Lockheed Electra L-188
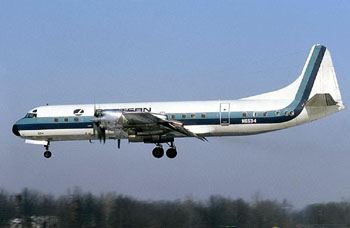
Photo copyright Bob Garrard - used with permission
Eastern Airlines, Inc. Flight 375, N5533
Boston, Massachusetts
October 4, 1960
On October 4, 1960, at 1740 Eastern Daylight Time, an Eastern Airlines Lockheed Electra L-188, N5533, crashed following takeoff from runway 09 at Logan International Airport in Boston Massachusetts. Immediately after takeoff, the airplane struck a large flock of starlings at an altitude of approximately 120 feet, ingesting birds into engines 1, 2, and 4. The propeller for engine 1 feathered automatically, and the engine was subsequently shut down by the flight crew. Engines 2 and 4 experienced abrupt thrust losses before recovering, though their recoveries were not simultaneous. The resulting thrust loss associated thrust asymmetry, and decay in airspeed caused a loss of control that led to the crash. Ten of the 72 persons on board survived the crash.
History of Flight
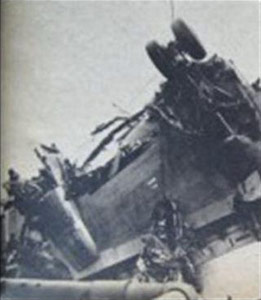
A few seconds after becoming airborne, at an altitude of approximately 120 feet, the airplane flew through a large flock of starlings. A number of these birds were ingested into engine numbers one, two, and four. Following the crash, the investigators recovered approximately 75 starling carcasses on/near the presumed area on the runway where the bird encounter occurred. The engine number 1 propeller was feathered by an autofeather system, as designed. Engine number 2 and 4 experienced substantial losses of power, but, by design, those propellers were prevented by the airplane’s system from also feathering automatically, since only one propeller is permitted to autofeather when the autofeather system is armed. The abrupt and intermittent loss and recovery of power and associated thrust asymmetry caused the airplane to yaw to the left and decelerate below the speed at which directional control could be maintained. When the speed decayed below that where the yaw could no longer be controlled, the left wing dropped, the nose pitched up, and the airplane rolled left and fell almost vertically into Winthrop Bay near the end of the runway.
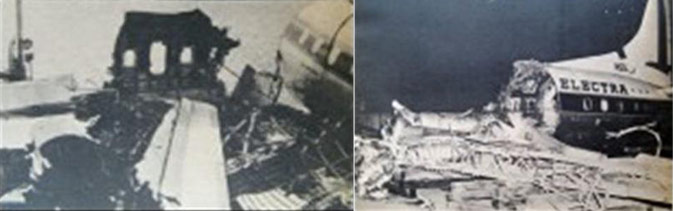
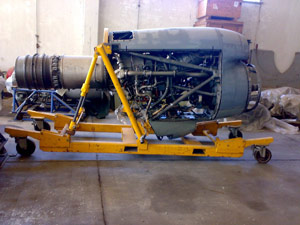
Engine Description
The L-188 Electra was powered by four Allison 501-D13 turboprop engines, each rated at a takeoff rating of 3,750 shaft horsepower. The Allison 501-D13 is a single shaft, modular design turboprop engine with a 14-stage axial flow compressor driven by a four-stage turbine. Power is supplied to the propeller through a reduction gearbox driven by a driveshaft connected to the power turbine. Gear reduction is through a series of planetary gears resulting in a 13.54 engine-to-propeller gear ratio. A complete description of the engine, propeller, and cockpit controls is contained in two documents available at these links: (Engine System Description 1) (Engine System Description 2)
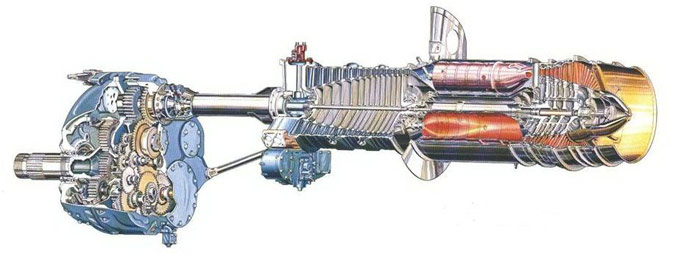
Propeller Description
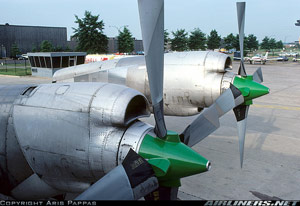
Photo copyright Aris Pappas - used with permission
The Aeroproducts A644FN-606 propeller design is a self-contained hydraulically operated propeller incorporating an integral propeller control system. Propeller rotation supplies the power through the hydraulic governor to change blade pitch, maintaining constant rotational speed by varying blade angle through a range of varying engine and aerodynamic loadings. Primary changes in propeller operating regimes, which involve governing, negative pitch, feathering, negative torque signal (NTS), and taxi operations, are initiated by mechanical signals from the cockpit control levers or engine sensors. This design concept provides an isolated propeller which functions independently of the other propellers, engine, or aircraft systems.
