Lockheed L-188 Electra
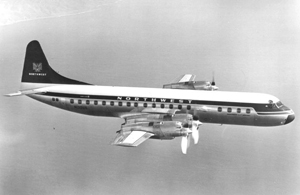
Braniff Airways Flight 542, N9705C
Buffalo, Texas
September 29, 1959
On September 29, 1959, Braniff Airways Flight 542, a Lockheed Model L-188A (Electra) airplane, experienced left wing airborne disintegration near Buffalo, Texas. The flight was scheduled between Houston, TX and New York International Airport, with stops in Dallas, TX, and Washington, DC.
Northwest Airlines Flight 710, N121US
Cannelton, Indiana
March 17, 1960
On March 17, 1960, Northwest Airlines Flight 710, a Lockheed Model L-188C (Electra) airplane, experienced right wing airborne failure near Cannelton, IN. The flight was scheduled between Minneapolis, MN and Miami, FL with a stop in Midway Airport, Chicago, IL.
The two accidents mirrored each other and shocked the aviation industry. The FAA Administrator requested Lockheed Aircraft Corporation to reevaluate the Electra. Both accidents were determined to have been the result of destructive wing flutter initiated by a propeller whirl mode. The whirl mode phenomenon was the result of a loss of structural rigidity following the failure of an engine mount during a hard landing. The propeller whirl-mode frequency coupled with a natural frequency of the wings drove a destructive flutter mode. The two accidents resulted in a substantial design evaluation, and a subsequent redesign of the engine nacelles and mounting structure.
Braniff Airways Flight 542 (September 29, 1959)
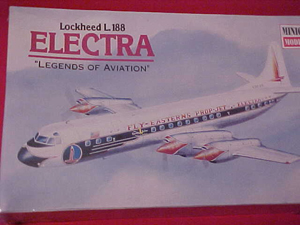
Braniff Airways Flight 542, a Lockheed Model L-188A (Electra) airplane, was scheduled between Houston, TX, and New York International Airport, with stops in Dallas, TX, and Washington, DC.
Flight 542 departed the ramp in Houston at 2237. There were 28 passengers and a crew of six onboard. At 2240, the flight was cleared for takeoff and was airborne at 2244.
Houston air traffic control (ATC) tower had Flight 542 in radar contact after takeoff and subsequently cleared it to 9,000 feet and advised the flight to contact San Antonio Air Route Traffic Control Center (ARTCC) (hereafter referred to as "Center") upon passing the "Gulf Coast" intersection.
Flight 542 reported to company radio at 2251, and at 2252, reported to San Antonio Center as being over the "Gulf Coast" intersection at 9,000 feet. San Antonio Center cleared Flight 542 to the Dallas airport and directed it to maintain 15,000 feet cruising altitude and to change to, and monitor, the Fort Worth frequency.
Shortly thereafter, Flight 542 contacted company radio with a message for maintenance. This was the last transmission from Flight 542, which was logged at 2307.
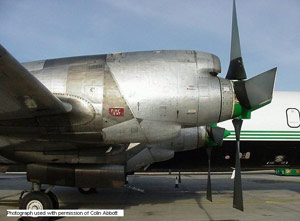
Photo copyright Colin Abbott - used with permission
Structural failure of the wing occurred at approximately 2309. The main wreckage was located 3.19 miles east-southeast of Buffalo, TX. The time correlates with impact-stopped watches recovered at the scene and from witnesses to the accident.
There were no radar or radio contacts with Flight 542, nor were any emergency calls received after 2307. There was no known traffic, missiles, or unmanned aircraft in the region at the time of the accident.
The recovered flight engineer's logbook recorded altitude at 15,000; airspeed of 275 knots; 15 degrees F outside air temperature; anti-icing off; and time of 2300.
Weather reports for the late evening of September 29, 1959, and the early morning hours of September 30, 1959, show a weak pressure gradient in southwestern Texas. A pilot en route from Dallas to Houston later reported encountering intermittent light rain and moderate turbulence at 7,000 feet, northwest of Buffalo, TX.
According to ground witnesses in Buffalo, TX, and the immediate area at the time of the accident, skies were partly cloudy, the visibility was good, and no lightning was observed.
