Embraer EMB-120
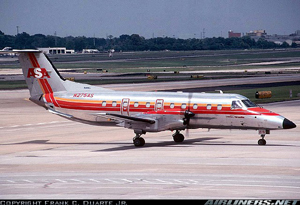
Photo copyright Frank C. Duarte Jr. - used with permission
Atlantic Southeast Airlines Flight 2311, N270AS
Brunswick, Georgia
April 5, 1991
On April 5, 1991, Atlantic Southeast Airlines, Inc., Flight 2311, an Embraer EMB-120, N270AS, crashed during a landing approach to runway 07 at the Glynco Jetport, Brunswick, Georgia. The flight was a scheduled commuter flight from Atlanta to Brunswick, Georgia, and was being conducted under instrument flight rules. The airplane was operating in visual meteorological conditions at the time of the accident. Due to the crash, the aircraft was destroyed. The two pilots, the flight attendant and all 20 passengers were killed.
Flight 2311 was cleared for a visual approach to Glynco Jetport a few minutes before the accident. Witnesses reported that as the airplane approached the airport, it suddenly turned or rolled to the left until the wings were perpendicular to the ground. The airplane then fell in a nose-down attitude and disappeared out of sight behind the trees.
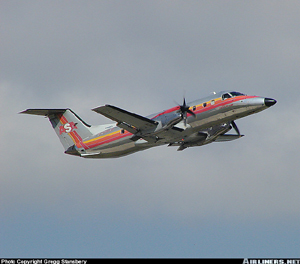
Photo copyright Gregg Stansbery - used with permission
History of Flight
On April 5, 1991, an Atlantic Southeast Airlines (ASA) Embraer EMB-120 operating as Flight 2311 departed Atlanta, Georgia in route to Brunswick, Georgia with 20 passengers and three crew members (captain, first officer and a flight attendant). The original aircraft for Flight 2311 had mechanical problems and a change was made to use N270AS. This aircraft had three previous flights that day with no reported problems. The flight departed at 1347, 20 minutes after the scheduled departure time. The aircraft was not equipped with a flight data recorder (FDR) or a cockpit voice recorder (CVR) as there were no requirements for either device at the time.
The flight deviated around weather in route and arrived in the Brunswick area approximately 1444. At 1448:10, the flight crew notified Jacksonville air route traffic control center they had the airport in sight. At 1448:13, Flight 2311 was cleared for a visual approach to Glynco Jetport in Brunswick, Georgia. At 1448:21 the crew acknowledged clearance for the visual approach. The crew then made an "in-range call" on the company frequency, and there was no indication of mechanical problems during that call.
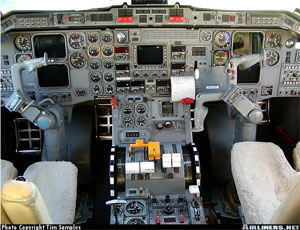
Photo copyright Tim Samples - used with permission
View Larger
There were several witnesses that observed the airplane approaching the airport who were subsequently interviewed by the investigators. The witnesses stated that the aircraft appeared to be in normal flight, on a downwind approach to runway 7. The aircraft continued a turn from the base leg in about a 20-degree bank and a gradual descent. As the airplane was completing the 180-degree turn from the downwind leg, the airplane appeared to pitch up about five degrees then roll left. The airplane continued to roll left until the wings were vertical, and then it pitched down until impact. Several witnesses reported hearing a loud squeal or whine from the engine just prior to the crash. Investigators concluded that this sound would be consistent with the sound of a propeller over-speed. The accident site was about ten thousand feet from the threshold of the runway.
The aircraft came to rest in an upright position in a densely forested, flat terrain area. Damage to the trees in the area showed indications that the airplane was banked approximately 90 degrees to the left and in a steep angle of descent. The aircraft was destroyed by the impact and the post-crash fire.
Propeller Operation
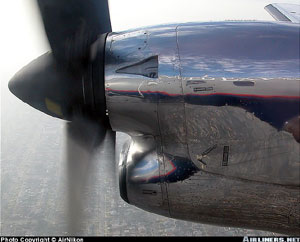
Photo copyright AirNikon Collection,
PIMA Air & Space Museum - used with permission
The Pratt and Whitney Canada PW-118 is a turbo-propeller engine consisting of two modules, the turbo-machinery module and the reduction gearbox module, joined to form a single unit. The turbomachinery includes two independent, coaxially mounted, centrifugal compressors, each driven by a single stage turbine, and a two-stage power turbine that drives the reduction gearbox by means of a coaxial shaft that passes through the compressor shaft. The reduction gearbox drives a flanged propeller shaft and also provides accessory drives.
