Boeing 737-275
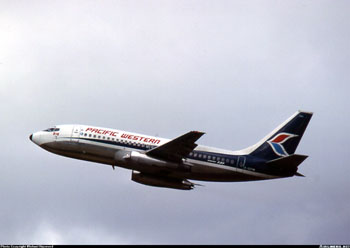
Photo copyright Michael Haywood - used with permission
Pacific Western Airlines Flight 314, C-FPWC
Cranbrook, British Columbia, Canada
February 11, 1978
A Boeing Model 737-275, powered by two Pratt & Whitney JT8D-9A engines, and operated by Pacific Western Airlines, crashed during landing at Cranbrook, British Columbia, Canada. The accident was determined to be the result of a loss of control during an attempted go-around after touchdown. This loss of control was the result of a thrust asymmetry following an incomplete stowage of the thrust reversers. The accident killed 42 of the 49 people on board.
Reverse thrust was selected on both engines upon touchdown, then immediately cancelled because of a need for a go-around in order to avoid collision with a snow removal vehicle on the runway. The aircraft lifted off and cleared the vehicle. However, the thrust reverser stow sequence was interrupted at liftoff, leaving the reversers in a partially deployed position. By design, hydraulic pressure used for the thrust reverser deploy/stow cycle was shut off as the aircraft became airborne. The thrust reverser on the right engine stowed fully and regained forward thrust, while the reverser on the left engine failed to fully stow and, following liftoff, gradually deployed fully due to aerodynamic loads. The resulting thrust asymmetry caused a loss of roll control, and the subsequent crash.
History of Flight
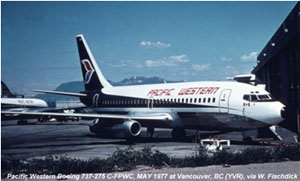
Photo copyright Werner Fischdick Collection - used with permission
Pacific Western Flight 314 was a scheduled passenger flight from Edmonton, Alberta (AB) to Castlegar, British Columbia (BC) in Canada, with intermediate stops in Calgary, AB and Cranbrook, BC. The flight departed Calgary at 12:32 local time on February 11, 1978, and headed for Cranbrook. After departure from Calgary, Calgary Air Traffic Control (ATC) transmitted an estimated time of arrival (ETA) of 13:05 to the Cranbrook Aeradio station. Cranbrook was an uncontrolled airport where an Aeradio station provided communications, weather, and advisory service. It was snowing in Cranbrook with visibility reported as three-fourths of a mile, and a radio-equipped snow removal vehicle was sweeping the runway. The Cranbrook Aeradio operator alerted the snow removal vehicle operator about the incoming aircraft at 12:35 and provided an ETA for Flight 314 of 13:05. The accepted arrival procedure at the time was that the flight would provide a position report upon arrival at the "Skookum" radio beacon. Both the Aeradio and vehicle operators expected that Flight 314 would make a position report prior to executing a straight-in approach to runway 16. The Skookum beacon was a non-directional beacon (NDB) located about 20 nautical miles (23 miles) north of Cranbrook airport and used for an instrument landing system (ILS) approach. Position reporting at the Skookum beacon would give the vehicle operator about seven minutes to exit the runway.
At 12:42, Flight 314 called Calgary ATC and requested descent clearance. Calgary ATC gave clearance for the approach to Cranbrook. At 12:46, Flight 314 made contact with the Cranbrook Aeradio station. At 12:47, the Aeradio station advised Flight 314 that snow removal was in progress and an update on the runway condition would be provided. The Aeradio station also gave the latest visibility. Flight 314 replied by simply stating "three fourteen checks." No further transmissions from the aircraft were received by the Cranbrook Aeradio station or Calgary ATC. A couple of minutes later, Flight 314 passed the Skookum beacon inbound on a straight-in approach to runway 16. No position report was made by Flight 314.
