Hughes 369D
14 CFR Part 133 Operator, N28MP
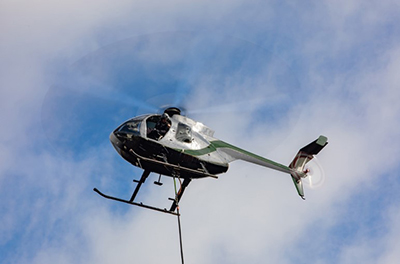
Childress, Texas
November 27, 2012
On November 27, 2012 at approximately 1558 local time, a Hughes 369D crashed approximately two miles east of Childress, Texas after it experienced a loss of engine power during an out of ground effect hover with an external load to support power line construction activities. At the time of the accident, the helicopter was conducting a 14 CFR Part 133 Class B Human External Cargo (HEC) operation. The aircraft was substantially damaged during the accident. The commercial pilot sustained serious injuries and the longline worker carried as HEC was fatally injured. Weather conditions at a facility six miles northeast of the accident site were reported as clear, visibility 50 plus miles, no precipitation, and wind calm.
The NTSB determined the probable cause of this accident to be the improper maintenance of the helicopter's fuel system which may have given erroneous fuel indications and the pilot's inadequate fuel management which led to fuel exhaustion.
NTSB accident report: CEN13FA075
History of the Flight
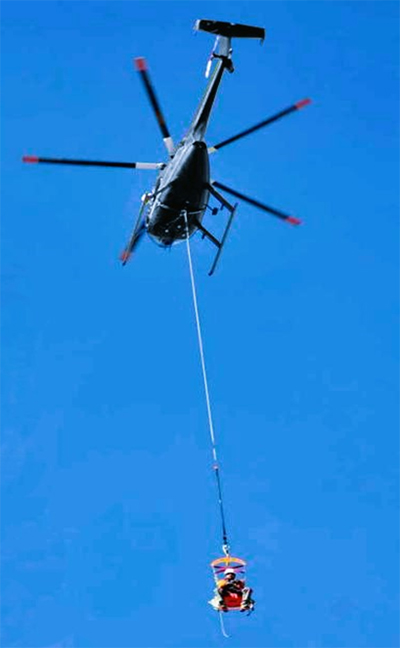
On November 27, 2012, a Hughes 369D helicopter supporting a power line construction project near Childress, Texas was operating under 14 CFR Part 133 with a Class B external load. On the accident flight, the Class B external load was a person, referred to as a longline worker, attached to a 50-foot-long external line.
The work plan was to install travelers on the power line towers. Travelers are similar to pullies and used to aid in the installation of power lines and other cables on towers. The pilot gave a safety briefing that same morning to the longline workers prior to starting work. During the briefing, the pilot stated he was not going to jettison the line in an emergency. The only method for the longline workers to jettison was to cut the line themselves.
The pilot started flying this project at approximately 0900 Central Standard Time (CST). After installing a few travelers, the helicopter flew back to the fuel truck and refueled. According to investigators, the amount of fuel that was typically added was 15 gallons and this was done by the company helicopter mechanic. During this project, different longline workers were swapped out to reduce worker fatigue.
At approximately 1100 CST, the pilot saw a company truck with passengers waving their arms. The pilot stopped working, landed, and shut down the helicopter.
The pilot was told that a section of fiber optic line near the highway fell on an energized line and they had to stop work. They requested the pilot fly the helicopter over to the fallen fiber optic line and move the line using a different external load configuration. The pilot completed this separate job at approximately 1400 CST then flew back to the fuel truck. The mechanic hooked up the original equipment that connects to the longline worker. According to the NTSB report, the mechanic hot-fueled the helicopter with 15 gallons of fuel. The longline worker was changed out with a third worker and the helicopter lifted off to continue installing travelers.
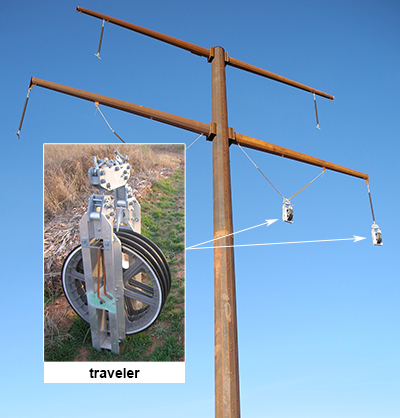
At approximately 1600 CST, the helicopter was in a hover at about 150 feet above the ground with the longline worker attached to the 50-foot longline and a secondary restraint system called a heli-bridle or belly band.