Company meteorologists provided the flight crew of Flight 542 with current and forecast weather information for the route and terminals concerned.
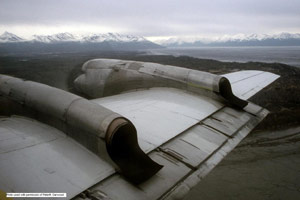
Photo copyright Peter M. Garwood - used with permission
Witnesses reported hearing various noises of different intensities and pitches (clapping of two boards together, thunder, roar of a jet breaking the sound barrier, etc.). The majority observed a large fire in the sky.
Wreckage was located within a total distance of 13,900 feet from the first recovered item to the nose crater, and it was distributed within a long narrow ellipse. At the main area, there were three basic concentrations of wreckage: around the nose crater, the center section crater, and the tail section. Light material was found a half mile to the north and northeast. The nose crater, about four feet deep, was at the easternmost end of the investigation area. The center section crater was approximately 200 feet northeast of the nose crater. The tail section was located 250 feet northwest of the center section.
After studying the wreckage distribution pattern, it became evident that the airplane had experienced airborne disintegration, which broke the airplane up into a number of major sections. Damage to the airplane was extensive, with only a few parts and system components recognizable. In addition, fire had destroyed or damaged individual components making functional checks impossible. As part of the investigation, considerable time was spent identifying, listing, and describing damage to parts and system components. No indication of operational distress, fire, or overheating was found through examinations. The Civil Aeronautics Board Aircraft Accident Report concluded that the probable cause of this accident was structural failure of the left wing resulting from forces generated by undampened propeller whirl mode.
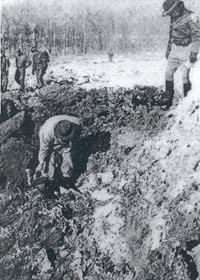
Northwest Airlines Flight 710 (March 17, 1960)
Northwest Airlines Flight 710, Lockheed Model L-188C (Electra) airplane was scheduled between Minneapolis, MN and Miami, FL, with a stop at Midway Airport, Chicago, IL.
Flight 710 departed Minneapolis at 1251 and arrived at Midway at 1355. Some of the passengers said the landing was very hard. The airplane was refueled and prepared for its flight to Miami.
The hard landing described by the passengers became significant in the determination of the accident cause. The Lockheed Electra exhibited landing characteristics such that if power were reduced at too high an altitude above touchdown, the resulting sink rate would cause a hard touchdown. The investigation concluded that a series of hard landings, or a single landing of sufficiently high sink rate could have caused the failure of the aft engine mount and reduced the stiffness of the nacelle to the point that it coupled with the natural frequency of the wing, leading to the described whirl mode event.
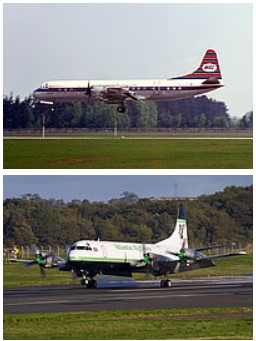
Photo copyright (top) Ralf Manteufel,
(bottom) Fred Seggie - used with permission
Flight 710 departed Chicago at 1438 for a nonstop flight to Miami. There were 57 passengers and a crew of six onboard. Prior to departure the crew was briefed by a company meteorologist on present and expected weather conditions along the route. There was no mention of clear air turbulence along the route. At 1445, the flight reported to Indianapolis Center at 18,000 feet. At 1513, Flight 710 reported over Scotland, IN maintaining 18,000 feet. This was the last known radio communication with Flight 710.
At approximately 1640, reports were received by Northwest Airlines at Minneapolis that Flight 710 had crashed near Cannelton, IN. The time of the crash was estimated at 1525.
Flight 710 was flying in an approximate north to south direction in level flight. Six United States Air Force (USAF) airplanes were on a refueling mission in the area at an altitude of 31,000 to 32,000 feet. Airmen manning the USAF airplane said they first saw a smoke trail at 1532. Ground witnesses reported seeing two puffs of white smoke followed seconds later by a large cloud of dark smoke. Two loud explosions were then heard and a large object was seen to emerge from the smoke cloud and fall nearly vertically, trailing smoke and flame. The fuselage struck the ground, spreading debris nearly 250 feet into the air.