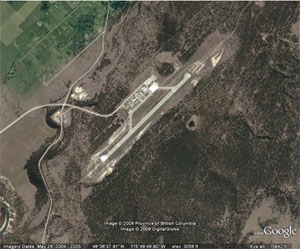
Flight 314 touched down on runway 16 at 12:55, ten minutes earlier than the ETA of 13:05 that had been projected after departure from Calgary one half hour earlier. Snow removal was still ongoing on the runway. Upon touchdown, the pilot selected reverse thrust as part of the normal landing sequence, and then became aware of the snow removal vehicle approximately 1,250 feet ahead. The pilot immediately cancelled reverse thrust and rotated the nose to initiate a go-around. During this sequence, the right thrust reverser stowed fully, but the left reverser remained partially deployed due to the loss of hydraulic "muscle" when the airplane lifted off. The aircraft became airborne before reaching the vehicle and flew down the runway at a height of 50 to 70 feet. About the time the aircraft flew over the snow removal vehicle, the left engine thrust reverser, which had not completely stowed after the cancellation of reverse thrust, deployed fully. Following liftoff, the flaps were selected from the 40-degree landing configuration to the 15-degree takeoff configuration. The landing gear remained down and locked. A few seconds after the selection of the 15-degree flap setting, the aircraft experienced a considerable yaw to the left followed by a roll to the left. Both pilots applied full right rudder and aileron in an attempt to correct the roll and yaw. The aircraft climbed to 300 to 400 feet above the airfield, banked steeply to the left, lost height, and impacted the ground to the left of the runway. Fire broke out on impact.
Evidence indicated that the thrust reverser on the left engine had been fully deployed at the time of impact. The right thrust reverser was in a nearly stowed position. The forward thrust levers for the left and right engines were found staggered apart. The left engine throttle was at or near idle, while the throttle for the right engine was at approximately full power.
View the Cranbrook Flight Path Animation below:
Thrust Reverser Design
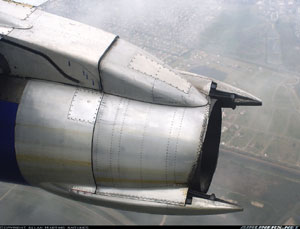
Photo copyright Allan Martins Antunes - used with permission
For the accident Boeing 737-275 aircraft, each Pratt & Whitney JT8D-9A engine was equipped with a clamshell-type (also called bucket-type) thrust reverser. A clamshell-type reverser uses two deflector doors, an upper and a lower door, installed on the aft end of the engine. When forward thrust is selected, those deflector doors are stowed and form the external cowling around the engine exhaust nozzle. When reverse thrust is selected, the deflector doors are moved aft and rotated to the position of about 30 degrees from the vertical in order to block and redirect the turbine exhaust gas flow. Exhaust gases are deflected forward and result in reverse thrust, which is directed rearward, instead of forward.
Control of Thrust Reverser
Thrust reverser operation is accomplished by manually moving a reverse thrust lever (also called "piggyback" lever) mounted on top of the forward thrust lever at the control stand in the cockpit. Left and right reverse thrust levers are available for independent operation of the thrust reversers installed on the left and right engines.
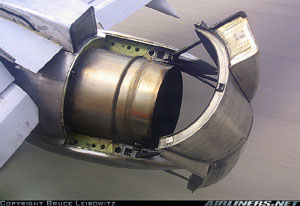
Photo copyright Bruce Leibowitz - used with permission
To move the reverse thrust lever, the forward thrust lever must be at the idle position. This prevents an inadvertent deployment of thrust reversers during forward thrust operation. Similarly, the reverse thrust lever must be at the stow position in order to advance the forward thrust lever. A lockout mechanism prevents simultaneous movement of the forward and reverse thrust levers. The lockout utilizes a pawl attached to the forward thrust lever and a lockout hole in the web of the control stand cover. When the forward thrust lever is at the idle position, the pawl is aligned with the lockout hole. As the reverse thrust lever is moved from the stow position, the control link that connects the reverse thrust lever and the thrust control drum forces the pawl into the lockout hole, causing to lock the forward thrust lever at the idle position. When the forward thrust lever is forward of the idle position, the pawl is not aligned with the lockout hole. Under this condition, the reverse thrust lever is locked in the stow position because the force of the control link, which is applied on the pawl when the reverse thrust lever is moved, is opposed by the control stand web. (See the figure)
In conjunction with the reverse thrust lever, the following three components are engaged in the thrust reverser operation: 1) a hydraulic isolation valve, 2) a directional control valve, and 3) hydraulically operated actuators.
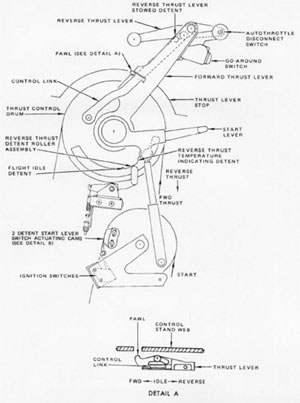
View Large
One hydraulic isolation valve is installed for each thrust reverser. The isolation valve is arranged between the aircraft hydraulic source and the directional control valve. It is spring loaded to the closed position, shutting off hydraulic pressure supply to the directional control valve. As the landing gear is compressed upon touchdown, an air-ground switch is closed, allowing electrical power to be sent to the isolation valve. The isolation valve opens when it is energized.