The Hamilton Standard 14RF-9 propeller is a flange-mounted, controllable-pitch, dual-acting, full-feathering, reversible, four-blade propeller with composite blades. The propeller control unit (PCU) is mounted on the back of the gearbox. The propeller and PCU have a common centerline and are connected through the propeller shaft by the oil transfer tube. The transfer tube provides high pressure oil from the gearbox-mounted main oil pump through the PCU to the propeller pitch change actuation system in the propeller hub. The PCU governor provides metered oil pressure to operate a ball-screw drive which imparts rotary motion to the transfer tube by means of a splined quill. The transfer tube turns an acme screw in the pitch change assembly. The acme screw positions the pitch change selector valve, which directs oil to the "increase pitch" or "decrease pitch" side of the piston.
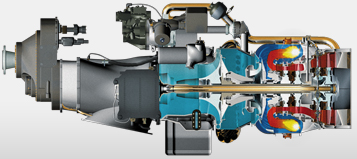
Mounted to the front of the propeller hub is a pressure cylinder that contains the hydraulic piston which drives an actuator yoke to change the pitch. The yoke is attached to offset pins on the blades so that yoke translation rotates the blades to change propeller pitch. The transfer tube provides the pressurized oil to change pitch and provides the control inputs to port oil to the increase or decrease pitch side of the piston.
To change pitch the PCU commands the transfer tube to rotate slightly slower than the propeller in order to increase pitch, and slightly faster in order to decrease pitch. The mechanism which converts the transfer tube rotational speed changes, in order to open and close oil ports, is contained in the hub and pressure cylinder. Also contained in the hub is a pitch lock mechanism that locks the blade pitch at the current operating setting if oil pressure is lost.
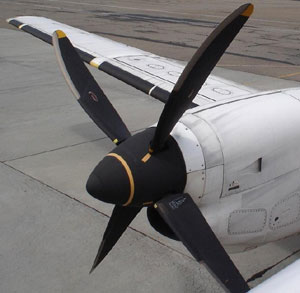
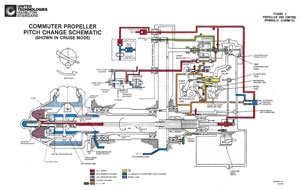
Image Provided by United Technologies
View Larger
Blade increase or decrease pitch is controlled by changing the rotational speed of the transfer tube with respect to the propeller rotational speed. The PCU monitors the propeller rotational speed with a governor, and commands the transfer tube rotational speed to increase or decrease blade pitch so that the propeller rotational speed remains at the speed set by the pilot. Nominally, the transfer tube rotates at the same speed as the propeller.
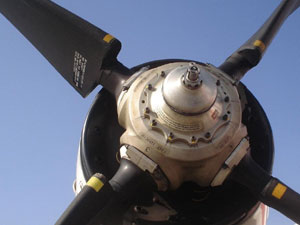
The PCU makes pitch change commands by increasing or decreasing oil pressure to drive a servo-piston back and forth. The servo-piston is attached to a ball screw that converts servo-piston back-and-forth motion into increase or decrease pitch transfer tube rotation. The outer sleeve of the ball screw rotates at the same speed as the propeller. The inner ballscrew sleeve nominally rotates at the same speed as the propeller until the servo-piston drives the outer sleeve forward or back.
The ball screw outer sleeve is connected to the servo-piston with a set of bearings. The ball screw inner sleeve is connected to the transfer tube with splines and a quill shaft. The bearings are needed on the servo-piston because the servo-piston does not rotate with the propeller. It only moves back and forth with the oil pressure changes commanded by the PCU. The ball screw inner sleeve has splines because it slides back and forth over the transfer tube and rotates with the transfer tube. When the oil pressure is stable, there is no relative motion as all rotational speeds are the same and the pitch does not change.
