature is currently used in FAA airworthiness standards and operating rules and is also commonly used in the aviation industry.
It is fundamental to operational safety that the pilot should be able to either safely complete the takeoff or bring the airplane to a complete stop if a decision is made to reject the takeoff no later than the V1 speed, even if power is lost from the most critical engine just before V1. This principle has been used as the basis for the takeoff performance standards required for the type certification of turbine-powered transport category airplanes since the issuance of Special Civil Air Regulation No. SR-422, effective August 27, 1957.
The takeoff performance standards of 14 CFR part 25 define how the takeoff performance and limitations contained in the AFM must be determined. The information provided in the AFM accounts for various operational factors affecting how long the runway must be for airplanes to be operated in accordance with the principle stated in the above paragraph. The operator is not permitted to take off from a runway that is shorter than the airplane requires for the given conditions. Since actual runway lengths are fixed, the operator, using the performance information contained in the AFM, may have to reduce the airplane's takeoff weight in order to take off from a given runway. Reducing the takeoff weight shortens the distance required for takeoff. The more restrictive the airworthiness standards for takeoff runway length are, the more the takeoff weight may have to be reduced to be able to take off from a given runway.
To reduce the airplane's takeoff weight, the operator must either reduce the amount of fuel to be carried or reduce the number of passengers or amount of cargo to be transported. Since the amount of fuel to be carried is dictated primarily by the route being flown, sometimes the operator's only option is to reduce the number of passengers or amount of cargo to be transported.
Amendment 25-42, affected airplanes manufactured after March 1, 1978, revised the takeoff performance standards on 14 CFR part 25 transport category airplanes making them more restrictive. Prior to amendment 25-42, the accelerate-stop distance shown in the AFM accounted for variations in pilot reaction time by generally adding two seconds to the time required for pilots to take the actions necessary to stop the airplane during flight tests (e.g., reduce power, apply the brakes, and raise the spoilers). During this pilot reaction time delay, the airplane is assumed to be traveling at a constant speed. With the adoption of Amendment 42, this time delay was changed such that the distance resulting from the time delay was equal to the distance covered during 2 seconds of all-engine acceleration. The change was highly significant in terms of the field length now required.
In 1977 an FAA report covering an 11-year period from 1964 through 1975 concluded that tires, wheels, or brakes accounted for a majority of RTOs and not engine failures. The report also stated that increased accelerate-stop distance is not accounted for in current regulations and that other corrections to takeoff calculations are made for local conditions such as wind, runway slope, etc., yet these can be less significant than a correction for a wet/slippery runway.
The FAA and industry were aware of RTO issues concerning increased accelerate-stop distances; however, there was controversy that more restrictive accelerate-stop distances would unnecessarily penalize operators and possibly add cost in increasing runway lengths.
When amendment 25-42 to 14 CFR part 25 was implemented in 1978, it revised the takeoff performance standards to make them more restrictive in an attempt to address RTO issues that involved failed tires, brakes, and wet/slippery runways. When the number of passengers or amount of cargo must be reduced for a given flight, the airplane operator experienced loss of revenue resulting in controversy regarding the safety benefits of the rule change. Also, there was a competitive disparity from applying different performance standards due to amendment 25-42 affecting only airplanes that were manufactured after the rule change was in effect. The Continental Airlines Model DC-10 accident in 1978 resulted in further investigations and improvements to accelerate-stop distances: pilot training and tire, wheel, and brake certifications.
1) Actual accelerate-stop distance was greater than the available runway length. This was the result of the cumulative effect of partial loss of airplane braking because of failed tires, and the reduced braking friction on the wet runway surface.
2) The FAA aircraft requirements in effect at the time of the original DC-10 certification for RTO, airplane operations, and pilot training did not address wet runway, slippery runway, or tire failure conditions.
3) The slide/rafts that were deployed from emergency exits were exposed to fire and radiant heat and failed before the evacuation was completed. Passengers and crewmembers still in the airplane when all slide/rafts had failed either jumped to the ground or slid down the escape rope from the first officer's side window in the cockpit. The slide/raft girt fabric also tore loose and failed, rendering a slide/raft useless because of an apparent overload when passengers went onto the slide/raft faster than those at the bottom of the slide/raft could leave it.