One directional control valve is installed for each thrust reverser. The directional control valve is arranged between the isolation valve and thrust reverser actuators. As the isolation valve opens and hydraulic pressure becomes available for reverser operation, the routing direction of the hydraulic fluid is controlled by the directional control valve. The directional control valve is mechanically linked to the reverse thrust lever; it is oriented to either the forward thrust or reverse thrust position, depending on the position of the reverse thrust lever. Through this valve, hydraulic pressure is applied to an appropriate port of the thrust reverser actuators.
A total of four actuators are used for the operation of each thrust reverser. Two actuators are used for locking purposes; they either lock or unlock a pair of the deflector doors at the stow position. The other two actuators are used for positioning the deflector doors; they provide mechanical force to move the deflector doors between the deploy and stow positions.
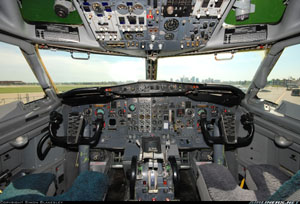
Photo copyright Simon Blakesley – used with permission
View Larger
When reverse thrust is selected, hydraulic pressure is applied to the unlock port of the locking actuators and the deploy port of the positioning actuators. Since less pressure is required to operate the locking actuators than the positioning actuators, the locking actuators retract to the unlock position first. The retraction of the locking actuators unlocks the door latches. As sufficient pressure builds up, the positioning actuators retract and move the deflector doors through a linkage assembly toward the deploy position.
When forward thrust is selected, hydraulic pressure is applied to the lock port of the locking actuator and the stow port of the positioning actuators. The locking actuators extend to the lock position, but the door latches remain unlocked until the doors are fully stowed. The deflector doors are retracted toward the stow position as the positioning actuators extend. The deflector doors mechanically snap the lock latches into the locked position.
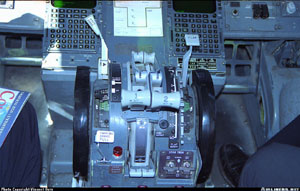
Photo copyright Vincent Gury – used with permission
A mechanical interlock is provided, integral to the flight deck aisle stand, as a safety feature to allow only idle thrust when the deflector doors are in transit between the stow and deploy positions. For reverse thrust operation, the reverse thrust lever is initially moved aft to an interlock position. Movement of the reverse thrust lever beyond that position is prohibited by the mechanical interlock. Initial lever movement initiates the deployment of the deflector doors while maintaining a low thrust setting. As the deflector doors approach the fully deployed position, the interlock allows the reverse thrust lever to move further aft for application of higher reverse thrust. Similarly, when the deflector doors are in transit toward the stow position, the mechanical interlock prohibits movement of the forward thrust lever beyond the interlock position until the deflector doors have almost reached the stow position.
The mechanical interlock also limits the thrust setting if the deflector doors are not in the correct position for the selected thrust condition. If the deflector doors inadvertently move to the deploy position during forward thrust operation, a cable feedback system forces the thrust setting to idle. Similarly, if the deflector doors inadvertently move to the stow position during reverse thrust operation, the thrust setting is also reduced to idle reverse.
View the Clamshell-type Thrust Reverser Animation below:
Procedure for stowing thrust reversers in flight
The thrust reverser is intended for ground use only. As the aircraft lifts off the ground, the isolation valve closes, and hydraulic pressure becomes unavailable for thrust reverser operation. If the deflector doors are not fully stowed before liftoff, they cannot be retracted to the stow position through a normal procedure since there is no available hydraulic pressure to accomplish the stow command. The only way to regain the control of the deflector doors from the cockpit is to move a thrust reverser override switch, located in the overhead panel, from the "normal" position to the "override" position. This will open the isolation valve, provided the landing gear has been extended. Two switches, one each for the left and right thrust reversers, are located on the overhead panel behind the pilot. Since those switches are provided for maintenance purposes only, they are guarded, and safety wired closed.