The longline worker was ready to get another traveler to install and the pilot was moving the helicopter around the eastern side of the tower structure while leaning out of the doorframe looking down at the longline worker when the helicopter suddenly yawed to the left. The pilot applied right pedal and could see the top arm of the tower through the right side of the helicopter. The helicopter started to settle as the pilot heard the engine-out horn, heard the engine spooling down, and saw the red engine-out annunciator light illuminate.
According to the NTSB's interview documents, the pilot's first thought was to get away from the tower as he would have hit the tower arm as he descended. He moved the helicopter away from the tower as it descended and then the pilot leaned back inside of the helicopter. The pilot was regaining his horizon reference and looking for an area to land. He maintained collective positioning to slow his descent until he believed the longline worker was close to or on the ground, then he lowered or "bottomed out" the collective completely to regain rotor RPM. He maneuvered the helicopter away from where he believed the longline worker was located to not land on top of the worker.
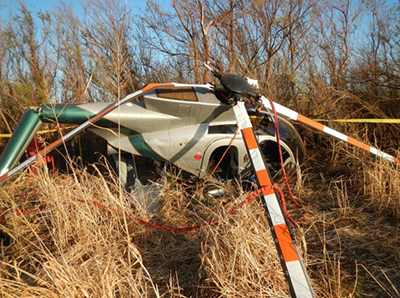
As the helicopter continued to descend, the pilot pulled collective prior to contacting the ground. The left side of the aircraft struck surrounding trees and brush and impacted the ground. After impact, the pilot stated he could not hear the engine running and pulled the fuel cutoff valve closed. The pilot also turned off the aircraft’s master electrical switch. The longline worker was approximately 10 to 15 feet behind the helicopter and was entangled in the longline and harness equipment. The other two workers who witnessed the accident came to assist. The pilot told one of the workers to call 911 and notify company personnel. The pilot and longline worker involved in the accident were taken by ambulance to the hospital where the injured longline worker was pronounced deceased.
Accident Investigation
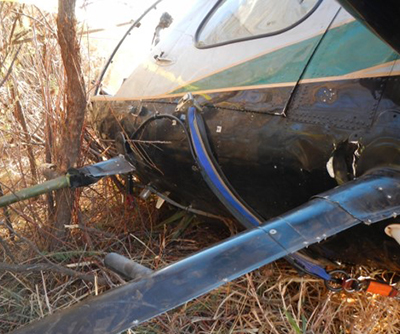
From interviews conducted during the accident investigation, witnesses stated the helicopter spun counterclockwise 180 degrees when it lost power and that the longline worker was hanging on the traveler when he was pulled off the traveler by the helicopter's longline.
The helicopter wreckage was at about a 30-degree right bank and slight nose-down attitude facing south. The tail boom was partially separated, and two of the five main rotor blades separated and were about 50 feet from the helicopter. The longline was wrapped around the main rotor mast and there was no sign of fuel around the site. The belly band was still attached to the longline worker’s harness. Although the helicopter’s main cargo hook was not attached to the longline, it is not known if this release occurred before impact or due to the impact.
The helicopter was recovered and moved to a hangar for further examination.
Incorrect Fuel Level Indications
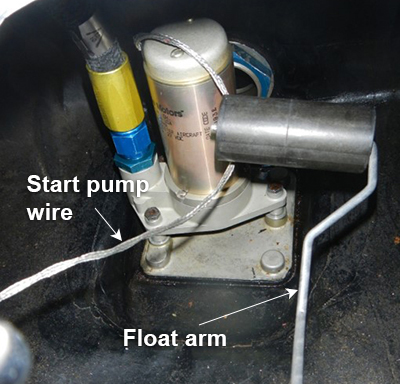
During the accident wreckage examination, investigators determined that the remaining fuel in the helicopter’s fuel tank, lines, and engine was consistent with fuel exhaustion. However, the cockpit fuel gauge was not representative of the actual fuel remaining in the helicopter’s fuel system.