The major portion of the airplane struck the ground in a nearly vertical attitude. Impact forces formed a crater measuring 30 feet across and 12 feet deep. Most of the airplane forming the crater disintegrated and buried. A shallow depression that contained fragments of the left wing extended southward from the crater for a distance of 16 feet. Portions of the vertical tail were imbedded in the west rim of the crater. The impact scattered wreckage up to 1,500 feet to the east and southwest.
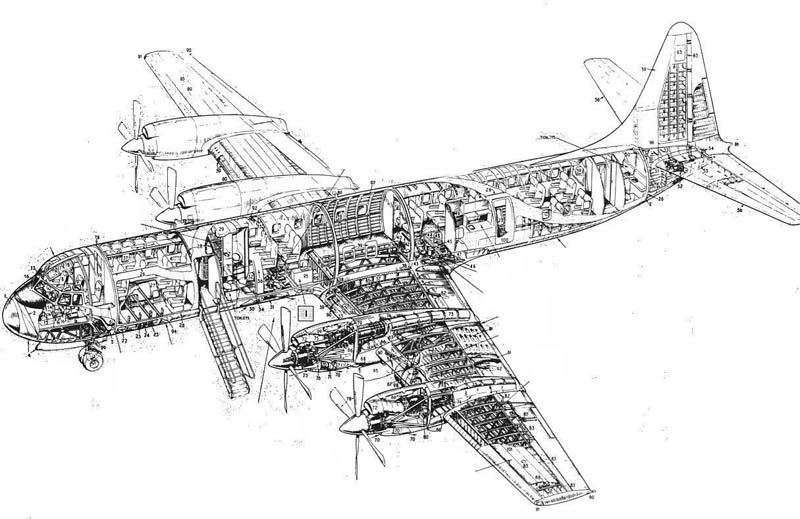
(View Large Image)
The south end of the crater contained the No. 2 engine and propeller, parts of the left main gear, and parts of the wing structure. The north end of the crater contained the fuselage structure. The main portion of the right wing, the outboard engines, and many small pieces of wreckage were widely scattered in north and northeast from the crater. Study of the wreckage and wreckage distribution at the scene disclosed that the outboard engines and engine support structures, the complete right wing, and the outer portions of the left wing and aileron separated from the rest of the airplane in flight. A detailed study of the main wreckage was conducted at the Lockheed factory. Various reconstructions were done to facilitate the study.
The Civil Aeronautics Board Aircraft Accident Report concluded that flutter was induced by oscillations of the outboard engine nacelles (undampened propeller whirl mode) and that it reached a magnitude sufficient to fail the right wing. Reduced stiffness of the nacelle structure, possibly due to the hard landing damage at Chicago and the entry of the airplane into an area of severe clear air turbulence, were contributing factors.
Lockheed Electra Action Program (LEAP)
Following several meetings, the FAA Administrator requested Lockheed Aircraft Corporation to conduct an engineering reevaluation of Electra model airplanes. The objective was to reveal any design or operational characteristics of the airplane that may cause structural wing failure in flight. Assistance was provided by NASA (Langley), Boeing, Douglas Aircraft Company, and other organizations. This reevaluation effort was named Lockheed Electra Action Program (LEAP).
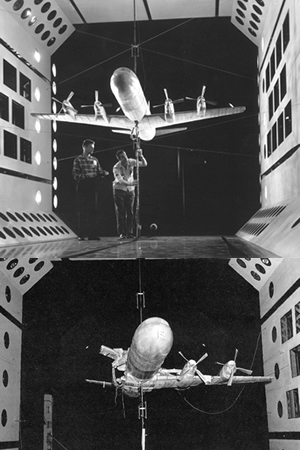
The program disclosed two discrepancies in the design of the airplane. One, significant loads imposed on the wing's intermediate ribs
between the fuselage and outboard nacelles by shell distortion had not been included in the design loads. Two, the dynamic response of the outboard nacelles in turbulence was different from the design assumptions.