Unintended deployment of thrust reversers and subsequent aircraft controllability
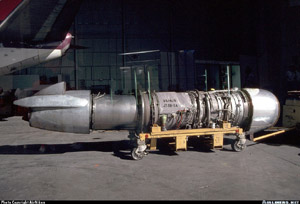
Photo copyright AirNikon Collection Pima Air and Space Museum - used with permission
In the accident flight sequence, reverse thrust was selected upon touchdown and then cancelled. An attempt to advance the forward thrust levers to takeoff power was made, but the airplane lifted off prior to the completion of the reverser stow cycle. This prevented the left reverser from being completely stowed, and further prevented the left thrust lever from being advanced beyond the idle position. By design, the forward thrust levers could be advanced from the idle position if the reverse thrust levers had been returned to the stow position and the deflector doors were nearly stowed. The Boeing Company conducted flight tests in order to study the effect of aerodynamic loads on the deflector doors at a partially deployed position. This study indicated that aerodynamic loads could be sufficient to move the deflector doors to the fully deployed position, depending on the initial door position. This finding was also confirmed by a similar study conducted by Pacific Western Airlines. In the Boeing flight tests, once the deflector doors started moving away from their nearly stowed position, the doors became fully deployed in approximately eight seconds.
As aerodynamic loads moved the deflector doors toward the deploy position, the associated forward thrust lever also moved to the flight idle position. This was due to the cable feedback system, which would prevent disagreement between the deflector door position and the forward thrust lever position. In the case of inadvertent in-flight deployment of the deflector doors, the system would retard the forward thrust lever to the flight idle position. In the Boeing flight tests, the forward thrust lever started retarding while the deflector doors were in transit toward deployment and moved to the idle position in approximately 2.5 seconds.
The Boeing Company also investigated controllability of the aircraft with one engine at idle reverse and the other engine at almost full-forward thrust. This investigation revealed that the aircraft could be controlled, depending on flap and landing gear configurations. The flight tests showed that the aircraft was controllable with the gear up and the flaps at 15 degrees. When the flaps were in transit from 40 degrees to 15 degrees with the landing gear extended, control of the aircraft was possible but marginal.
Flight Crew Response
The pilots of Flight 314 saw the snow removal vehicle on runway 16 after the aircraft touched down and reverse thrust was selected. It was possible that the vehicle on the runway was hidden from the pilots' sight by snow thrown up by the vehicle, in addition to being obscured by reduced visibility in falling snow. There were no applicable procedures or training which addressed this situation. A go-around after selecting reverse thrust had been cautioned against in the Boeing 737 Operations Manual. The decision to execute a go-around required a number of prompt actions in the cockpit: cancelling the reverse thrust selection, advancing the forward thrust levers, moving the flap selector lever from the full landing flap position to the 15-degree position, and raising the landing gear after liftoff. After being on the runway for only about 2.5 seconds, Flight 314 lifted off and then cleared the vehicle. However, the landing gear was left down throughout the go-around sequence, and the flap selection to the 15-degree position was not made until about seven seconds before impact.
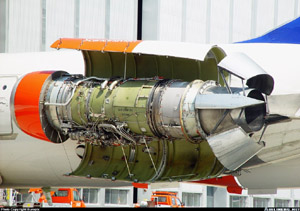
Photo copyright Europix - used with permission
As aerodynamic loads began moving the deflector doors on the left engine toward the deploy position, the associated forward thrust lever also started moving toward the idle position. Consequently, the left engine reduced its power to flight idle, while the right engine remained at near takeoff power. This asymmetric thrust would have caused the aircraft to yaw to the left. The fact that the aircraft maintained its straight flight for a few seconds indicated that right rudder had been applied to counteract asymmetric thrust.
Full details of the actions in the cockpit and the reactions of the aircraft were unknown due to loss of flight recorder data. However, evidence indicated that a considerable yaw to the left occurred, followed by a roll to the left about six seconds before impact. Accident investigators suspected that either the removal of right rudder application or a momentary application of left rudder caused this considerable yaw. Such an undesirable action at a critical phase of the flight might have been an inadvertent action associated with an attempt to reach the thrust reverser override switch. Evidence indicated that the guard for the left thrust reverser override switch had been moved to the open position. The safety wire on the guard had been broken, and the switch was exposed but had not been moved from the normal position.
Go-Around Instruction in the Boeing 737 Operations Manual
The accident airplane was manufactured in 1970. In the Boeing 737 Operations Manual available to Pacific Western Airlines, the following "caution" regarding a go-around appeared as an amendment to the manual, dated September 20, 1977:
- "Do not attempt a go-around after reverse thrust has been initiated. Failure of a thrust reverser to return to the forward thrust position may prevent a successful go-around"
The thrust reverser design for the Boeing 737-200 was in compliance with the applicable FAA standards under which the aircraft was constructed. The ability to abort landing after touchdown and reverse thrust selection was not considered an appropriate operational procedure and was therefore not addressed by FAA design standards for transport airplanes.