1) Tires certified under FAA requirements and maintained in accordance with accepted maintenance and operational practices at the time were considered safe.
2) Certification requirements would adequately address operational variances such as runway surface conditions and airplane failures. It was assumed that an engine failure at the most critical time period during the takeoff roll presented the most adverse situation relative to accelerate-stop performance.
Model DC-10 series airplanes met certification requirements for RTO on dry runways with full braking capability and were not required to consider the effects of wet runways and worn brakes that would result in longer accelerate-stop distances.
3) Pilot training via simulation of high energy accelerate-stop situations was adequate.
Training for situations requiring maximum energy stops is by necessity limited to simulation and may not reflect the pilot's, or the airplane’s, actual performance.
4) Due in part to the short time duration for which they are required, it was assumed that evacuation slides would not be subject to the adverse effects of radiant heat.
Slide/raft devices are used for a very short period during passenger and crew emergency evacuation. Model DC-10 certification required all passengers and crew to evacuate the airplane in 90 seconds with half of the exits blocked. Failure of the slide/rafts due to radiant heat was not considered during airplane certification.
5) Slides would adequately accommodate weight loadings for the period of an emergency evacuation. The Slide/rafts were designed to evacuate 30 passengers per minute, therefore during an emergency evacuation, passenger overloading and failure of the slide/raft should be low probability/risk.
There were numerous precursor RTOs related to wet runways, worn brakes, and blown tires that did not result in an incident or accident.
In FAA report, "Jet Transport Rejected Takeoffs, Final Report, February 1977, Flight Standards Services," the FAA indicates that 87 percent of RTOs were caused by some failure or malfunction of tires, wheels, or brakes and that engine failures have not been the dominant cause. The airplane stopping distances significantly increase as a result of tire, wheel, or brake failure because its ability to develop or transmit braking torque to the runway surface is reduced. Despite causing 87 percent of RTOs, the effects of these failures were not considered in calculating stopping distance.
The FAA report, "Trans World Airlines, Inc., B-707, N69TW, Fiumicino Airport, Rome, Italy, November 23, 1970," cites wet or slippery runway involvement in three major RTO accidents between 1964 and 1975.
1) Boeing Model 707 series airplane, N769TW, Trans World Airlines, Inc., Rome, September 23, 1964.
2) McDonnell Douglas Model DC-8 series airplane, N4909C, Capitol International Airways, Inc., Anchorage, Alaska, November 27, 1970.
3) McDonnell Douglas Model DC-10 series airplane, N1032F, Overseas National Airways, Inc., Jamaica, New York, November 12, 1975.
The FAA report recommends that "The increased accelerate-stop distance required on wet slippery runways be taken into account in takeoff calculations and the necessary changes to airplane flight manuals, procedures, and regulations be incorporated to accommodate this." The NTSB determined that no FAA actions had been taken before the Continental Airlines Model DC-10 accident concerning this recommendation.
Although this accident occurred in 1978, regulatory development continued well into 1990's. This accident was the catalyst for a number of rule changes affecting runway performance, some of which have only recently been added to the certification requirements for transport airplanes.
Tires
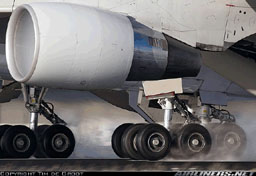
Photo copyright Tim De Groot - used with permission
In response to NTSB Safety Recommendations A-78-67 through 74, the FAA has revised TSO-C62b to include updated tire rating criteria, performance standards, test requirements for re-treaded tires, and tire usage and mountings.
The revised TSO-C62c requires the manufacturer to furnish to the Manager aircraft certification office (ACO) having geographical purview of the manufacturer's facilities, the following technical data: speed rating, load rating, rated inflation pressure, tire size, width, outside diameter, mold skid depth, nominal loaded radius at rated load and inflation pressure, permissible tolerance on the nominal loaded radius, the actual loaded radius of the test tire at rated load and inflation pressure, weight, static unbalance of the test tire, wheel rim designation, manufacturer's part number and, for high-speed tires, a load deflection curve at loads up to 1.5 times load rating and a summary of the load-speed-time parameters used in the dynamometer tests. As used in this section, the term "high-speed tire" means a tire tested at a speed greater that 120 mph.