Secondary changes in propeller operations, which concern synchronizing, phase synchronizing, or auto-feathering, are controlled by electrical power supplied to the propeller. In the case of synchronizing or phase synchronizing, electrical power is used only to adjust or trim the self-contained hydraulic system.
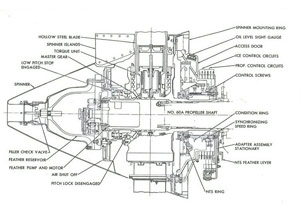
View Larger
During feathering, electrical power actuates a feathering solenoid, allowing propeller control hydraulic fluid to move the propeller blades to the full-feathered position. Electrical power is also supplied to the propeller for anti-icing, un-feathering and autofeather check procedures.
In conjunction with these primary and secondary concepts, certain design and safety features were incorporated to increase reliability, maintainability, and functional capability of the propeller. The functions include:
- The hydraulic system includes four mechanically driven pumps and one electrically driven pump.
- A hydraulic low pitch stop is provided to complement the mechanical low pitch stop as part of the over-speed protection system.
- The spinner and blade cuffs incorporate electrical anti-icing elements.
- A beta (blade angle associated with propeller reversing) range indicator is provided; and
- An air shutoff is activated when the propeller is feathered to prevent the flow of cooling air through the spinner.
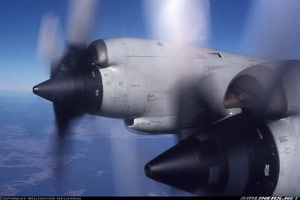
(On top of nacelle) for Allison engines
Photo Copyright Wolodymir Nelowkin – used with permission
The propeller converts engine torque to thrust, regulates this thrust to absorb engine power under varying conditions, and maintains a constant propeller rotational speed. The integral hydraulic system supplies the power required for changing propeller pitch to compensate for various loading conditions. The hydraulic system is controlled by a mechanical linkage from the power lever in the cockpit. An electrical control system trims propeller speed for synchronizing and phase synchronizing to a master propeller.
A reduction gearbox reduces the engine RPM to a useable propeller speed. For example, at takeoff and maximum continuous power, the engine operates at 13,820 RPM, while the propeller is governed to 1,020 RPM. Safety devices incorporated into the reduction gear box include a propeller brake and a negative torque system.
Autofeather system
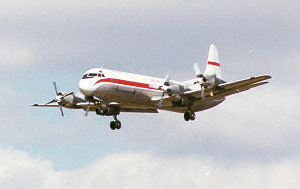
a feathered number 4 propeller
The autofeather system is intended to automatically reposition the propeller blades to a minimum drag angle, i.e., feather, for low speed, high power phases of flight, such as takeoff. Since the “windmill” drag (drag associated with a freely rotating, unpowered propeller assembly while in flight) of an unfeathered turbo propeller is extremely high, resulting thrust asymmetry can result in an airplane loss of control during low-speed flight phases. In order to reduce this risk, autofeather systems were introduced on most turboprop airplanes, including the L-188, in order to protect airplane takeoff performance and not rely on manual feathering by the pilot during critical phases of flight. Since takeoff performance is only predicated on a single engine failure, safeguards are necessary in the autofeathering circuitry in order to prevent more than one propeller from feathering during a single event.