Safety Vulnerability
Instrument Approach to an Uncontrolled Airport
Flight 314's failure to report its position on final approach was the primary cause of the traffic conflict on runway 16 at Cranbrook. Transport Canada examined Canadian aviation regulations and other documents related to instrument flight and position reporting procedures to determine their applicability to the instrument approach procedures at Cranbrook.
Transport Canada concluded that an intent of the document, entitled "Flight Planning and Procedures Canada and North Atlantic," was that the pilot should provide position reports on final approach. However, there was no obligation for a pilot to do so because that document was considered informational in nature and was not regulatory. Transport Canada also interviewed pilots from Pacific Western Airlines and other organizations to ascertain what communication procedures were used for landing at uncontrolled airports such as Cranbrook. The consensus among those pilots was that once an ATC clearance for the approach had been given, there was no obligation to pass a further position report unless requested by ATC. However, the pilots were unanimous that it would be good airmanship to make position reports on every approach regardless of the legal requirements. Transport Canada confirmed that each Pacific Western Airlines crew passed a position report to Cranbrook when inbound during the three days prior to the accident.
Procedures for Controlling Maintenance Vehicle Operation
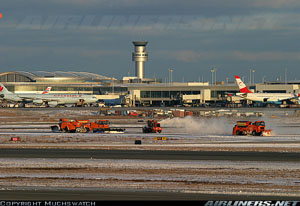
Photo copyright J. J. Cai - used with permission
When Flight 314 departed Calgary, a maintenance vehicle was in process of removing snow on runway 16 at Cranbrook. Such a maintenance activity was necessary to maintain the runway in a serviceable condition and was allowed to operate between flight arrivals and departures. Procedures for controlling the maintenance vehicle activities were provided in the manuals entitled "Telecommunications, Maintenance and Operations Manual" and "Recommended Vehicle Operating Procedures at Airports." According to those manuals, Aeradio and vehicle operators were required to maintain close communication, so that maintenance vehicles would remain clear of all runways and taxiways where aircraft operation was occurring or expected to occur. At Cranbrook, the Aeradio operator alerted the vehicle operator about the incoming aircraft at 12:35 and gave him the ETA of 13:05.
At 12:47, the Aeradio operator also advised Flight 314 that snow removal was in progress, and Flight 314 acknowledged. This communication appeared to agree with the following procedure provided in one of the manuals:
- The presence of vehicles in the maneuvering area of an airport shall be transmitted to incoming aircraft in the text of Airport Advisory messages even when these vehicles are not located on the runway in use.
After Flight 314's acknowledgement at 12:47, no further transmission from Flight 314 was received by the Cranbrook Aeradio station or Calgary ATC. At 12:55, ten minutes earlier than the ETA of 13:05, the snow removal vehicle was still in operation when Flight 314 touched down on runway 16. One of the manuals provided the following procedure indicating when vehicles should be removed from the runway prior to aircraft arrival:
- Vehicles shall be advised by radio or by alternate means to leave a runway five minutes prior to an estimated aircraft arrival and immediately prior to the time a departing aircraft is ready to commence taxiing to the point of takeoff.
In order for the above procedure to be effective, ETAs had to be accurate. For this accident flight, the ETA generated by Calgary ATC was in error by ten minutes, and it was never updated during the flight. The error in the ETA could have been detected by a position report from Flight 314 on final approach. Position reporting was important particularly at an uncontrolled airport with only an advisory service. However, Flight 314 did not report its position on final approach, and as a result, it touched down at Cranbrook before the operator of the snow removal vehicle was advised to leave the runway.
Communication Practices in the Cockpit
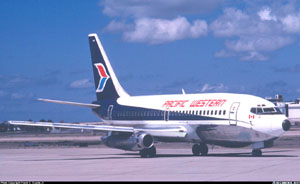
Photo copyright Frank C. Duarte Jr. - used with permission
In addition to the failure of position reporting on final approach, accident investigators suspected that the captain of Flight 314 was not aware of the runway information provided by the Cranbrook Aeradio station. During an instrument approach, it was usual for the captain to monitor all flight deck activities including radio communications made by the first officer. Evidence indicated that one VHF transceiver was on a company frequency during the time the runway information was transmitted by the Cranbrook Aeradio station. Pilots on two different aircraft operating in the area during that time reported hearing the captain of Flight 314 conversing with another flight on company frequency. The first officer of Flight 314, who replied to the Cranbrook Aeradio station, might not have passed the runway information to the captain. Furthermore, accident investigators considered that the first officer's reply to Cranbrook, which was simply "three fourteen checks," provided no assurance that he received the entire message. The investigation concluded that the failure to report on final approach and the unnecessary talk on company frequency represented an unacceptable standard of cockpit practice and discipline.
