McDonnell Douglas MD-11
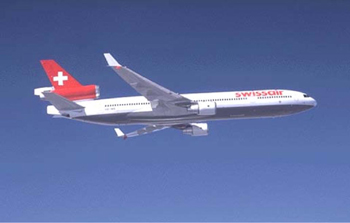
Swissair Flight 111, HB-IWF
Peggy's Cove, Nova Scotia
September 2, 1998
Swissair Flight SR 111, a Boeing (formerly McDonnell Douglas) MD-11, departed John F. Kennedy Airport (JFK) in Jamaica, New York, en route to Geneva, Switzerland.
While passing through Canadian airspace, an in-flight fire ensued in the area above the flight deck ceiling, causing loss or malfunction of numerous airplane systems and instruments. As the fire progressed, electronic navigation equipment and communications radios stopped operating, leaving the pilots with no accurate means of establishing their geographic position, navigating, or communicating with air traffic control.
The airplane crashed into the Atlantic Ocean near Peggy's Cove, Nova Scotia, while attempting an emergency descent and approach into Halifax, approximately 1 hour and 13 minutes after departure from New York. All 215 passengers and 14 crew members were lost. The accident was investigated by the Transportation Safety Board of Canada (TSB). The TSB concluded that an arcing event from an electrical wire associated with an in-flight entertainment system that had been installed via an FAA approved supplemental type certificate was likely associated with the fire initiation event. However, the TSB report stated that it could not be determined whether the arced wire was the lead event. The TSB found that once the fire had started, the thermal/acoustic insulation material installed in the airplane had a propensity to continue burning.
On September 2, 1998, Swiss Air Flight 111, a Boeing/McDonnell Douglas MD-11, departed John F. Kennedy (JFK) International Airport, New York at 2018 eastern daylight savings time (0018 Universal Coordinated Time [UTC]), on a flight to Geneva, Switzerland. The flight included 215 passengers, and a crew of two pilots and twelve flight attendants. Approximately one hour into the flight, the pilots detected an unusual smell. Fourteen minutes later the pilots declared an emergency. Six minutes after the declared emergency, Flight 111 impacted the ocean about five nautical miles southwest of Peggy's Cove, Nova Scotia, Canada. The aircraft was destroyed and there were no survivors.
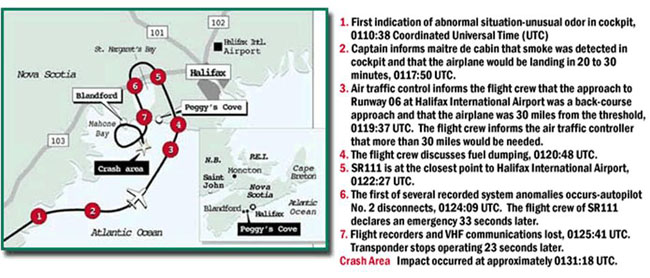
History of Flight
The first indication to the flight crew of an anomalous situation was their detection of a strange odor in the flight deck at 0110:30 UTC. The flight crew noticed some smoke in the flight deck, but it appeared to dissipate. When a flight attendant was queried, it was determined that there was no evidence of smoke or odors in the cabin. The flight crew decided that the odor and smoke were associated with the air conditioning system.
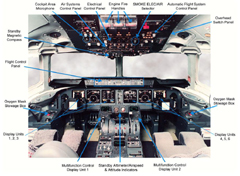
View Larger
At 0114:15, while 66 nautical miles southwest of Halifax, the flight made a PAN PAN PAN radio transmission, and indicated to air traffic control that there was an in-flight problem in progress. The flight requested a diversion to "a convenient place," initially requesting a return to Boston, which was 300 nautical miles behind them. The controller suggested Halifax, which by then was only 56 nautical miles away. At this time, the flight crew donned oxygen masks.
At 0116:34, the controller cleared the flight to descend to 10,000 feet. Following a handoff to another air traffic controller, the flight was further cleared to 3,000 feet. The flight requested an intermediate altitude of 8,000 feet until the cabin was ready for landing.
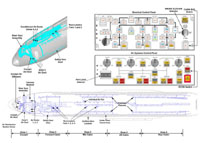
Source: TSB accident report
View Larger
Beginning at 0119:38, a series of communications with air traffic control attempted to position the airplane for an extended approach into Halifax. At this point, the flight informed air traffic control that fuel dumping would be required prior to landing at Halifax, so a series of maneuvers was begun to position the airplane for fuel jettisoning and then an approach to Halifax.
At 0123:53, the flight was positioned 35-40 nautical miles from Halifax "in case they needed to get to the airport in a hurry." The flight crew acknowledged and asked for clearance to begin dumping fuel, and further requested a block altitude of 9,000 to 11,000 feet. The controller cleared the flight for any altitude between 5,000 and 12,000 feet.
At 0124:42, the flight declared an emergency and indicated that an immediate landing was necessary. The flight also informed the controller that fuel dumping had commenced.
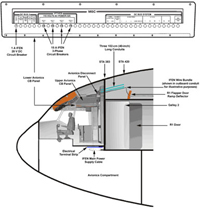
Source: TSB accident report
View Larger
At 0125:02, the flight again declared an emergency. The controller acknowledged this transmission, which was the final communication from Flight 111. At approximately 0130, observers on the ground saw a large aircraft fly overhead and heard the sound of its engines. At 0131, several observers heard a sound described as a loud clap. Seismographic recorders in the region also recorded a seismic event at 0131:18, which coincided with the time the aircraft struck the water.