An eighth-scale powered model of the Electra was tested in the NASA Langley 19-foot tunnel. Lockheed and Langley flutter experts were concerned that the propeller-driven Electra may have exhibited the phenomenon known as whirl mode, in which the stiffness of the engine mounts interacts with the gyroscopic torques produced by the engine and propeller combination. This interaction results in an unstable wobbling motion that could resonate with natural frequencies of the wing structure and could cause catastrophic flutter of the wing. The Lockheed and Langley team reduced the stiffness of the outboard engine mounts on the model and found that the propeller whirl mode motion coupled with the natural flapping frequency of the wing. The interaction resulted in an unstable wobbling motion.
Normally, whirl-mode flutter can operate only within the flexibility limits of the engine mounting structure, and is quickly dampened. If the stiffness of the supporting system is reduced through failed or damaged engine structure, mounts (as was suspected in the Northwest Airlines Flight 710 due to hard landing), or nacelle structure, the damping of whirl-mode flutter is reduced. An unstable wobbling motion plus an external force, such as clear air turbulence, might result in structural disintegration of the wing.
Lockheed redesigned the engine mounts, nacelles, and cowlings, and modified the wing to improve strength capabilities. No Electra accidents have resulted from whirl-mode flutter since.
Civil Aeronautics Board Aircraft Accident Reports:
Civil Aeronautics Board Aircraft Accident Reports:
Section 4b.308, "Flutter, Deformation, and Vibration," of the Civil Aviation Regulations (4b.308).
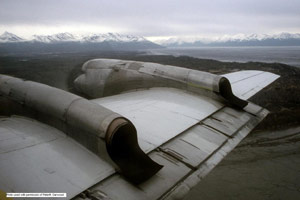
Photo copyright Peter M. Garwood - used with permission
At the time of its introduction into service, the Lockheed Electra provided a significant advance in airplane/engine technology. Past designs had employed relatively low horsepower reciprocating engines, driving relatively smaller diameter, narrow chord propellers.
The Lockheed Electra introduced turboprop engines of approximately 5000 horsepower apiece, with large diameter, wide chord propeller blades, capable of producing high levels of thrust or, at low power settings, high drag. At high power settings, the propellers also produced a large, high velocity airflow across the wing, enhancing its ability to generate lift, much the same as in more modern short takeoff and landing (STOL) type airplanes.
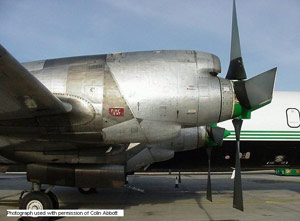
Photo copyright Colin Abbott - used with permission
Typical landing techniques for the older designs involve reducing engine power to idle at a relatively high altitude above touchdown, with a short glide and landing flare. However, use of these older landing techniques with the Electra results in a large increase in propeller drag when the thrust is reduced to idle. And the sudden lack of airflow across the wing causes a reduction of wing lift, producing a high sink rate close to the ground. The two combined effects increase the potential for a very hard landing. A more effective technique, which wasn’t fully understood by aircrews transitioning into the Electra, was to fly the airplane onto the runway while slowly reducing power, reaching idle only as the wheels touched. At the time of these two accidents, hard landings in the Electra were a relatively common occurrence, until the pilots learned these new landing techniques. The significance of the “hard landing” phenomenon was the accompanying damage and/or failure to the engine mount structure. The engine was mounted on a highly cantilevered strut, and a hard landing produced engine mount loads that could result in failure of the engine mount structure. With a failed mount, the natural frequency of the engine/nacelle became more closely matched with the natural frequency of the wing, raising the probability of developing whirl-mode instability.
The Electra exhibited the phenomenon known as whirl mode in which the stiffness of the engine mounts interacts with the gyroscopic torques produced by the engine and propeller. This interaction resulted in an unstable wobbling motion that coupled with the torsional natural frequency of the wing structure and caused catastrophic failure of the wing.
1) The original engine mounting system of the Electra was dynamically stable.
2) During the original certification, the Electra was equipped with Allison engines and Aeroproducts propellers. Certification included a vibratory stress survey of the propellers. It was determined, based on experience, that the inboard propellers were more critical, and only the inboard propellers were instrumented. Later, a Hamilton Standard propeller was installed on the airplane and a supplemental type certificate was sought. At this time, it was decided that a vibratory stress survey on one outboard and one inboard propeller was to be conducted. As a result of this test, it was found that the outboard propellers were more highly stressed than the inboard propellers and that these stresses exceeded acceptable levels.