The manufacturer must also furnish the applicable maintenance and repair instructions that include inspection criteria for recapped tires to continue in service. Recapping procedures must be included along with any special repair procedures and special nondestructive inspection techniques applicable to that tire. TSO-C62b and TSO-C62c
In order to improve the capability of tires to withstand present operating loads, especially in large transport airplanes, a substantially revised series of dynamometer tests were imposed in TSO-C62c. These tests include a combination of high speed takeoff cycles, taxi cycles, an overload cycle, and overload taxi cycles, which are expected to result in major improvements in tire design with a significant increase in the safety level of high speed tires produced under the revised TSO.
In addition, the FAA published Advisory Circular (AC) 145-4A, "Inspection, Retread, Repair, and Alterations of Aircraft Tires," dated July 10,2006, on qualification of retread tires that provides guidance for the development, qualification, and approval of aircraft tire repair and retread process specification, and the use of special nondestructive inspection techniques. The AC also provides information related to rule changes on aircraft tires used on transport category airplanes in order that tire reliability will be enhanced and the incidence of tire failures decreased. AC 145-4A
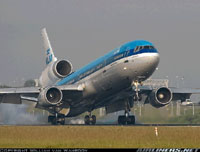
Photo copyright William Van Wanrooy - used with permission
The FAA also published Advisory Circular 20-97B, "Aircraft Tire Maintenance and Operational Practices," dated April 18, 2005, that provides recommended tire care and maintenance practices needed to ensure the safety of support personnel and the continued airworthiness of aircraft. Specifically, this AC provides guidance on the installation, inflation, maintenance, and removal of aircraft tires. In addition, this AC provides guidance on those operational practices necessary to maintain safe aircraft operations. AC No. 20-97B
Amendment 25-49, issued on November 21, 1979, revised 14 CFR 25.733 to include a 1.07 factor in establishing the required load rating of the tire on the airplane. When the load factor of 1.07 is considered in conjunction with the new overload takeoff test proposed in TSO-C62c for tires, this change effectively required high-speed aircraft tires to withstand an overload of 1.61 times the present load rating, a substantial upgrading of previous requirements.
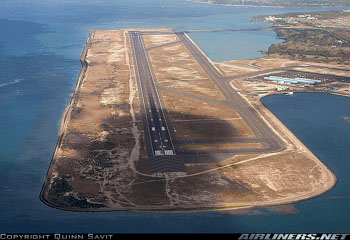
Photo copyright Quinn Savit - used with permission
Takeoff and Landing Performance Standard
(1) FAA rule changes mandated by:
Amendment 25-92 issued February 10, 1998, revised several sections of 14 CFR parts 25, 91, 121, and 135 concerning the methods for determining and applying the takeoff and landing performance standards for turbine-powered transport category airplanes.
The standards revised by amendment 25-42 require the accelerate-stop distance to include, in addition to the time delay associated with each deceleration device, two seconds of continued acceleration beyond V1 speed before the pilot takes action to begin stopping the airplane. This revision results in longer accelerate-stop distances being required for airplanes whose application for a type certificate was made after amendment 25-42 became effective. Consequently, turbine-powered transport category airplanes that are currently being manufactured under a type certificate that was applied for prior to March 1, 1978, have a significant operational economic advantage over airplanes whose type certificate was applied for after that date. This competitive disparity resulting from applying different performance standards has created a compelling need to amend the takeoff performance standards of part 25 without adversely affecting safety.
Amendment 25-42 was a broad brush approach, applying to all takeoffs, to increase the required accelerate-stop distance. This broad brush approach was taken because the takeoff performance standards do not explicitly account for many of the important operational factors that may affect takeoff performance. For example, amendment 25-42 standards did not distinguish between dry and wet runways, nor were the effects of worn brakes taken into account. Wet runways and worn brakes would result in an airplane requiring a longer accelerate-stop distance than with new brakes on a dry runway. By proposing to account for wet runways and to base stopping performance on brakes that are completely worn, these amendments would provide additional safety margins in the conditions where it is specifically needed in operational service.