System Failures
During the descent, beginning at 0124:09 and continuing for the next 92 seconds until the flight data recorder stopped functioning, multiple system failures were recorded. The first event was the disconnection of the autopilot. At 0124:18, both pilots confirmed that the autopilot had disconnected, and its associated aural warning tone continued until the cockpit voice recorder ceased recording. The Canadian TSB speculated in the accident report that the flight crew may have attempted to engage the other autopilot at this point, but there was no evidence that it engaged, and the aural warning did not cease, indicating that the circuitry for warning cancellation may have already been compromised by the fire.
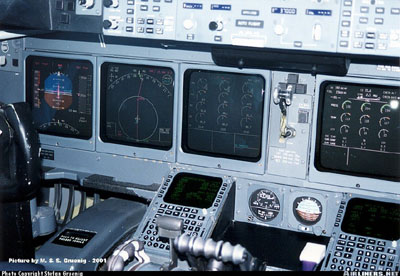
Photo copyright Stefan Gruenig - used by permission
At 0124:46, the cabin crew informed the flight crew that electrical power in the cabin had been lost, and the cabin crew was using flashlights to continue landing preparation. The accident report indicated that this may have been the result of the flight crew depowering the cabin electrical bus, per procedure. At 0124:54, the failure of lower yaw damper A was annunciated, followed by the annunciated failure of flight control computer 1 at 0124:57.
At 0125:06, the left emergency AC bus failed, followed immediately by the loss of airspeed, altitude, and total air temperature indications. At the same time, the transponder mode C, which transmits altitude information, stopped transmitting, but transponder mode A (which transmits aircraft identification) continued transmitting. Also at this time, the pilot's instrument displays went blank.
At 0125:33, the first officer reported that his instrument displays were all blank, followed by the failure of upper yaw damper A. Following these failures, the flight data recorder failed, so no further information was recorded. At 0125:41, the cockpit voice recorder also failed.
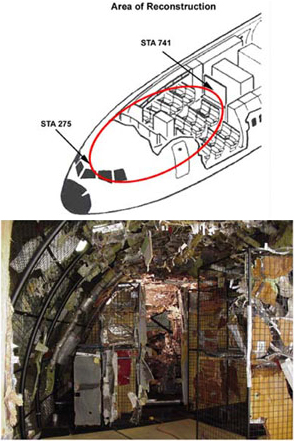
Source: TSB accident report
At 0126:04, both the mode A and mode C transponder signals failed. At some point following the failure of the data recorders, engine No. 2 experienced a loss of thrust resolver angle, which would cause thrust to remain fixed at the value present when the failure occurred. The investigation further concluded that fire-related wire failures in the flight deck ceiling could also have resulted in a No. 2 engine fire warning, causing the flight crew to shut down that engine. Wreckage examination results were consistent with that engine not operating at impact.
Fire Origin
Damage patterns observed in the reconstructed forward section of the fuselage revealed that the fire occurred in the areas above the cockpit ceiling liner and above the forward cabin drop-ceiling as shown:
Recovered electrical components that had been installed within the fire-damaged area were examined for internal failures. Such failures can be a source of heat, and therefore have the potential to be a source of ignition. Examination of these components did not show any evidence of their being involved in the initiation of the fire.
The reconstruction also revealed significant heat damage on portions of the airframe structure and air conditioning system ducts in these areas, extending from approximately STA 338 to STA 675.
Most of the heat damage in the cockpit was concentrated above the level of the bottom of the upper avionics circuit breaker (CB) panel approximately 72 inches above the cockpit floor, and in the area of the forward cabin drop-ceiling.
In the search for an ignition source, electrical wiring recovered from the wreckage was examined by the investigators for evidence of melted copper. The nature and extent of heat damage to items in the cockpit interior indicated that the fire did not reach temperatures high enough to melt copper. However, electrical arcing can result in localized temperatures that can exceed the melting point of copper. For this reason, the investigation suspected electrical arcing may have occurred wherever wire conductor damage included melted copper.