Investigation revealed that the start pump electrical wire was not secured inside the fuel tank. When investigators moved the start pump wire to various positions, it interfered with the fuel quantity float transmitter giving inconsistent fuel indications.
Investigators also discovered during removal of the fuel quantity float/transmitter that three of the top retaining bolts, all adjacent to each other, exhibited a lack of torque, and the fuel low-level spring wire (low-fuel sensor whisker) was not attached and not found.
Maintenance was performed on the accident helicopter 4.2 hours prior to this accident. The fuel control and fuel start pump were replaced during this 100-hour maintenance inspection.
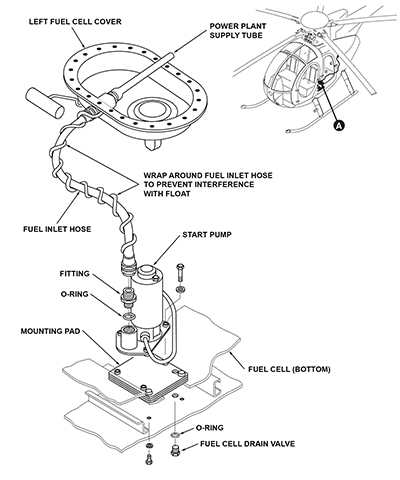
View Larger
Investigators determined that proper maintenance procedures were not followed which resulted in the start pump wire interfering with the fuel float mechanism, which gave incorrect fuel quantity indications to the pilot.
Additionally, the investigation report stated that following the replacement of the start pump, the post installation test of the fuel system's FUEL LEVEL LOW caution light failed to meet the requirements of the manufacturer's instructions for continued airworthiness. The MD Helicopters, Inc. Maintenance Manual states that testing of the FUEL LEVEL LOW caution light should illuminate when less than 35 pounds of fuel remain.
When investigators asked the mechanic how he checked the low fuel annunciator light, the mechanic said that he grounded the fuel quantity transmitter by contacting the top of the transmitter with a safety wire. This post-installation test, which was a non-standard maintenance practice, was insufficient to test the operation of the system. This maintenance practice, as it was described to investigators, would have only tested the function of the FUEL LEVEL LOW caution light circuit. The post-installation test provided by the manufacturer was intended to test the function of the entire low fuel warning system.
When this accident occurred, there was a known issue, referenced in Service Bulletin DN-150, where the fuel tank start pump wiring interfered with the fuel float after the start pump and fuel quantity sending unit had been replaced in the field. Investigators determined that improper maintenance resulted in erroneous fuel gauge indications.
Normal operation of the fuel indication system allows free movement of the float so it can move up or down to accurately indicate the fuel remaining in the tank. As the fuel level decreases, the fuel float normally moves lower to represent the fuel remaining in the tank. A float arm is attached to the float and pivots inside the fuel quantity sending unit to indicate the fuel level. The fuel tank start pump wire, if not installed correctly, can interfere with the float and float arm.
When interviewed during the accident investigation, the pilot stated he did not see any red or yellow annunciator lights illuminate before the loss of engine power.
In this accident, investigators determined the interference of the start pump wire with the fuel float and the separation of the low-fuel spring wire created erroneous and false information to the pilot.
In-flight Fuel Management Errors
From an NTSB Safety Alert SA-067 published in August 2017 regarding fuel-related accidents, fuel exhaustion and fuel starvation continue to be leading causes.
From 2011 to 2015, an average of more than 50 accidents per year occurred due to fuel management issues. Fuel exhaustion accounted for 56% of fuel-related accidents while fuel starvation was responsible for 35% of these accidents.
Fuel exhaustion is running out of fuel whereas fuel starvation is having fuel onboard, but it does not reach the engine for reasons such as a blockage, improperly set fuel selector, or water contamination.
An Interagency Accident Prevention Bulletin from the U.S. Department of the Interior published on May 30, 2023 stated there were 356 single-pilot accidents between 2012-2022 where pre-flight and/or in-flight fuel management errors led to significant aircraft damages and fatalities. The contributing factors that led to these incidents are as follows:
- Improper pre-flight planning – These events included not validating fuel levels during pre-flight inspection, improper validation of fuel quantity, or a simple misjudgment of fuel required.