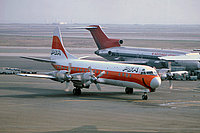
Photo copyright Richard Silagi - used
with permission
Following the Electra accidents, CAR 4b was revised, in October 1964, to add new aeroelastic requirements to CAR 4b.308. The preamble to
Amendment 16 of CAR 4b and the Notice of Proposed Rulemaking for CAR 4b.308 describe the changes to the regulation, specifically requiring the consideration of the effects of "forces associated with rotations and displacements of the plane of the propeller." The preamble material referred to the two Electra accidents, and required the consideration of the effects of failures of airplane structure, including engine mounts, on the aeroelastic stability of an airplane design. The amended rule also required consideration of the failure of other structural elements for which fatigue and/or fail-safe analyses had been performed per 4b.270, and for elements of the flight control system.
During this same period, 14 CFR part 25 was codified, and 14 CFR 25.629 was adopted in November, 1964, as part of the original publication of part 25. 25.629 adopted the requirements of CAR 4b.308, and also added a more specific speed envelope inside which an airplane was required to be free from flutter. In addition, 25.629 introduced fail-safe criteria, and required consideration of failures of structural elements for which fail-safe criteria/analyses had been applied. The rule further linked these criteria to fail-safe criteria in 14 CFR 25.571(c).
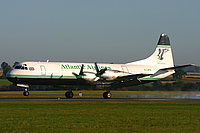
Photo copyright Terry Wade -
used with permission
In 1978, as a response to other accidents, 14 CFR 25.571 was re-titled, and amended to introduce the concept of damage tolerance in relation to damage resulting from fatigue of principal structural elements. Damage tolerance has become the preferred choice for managing fatigue related damage. The Lockheed Electra accidents along with others, including the fatigue failure of a 707 fail-safe horizontal stabilizer, began the evolution that culminated in the damage tolerance regulations. These early accidents led to the first steps in a series of steps in the development of damage tolerance regulations.
Damage tolerance is a fatigue management philosophy based on maintaining safety through the use of inspections. Fatigue is a progressive mechanism. Material degradation due to a cyclical repetition of loads results in the nucleation and propagation of cracks which can culminate in complete structural failure.
While not directly related to the development of the damage tolerance regulations, the Electra accidents contributed to a re-evaluation of the mechanisms by which airplane structure can fail and led to a more comprehensive approach in assuring structural integrity in the operational fleet. By utilizing a program of managed inspections to detect damage resulting from manufacturing, accidents, fatigue, and environmental damage (i.e. corrosion) before these factors can degrade the structural strength below specified levels, 25.571 attempts to address all damage tolerance based accident causes and contributing factors. In addition to fatigue, 25.571 also defines the requirements for safe-life structure, and addresses structural damage resulting from rotor burst, bird strike, and sonic fatigue.
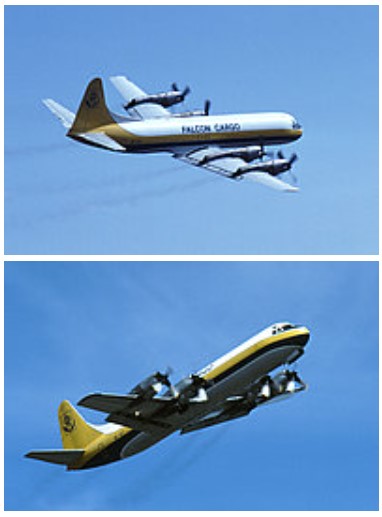
Photos copyright Tom Edvardsson - used with permission
On March 20, 1960, the FAA issued, as a temporary measure, an emergency AD applicable to LOCKHEED Model 188 series airplanes: To reduce the maximum structural cruising speed (Vno) from 324 knots calibrated air speed (CAS) to 275 knots CAS.