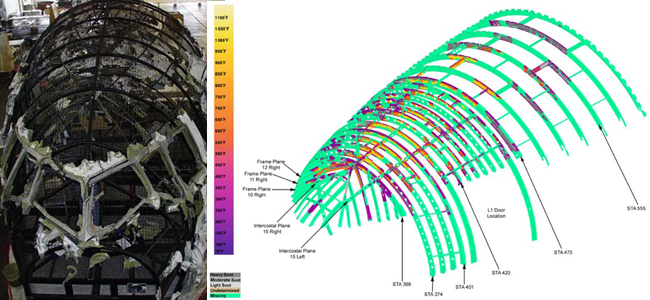
Source: TSB accident report
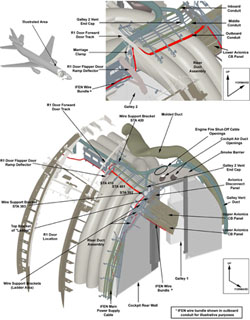
Source: TSB accident report
View Larger
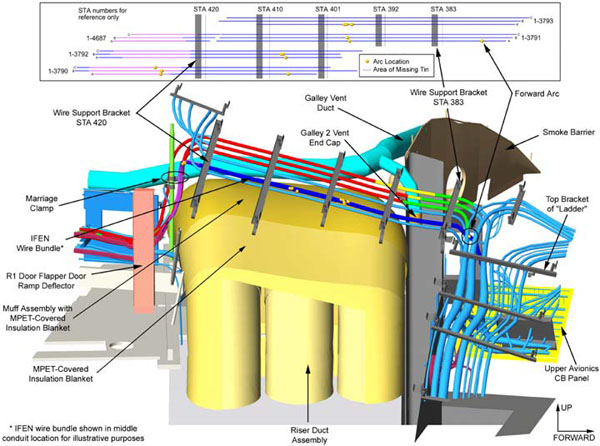
Source: TSB accident report
View Larger
Among the thousands of wire segments that were recovered and analyzed, areas of arc damage were found on 20 wire segments. Eight of these segments were identified as being part of wires that were associated with the in-flight entertainment network (IFEN) that was installed in the accident airplane as a post-delivery modification. One of the IFEN wire segments that exhibited arc damage was located near STA 383 in the area where the TSB believed the fire most likely originated.
Although the exact wire or wires that were involved in the lead arcing event could not be positively identified, the TSB did conclude that the most likely ignition source was electrical arcing in the area above the cockpit ceiling. During the investigation, the TSB employed software tools to simulate the fire, and how it may have propagated, based on air conditioning and cabin/flight deck airflow results obtained during flight tests. An example of the fire propagation from those TSB simulations is available below:
Cabin Material Flammability Standards
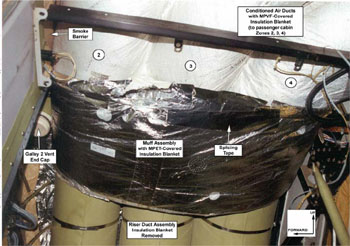
Source: TSB accident report
Metalized polyethylene terephthalate (MPET) covered insulation blankets were identified as the most likely source of fuel. The TSB determined that the insulation blankets would be the first materials to be ignited by an electrical arc in the cockpit attic area. The MPET covered insulation blankets complied with the flammability requirements (14 CFR Part 25.853(b), Amendment 25-61) at the time the MD-11 airplane was certified, in that the test MPET did not readily ignite, or sustain combustion when exposed to a heat/flame source, as specified in the regulation.
The ability of MPET covered insulation blanket to ignite and sustain a fire was investigated by the TSB as part of the investigation into the crash of Swissair 111. Examination of typical MPET installations resulted in TSB material flammability tests in different configurations than those required by the applicable regulations. One such test involved rolling the MPET into a cylinder, and igniting the cylinder with a match. A video of this TSB test is available below. (MPET Cylinder Burn Test). This cylindrical configuration was, according to the TSB, more representative of MPET installations, in that MPET was, in many instances, installed such that multiple MPET covered surfaces were in close proximity to one another. As a result, heat from a fire on one surface could radiate and/or reflect, and thereby inhibit the flame resistance properties of the material.
Burn testing of MPET insulation blankets on a larger scale was conducted at the Federal Aviation Administration (FAA) Technical Center in Atlantic City, New Jersey using a rough mockup of the attic area of a fuselage.
In-flight Entertainment System Certification
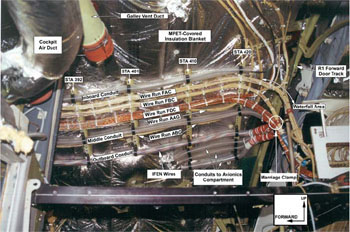
Source: TSB accident report
The in-flight entertainment system (IFEN) had been installed in Swissair's MD-11 fleet via an FAA-approved supplemental type certificate (STC). An STC is a modification to an airplane that alters, or "supplements," the original type design. An STC is usually obtained by an organization other than the original airplane manufacturer, and in this case was obtained by a company contracted by Swissair for that purpose. The STC applicant was an FAA Designated Alteration Station (DAS), which, under its delegation certificate, has sufficient organizational infrastructure and expertise to issue the STC.
The IFEN system was certified as a "non-essential" and "non-required" system, meaning, in part, whether failed or operating properly, it would have minimal or no impact on airplane safety. As a result of this categorization, the only tests completed during the certification of the system were electromagnetic interference, and system failure tests.
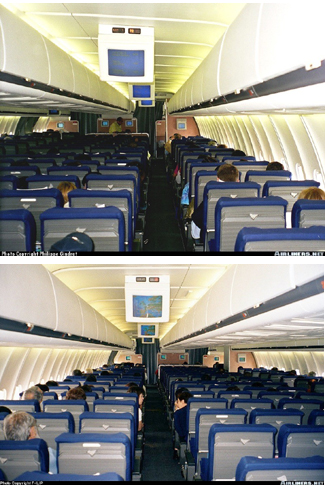
Photo copyright Phillipe Gindrat - used with permission
Per 14 CFR 25.1309, a system safety analysis was required that assessed the safety impacts of system operation both in normal and failure modes. An outcome of the prescribed testing demonstrated that the impacts of system failures were minor and in accordance with the categorization as a non-essential system. As a further outcome, since the system was considered non-essential, a quantitative system integration analysis was not conducted. Such an analysis, if conducted, would have addressed safety functions such as emergency electrical load shedding. Many non-critical electrical loads are isolated on a single electrical bus such that they can be either automatically shed in an emergency, or be easily deactivated by the flight crew. In the case of this IFEN, there was no means provided for the flight crew to deactivate electrical power to the system, nor were there procedural instructions for system deactivation. The TSB stated that had the referenced analysis been conducted, it would have established whether the IFEN system integration retained the original integrity of the MD-11 type certificate with respect to emergency deactivation of non-essential electrical loads.