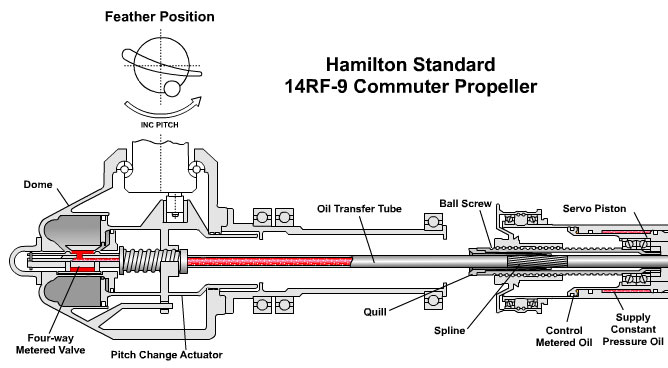
The spline teeth on the transfer tube are about four inches long, and the mating spline on the quill is about 1/8 inch long. The spline on the transfer tube needs to be long to accommodate the back-and-forth motion on the quill, which is attached to the ball screw.
In summary, if the PCU governor senses a need to increase propeller speed, the PCU decreases the metered pressure on the servo-piston, causing it to translate forward, driving the ball screw, decreasing the speed on the transfer tube. This decrease in transfer tube speed results in an oil pressure change in the hub, thereby increasing propeller speed.
Propeller Control System Failure
The investigation determined that the accident resulted from an uncommanded propeller pitch change on the left engine. The propeller entered a low-pitch mode resulting in extremely high drag and leading to a loss of control of the airplane. Investigators determined that the propeller control system failure was the result of a disengagement between the transfer tube spline and the quill spline. The disengagement resulted from the harder, rougher surface of the titanium nitride transfer tube causing abnormal wear on the softer quill spline. The titanium nitride transfer tube was a design change that replaced the original nitride transfer tube. It was learned during the investigation that if the transfer tube and quill become disengaged, the propeller can change pitch (in either increase pitch or decrease pitch) independent of PCU control.
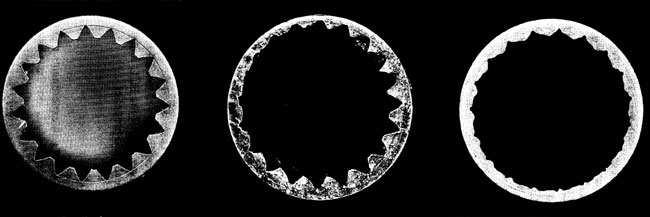
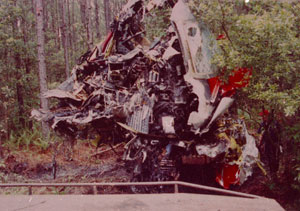
NTSB Photo
In the absence of flight data and cockpit voice recorders, the investigation assumed a specific accident sequence. During approach, the pilot set the condition levers to 100% propeller rotational speed and pulled the power levers back to the flight idle stop, which would be a normal occurrence on every approach. Propeller blade angles would decrease to maintain 100% speed at this low power setting. Also, during the approach, due to the excessive wear on the quill, the quill and transfer tube became disengaged, allowing propeller pitch to further decrease, and causing the propeller rotational speed to increase above 100%. The PCU responded by commanding increase pitch. The servo-piston responded and drove the ball screw to decrease the speed of the transfer tube and increase propeller pitch. However, due to the failure, the transfer tube was disengaged, so the propeller could not respond to the commanded pitch change. The propeller pitch continued to decrease, and propeller rotational speed continued to increase, resulting in very high asymmetric drag. This asymmetry caused the pilot to lose control of the airplane. An animation of this sequence of events is available below:
Examinations of the left propeller components indicated a propeller blade angle of about three degrees at impact, while the left propeller control unit ball screw position was consistent with a commanded blade angle of 79.2 degrees. The investigation concluded that the discrepancy between the actual propeller blade angle and the commanded angle was a strong indication of a discrepancy inside the PCU prior to impact, and that the left propeller had achieved an uncommanded low blade angle.
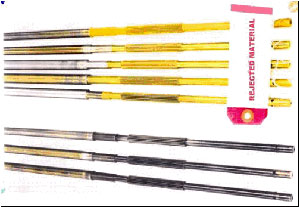
Gold color is unacceptable.
Therefore, the investigation concluded that the differences in surface hardness between the transfer tube and the quill caused the transfer tube splines to act like a file, resulting in abnormal wear of the gear teeth on the quill. The investigation found that quill wear was not envisioned during the development and certification of the propeller system.
As a result of the determination of abnormal wear of the quill, Hamilton Standard issued an alert Service Bulletin that included a description of ranges of acceptable transfer tube surface characteristics which could be identified by surface color. It was noted in the bulletin that transfer tubes which had gold-colored splines were not acceptable for use.