Because wet runways and worn brakes would be accounted for in amendment 25-92, the FAA also proposed replacing the two seconds of continued acceleration beyond V1 with a distance equal to two seconds at V1. The distance equal to two seconds at V1, while shorter than that resulting from the continued acceleration beyond V1 required by amendment 25-42, is a distance margin that must be added to the accelerate-stop distance demonstrated during flight testing for type certification. This distance margin, based on the V1 speed and a time "delay" of two seconds, accounts for variability in the time it takes for pilots, in actual operations, to accomplish the procedures for stopping the airplane.
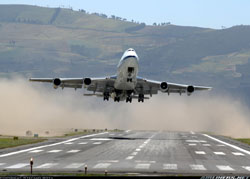
Photo copyright Stefano Rota - used with permission
Amendment 25-42 required the two seconds of time delay to be applied prior to the pilot taking any action to stop the airplane. This more restrictive approach caused the airplane to reach a higher speed during the accelerate-stop maneuver and resulted in a longer distance than the distance equal to two seconds at V1 speed. Inserting the time delay before the pilot takes any action to stop the airplane, however, did not accurately reflect the procedures that pilots are trained to use in operational service. Also, V1 is intended to be the speed by which the pilot has made the decision to reject the takeoff and has begun taking action to stop the airplane. The time it takes for the pilot to recognize the need for an RTO, which no longer exists once V1 is reached, is considered separately within the airworthiness standards. Therefore, the new amendments more accurately reflect rejected takeoff procedures and the intended use of V1 speed, and account for variability in the time it takes for pilots, in actual operations, to accomplish the procedures for stopping the airplane.
The purpose of the amendment 25-92 revising the takeoff performance standards of 14 CFR parts 25, 91, 121, and 135 was to rationally reflect the operational factors involved and thus reduce the impact of the standards on the competitiveness of new versus derivative airplanes. The new amendments also would require more restrictive standards to be met for takeoffs from wet runways than for takeoffs from dry runways. In addition, the accelerate-stop distance, which must be provided as an AFM takeoff limitation, is based on worn brakes rather than new brakes. Lastly, the airplane is assumed to maintain a constant velocity for the two-second time delay after reaching V1 speed (instead of accelerating). Overall, the amended standards are more rational and less restrictive than the existing standards, even though they remain slightly more restrictive than the standards that existed before amendment 25-42 became effective.
Amendment 25-92 revised the following parts of the 14 CFR 25:
1) Replace the two seconds of continued acceleration beyond V1 with a distance margin equal to two seconds at V1 speed;
2) Require that the runway surface conditions (dry or wet) be taken into account when determining the runway length that must be available for takeoff; and
3) Require that worn brakes be taken into account when determining the capability of the brakes to absorb energy and provide a stopping force for takeoff and landing.
This amendment revised several sections of 14 CFR parts 25, 91, 121, and 135 that provide the methods for determining and applying the takeoff and landing performance standards for turbine-powered transport category airplanes. Also, this notice proposes to amend part 1 to add a definition of the term "takeoff decision speed" and an explanation for the abbreviation "VEF."
Part 1 was amended to add a definition of the term "takeoff decision speed" and an explanation for the abbreviation "VEF."
Paragraph (i) of section 25.101 (14 CFR 25.101(i)) was amended to require that accelerate-stop and landing distances must be determined with all the airplane brakes at the fully worn limit of their allowable wear range.
14 CFR 25.105 was amended to require the airplane takeoff performance data be based on wet in addition to dry runways.
14 CFR 25.109 amended the method of determining the accelerate-stop distance prescribed by replacing the two seconds of continued acceleration after reaching V1 with a distance equal to two seconds at V1 speed. This would reduce the accelerate-stop distance that must be available for an RTO because the airplane would be assumed to begin stopping from a lower speed (V1 rather than the speed reached after two seconds of acceleration beyond V1).
14 CFR 25.109 was amended to provide the details of how the accelerate-stop distance would be calculated for a wet runway. This amendment contains a rational approach that includes consideration of the major variables affecting the stopping performance on a wet runway. This approach to determining the wet runway RTO performance includes: 1) taking into account the reduced braking force due to the wet surface; 2) permitting performance credit for using available reverse thrust as an additional stopping force; and 3) permitting a lower minimum airplane height over the end of the runway after takeoff. This approach would reduce the risk of overruns during RTOs on wet runways while retaining safety margins for continued takeoffs similar to those required for dry runways.