- Flight plan variance – These events occurred when the pilot deviated from the initial flight plan, such as changing destination or adding stops but not fuel.
- In-flight management errors – These events included fuel burn errors, lack of in-flight monitoring, monitoring of inaccurate gauges, or not noticing indicators.
In this 2012 accident, there was no formal pre-flight fuel planning, and there was no regulatory requirement to do so. The investigation revealed that there was a flight plan variance when the pilot flew to pick up the fiber optic line as a separate flight task that deviated from the original flight plan which added flight time and included a change of destination. Accident investigators also revealed that in-flight management errors occurred due to the inaccurate fuel gauge and lack of in-flight monitoring.
According to interview statements made by the helicopter mechanic during the investigation, the helicopter mechanic drove the fuel truck and was the person who conducted the fueling for the helicopter on the day of the accident. He said on that morning he filled the helicopter with a full load of fuel. He also stated that he fueled the helicopter two additional times on the day of the accident. Each time he refueled, he said he did so with 15 gallons as that was the amount specified by the pilot. The mechanic said that on average, 15 gallons of fuel provided about 25 minutes of flying time.
No fueling logs were kept by the pilot, the mechanic, nor the operator. This made it difficult for anyone to back up the pilot when determining how much fuel was on the helicopter at any given time. The pilot was the sole person responsible for tracking inflight fuel remaining.
The pilot stated that as a rule, he would obtain fuel when the fuel gauge indicated close to 100 pounds of fuel (approximately 15 gallons) remaining which he said would be about one half hour of flight time. This practice is a reliable method to determine remaining fuel only if the fuel gauge is accurate. Unfortunately, the fuel gauge was not accurate for the accident flight.
Another inflight fuel management consideration is having the fuel truck staged in proximity to the work area. When the fuel truck is nearby, this allows the pilot to remain close to fuel reserves. This allows the helicopter to operate at minimal fuel weight which results in a higher helicopter payload and having greater power margins when operating with heavy loads or when precise flying is required. This practice of flying with minimal fuel is not uncommon in helicopter operations but it can make in-flight fuel management more critical to avoid fuel exhaustion.
The external load operation that the accident pilot was flying can be a high workload type of flying. In this dynamic, low-level operational environment, the flights may require elevated concentration to react to a multitude of challenging conditions. Flying low level near the powerline, towers, trees, and having to focus on precisely moving a person hanging on a line extending from the helicopter is a difficult task. Flying the same task of hanging travelers on multiple towers can distract from fuel management.
Investigators concluded these conditions which may have led to fuel management errors:
- No written company fuel management procedures or requirements
- Fueling was not logged or tracked formally by any person
- The pilot's inadequate fuel management
- Inaccurate fuel gauge indications due to faulty maintenance procedures
Part 133 External Load Helicopter Operations
This accident occurred while the pilot was performing a 14 CFR Part 133 operation with a Class B load where the external load was a live person, referred to as Human External Cargo or HEC.
Emergency Procedures for Power Loss During External Load Operations
Below are the applicable flight manual procedures for engine failure when performing external load operations for this accident aircraft:
- External Load - Engine Failure - the presence of an external load may further complicate a failed engine condition. Release of loads attached through the cargo hook should be accomplished as soon as practical; consistent with other safety of flight factors (e.g., rotor RPM, altitude, airspeed, ground personnel safety, etc.).
In this accident, although the pilot did not release the external load as soon as practical, there were other conditions that the pilot may have considered to perform the emergency procedures consistent with other safety of flight factors which included having a live person on the helicopter's external longline.
Emergency Procedures for Power Loss During Human External Cargo (HEC) Operations
At the time of this accident, operations conducted under 14 CFR Part 133 External Load Operations required a pilot test of knowledge and skill specific to the rotorcraft load combination (or class) of external load flown. Piloting these types of operations requires a unique skillset, and the FAA has recognized this by requiring a satisfactory demonstration of the knowledge and skill regarding external-load operations per 14 CFR Part 133.23. According to the accident report, the pilot received his knowledge and skill test for this company two months prior to this accident.
In 2012, there was no specific difference in the knowledge and skill test between a non-human external cargo (non-HEC) and an HEC operation.