The TSB, while not able to conclusively identify the source of the fire, concluded that the most likely source was wiring related to the IFEN. They further cited deficiencies in the certification of the IFEN system, particularly related to interpretations of 25.1309 regarding non-essential systems.
Accident Memorial
Memorial to the victims of Swissair Flight 111 located near Peggy's Cove, Nova Scotia.
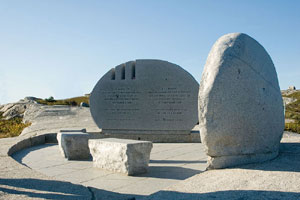
Report Number A98H0003 describing the investigation into the crash of Swissair Flight 111 was released by the Transportation Safety Board (TSB) of Canada on April 3, 2003.
The TSB issued 55 findings separated into three categories:
- Findings as to cause and contributing factors (11 findings),
- Findings as to risk (24 findings), and
- Other findings (20 findings).
The complete text of the TSB findings is available at the following link: Accident Board Findings
The complete accident report is available at the following link: TSB Accident Report
A total of twenty-seven safety recommendations were issued by the Canadian TSB and the United States National Transportation Safety Board (NTSB) addressing a variety of issues relevant to this accident. Of these, twelve were TSB aviation safety recommendations, eleven were TSB interim safety recommendations, and four were NTSB safety recommendations. These safety recommendations are summarized below.
- Flammability requirements: Five TSB safety recommendations address flammability of interior materials and electrical wiring.
- Fire hardening of airplane systems: One TSB safety recommendation addresses fire hardening of airplane systems. The TSB recommends that as a prerequisite to certification, all aircraft systems in the pressurized portion of an aircraft, including their sub-systems, components, and connections, be evaluated to ensure that those systems whose failure could exacerbate a fire in progress are designed to mitigate the risk of fire-induced failures.
- Review of the STC process: One TSB safety recommendation addresses the STC process and recommends that modifications of in-service airplanes undergo review to ensure compatibility with the safety features that are part of the type certificated design.
- Standards for resetting of circuit breakers: One TSB safety recommendation addresses the need for establishing requirements and industry standards and conditions for in-flight resetting of circuit breakers to prevent multiple attempts at closing circuit breakers into electrical faults.
- Increase capability and reliability of cockpit voice (CVR), flight data (FDR), video image recorders: Four TSB safety recommendations address numerous issues related to the CVR, FDR, video image, and "quick access" recorders. Recommendations are made for longer recorder duration, recording of increased number of parameters (including recording of non-mandatory parameters such as "quick access" recorder data) by flight data recorders, improved CVR intelligibility, redundant power sources for recorders, and provisions for recording of video images.
The following Interim Safety Recommendations were issued by the TSB to address, on an expedited basis, several issues that were determined by the TSB to be of an urgent matter:
- Review of current firefighting procedures and provisions: Two TSB Interim Safety Recommendations call for the review of in-flight firefighting as a whole, to ensure that flight crews are provided with the tools needed to maximize the likelihood of successfully detecting and suppressing in-flight fires.
- Smoke/fire detection and suppression systems in pressurized areas: One TSB Interim Safety Recommendation recommends that regulatory authorities and the aviation industry review the methodology for establishing designated fire zones in pressurized sections of aircraft with the goal being the incorporation of improved smoke/fire detection and suppression in these areas.
- Flight crew procedures during in-flight fires: Two TSB Interim Safety Recommendations were issued to address flight crew procedures and responses during in-flight fires. In particular, the TSB identified a need for flight crews to recognize that the most appropriate course of action after recognition of smoke/fire from an unknown source is to land the airplane expeditiously.
The recommendations are contained in a section of the TSB report entitled "Safety Action". This section of the report is excerpted and available at the following link: TSB Recommendations
The NTSB issued four safety recommendations, one associated with the electrical wiring in certain areas of the MD-11 cockpit, and three associated with duration and power supply reliability of CVRs and FDRs.
Inspection of MD-11 electrical wiring. The NTSB recommended that the FAA require, on an expedited basis, the inspection of all MD-11 airplanes for discrepancies of wiring in and around the cockpit overhead circuit breaker panel and the avionics circuit breaker panel.
Enhanced CVR and FDR capability, duration, and power supply reliability. The NTSB issued three safety recommendations that propose the mandatory installation of CVRs with increased recording duration and powered by independent power sources.
These recommendations also call for the installation of two combination CVR/DFDR units and the revision of 14 CFR Part 25.1457 and Part 25.1459 to require that CVR's, FDR's, and redundant combination flight recorders be powered from separate generator buses with the highest reliability.