14 CFR 25.109 was also revised to permit the use of available reverse thrust when determining the accelerate-stop distance for a wet runway. "Available" reverse thrust is interpreted as meaning the thrust from engines with thrust reversers that are operating during the stopping portion of the RTO. Allowance for reverse thrust has been included because the most significant variable that affects the stopping performance on a wet runway, reduced braking friction, has been accounted for as part of the rational approach to wet runway RTO.
This amendment replaces the most costly and controversial aspect of amendment 25-42 with a requirement that closely represents the pre-amendment 25-42 criteria of 14 CFR 25.109, as applied to the certification of recent U.S.-manufactured airplanes.
14 CFR 25.113 was amended to allow the distance required for a continued takeoff from a wet runway to include taking off and climbing to a height of 15 feet, rather than the 35 feet required on a dry runway. This lower "screen height" (which is the height of an imaginary screen that the airplane would just clear with the wings in a level attitude when taking off or landing) reduces the balanced field length V1 speed, thereby reducing the number of high-speed RTOs on wet runways.
The FAA considers lowering the screen height to be an acceptable method of reducing the risk of overruns on wet runways because of the similarity to current rules when operating from dry runways that have a clearway. The minimum height permitted over the end of the runway for current dry runway takeoffs may be 13 to 17 feet, depending on the airplane, when a clearway is present. In addition, a 15-foot minimum screen height and vertical obstacle clearance distance has been allowed for many years by the British CAA for wet runway operations without any problems being reported.
The amended 14 CFR 25.113 did not permit the combination of clearway credit and a 15-foot screen height. 14 CFR 25.113 was clarified, however, to ensure that for wet runways the presence of a clearway does not result in the anomaly of requiring longer runway lengths than if there were no clearway.
14 CFR 25.115 was amended to permit the minimum vertical distance required between the takeoff flight path defined in 14 CFR 25.115 and obstacles (e.g., trees, hills, buildings, etc.) would be reduced by a corresponding amount. To accomplish this, CFR 25.115 would be revised to state that the takeoff flight path shall be considered to begin at a height of 35 feet at the end of the takeoff distance.
This revised definition of the takeoff flight path would apply equally to dry and wet runways, even though the height at the end of the takeoff distance (i.e., screen height) for wet runways is only 15 feet. The effect of this amendment is to permit the flight path information currently contained in the AFM for dry runways to also be used for wet runways. Because of the reduced screen height, at a given point in the flight path, the height of an airplane taking off from a wet runway will be approximately 20 feet lower than the height of that airplane taking off from a dry runway. Therefore, using the flight path information currently in the AFM will reduce the airplane's actual height over obstacles by approximately 20 feet when the airplane takes off from a wet runway.
Prior to amendment 25-92, regulations required the airplane's flight path to be higher than any obstacles by a combination of an increment of height and an increment of gradient (i.e., the slope of the flight path). This amendment reduces the height increment by approximately 20 feet, but the gradient increment is not changed. As the distance from the end of the takeoff distance increases, the gradient increment provides an increasingly greater portion of the total height difference between the airplane and the obstacle. Therefore, the effect of reducing the height increment over obstacles by 20 feet diminishes as the distance from the end of the takeoff distance increases.
Paragraph (f)(3) of section 25.735 (14 CFR 25.735(f)(3)) was amended to require that the brake energy capacity rating must be determined with each brake at the fully worn limit of the allowable wear range. 14 CFR 25.735 was also amended to add a requirement for a flight test demonstration of the maximum kinetic energy rejected takeoff with not more than 10 percent of the allowable brake wear range remaining.
Manufacturers or operators of previously certificated airplanes may elect to comply with these proposed later amendments by a change to the type design, and thus the benefits of the revision to the time delay criteria of 14 CFR 25.109 would be available to relieve the economic burden imposed by amendment 25-42. The more rational accounting for reduced stopping capability on wet runways during RTO and for the reduced capability of worn brakes would also be included in such a recertification. It is expected that, for airplanes whose certification basis includes amendment 25-42, applicants will elect to comply with this proposal because it will be economically beneficial for them to do so.