The accident was investigated by Transport Canada, Aviation Safety Bureau, Aviation Safety Investigation Division. Eight findings were issued covering a variety of subjects. The most pertinent findings were related to operational aspects which caused a traffic conflict at Cranbrook. One finding was related to the FAA design standards under which the Boeing 737-200 was constructed. The complete text of the findings is available at the following link: Accident Board Findings
The entire report of the Cranbrook accident investigation is available at the following link: Accident Report
Design Standards - Thrust Reversers
14 CFR, §25.933: Reversing Systems
(a) requires that no single failure or malfunction of the reversing system will result in unwanted reverse thrust under any expected operating condition for reversing systems intended for ground operation only.
(b) requires that no unsafe condition will result from any failure or likely combination of failures for reversing systems intended for in-flight use.
(c) establishes propeller reversing system low-pitch requirements.
Effective 2/1/1965
Operational Standards - Uncontrolled Airports (Canada)
At the time of this accident, the Canadian aviation regulations in effect were the Air Regulations and Air Navigation Orders. Under those regulations, there was no legal requirement for a pilot to make position reports during an instrument approach unless requested by ATC. Transport Canada concluded that regulatory provisions concerning mandatory pilot position reporting during instrument approaches were inadequate.
The Transport Canada Aeronautical Information Manual (TC AIM) also provides information concerning the rules of the air and procedures for aircraft operation in Canadian airspace. Operational procedures pertaining to flight in the vicinity of an uncontrolled airport are provided in section 4.5 of "RAC - Rules of the Air and Air Traffic Services" in the TC AIM. Procedures for the pilot establishing communications with an air-to-ground facility at an uncontrolled airport are provided in RAC 9.11. The required reporting procedures of CAR 602.104 are provided in RAC 9.12.
An example of the Transport Canada Aeronautical Information Manual, effective October 22, 2009, is available at the following link: TC AIM 2009-2010
During the investigation of the Cranbrook accident, Transport Canada noted that pilots had not in all cases reported operating irregularities to their companies, or through their companies to the manufacturer or to Transport Canada. In addition, pilots and other personnel had been lax in reporting traffic conflicts at uncontrolled airports, and there was no well defined system or procedure for them to do so. Investigators concluded that this situation, combined with the lack of a formal investigation and collation procedure, allowed problems to persist.
- Attempting a go-around after selecting reverse thrust. The Boeing Model 737-200 airplane was not certified with the ability to accomplish the "Cranbrook maneuver." The Boeing 737-200 Operations Manual cautioned against a go-around after the selection of reverse thrust.
- Failure to provide adequate position reports relative to landing at uncontrolled airports, resulting in a vehicle on the runway at the time of airplane landing.
- Flight crew would report the aircraft position on final approach. Position reporting on final approach could detect any error in the ETA and therefore could avoid the traffic conflict between the landing aircraft and authorized vehicles on the runway. Position reporting was commonly practiced at Cranbrook but was not mandated by regulations.
- A go-around would not be attempted following touchdown and deployment of thrust reversers.
Transport Canada noted that there were many incidents of go-around due to runway obstacles or related communication problems at uncontrolled airports. However, only five had been formally investigated and documented. There was no effective system for reporting, investigating, and documenting such incidents, and collating the resulting information in a suitable location.
Thrust Reverser Requirements
The Boeing Model 737-200 airplane was certified in December 1967. The certification was accomplished under the regulations in effect at the time of application for type certificate. The certification basis was Code of Federal Regulations 14 CFR part 25, amendments 25-1 through 25-3, 25-7, 25-8, and 25-15. The regulation pertinent to the thrust reverser design was 14 CFR 25.933 which required that no single failure or malfunction of the reversing system would result in unwanted reverse thrust under any expected operating condition for reversing systems intended for ground operation only.
After becoming effective on February 1, 1965, 14 CFR 25.933 was revised multiple times. Amendment 25-11, effective June 4, 1967, revised 14 CFR 25.933 by adding a requirement for each turbojet reversing system to have means to prevent the engine from producing more than "idle forward thrust" when the reversing system malfunctions.
Amendment 25-40, effective May 2, 1977, revised 14 CFR 25.933 to require that the engine will produce no more than flight idle thrust under all cases of in-flight thrust reversal of a reverser intended for ground operation only. In addition, either one of the following capabilities were required to be shown: 1) the reverser can be restored to the forward thrust position; or 2) the airplane is capable of continued safe flight and landing under any possible position of the thrust reverser.