14 CFR Part 25.853, Amendment 25-61, Compartment Interiors
This regulation defined the flammability standards for cabin materials.
25.853 referred to standards in Appendix F to 14 CFR 25, and further specified that cabin materials tested in the prescribed manner could not burn for more than 15 seconds or have a burn length of more than eight inches before self-extinguishing.
14 CFR 25 F25.1, Appendix F--Part I--Test Criteria and Procedures for Showing Compliance with Sec. 25.853 or Sec. 25.855.
This Appendix, in Part 1, detailed the tests, apparatus required, and pass/fail criteria for cabin materials identified in this appendix.
14 CFR Part 25.1309, Amendment 25-41, Equipment, Systems and Installations
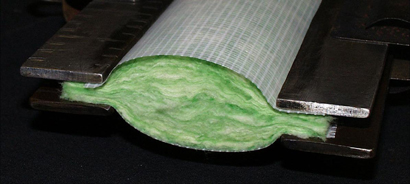
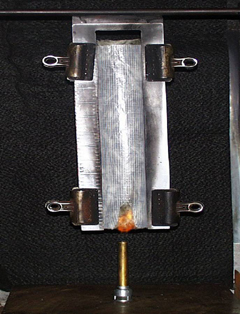
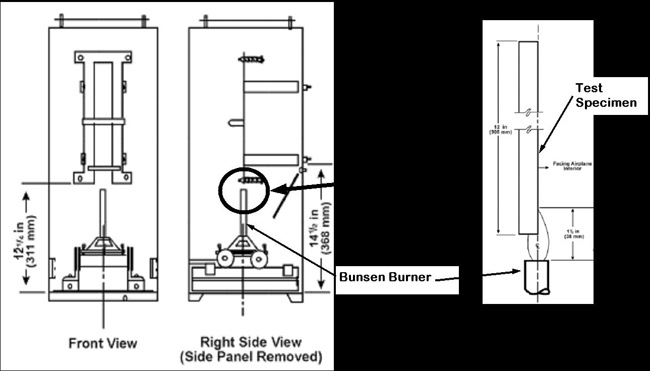
The Supplemental Type Certificate which approved the design and installation of the IFEN system on an MD-11 airplane was issued by an FAA-approved Designated Alteration Station (DAS. The IFEN system was designed by an outside organization (not the DAS), and the DAS submitted a letter of intent (LOI) to the FAA describing the intended system design and plan for certification. The original design intent had been for the IFEN system to be powered from the cabin electrical buses. Inclusion on the cabin buses would have allowed electrical isolation of all "non-essential" electrical loads. In the event of an in-flight emergency, crew procedures for smoke/fumes of unknown origin required deactivation of the cabin electrical buses. Deactivation of the cabin electrical buses is via an overhead switch in the flight deck.
An early design review had discovered that the cabin buses did not supply adequate electrical power for the full 257 seat configuration, so the system was redesigned to draw power from AC bus 2 (an essential bus). This would have been an acceptable design if: an independent switch for deactivating the IFEN system had been included; or a switching relay connected through the cabin bus switch. However, no options were provided, and deactivation of the cabin bus switch resulted in the IFEN system remaining electrically powered.
The TSB could not determine if the design changes were shared with the DAS. The TSB postulated that under normal circumstances, a design change of this significance would have resulted in a revision to the LOI. No revision to the LOI was submitted. The TSB also stated that FAA oversight of this project would likely not have uncovered the design change in a timely manner, as the FAA was reliant on the DAS to inform them of changes in the scope of the project.
The TSB believed the flight crew was unaware that the IFEN system was powered by AC bus 2, and further believed that having accomplished the emergency procedure associated with smoke/fumes of unknown origin, which deactivated the cabin electrical buses, the IFEN system had been eliminated as a source of ignition. With the IFEN system continuing to be powered electrically, it remained as a potential ignition source, and the TSB believed electrical arcing in the IFEN system wires did, in fact, ignite the MPET in the area of the flight deck attic.
- MPET thermal/acoustic insulation, in certain installations, had significantly different flammability characteristics than had been demonstrated in compliance tests.
MPET material was successfully shown to comply with existing flammability standards at the time of MD-11 certification. The standard applied to this airplane involved a vertical burn specimen test, and self-extinguishment following flame removal. However, in certain other orientations, the material was found to have a significantly different flammability behavior and continued to burn following flame removal.
- The inability of the flight crew to easily remove electrical power from the IFEN system (lack of a flight deck switch).
The IFEN system did not have a means for the flight crew to easily remove electrical power from the system. The TSB speculated that, having accomplished the appropriate emergency procedures, the flight crew may have believed that power had been removed from the IFEN system, when in fact, it had not, and IFEN wiring may have continued to arc. During the course of post-accident inspections of similarly configured MD-11 airplanes, as well as other non-MD-11 airplanes, investigators discovered that many entertainment system designs in service at that time had similar shortcomings in their power supply arrangement. Numerous ADs were issued which required electrical circuit changes in order to enable the flight crew to depower the entertainment system through normal flight deck procedures.
- MPET thermal/acoustic insulation material would not continue to burn when exposed to an ignition source.
- The IFEN system could be depowered via accomplishment of appropriate flight crew emergency procedures.