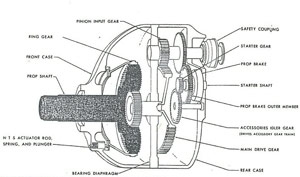
View Larger
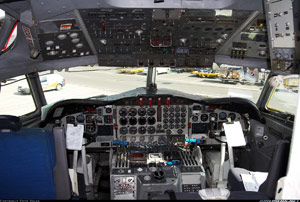
Photo copyright Petr Volek – used with permission
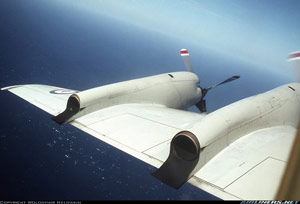
in flight with Number 1 propeller feathered
Photo copyright Wolodymir Nelowkin - used with permission
The system automatically feathers the propeller anytime the autofeather system is armed, the power lever is above 75°, and the engine is producing less than 500 pounds of thrust. Engine power loss is sensed by a system that monitors torque produced by the engine drive shaft. If a sudden loss in torque is sensed (negative torque system) the autofeather system interprets this torque loss as an engine failure and triggers an autofeather command to the propeller. A bird ingestion event, such as occurred on Eastern Flight 375, results in a momentary disruption in the gas flow path and a momentary drop in engine torque.
The autofeather system is made up of a network of inter-locking circuits through contacts in the cockpit feather switches. The arrangement is such that: (1) if any single propeller receives an auto-feather signal, or if it receives a signal in advance of signals from other propellers, it will autofeather and disarm the autofeather system for the propellers on the other three engines; and (2) if thrust switches on more than one engine close simultaneously, the inter-lock of the auto-feather circuits establishes a priority sequence (4, 1, 3, 2), allowing only one propeller to autofeather. The other propellers must be feathered manually, just as if the signals had been triggered sequentially rather than simultaneously. See cockpit diagram showing propeller controls, including autofeather system.
Bird Ingestion
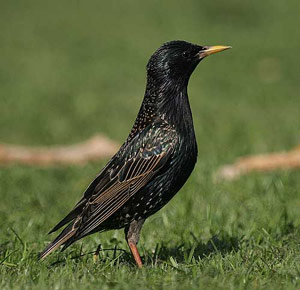
This accident was the first major transport airplane accident with substantial loss of life attributed to engine failure following bird ingestion. Turbojet and turbopropeller engines were newly introduced into commercial service in the 1950’s. As such, little was known regarding threats that would soon be experienced in service, such as failures due to bird ingestion. The engine standards associated with the Allison 501 D-13 and other turbine engines of that era did not include requirements to continue running after any type of bird ingestion event.
As a result of this accident, there was an industry-wide recognition that some level of bird threat capability would be necessary for all turbine engines. This capability has evolved into two safety objectives associated with bird ingestion threats. The first involves the assumption that an ingestion event occurs on a single engine and will fail in a manner (e.g., burst, catch fire, etc.) that will not threaten the continued safe flight of the airplane. This threat is assumed to be a large bird (goose, eagle, etc.). The second bird ingestion scenario assumes that all engines of a multi-engine airplane ingest birds simultaneously, and the combined power or thrust loss associated with each engine is no greater than the loss of a single engine on a four-engine airplane. This threat is assumed to be from small or medium size birds such as starlings, small gulls, pigeons, etc.
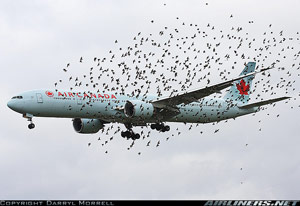
Photo Copyright Darrell Morell – used with permission
The birds encountered by Eastern Flight 375 were common starlings, which tend to congregate in huge flocks in flight, known as “murmurations.” It was believed by investigators that engines 1, 2, and 4 ingested numerous starlings. Engines 1 and 2 were primarily affected, with the propeller for engine 1 being automatically feathered and then manually shut down, and engine 2 experiencing a partial power loss and subsequent recovery. Engine 4 also experienced a partial power loss, but the investigation stated that it was not as severely affected as engines 1 or 2.
The starling was identified as a small bird for the purposes of engine ingestion standards and would later be identified as an eight-ounce threat. Because of its small size, a single bird ingestion event on large turbine engines often result in little, if any, damage. However, the major threat from birds such as Starlings comes from their tendency to congregate in large, dense flocks, which poses a particularly high threat to aviation safety.
Flocking birds, such as Starlings, are a particular hazard to aircraft due to their natural tendency to fly in close groups of several thousand individuals. This behavior has frequently led to large numbers of birds striking aircraft and engines, causing engine malfunction by gas turbine fan blade damage and/or core ingestion, as with this case in point.