A copy of the alert service bulletin is available at the following link: (Service Bulletin)
Special Certification Review
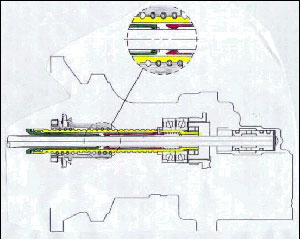
As a result of this accident, the FAA conducted a special certification review of the Hamilton Standard 14RF-9 propeller system. The purpose of this review was to assess potential airworthiness deficiencies of the propeller and identify opportunities for improvements. A key recommendation of the SCR report was to redesign the propeller system to include fail-safe features. A copy of the report issued by the special certification review team is available at the following link: (SCR Report)
As a result of the SCR recommendations, Hamilton Standard provided a redesign of the propeller system that incorporated fail-safe features. The redesign incorporated the installation of a secondary quill, which was proposed as an alternative to the requirement for repetitive inspections of quill tooth wear. A service bulletin provided instructions for installation of the secondary quill. The service bulletin is available at the following link: (Secondary Quill Installation Bulletin) Installation of the secondary quill provided a fail-safe feature in the event of a primary quill failure.
The National Transportation Safety Board (NTSB) determined that the probable cause of this accident was: "...the loss of control in flight as a result of a malfunction of the left engine propeller control unit which allowed the propeller blade angles to go below the flight idle position. Contributing to the accident was the deficient design of the propeller control unit by Hamilton Standard and the approval of the design by the Federal Aviation Administration. The design did not correctly evaluate the failure mode that occurred during this flight, which resulted in an uncommanded and uncorrectable movement of the blades of the airplane's left propeller below the flight idle position."
The NTSB, in addition to the probable cause, issued 17 findings. The key findings were:
- At impact, the left propeller blade was below the flight idle low pitch stop.
- The left propeller actuator did not respond to a propeller control unit (PCU) signal because the quill spline teeth were severely worn.
- The relatively low torque loading of the transfer tube, quill or servo ball screw would not produce mechanical wear on these components and the propeller blade angle would go to feather should a failure occur.
- The harder titanium-nitrate surface of the transfer tube spline produced rapid wear of the quill spline teeth.
- The drag from the propeller blade angle exceeded the limits of the aircraft control.
- The certification testing used a titanium-nitrate transfer tube with a smoother finish than some found in service.
The complete text of findings is available at the following link: NTSB Findings
The NTSB issued an Aircraft Accident Report on April 28, 1992, and is available at the following link: NTSB Accident Report
The Atlantic Southeast Airlines investigation team issued four recommendations to the Federal Aviation Administration (FAA) and one each to Atlantic Southeast Airlines (ASA) and the Regional Airline Association (RAA).
The FAA was tasked to:
- Conduct a certification review of the Hamilton Sundstrand 14RF propeller system.
- Examine the certification basis of other propeller systems with a similar design.
- Establish an inspection schedule for the 14RF propeller and other propellers with a similar design.
- Issue an Air Carrier Operations Bulletin (ACOB) to clarify the reduced rest regulation.
The recommendations to ASA and RAA dealt with the reduced rest periods of the flight crew.
The complete text of the recommendations extracted from the NTSB report is available at the following link: NTSB Recommendations
Low Pitch Service Experience on the EMB-120 Fleet
At the time of this accident, there had been an operational history of using the propeller pitch to gain additional descent performance. Putting the propeller pitch in reverse pitch during flight allows for a steeper descent and improved field performance. The use of reverse pitch in flight was believed to have been common even though it was not an approved procedure. In order to prevent the use of reverse pitch in flight, beta lockouts were mandated.
Another way of enhancing the performance of the aircraft during descent is to put the propeller in a low-pitch setting. With a propeller in low pitch, drag increases and can lead to a propeller over-speed if the propeller pitch drops below the flight low pitch stop. At the time of the accident, the EMB-120 had a history of propeller over-speed occurrences.
In the late 1980's, an EMB-120 over-speed committee was established to investigate these over-speed incidents. The committee consisted of representatives from Embraer, Hamilton Sundstrand, Pratt & Whitney Canada and United Technologies Research Center (as the committee chair). The investigation concluded the over-speed incidents were the result of pilot actions and not propulsion related. The corrective action was to provide a lockout mechanism in order to prevent the movement of the power levers below the flight idle detent during flight. This was eventually mandated on the EMB-120 by AD 90-17-12.