- November 1993: Fire on a McDonnell Douglas MD-87 airplane while taxiing after landing at Copenhagen, Denmark. The fire was found to have been initiated by an electrical fault behind a sidewall, but investigators later determined that the insulation materials contributed to the propagation of the fire.
- November 1995: Cabin fire on a McDonnell Douglas MD-82 airplane prior to takeoff at Turin, Italy. The cause of the fire was ruptured lighting ballast. In that case, other interior materials played a more significant role in propagating the fire, but there was evidence that the fire also propagated on the film of the insulation.
- 1994, 1995: In June of 1996, the FAA was informed by the Civil Aviation Authority of China (CAAC), of three incidents of interior fires that occurred in China in 1994 and 1995. Those incidents involved McDonnell Douglas and Boeing airplanes and were caused by electrical problems or inappropriate maintenance actions. In each of those cases, physical damage to the airplane was minimal, but there was clear evidence that the fires had propagated on the insulation.
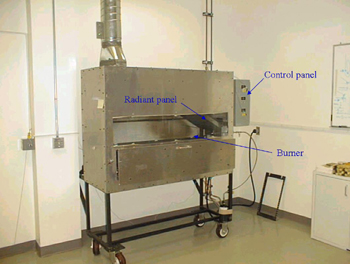
14 CFR 25.856, Thermal/Acoustic Insulation Material
25.856 was adopted as a new regulation following this accident. The rule provides specific flammability standards for thermal/acoustic insulation materials typically installed behind interior panels in transport category airplanes. These new standards include the adoption of flammability test methods and criteria that specifically address flame propagation and entry of an external fire into the airplane (burn through) under realistic fire scenarios.
14 CFR F25.1, Appendix F--Part I--Test Criteria and Procedures for Showing Compliance with Sec. 25.853 or Sec. 25.855.
Part I to Appendix F was revised to add testing requirements for insulation blankets.
14 CFR F25.6, Appendix F--Part VI--Test Method to Determine the Flammability and Flame Propagation Characteristics of Thermal/Acoustic Insulation Materials.
Based in part on information obtained during the investigation relative to the flammability characteristics of MPET insulation, this regulation adopted a new flammability test strategy for MPET, requiring that the material be subjected to a radiant panel test. It had been discovered during the investigation that the manner in which MPET had been installed throughout the airplane allowed for the material to radiate heat to surrounding MPET, overwhelming any tendency for the material to self-extinguish. This new regulation specified the required test apparatus, test procedures, and provided more stringent pass/fail criteria than those in the vertical burn test.
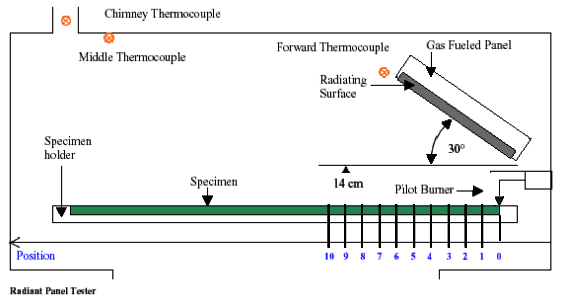
14 CFR F25.7, Appendix F--Part VII--Test Method To Determine the Burn-through Resistance of Thermal/Acoustic Insulation.
This new regulation provided requirements and test criteria, as well as the required test apparatus for determining the burn-through resistance of thermal/acoustic insulation material. The pass/fail criteria required that the test specimen not be penetrated by fire or flame for at least four minutes and required that heat flux on the cold (opposite side from where flame was applied) not exceed 2 btu/ft2 at a distance of 12 inches from the test specimen.
14 CFR 121.312, Materials for compartment interiors.
This regulation required all airplanes in 14 CFR 121 commercial service to comply with the requirements of 14 CFR 25.853. Depending on the date of certification and/or the date of airplane manufacture, compliance with specific amendment levels of 25.853 is required, commensurate with amendment levels in effect at the specific dates. Further, for airplanes that have undergone interior replacements, compliance with 25.853 is required, as well as cabin materials being required to meet the flammability standards of 14 CFR 25.856. This regulation effectively required that all airplanes in commercial (14 CFR 121) passenger service meet the requirements of 25.853 regardless of the date of manufacture, and independent of the original effective date of 25.853.
Thermal/Acoustic Material Testing
In September 1997, The FAA provided a final technical report (DOT/FAA/AR-97/58) entitled, "Evaluation of Fire Test Methods for Aircraft Thermal Acoustical Insulation". The report was a response to a number of in-service incidents involving fire propagation in insulation. Testing conducted included vertical flammability and cotton swab testing. Test data indicated that the cotton swab test produced consistent test results, whereas the vertical flammability test did not. The report concluded that, "The front face of the MPET blanket sample was totally consumed when subjected to the cotton swab test" and, "This is in sharp contrast to the vertical flammability test results which indicated the MPET samples passed most of the time."
Special Certification Review
Preliminary information that failures of IFEN system wiring might have served as the source of ignition of the fire on Flight 111 was received by the FAA within the first few months following the accident.
This information prompted a Special Certification Review (SCR) of the installation which was originally approved via Supplemental Type Certificate (STC) Number ST00236LA-D. The purpose of the SCR was to determine if any unsafe design or installation features existed, and to review the practices of the FAA Designated Alteration Station (DAS) that installed and certified the system.