On March 25, 1960, the FAA issued a second emergency AD, AD 60-09-03, amendment 134, applicable to LOCKHEED Model 188 series airplanes: To limit Vno to 225 knots CAS and establish a never-exceed speed (Vne) of 245 knots CAS. Also included were requirements for immediate propeller feathering if the torque meter indicator registered zero or full scale; deactivation of the autopilot until appropriate modifications could be designed and installed; and adherence to Lockheed prescribed procedures in refueling operations.
Airplane Life Cycle
- Design / Manufacturing
Accident Threat Categories
- Structural Failure
Groupings
- N/A
Accident Common Themes
- Flawed Assumptions
- Pre-existing Failures
- Unintended Effects
Flawed Assumptions
1) The original engine mounting system was dynamically stable.
2) During the original certification of the Electra, the airplane was equipped with Allison engines and Aeroproducts propellers. Certification included a vibratory stress survey of the propellers. It was determined, based on experience, that the inboard propellers were more critical, and only the inboard propellers were instrumented. Later, a Hamilton Standard propeller was installed on the airplane and a new supplemental type certificate. At this time, it was decided that a vibratory stress survey on one outboard and one inboard propeller was to be conducted. As a result of this test, it was found that the outboard propellers were more highly stressed than the inboard propellers and that these stresses exceeded acceptable levels.
Pre-existing Failures
A major cause of these two accidents was the pre-existing failure of the engine mount structure. As a result of one or more hard landings, the engine mounting structure had suffered undiscovered failures. The resultant loss of stiffness in the engine mount structure changed the fundamental vibratory frequencies to nearly the same as those for the wing structure. This allowed a coupling of the whirl-mode induced engine vibrations with the wings, and the subsequent wing failures.
Unintended Effects
The capability of the engines to develop high levels of thrust, in combination with the large diameter, wide chord propeller blades capable of absorbing the horsepower output of the engines, resulted in enhanced lift effects on the wing, and a high propeller drag configuration at low power settings. These factors resulted, at introduction into service, in a high incidence of hard landing events, and failure of engine mount structure, eventually resulting in a coupling of wing and engine/nacelle natural frequencies, and destructive whirl mode flutter. This realization ultimately became the key to the accident investigation.
Technical Related Lessons:
High inertia rotating systems, (e.g. propellers), can exhibit unstable whirl mode characteristics which can be influenced by engine mount stiffness. (Threat Category: Structural Failure)
- The Electra exhibited the phenomenon known as whirl mode in which the stiffness of the engine mounts interacts with the gyroscopic torques produced by the engine and propeller. This interaction results in an unstable wobbling motion that could resonate with natural frequencies of the wing structure and could cause catastrophic failure of the wing.
Airplane structure should be sufficiently robust that anticipated usage, and expected inservice damage, do not result in a catastrophic outcome. (Threat Category: Structural Failure)
- The Electra L-188 landing characteristics resulted in a relatively high percentage of hard landing events in the early days of service. These events, in combination with the large overhung engine/propeller mount arrangement, resulted in some instances of hard landings, causing the upper engine mount of the five-mount system to break. Since this upper mount failure was not detectable during normal walk arounds (the engine did not "droop"), this condition constituted hidden damage. This damage condition, and the resulting catastrophic outcome, gave rise to the concept of "damage" capable structure, and is now a requirement for all transport airplane structural designs. This concept evolved into "damage tolerance", and is currently an attribute where expected structural damage from fatigue is found to not pose a hazard for a period of time sufficient to allow the damage to be discovered and repaired. Other damage events, such as bird strikes, fuselage openings, etc, are addressed in other specific requirements within 14 CFR part 25.
Common Theme Related Lessons:
New aircraft entering service can introduce new features and operational characteristics which are unfamiliar to their operators. Particular attention should be paid to difficulties being experienced due to this unfamiliarity and the potential hazards (e.g., hard landings, difficulty in performing servicing tasks, etc) that can result. (Common Theme: Unintended Effects)
- The early difficulty in landing the Electra L-188 is not unusual in the history of introduction of new technology with new features or flying characteristics (e.g. jet engines, ground proximity warning systems, GPS navigation, TCAS, electronic flight displays, autopilots, etc.). As these challenges are being observed, care should be given to consideration of the effects that these challenges might be having on the airplane's airworthiness, or the safety of its operation.