In this accident, investigators learned that the pilot provided specific emergency procedures that he briefed to the longline workers that he believed were consistent with the safety of flight factors in the event of an engine or driveline failure.
When investigators interviewed the pilot, he stated during the safety briefing with the longline workers that he would not release the external load in an emergency. In addition, the longline workers stated there was no discussion nor were there any procedures for self-releasing from the longline.
When the engine failure occurred due to fuel exhaustion, the pilot did not release the longline worker immediately. The pilot attempted to fly the longline worker to the ground first then entered an autorotation, likely to protect the worker from injury. In his interview, the pilot stated he did not remember releasing the longline. However, when investigators were examining the accident site, they observed that the primary hook was no longer attached to the longline, but a secondary attaching device was still attached.
At the time of this accident, the FAA had limited guidance for FAA inspectors to authorize Class B-HEC operations. In addition, the FAA had limited guidance and requirements for surveillance or oversight to evaluate standard and emergency procedures for Class B-HEC.
Aircraft Certification Requirements for the Cargo Hook
Flying a human (HEC) on a line suspended from the bottom of a helicopter is a unique operation. In 1999, the FAA revised the certification requirements for the cargo hook to carry humans. These requirements include:
- A dual actuation device for the primary quick release subsystem;
- A separate dual actuation device for the backup quick release subsystem;
- A reliable, approved personnel carrying device system that has the structural capability and personnel safety features essential for external occupant safety;
- Placards and markings at all appropriate locations that clearly state the essential system operating instructions and, for the personnel carrying device system, the ingress and egress instructions;
- Equipment to allow direct intercommunication among required crewmembers and external occupants; and
- Appropriate limitations and procedures incorporated in the flight manual for conducting human external cargo operations.
View Part 133 External Load Helicopter Operations for more information.
However, when this accident occurred in 2012, the accident helicopter’s cargo hook had not been evaluated by the FAA to determine if it met the aircraft certification requirements to carry humans as required in 14 CFR Part 27.865(c). Due to the lack of any FAA-approved cargo hooks meeting the specific requirements for HEC, and the helicopter operators attempting to mitigate the risks involved with HEC, a secondary attaching device was often used for HEC operations.
Secondary Attaching Device – Belly Band
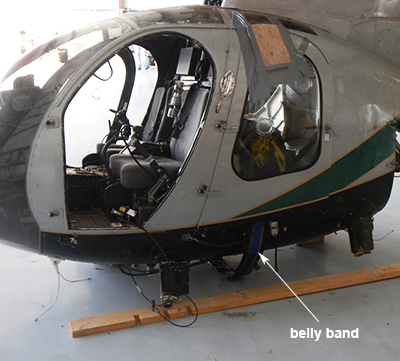
There was a secondary attaching device referred to as a belly band on this accident aircraft that was used to prevent the accidental release of a person carried as an external load. This system wraps around the lower fuselage of the helicopter through the doors to form a loop. The belly band allows the longline to be connected to both the helicopter's cargo hook and the belly band.
This secondary attaching device was used as a backup system by most HEC helicopter operators at the time. The FAA published an Information for Operators (InFO 12015) addressing the belly band on September 10, 2012, about two months prior to this accident.
The intent of the belly band was to prevent an inadvertent release of the longline worker. However, the belly band's design included a separate jettison handle for the pilot, which required the pilot to remove their hand from the flight controls to rapidly release the longline worker from the helicopter, if required to do so during an emergency.

Although there was a discussion that the pilot would not release the longline worker during an emergency, there was no ability for the longline worker to self-release. The external worker's longline was attached to the belly band and was not attached to the cargo hook, which was in the closed position.
Witness reports say the longline worker was hanging on the traveler when the helicopter’s engine failed. The longline worker was then pulled off the traveler as the helicopter descended, resulting in the fatal fall. A post-accident pilot interview noted it appeared the pilot was not aware that the longline worker was hanging on the traveler as he was trying to set the longline worker down on the ground after experiencing the power loss before he entered autorotation.
Conclusion
The investigators determined that the main cause of this accident was the improper maintenance performed on the fuel system which led to incorrect fuel indications. Due to incorrect fuel indications, the pilot did not know exactly how much fuel was on board. The pilot did not have an additional method to accurately determine remaining fuel other than using the erroneous fuel gauge, resulting in the helicopter's engine losing power due to fuel exhaustion.