Paragraph (b) of section 25.1587 (14 CFR 25.1587(b)) was amended to require that performance information for wet runways be included in the AFM. The AFM contains, along with other information, all of the performance information computed under the provisions of 14 CFR part 25.
14 CFR 91.605, 14 CFR 121.189, and 14 CFR 135.379 of the operating rules were amended to require that wet runways be taken into account when determining the runway length that must be available for takeoff, if wet runway performance information exists in the AFM. Thus, this rule would apply only to airplanes whose application for type certification occurs after the rule becomes effective.
Evacuation Slides
In response to NTSB Safety Recommendations A-79-16, A-79-18, and A-79-19, the FAA undertook research and development testing which resulted in the issuance of new TSO-C69 slide and slide/raft fire resistance requirements, girt strength, and critical angle testing.
1) TSO-C69a, "Emergency Evacuation Slides," dated June 3, 1983, included the following changes:
- Added new radiant heat testing requirements of inflatable emergency evacuation slide/raft material. The test required three specimens tested at 1.5 BTU/ft2 sec, and the resultant times to failure in which average time to failure must not be less than 90 seconds. Time to failure is the time between first application of heat to the specimen and first drop in pressure below the maximum pressure attained in the test cylinder during the test.
- Updated the slide/raft material flammability requirements to comply with paragraph (b) of section 25.853, "Compartment interiors," (14 CFR 25.853(b)).
- Revised the slide/raft strength requirement: "The device, installed at its critical angle, may not collapse when loaded to its maximum capacity as determined by a test in which a sufficient number of adult (170 pounds or more) evacuees crowd closely in line at the top of each lane of the device and jump into the device in rapid succession at a rate not less than one evacuee per second per lane. It must demonstrate the means used to connect the device to the airplane (girt material) will not fail when the device is operated at low angles (from horizontal) and at maximum evacuee loading conditions (including asymmetrical loading) expected in service. Also, the angles and loads selected may not be greater than 30 degrees and less than 1,050 pounds per lane, respectively. If the device is equipped with outrigger pontoons, additional test loads must be applied to account for asymmetrical loads that would result from evacuees inadvertently entering the pontoon areas during an emergency evacuation.
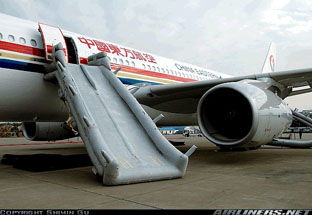
Photo copyright Yusu Ren - used with permission
Photo copyright Ronen Eckstein - used with permission
Additional Slide/Raft requirements beyond the NTSB recommendations were also initiated by the FAA to increase passenger/crew survivability
- Evacuation rate increased from 30 evacuees to 60 evacuees per minute per lane at representative sill heights for a duration of at least 70 seconds.
- Inflation time decreased from 25 seconds to 10 seconds after the actuation of the inflation controls begins. An additional wing-to-ground slide now requires the device to automatically erect in 15 seconds after actuation of the inflation control.
- Slide/raft devices must be equipped with side guards or other means to prevent evacuees from accidentally missing or falling from the device.
- Self-illuminated slides must be designed so the illumination means is activated automatically during deployment or inflation and the level of illumination meets the appropriate requirements in 14 CFR 25.812.
- Slide/raft must have the capability, in 25-knot winds directed from the most critical angle, to deploy and with the assistance of only one person, to remain usable after full deployment to evacuate occupants safely to the ground.
- At least five consecutive deployment and erection tests must be demonstrated without failure to ensure that the slide/raft device performs its intended function. Section 25.809, "Emergency exit arrangement," (14 CFR 25.809) contains requirements pertaining to the deployment and erection characteristics as well as the installation of the device on the airplane, which may be taken into consideration along with the requirements of this TSO.