The SCR identified six shortcomings in the design and certification of the IFEN which are described in the SCR final report, dated June 14, 1999, and revised on June 9, 2000. The findings are:
SCR Finding 1: The control of electrical power to the IFEN system was not compatible with the design concept of the MD-11 airplane with regard to the response by the flight crew to a cockpit or cabin smoke/fumes emergency. As a result, placing the cockpit CABIN BUS switch to the off position, which is part of the MD-11 flight crew procedure for smoke/fumes of undetermined origin, would not result in the removal of electrical power from the IFEN system. This finding emphasizes the need for ensuring that all modifications of in-service airplanes be closely reviewed to ensure compatibility with the safety features and procedures that are embodied in the original type design of the airplane.
SCR Finding 2: In many cases, the STC holder did not follow proper certification procedures. Deficiencies included failure to properly document test flights with a Type Inspection Authorization and performing flight testing of changes to STC-approved installations after issuing the amended STC.
SCR Finding 3: FAA oversight of the DAS during the IFEN STC certification program was in accordance with established procedures; however, the procedures were deficient in several areas.
SCR Finding 4: The FAA failed to ensure that problems identified during scheduled DAS audits were corrected.
SCR Finding 5: The SCR revealed inadequate technical information in engineering drawings with regard to wire crimping, wire bundle bend radii, terminal torque requirements, wire bundle routing and wire separation.
SCR Finding 6: FAA conformity inspections of the IFEN installation on three Swissair MD-11 airplanes revealed non-conformities between the installation drawings and the actual installations. In some areas, the installation drawings themselves were determined to be inadequate.
Interim IFEN Policy
As a result of the FAA Special Certification Review, the FAA issued Interim Policy Guidance for Certification of In-Flight Entertainment Systems No. 00-111-160. This policy provided additional guidance to be used during the certification of in-flight entertainment (IFE) systems on transport category airplanes. This policy was the result of the FAA Special Certification Review (SCR) and of reviewed IFEN systems certified by supplemental type certificate (STC) conducted after the SCR. These reviews indicated a wide variation in the type of design approvals granted, level of FAA involvement in the approvals, understanding of applicable airworthiness regulations, and the quality and comprehensiveness of data that is used in showing compliance with applicable 14 CFR part 25 regulations.
The FAA policy statement can be viewed at the following link: FAA Interim IFEN Policy
Enhanced Airworthiness Program for Airplane Systems/Fuel Tank Safety (EAPAS/FTS)
As a result of this accident, and TWA 800, which occurred in 1996, a number of regulatory changes were developed relative to aging systems, particularly in the area of airplane wiring systems certification, maintenance, and operational requirements. Significant revisions to 14 CFR parts 1, 21, 25, 91, 125, and 129 were issued, and 14 CFR part 26 was issued as a new rule, which requires the development of wire systems maintenance programs for the existing fleet of large transport category airplanes.
The following FAA Airworthiness Directives (AD) were issued as a direct result of the crash of Swissair Flight 111:
AD 2000-11-02, Removal/Replacement of Metalized Polyethylene Terephthalate (MPET) Insulation Blankets from Boeing DC-10 and MD-11 Series Airplanes.
This AD mandated the removal of MPET thermal acoustic insulation blankets from all Boeing DC-10 and MD-11 airplanes.
AD 99-20-08, Prohibit the installation of in-flight entertainment (IFEN) systems previously approved under STC ST00236LA-D.
This STC provided design approval of the IFEN system that was installed in the accident airplane and in several other MD-11 airplanes of Swissair's fleet. The possibility of electrical arcing of the wiring associated with this system was one of the suspected sources of ignition of the insulation blankets. This AD revokes the installation approval of the STC.
AD 2008-23-09, As a direct result of the Swissair accident, the FAA examined other transport airplanes in the fleet to determine if other flammability hazards existed, similar to MPET. As a result, AD 2008-23-09 was issued, applicable to certain Boeing airplane models. This AD requires replacing any insulation blanket constructed of polyethyleneteraphthalate (PET) film, or ORCON Orcofilm AN-26, with a new insulation blanket that meets the requirements of 14 CFR 25.856(a).
In addition to the ADs mentioned above, the FAA also issued 20 additional ADs intended to address similar potential unsafe conditions in other airplane models. The groupings of these ADs are as follows:
Removal and replacement of MPET covered thermal acoustic insulation blankets. The FAA issued one AD that mandated removal of MPET covered thermal acoustic insulation blankets, and replacement of those blankets with blankets made of less flammable materials. These ADs were applicable to Boeing Model DC-9, MD-88, and MD-90 airplanes. Other Boeing models were not affected since they did not employ MPET covered insulation blankets.
Removal or deactivation of other IFEN or in-flight passenger telephone system. Four ADs were issued that mandated the removal or deactivation of IFEN and in-flight passenger telephone systems that did not provide flight and/or cabin crew members with a readily available means for the rapid removal of electrical power from the system components and wiring in the event of smoke and/or fire of unknown origin.
Modification of other IFEN systems. The IFEN systems associated with 22 STCs did not provide the flight and/or cabin crew with a readily available means for the rapid removal of electrical power from the system components and wiring in the event of smoke and/or fire of unknown origin. These systems were installed and in use on airplanes in active service. To allow continued use of these systems, the FAA mandated corrective modifications in lieu of removal of the IFE systems. Fifteen ADs were issued to mandate the installation of power shutoff circuitry and the incorporation of necessary procedures into the flight and cabin crew procedures manuals.