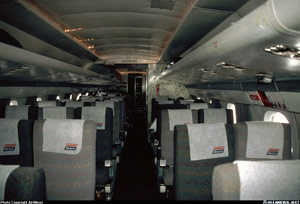
Photo Copyright Air Nikon - Used with Permission
Cabin & Seats
Investigators determined that seat restraint failures jeopardized passenger survivability in this accident, and they recommended that research be conducted which could lead to enhancements in the L-188 seat restraint structure. This accident was one of the first in a series of accidents which would lead to the development of enhanced seat, seat retention, and seatbelt standards. Although no regulations resulted as a direct consequence of this accident, it was a catalyst for advancements in the area of cabin safety.
Accident Board Findings
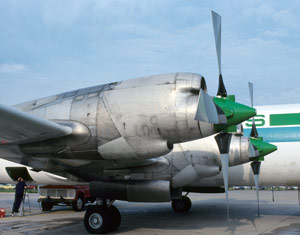
Photo copyright Aris Pappas - used with permission
The Civil Aeronautics Board (CAB) determined that:
“…the probable cause of this accident was the unique and critical sequence of the loss and recovery of engine power following bird ingestion, resulting in loss of airspeed and control during takeoff.”
The CAB report on this accident is 13 pages long. The CAB findings begin on page 8. View the accident report here
The Civil Aeronautics Board recommended on December 5, 1960, that a basic research program be initiated by the FAA aimed at improving the tolerance of all turbine engines to bird ingestion. It was also recommended that a study be made of the means of precluding bird entry into turbine engines.
The accident investigation disclosed the first failure points of the seat and seat belt attachments and also pinpointed an injury-producing environment within the cabin. In view of these findings, recommendations were made by the Civil Aeronautics Board soon after the accident with the objective of enhancing passenger safety aspects of the Electra L-188 airplane. Based on these recommendations, considerable research was engendered, intended to in an overall improvement in passenger safety.
View the text of the recommendations from page 13 of the accident report here.
CAR 4b.115, Accelerate-Stop Distance
An autofeather system aids in mitigating airplane control difficulties inherent with reacting to an engine failure, and thereby results in shorter required accelerate-stop distances than if no autofeather system was present. No crew action to shut down an engine or manually feather a propeller is allowed in response to an engine/propeller failure during takeoff.
CAR 4b.116, Takeoff Path
An autofeather system following an engine failure moves the propeller to its lowest drag blade angle. The drag reduction associated with autofeathering mitigates potential control difficulties induced by a windmilling propeller, and also allows increased engine-out climb performance when compared to a non-feathered propeller.
CAR 4b.120, One Engine Inoperative Climb
An autofeather system allows the drag benefits associated with a feathered propeller to be extended to the climb performance for the entire takeoff profile.
The text of the applicable regulations can be viewed at the following link (CAR 4b Regs). The included regulations are from CAM 4b, which includes interpretive and policy material embedded within the applicable regulations. The regulations themselves, however, are the applicable CAR 4b regulations.
CAR 13 Subpart C, Turbine Engines
CAR 13.200, Design and Construction
Within the original CAR 13 requirements for turbine engines, while the regulations did not allow any hazardous or unreliable features, there were no specific regulations regarding birds, bird strikes, or bird ingestion.
Prior to the accident there were no explicit standards relative to the bird threat for airplanes or engines. Historically, birds had not shown themselves to be a particularly major threat. Prior to the accident there were no explicit standards relative to the bird threat for airplanes or engines. Historically, birds had not shown themselves to be a particularly major threat. Reciprocating engines require lower airflows than do turbine engines, which results in smaller air intakes, and associated naturally smaller capture areas than on turbine engines. Further, reciprocating engines, due to their lower overall airflow requirements are capable of withstanding larger variations in inlet airflows than are turbine engines, so may have been less susceptible to foreign object ingestion than a turbine engine. The overall effect was that bird ingestion did not seem to be a threat to an engine's ability to experience a bird ingestion event and continue to run.
With the inception of turbine powered airplanes, it was expected that the favorable operational history with reciprocating engine-powered airplanes would continue. The Electra accident and subsequent incidents and accidents would underscore the need for specific bird standards to be applicable to turbine engines and turbine engine-powered airplanes.