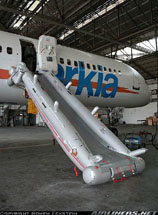
2) TSO-C69b Emergency Evacuation Slides, dated August 17, 1988, revised:
- Inflation time to decrease from 10 seconds to 6 seconds after the actuation of the inflation controls begins. An additional wing-to-ground slide now requires the device to automatically erect from 15 seconds to 10 seconds after actuation of the inflation control.
3) TSO-C69c Emergency Evacuation Slides, dated August 18, 1999, revised:
- The slide/raft material flammability requirements to comply with paragraph (a) of 14 CFR 25.853 and the criteria described in paragraph (a)(1)(ii) of Appendix F, part I, of 14 CFR part 25.
- Evacuation rates to increase from 60 evacuees to 70 evacuees per minute per lane at representative sill heights for a duration of at least 70 seconds.
- Radiant heat testing requirements of inflatable emergency evacuation slide/raft material. The pressure holding materials in the device must meet the 90-second minimum-time-to-failure requirement and the 180-second average-time-to-failure requirement of the radiant heat resistance test.
This accident was instrumental in addressing worn brake issues and provided the basis for further study that resulted in a number of airplane-specific ADs requiring changes to brake-wear limits and brake-life monitoring. The operational effect of the ADs was to reduce the amount of brake wear allowable on any given make/model airplane, and to control combinations of worn/new brakes such that configurations with all brakes worn to, or near to, their limits is avoided.
Airplane Life Cycle:
- Maintenance / Repair / Alteration
- Design / Manufacturing
- Operational
Accident Threat Categories:
- Cabin Safety / Hazardous Cargo
- Landing / Takeoff Excursions
- Uncontrolled Fire / Smoke
Groupings:
- N/A
Accident Common Themes:
- Organizational Lapses
- Flawed Assumptions
- Pre-existing Failures
Organizational Lapses
- The FAA, British CAA, and industry were aware of RTO issues concerning increased accelerate-stop distances due to wet runways and worn brakes. However, there was controversy that more restrictive accelerate-stop distances would unnecessarily penalize operators with increased pilot training costs, decreased operator revenue due to limiting passenger/cargo loading, and possibly adding cost in increasing runway lengths. Industry pressure challenging the safety benefits that would be gained with increased accelerate-stop distances due to wet runways and worn brakes could have possibly delayed the FAA in timely implementation of current regulations.
Flawed Assumptions
- Tires certified under current requirements and maintained in accordance with accepted maintenance and operational practices were considered safe. Experiencing multiple failed tires on one landing gear, resulting in partial loss of airplane braking, was unlikely to occur and has had no previously reported occurrences.
- McDonnell Douglas Model DC-10 series airplanes met certification requirements for rejected takeoff on dry runways with full braking capability and did not consider the effects of wet runways and worn brakes that would result in longer accelerate-stop distances. Thrust reversers were not permitted in determining accelerate-stop distances. However, during an RTO, thrust reversers are typically used and may give the flight crew a false sense of security, especially when wet runway and worn brake conditions exist.
- Pilot training in actual RTOs requiring maximum energy stops is by necessity limited to discussion and simulation. In some cases, simulator training may provide a false sense of security to the pilot by reflecting airplane performance in excess of that actually available for stopping on wet runways.
- An analysis of 74 RTO accidents and incidents showed that 24 percent were engine RTOs, and the remaining 76 percent were RTOs initiated for a variety of reasons which included tire failures, procedural error, malfunction indication or lights, noises and vibrations, directional control difficulties, and unbalanced loading situations where the airplane failed to rotate. The fact that the majority of the accidents and incidents occurred on airplanes that had full thrust available suggested pilots were unnecessarily initiating RTOs.
- Slide/raft devices are used for a very short period during passenger and crew emergency evacuation. Certification of Model DC-10 series airplanes required all passengers and crew to evacuate the airplane in 90 seconds with half of the exits blocked. Failure of the slide/rafts due to radiant heat was not considered during airplane certification and it is not fully understood why. There were no slide/raft failures caused by radiant heat reported prior to this accident and that the probability was low that the majority of the slides would be disabled due to radiant heat.
- Slide/raft was designed to evacuate 30 passengers per minute, therefore during an emergency evacuation, passenger overloading and failure of the slide/raft should be low probability/risk.