It became apparent that demonstrating the capability to stow an undamaged reverser would not assure that the reverser damaged during an unwanted in-flight deployment could be stowed. Because an unwanted in-flight deployment was generally accompanied by damage to the reversing system due to the dynamic nature of the deployment, it was possible to lose in-flight stow capabilities due to unpredictable damage. Based on this consideration, Amendment 25-72, effective on August 20, 1990, revised 14 CFR 25.933 to require both of the following capabilities to be shown: 1) each operable reverser can be restored to the forward thrust position; and 2) the airplane is capable of continued safe flight and landing under any possible position of the thrust reverser.
At the time of the Cranbrook accident, the Canadian aviation regulations in effect were the Air Regulations and Air Navigation Orders. The Air Regulations mandated airworthiness standards specified in the Airworthiness Manual. Airworthiness standards for transport category airplanes were specified in Airworthiness Manual Chapter 525, whose content was based on U.S. Title 14 Code of Federal Regulations (CFR), Part 25. The first issue of Airworthiness Manual Chapter 525 became effective on July 1, 1986.
Transport Canada issued Airworthiness Manual Advisory (AMA) 525.933, dated May 1, 1986, to provide guidance on acceptable means of demonstrating compliance with standards pertaining to the operations of thrust reversing systems. Airworthiness standards addressed in AMA 525.933 were Airworthiness Manual Chapter 525, Sections 525.143, 525.933, 525.1155, and 525.1581.
AMA 525.933 was superseded by AMA 525/3, dated August 24, 1988. In addition to those standards identified in AMA 525.933, AMA 525/3 included Section 525.905 to address consideration on turbine engine propeller reversing systems.
AMA 525/3 was then cancelled and updated to Advisory Circular (AC) 525-005, "Operation of Thrust Reversing Systems" with an effective date of December 1, 2004. With the exception of minor editorial changes, the content of AC 525-005 is identical to that of AMA 525/3. AC 525-005 provides Transport Canada's interpretation of the requirements of Section 525.143.
Section 525.143 requires that the airplane be safely controllable and maneuverable during takeoff and landing, and that it must be possible to make a smooth transition from one flight condition to any other flight condition without exceptional pilot skill, alertness, or strength under any probable operating condition, including configuration changes such as deployment or retraction of deceleration devices.
According to AC 525-005, Transport Canada's interpretation of the requirements of Section 525.143 includes a go-around following landing touchdown and selection of reverse thrust. Therefore, airplanes operated in Canada must show their capability to accomplish the "Cranbrook maneuver," which involves the following sequence: touchdown, deploy the thrust reversers, stow the reversers, generate forward thrust, and safely fly away.
Compliance with applicable standards may be shown by acceptable analysis or a combination of acceptable analysis and test. AC 525-005 also requires the applicant to demonstrate that there is no hazard such as:
- Becoming airborne with an unlocked thrust reverser
- One engine developing forward thrust and the other reverse thrust
- Insufficient system capability to handle the peak system demands
- Power control anomalies which would allow the power levers to be pushed forward before the thrust reversers were fully stowed, and hence result in reverse thrust
AC 525-005 also requires an aircraft flight manual limitation prohibiting a go-around following thrust reverser deployment, but such a limitation is not considered adequate, by itself, to demonstrate compliance with applicable standards.
Comparison of FAA and Transport Canada Thrust Reverser Requirements
Thrust reverser design criteria are addressed by both authorities within 14 CFR 25.933 (FAA), and Airworthiness Manual Chapter 525.933 (Transport Canada). Further, Transport Canada has issued Advisory Circular 525-005, "Operation of Thrust Reversing Systems," which provides guidance on compliance to 525.143, Airplane Controllability. A portion of the material contained in the AC interprets 525.143 to include the "Cranbrook maneuver" as part of the airplane controllability compliance findings associated with this rule. A similar airplane controllability advisory circular, addressing thrust reverser functioning associated with the "Cranbrook maneuver," has not been issued by the FAA.
Operation at Uncontrolled Airports
In 1996, the Air Regulations and Air Navigation Orders were consolidated into a set of new regulations entitled the Canadian Aviation Regulations (CARs). Operating and flight rules are provided in the CARs Part VI. Required reporting procedures for an instrument flight rules (IFR) aircraft when approaching to or landing at an uncontrolled airport are specified by CAR 602.104. According to CAR 602.104, the pilot-in-command of an IFR aircraft must report his/her intentions regarding the operation of the aircraft five minutes before the estimated time of commencing the approach procedure, stating the estimated landing time. The pilot-in-command must also report the aircraft position (1) when passing the fix outbound, when the pilot-in-command intends to conduct a procedure turn, or, if no procedure turn is intended, when the aircraft first intercepts the final approach course, (2) when passing the final approach fix or three minutes before the estimated landing time when no final approach fix exists, and (3) on final approach.