Airplane Life Cycle:
- Design / Manufacturing
Accident Threat Categories:
- Uncontrolled Fire / Smoke
- Cabin Safety / Hazardous Cargo
- Lack of System Isolation / Segregation
Groupings:
-
N/A
Accident Common Themes:
- Organizational Lapses
- Flawed Assumptions
Organizational Lapses
The IFEN system was considered, and certified, as a non-essential, non-required system and was installed via a supplemental type certificate issued by an FAA Designated Alteration Station. In part, as a result of the non-essential classification, FAA oversight of the certifying organization was minimal, and the Canadian TSB cited the lack of FAA oversight, and interpretation and application of 14 CFR 25.1309, as factors in the accident. During the initial stages of the certification program, the IFEN design was modified to change the system electrical source to one of the airplane essential buses, rather than the cabin electrical bus, as originally designed. The TSB surmised that the design change was not made apparent to the DAS responsible for the certification, who further did not inform the FAA.
Flawed Assumptions
Based on assessments of the IFEN system at the time of its installation approval, the system was considered non-essential, and by the nature of this classification led to the assumption that the system would not have a significant impact on airplane operation or on other systems. The Canadian TSB concluded that the most likely source of the fire that resulted in the crash was initiated by arcing in wires associated with the IFEN system. The arcing event led to ignition of MPET-coated insulation in the flight deck ceiling area, which rapidly propagated, ultimately resulting in failure of multiple airplane systems and leading to the crash of the airplane.
MPET-coated insulation material was used extensively in the MD-11. MPET had undergone flammability testing per 14 CFR part 25 and complied with those requirements. Based on the successful outcome of flammability testing, it was assumed that MPET was a safe material for use in the MD-11 and other transport airplanes. During the accident investigation it was discovered that circumstances existed that could result in MPET material being highly flammable. This discovery led to mandatory action requiring the removal of MPET from transport airplanes on which it was installed.
On August 19, 1980, a cargo fire on a Saudi Arabian Airlines L-1011 in Riyadh, Saudi Arabia penetrated into the cabin while the airplane was in flight. The fire propagated rapidly in the cabin, and though the airplane was successfully landed following an emergency return to Riyadh, an evacuation was never initiated, and all 301 passengers and flight crew perished in the fire.
See accident module
On June 2, 1983, while enroute at 33,000 feet, an Air Canada DC-9 experienced an inflight fire that originated in an aft lavatory. An emergency landing was made at Cincinnati International Airport. During the evacuation of the airplane a flashover occurred, resulting in the cabin being consumed by the fire. Of the 41 passengers onboard, 23 died in the fire.
See accident module
Technical Related Lessons:
Flammability standards for cabin materials should be representative of realistic installation features within which the materials will be expected to perform. Also, these standards should be continuously evaluated as lessons are learned from subsequent testing and/or service experience. (Threat Category: Uncontrolled Fire)
- Though it had successfully undergone flammability testing involving a vertical burn test standard during airplane certification, the metalized polyethylene terephthalate (MPET) coated insulation material, installed throughout the airplane, proved to be highly flammable when exposed to a flame source in a tightly enclosed environment. The Transportation Safety Board of Canada (TSB) determined that the flammability characteristics of the MPET coated insulation material, when arranged as installed in many areas of the MD-11, caused the fire to propagate rapidly in areas of the cabin ceiling where it was very difficult to combat. Subsequent investigations into the flammability characteristics of the material resulted in its mandated removal from fuselage interiors, and changes to FAA regulations regarding flammability testing.
Common Theme Related Lessons:
Modification of in-service airplanes must be accomplished in a manner that preserves the original safety features of the airplane. (Common Theme: Organizational Lapses)
- The inflight entertainment system (IFEN) installation did not include a means for the flight crew to remove power from the system in the event of electrical arcing or a fire. As the system was considered non-essential, it was not, at the time, considered necessary to provide a means on the flight deck to remove system electrical power. Subsequent to this accident, a series of evaluations of existing designs was conducted, and other IFEN installations were found to have similar deficiencies. As a result, numerous airworthiness directives were issued to require a means in the flight deck to deactivate the system by operation of a single switch. Following the accident, it was also learned that the IFEN system design organization had redesigned the system following submittal of design data to the FAA. The TSB surmised that the design change was not made apparent to the DAS and was therefore not passed on to the FAA. It was determined that the change to the electrical power source for the IFEN subsequently resulted in the inability to isolate the IFEN system from electrical power and contributed to the propagation of the fire.
The process for achieving safety and compliance must be sufficiently robust to preclude hazards, regardless of the criticality of the system being assessed. (Common Theme: Flawed Assumptions)
- The IFEN system was considered to be a non-essential system, and associated certification criteria were therefore limited to examination of system failures, and verification that an IFEN failure did not have an adverse effect on other airplane systems. System analyses did not consider failures such as wire arcing, that could potentially cause fires in confined areas, or failures other than those that resulted in a failure of the system to operate. The assumption that all IFEN system failures would be benign, and not result in adverse effects on the airplane, ultimately proved incorrect.