Pre-Existing Failures
- Tire No. 2 was the first tire to fail, resulting in a cascading failure of three of the tires on the same main landing gear. The investigation determined that tire No. 2 has lost its tread and concluded that two different scenarios may have led to tread separation and the initiation of the cascading failure. The No. 2 tire was found to have had internal patches installed during manufacture, and that these patches may have leaked under the tread, causing the tire to be underinflated, and subject to sidewall temperature increases, and rapid tire deterioration. The investigation also stated that air leakage between the tire carcass and the tread could have led to tread separation. The other scenario required that the No. 1 tire became underinflated, causing the No. 2 tire to carry a higher load than intended, again leading to higher sidewall deflections and temperatures. These high loads and temperatures then led to a premature tire failure, initiating the cascading failure.
A training guide titled "Pilot Guide To Takeoff Safety" points out some of the lessons that have been learned through the RTO experiences of other airline crews from 1960 to 1990. Data contained in this guide include the following observations:
- In two separate categories, almost 25% percent of the 74 RTO overrun accidents/incidents were caused by wheel/tire or wet runway conditions.
1960 through 1990 | |
---|---|
Takeoffs | 230,000,000 |
RTOs (estimated) | 76,000 |
RTO Overrun Accidents/Incidents | 74 |
• 1 RTO per 3,000 takeoffs
• 1 RTO overrun accident/incident per 3,000,000 operations
• Of the 74 RTO overruns caused by runway conditions:
• 37.8% dry runway condition
• 28.4% not reported
• 24.3% wet runway conditions
• 9.5% ice/snow runway conditions
• Of the 74 RTO overruns (other causes):
• 24.3% engine was the cause for the RTO
• 22.9% wheel/tire was the cause for the RTO
• 12.3% airplane configuration was the cause for the RTO
• 9.5% indicator/light was the cause for the RTO
• 8.1% flight crew coordination was the cause for the RTO
• 6.8% bird strike was the cause for the RTO
• 2.7% air traffic control was the cause of the RTO
• 13.5% not reported was the cause for the RTO
Technical Related Lessons:
Regulatory "safety margins" should be sufficiently robust to address expected operational situations. (Threat Category: Landing/Takeoff Excursions)
- The captain of Flight 603 reacted promptly to the tire failures in accordance with Continental Airlines procedures. However, the actual accelerate-stop distance was greater than the available runway length as a result of the cumulative effect of failed tires leading to a partial loss of braking, and the reduced braking friction on the wet runway surface. Also, the FAA airplane certification requirements for RTO, aircraft operations, and pilot training at the time did not address wet runway, slippery runway, worn brakes, or tire failure conditions.
Evacuation slides should be designed and certified to withstand radiant heat and should have weight/loading margins adequate for the expected evacuation loading. (Threat Category: Cabin Safety/Hazardous Cargo)
- In this accident, the escape slides failed due to both radiant heat from the fire, and apparent overload. Some of the slides failed almost immediately, and were not available for evacuation, even though they had been deployed. Following the accident, regulatory changes intended to decrease failure susceptibility when subjected to radiant heat, and provide for greater passenger evacuation capacity, resulted in increased passenger and crew survivability under actual emergency evacuation conditions.
Common Theme Related Lessons:
Escape slides need to be sufficiently heat resistant to allow for the complete evacuation period following an otherwise survivable accident. (Common Theme: Flawed Assumptions)
- It was assumed that since the required evacuation time was 90 seconds, the required number of escape slides would be capable of withstanding the heat of a fire for a period sufficient to allow the complete evacuation of the airplane. In this accident, the slides failed well before the 90 second period, and indicated that new criteria were required in order to ensure the continued integrity of the escape slides when exposed to the radiant heat of a fire.
Designs which are dependent upon redundancy, such as with dual-tire arrangements, must include provisions for ensuring that each path of the redundancy has the requisite integrity to withstand single path loading conditions, and do not result in cascading failures. (Common Theme: Pre-existing Failures)
- In the case of this accident, a pre-existing failure in one of the tires resulted in an excessive loading on the remaining tire in that axle pair. The tire was not capable of sustaining this increased load, and failed almost immediately (i.e., cascading failure), leading to a loss of required braking capability, and the catastrophic runway overrun.