No Airworthiness Directives pertaining to the thrust reversers on the accident aircraft were issued by the FAA.
Airplane Life Cycle:
- Operational
Accident Threat Categories:
- Uncommanded Thrust Reversal
- Landing / Takeoff Excursions
- Midair / Ground Incursions
Groupings:
- Loss of Control
- Approach and Landing
- Automation
Accident Common Themes:
- Human Error
- Organizational Lapses
Human Error
The flight crew did not report the aircraft position on final approach to Cranbrook airport, contrary to the accepted common practice. Although there was no legal requirement for position reporting, it was a vital component in safe airport operation, allowing ground maintenance operations (in this case, runway snow removal) between airplane takeoffs or landings. Position reporting was particularly important at an uncontrolled airport with only an advisory radio service.
Organizational Lapses
The procedures for controlling maintenance vehicle activities on the runway, as addressed in airport operational manuals, were established on the basis of receiving an accurate ETA from inbound flights. There was no standard method of calculating an ETA, and the estimate produced by ATC could not be accurate enough for vehicle control purposes because a number of en route variables could affect the actual arrival time. The procedures therefore required the vehicle operator to rely on an update on the flight progress that would come from the flight crew. The assumption that a flight update or an ETA would be accurate could cause a miscommunication that may pose a serious threat on aircraft operation in the vicinity of or at an airport.
Alaska Airlines Flight 60, Boeing 727-81, N124AS, Ketchikan International Airport
On April 5, 1976, Flight 60 touched down on the wet runway beyond the normal touchdown point and at an excessive speed. After selecting reverse thrust, the captain determined that the braking action was poor and decided to execute a go-around. He attempted to obtain takeoff thrust; however, the thrust reverser mechanism did not disengage fully, and the forward thrust could not be obtained. The captain reapplied reverse thrust in an attempt to slow the aircraft. The aircraft came to rest in a ravine 700 feet past the departure end of the runway. Alaskan Airlines B-727-100 Flight Handbook, dated May 15, 1974, cautioned against the use of thrust reversers unless a full-stop landing was intended.
Ozark Airlines Flight 650, McDonnell Douglas DC-9-31, N994Z, Sioux Falls Regional Airport, South Dakota
While landing in a snowstorm on December 20, 1983, the airplane struck a snowplow on the runway. The impact ripped the right wing from the plane destroying the snowplow and killing its driver. The leaking fuel from the wing briefly created a fireball that engulfed the snowplow. The plane spun through 180° before coming to rest of the runway to the left of the center line. Passenger evacuation was initiated through the front two doors. No passengers were injured in the evacuation, but two flight attendants suffered minor injuries.
Technical Related Lessons
Takeoff or landing operations, especially at uncontrolled airports, require active, robust two-way communication to confirm that the runway is clear prior to performing those operations. (Threat Category: Midair/Ground Incursions)
- Cranbrook was an uncontrolled airport, where operations were monitored by an advisory radio service, providing guidance to both air traffic and ground vehicles. Traffic conflicts were intended to be mitigated by the combination of position reports from aircraft and advisory information from ground vehicles that the runway was clear, or that ground vehicles were currently on the runway. In this accident, Flight 314 did not make an expected position report, which resulted in a snow removal vehicle being on the active runway when the flight arrived. Had a robust communication chain been established, both the airplane and the snow removal vehicle would have been aware of the other's presence.
Common Theme Related Lessons
Safety processes should be sufficiently robust that the failure of any single individual to perform a task should be consistently counteracted by standard operating procedures, and prevent the occurrence of a catastrophic event. (Common Theme: Organizational Lapses)
- On initial communication with Cranbrook Aeradio, approximately ten minutes prior to landing, Flight 314 was advised that snow removal equipment was on the runway. Rather than request further information relative to runway status, Flight 314 acknowledged the information, but did not request to be informed when the runway was clear, nor confirm that landing could proceed without any traffic conflicts. Both the Aeradio operator, and the snow removal equipment operator were basing snow clearance operations on the assumption that Flight 314 would provide a position report in time for the equipment to leave the runway. This combination of errors led to a landing with snow removal equipment still on the runway and an improvised go-around procedure that resulted in a loss of control of the airplane. If the flight had attempted to confirm that the runway was clear prior to their landing, the accident could have been avoided.