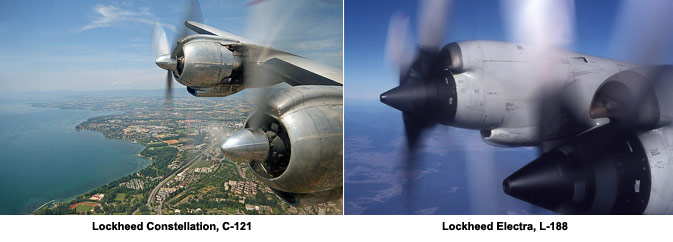
Left: Photo copyright Christian Waser - used with permission
Right: Photo copyright Wolodymir Nelowkin - used with permission
- Ingestion of multiple birds into the engines caused an engine failure and significant thrust loss on multiple engines, resulting in a loss of airplane control.
- Prior to the Electra accident at Boston, power plants on large commercial airplanes were assumed to not be vulnerable to failing when struck by birds. As such, no bird strike/ingestion standards existed at the time that the Allison 501 engine or the Lockheed L-188 aircraft were developed and certified. As a result of knowledge gained from the investigation of this accident, and subsequent experiences on other engines and airplanes, turbine engines of large commercial airplanes being produced today exhibit a substantial bird strike resistance capability to a wide variety of threats.
While bird impacts have been a regular occurrence throughout aviation history, this accident was the first transport airplane accident to have been attributed to a bird encounter. As such, there were no precursor events.
Following this accident, a comprehensive program of research into turbine engine bird ingestion was initiated by the FAA.
At the time of the accident, the Civil Air Regulations (CAR) were the effective regulations regarding certification and operation of airplanes and engines. By the time regulatory changes were issued, 14 CFR part 25 and 33 had replaced the CARs. As operational history was collected on turbine powered transport airplanes, a number of engine failure threats from foreign object ingestion had surfaced, bird threats being only one.
Advisory Circular 33-1A, Turbine-engine Foreign Object Ingestion and Rotor Blade Containment Type Certification Procedures, was published in June 1968 and included the first guidance on bird ingestion and criteria for engine certification.
While not a direct result of this accident, continued service experience with turbine engine bird ingestion, and a greater understanding of the bird threat, resulted in regulatory changes. These changes were subsequently adopted as:
14 CFR 33.77, Foreign object ingestion adopted on October 31, 1974, to initially address the threat from bird ingestion.
14 CFR 33.76, Bird ingestion,
was adopted in December 2000. This regulation is intended to improve the tolerance of turbine engines to bird ingestion.
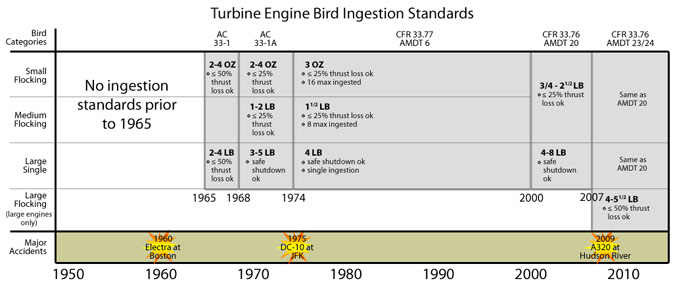
Airplane Life Cycle:
- Design / Manufacturing
Accident Threat Categories:
- Bird Hazards
Groupings:
- Loss of Control
- Automation
Accident Common Themes:
- Flawed Assumptions
Flawed Assumptions
Prior to this accident it was assumed that birds did not pose a large threat to transport airplanes. While bird encounters were relatively common, it was widely believed that a transport airplane could experience a bird impact encounter and not be adversely affected. The previous history of bird encounters tended to support that assumption. Further, design and test considerations existing in the airplanes fleet of this era, and based on operational safety prior to this accident, appeared to be effective. This accident demonstrated that certain types of bird encounters could result in transient airplane effects that, in critical phases of flight, could result in operational impacts beyond the capabilities of airplanes and flight crews.
Orville Wright in 1905
The first bird strike was reported by Orville Wright in 1905, and according to their diaries Orville … flew 4,751 meters in 4 minutes 45 seconds, four complete circles. Twice passed over fence into Beard's cornfield. Chased flock of birds for two rounds and killed one which fell on top of the upper surface and after a time fell off when swinging a sharp curve.
Cal Rodgers in 1912
The first bird strike fatality was reported in 1912 when aero-pioneer Cal Rodgers collided with a gull which became jammed in his aircraft control cables. He crashed at Long Beach, California, was pinned under the wreckage, and drowned.