From 1988 to 1992 the EMB-120 had eight occurrences of propeller over-speed during approach. Six of these airplanes did not have a beta lockout device installed. Two of these over-speed excursions were not recoverable. A brief description of the EMB-120 over-speed occurrences is available at the following link: EMB-120 Over-speed History
On October 11, 1991, a Flight Data Recorder (FDR) and a Cockpit Voice Recorder (CVR) were required to be installed on EMB-120 aircraft. The aircraft involved in a July 21, 1992, incident had an FDR and the beta lockout installed. Investigators determined from the FDR that the beta lockout circuit breakers had been pulled.
There was no indication that the pilots on ASA Flight 2311 had accidentally or intentionally brought the power lever past the flight idle stop.
Passenger Manifest
Among the 23 people killed in the accident were Texas Senator John Tower, his daughter Marian, and NASA astronaut Manley "Sonny" Carter. The deaths of these prominent public figures caused additional media focus on this accident.
- Abnormal wear on the mating surfaces between the quill and transfer tube, leading to a disengagement of the quill from the transfer tube, and loss of blade pitch control. This further led to an uncommanded low-blade pitch, very high asymmetric drag, and a loss of airplane control.
The design load (torque) of the spline to quill is relatively small at 7 inch-pounds. Therefore, quill wear was not a concern.
Disengagement of the quill with the transfer tube or ball screw would cause the propeller to drift into the feathered position or maintain the blade angle at the time of failure.
Quill disengagement (failure) would only occur during ground feather/unfeather check when the torque loads are highest.
The introduction of the titanium nitrate-coated surface of the transfer tube was significantly harder than the case-hardened nitrate surface of the quill. The difference in hardness was not a factor due to the low loads in the system.
The first worn quill was discovered in January 1991 during a service inspection. The next worn quill was discovered on February 14, 1991. Both of the worn quills were sent in for service after the operators were unable to perform the feather/unfeather ground check.
There was no quill-wear problem reported prior to January 1991.
AD T91-10-51 This emergency AD was published on May 9, 1991 and required an immediate inspection for excessive wear of the quill and quill replacement, if necessary.
AD T91-11-51 published on May 22, 1991, and superseded AD T91-10-51. This AD referenced Hamilton Standard Service Bulletin 14RF-9-61-A49, Revision 1 for the 14RF-9 Propeller and reduced the allowable wear limits on the quill.
AD 92-08-03 was published on April 27, 1992. This AD required an initial and repetitive inspection of the ball screw internal spline teeth for wear.
AD 93-06-06, published July 6, 1993, supersedes T91-11-51 and required replacement of the quill with a new quill that did not have the nitride coating.
AD 93-16-02 published on September 7, 1993, superseded AD 93-06-06, to require inspections on other propeller models.
AD 94-22-12, published on December 5, 1994, superseded AD 93-16-02. This supersedure increased the inspection times of the previous AD due to improved materials that had been incorporated into the fleet.
AD 95-22-12, published on November 8, 1995, superseded AD 94-22-12. This superseding AD increased the inspection interval of the superseded AD. This AD also required installation of a secondary drive quill, which functions as a redundant load path, installation of a quill damper to improve lubrication and reduce motion, and repetitive inspections.
AD 96-25-20 was published January 8, 1997. This AD requires the initial and repetitive inspections of critical control components and integrates inspection items not covered by AD 95-22-12.
Airplane Life Cycle:
- Design / Manufacturing
Accident Threat Categories:
- Uncommanded Thrust Reversal
Groupings:
- Loss of Control
- Automation
- Approach and Landing
Accident Common Themes:
- Flawed Assumptions
Flawed Assumptions
The transfer tube manufacturing process was changed to improve the surface finish on the spline. Hamilton Standard had considerable experience with titanium nitrate coatings on similar applications with different finishes without any problems. However, in this application, the surface roughness, the difference in hardness and the environment in which the transfer tube operated was critical. It had been assumed that since the loads imposed on the quill were very low, that the difference in surface finish and hardness between the transfer tube and quill was not an important factor. Due to the range in allowable surface finishes that could result from the coating process, the transfer tube could induce abnormal wear on the quill and cause a loss of engagement between the transfer tube and quill, leading to a loss of propeller blade pitch control. Following the accident, the surface finish specification on the transfer tube spline was significantly revised to ensure a smoother finished surface. The revised finish specification applied to the spline surface finish both prior to and after nitrating.