United Airlines Flight 297, a Vickers-Armstrongs Model Viscount 745D
On November 23, 1962, United Airlines Flight 297, a Vickers-Armstrongs Model Viscount 745D airplane, was en route between Newark, NJ and Washington, D.C. The airplane struck two Whistling Swans, one of which penetrated the horizontal stabilizer. The left horizontal stabilizer separated from the airplane, resulting in a loss of control and the crash. All 17 people aboard the airplane were killed.
See accident module
Overseas National Airways DC-10
On November 12, 1975, an Overseas National Airways DC-10 crashed while performing a rejected takeoff. The takeoff abort was performed following impact with a flock of gulls that had been roosting on the takeoff runway. During the rejected takeoff, the number 3 engine failed catastrophically and caught fire. The engine failure caused a fuel leak, which aided fire propagation. The airplane was totally destroyed by fire. All passengers and crew members successfully evacuated.
See accident module
U.S. Air Force E-3 Sentry AWACS
On 22 September 1995, a U.S. Air Force E-3 Sentry AWACS aircraft (Call sign Yukla 27, serial number 77-0354), crashed shortly after takeoff from Elmendorf AFB, Alaska. The plane lost power to both port side engines after these engines ingested several Canada Geese during takeoff. The aircraft went down in a heavily wooded area about two miles northeast of the runway, killing all 24 crew members on board.
Space Shuttle Discovery - STS-114
The Space Shuttle Discovery hit a bird (a vulture) during the take-off of STS-114 on July 26, 2005. The collision occurred early during takeoff and at low speeds, with no obvious damage to the shuttle.
US Airways Flight 1549
On January 15, 2009, US Airways Flight 1549 from LaGuardia Airport to Charlotte/Douglas International Airport ditched into the Hudson River after experiencing a failure of both engines. The investigation has initially determined that the engine failures were caused by running into a flock of geese at an altitude of about 975 meters (3,200 feet), shortly after takeoff. All 150 passengers and five crew members were safely evacuated after a successful water landing. At the time of this entry (early in the accident investigation), the NTSB accident report has not been issued. The report will be issued at the conclusion of the investigation.
Technical Related Lessons
Turbine engine inlet ingestion of large numbers of birds can cause substantial, and in some cases catastrophic, loss of thrust or power. Safety of flight must include both a robust engine run capability following bird ingestion as well as operational strategies aimed at avoiding the bird hazard. (Threat Category: Bird Hazards)
- Due to the threat of multiple engines being adversely affected by small bird ingestion, turbine engines must have an adequate "continue to run" capability following a severe encounter with a flock of small birds. This accident was the result of the ingestion of a large number of small birds (starlings), the failure of one engine, and temporary thrust losses on two other engines. The adverse engine reactions resulted in a loss of airplane control and the accident.
Common Theme Related Lessons
Introduction of new configurations, technologies, or operations has the potential of exposing new vulnerabilities. Conversely, existing configurations may be operating safely only because these threats are being inherently protected from exposure without deliberate design intent. (Common Theme: Flawed Assumptions)
- Prior to this accident, operational experience of large transport airplane engines with respect to bird encounters and bird ingestion had been favorable. Birds were not considered to be a major threat relative to their ingestion effects. With the development of the Electra L-188, the Allison 501-D13 turbo propeller engine, and other turbine-powered airplanes of the era, it was expected that this favorable powerplant experience would continue, and that engines would be sufficiently robust to withstand whatever bird threats may exist. This accident, and subsequent accidents and incidents, underscored the need for specific standards to reduce the threats posed to turbine engine inlet systems and turbine powered airplanes.
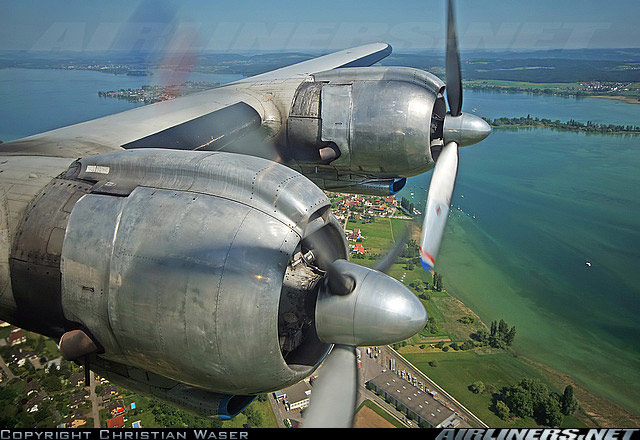
Photo copyright Christian Waser – used with permission