Also, a disconnect of the transfer tube from the quill was considered fail-safe. The assumption had been that the disconnect would occur only when relatively high torque loads were applied to the quill. The high torque only occurs when ground idle is selected, during a feather/unfeather check, or during a rapid increase in power lever angle. Further, should a disconnect occur in flight, the analysis showed the propeller would either drift towards the feathered position or maintain the blade angle at the time of disconnect.
Luxair Flight LG9642/LH2420, Fokker F27 Mk 050, Luxembourg, November 6, 2002
On November 6, 2002, a Fokker F27 Mk 050 turboprop-powered airplane, owned and operated by Luxair and registered as LX-LGB, departed Berlin as Flight LG 9642/LH 2420 to Luxembourg. Inadequate landing visibility was reported at the destination airport and remained throughout the approach. The crew attempted an approach, but visibility remained inadequate, and a go-around was initiated. Shortly after initiation of the go-around, ATC reported that visibility had improved to above the required minimums. The captain aborted the go-around and attempted to capture the glide slope from above. In attempting to capture the glide slope, the captain moved the power levers below the flight idle detent. Moving the power levers below the flight idle detent in flight was specifically prohibited by the Airplane Flight Manual. Upon landing gear extension, a design defect momentarily released the secondary mechanical low pitch stops and allowed the propellers on both engines to transit into the reverse pitch (beta) range.
The captain recognized that reverse pitch had been attained, and he moved the power levers back into the forward thrust region. However, the pitch on the right propeller continued to reduce and eventually went fully into reverse. In response to the effects of increased drag, loss of lift, and thrust asymmetry, the captain chose to shut down both engines in an attempt to maintain control. After shutdown, the left propeller feathered, but the right propeller remained in full reverse.
The airplane touched down near the edge of a highway 3.5 km short of the runway, bounced over the highway, broke up, and caught fire. Of the 19 passengers and three crew members on board, only the captain and one passenger survived.
See accident module
Technical Related Lessons
Manufacturing processes for critical propeller control components, and changes to those manufacturing processes, must be assessed by robust process validation procedures before being implemented. With proper process validation, it is expected that no propeller failures due to manufacturing-induced defects will occur in the life of the propeller fleet. (Threat Category: Uncommanded Thrust Reversal)
- The transfer tube is approximately 36 inches long and designed to very close tolerances over this length. The close tolerances on the transfer tube were difficult to maintain after application of the nitrate coating. The hot bath method used to coat the spline of the transfer tube with nitrate produced a finish scaling and a straightening problem. To produce a more consistent transfer tube surface finish, a minor design change was made to a titanium nitrate coating method. This changed process employed a vapor deposit technique to apply the titanium nitrate at a much lower temperature. This design change solved the manufacturing issue but introduced a more coarse and harder surface on the transfer tube spline.
The coating change on the transfer tube had the unintended effect of causing a wear rate on the quill that was three or four times greater than the wear rate for the tube. However, this higher wear rate was not considered critical due to the relatively small design loads which were believed to exist between the quill and the transfer tube. This proved to be false, as vibration between the two parts caused the splines to be "filed" off of the quill. The quill splines became so worn that they were no longer able to engage the transfer tube, and the ability to change the propeller pitch was eventually lost. Consequently, due to the loss of engagement between the quill and transfer tube, the propeller blades on the left engine went to an uncommanded low pitch during approach, leading to very high asymmetric airplane drag, and a loss of airplane control.
Common Theme Related Lessons
It is essential that critical manufacturing processes, including changes to these processes, are subjected to robust validation. It is expected that when implemented, these validation processes will achieve a level of safety which results in no loss of propeller control events occurring in service during the life of a propeller fleet. (Common Theme: Flawed Assumptions)
- The titanium nitrate coating on the transfer tube produced a range of finishes from glossy, to matted or dull. The surface finish specifications allowed this range in finishes. The matted finish was much rougher and caused a more rapid wear of the quill. During validation testing, the titanium nitrate transfer tube used had a "bright gold" or "shiny" finish. Testing was not conducted using a transfer tube with a "matted gold" or dull finish, i.e., tests were not conducted to evaluate the effects of the range of finishes that could result from the coating process. Also, tests were conducted using a General Electric turbine engine, not the Pratt & Whitney PW120 engine as installed on the EMB-120. The tests did not take into account the different aerodynamic loads on the propeller and the dynamic effects of engine and airplane vibration.