The NTSB listed the probable cause as improper maintenance of the helicopter fuel system that resulted in erroneous fuel gauge indications and the pilot's inadequate fuel management, both of which resulted in fuel exhaustion during a longline hover. Also causal was the lack of company procedures to ensure adequate maintenance and fuel planning.
The NTSB listed findings related to personnel issues from the improper installation of the fuel pump by maintenance personnel and the pilot's lack of use of available resources.
Investigators also listed findings related to the aircraft's fuel level, fuel management, and incorrect servicing and maintenance of the fuel indication system.
Organizational issues identified in the findings report included availability of policy and procedures of the operator and general regulatory issues.
NTSB accident report: CEN13FA075
14 CFR Part 27.865(c) External loads
There are specific requirements within this regulation that apply to HEC.
14 CFR Part 43.13(a) - Performance rules (general)
The person performing the maintenance on the fuel system did not use the appropriate methods, techniques, and practices prescribed by the manufacturer or a practice acceptable to the Administrator.
14 CFR Part 43.15 - Additional performance rules for inspections
The person performing the inspection did not determine that all applicable airworthiness requirements were met.
14 CFR Part 91.151(b) Fuel requirements for flight in VFR conditions
The helicopter was required to have a 20-minute fuel reserve.
14 CFR Part 133.23 Knowledge and skill
This regulation requires the pilot performing rotorcraft external load operations to complete a satisfactory demonstration of knowledge and skill to the FAA.
14 CFR Part 133.43(a)&(b) Structures and design
The helicopter's external load attaching means must meet all applicable requirements of Part 27 to conduct 133 operations. In addition, the quick release device must be approved under Part 27. At the time of the accident, there were specific requirements within Part 27 for carrying HEC that the accident helicopter did not meet.
This Advisory Circular (AC) dated October 16, 1979 was applicable at the time of this accident and had no reference to HEC operations. Although there were changes to operational regulations and helicopter equipment requirements for external loads since the original publishing of AC 133-1A, it was not revised until after this fatal external load accident.
Safety Alert SA-067: Flying on Empty
An NTSB published document that contains fuel-related accident information, advice on fuel management to prevent fuel exhaustion and fuel starvation, and what a person can do to avoid having a fuel-related accident.
The is a mandatory manufacturer service bulletin in effect at the time of this accident for the start pump wire routing and fuel quantity sending inspection.
FAA Document P-8740-03: Time in Your Tanks
This FAA document provides general tips on fuel management and was referenced in the NTSB's accident report.
UPAC/HAI Guide (Nov 2011 Version)
This is a safety guide published by the Helicopter Association International (HAI) and Utilities, Patrol, and Construction Working Group (UPAC) relating to guidelines, general information, and recommendations to mitigate associated risks for those individuals and companies involved in power line or pipeline patrol and inspection, power line construction, and related power line maintenance operations.
DOT/FAA/AM-98/13 A Human Factors Perspective on Human External Loads
In 1998, to determine if there was a need for imposing new regulations on HEC operations, the Rotorcraft Standards Directorate of the Aircraft Certification Service requested the Civil Aeromedical Institute review all available accident databases to determine if HEC operations are unsafe or sufficiently problematic to warrant a change in the existing regulations. This publication described the recommendations and results of that study.
Maintenance Manual CSP-HMI-2
Manufacturer's maintenance manual mentioned in the NTSB accident report. The information in the maintenance manual referenced the proper procedures for maintenance and inspections for the accident helicopter.
InFO12015: Classifying and Using a Belly Band System as a Portable Safety Device (PSD) in Part 133 Operations
This FAA document published two months prior to this accident clarifies the use of Portable Safety Devices (PSD) for helicopter operators performing 14 CFR Part 133 Class B external load operations that involve the carriage of persons. It also provides recommendations for further equipment safety improvements for Part 133.35 operations.
These operations often support a public need, safety function, or other service that is either more efficient, safer, or only possible when conducted by a helicopter. External load operations are outside of the more structured commuter and on-demand passenger-carrying operations.
HEC Demands
Helicopters involved in these types of HEC operations often support the construction and maintenance of the nation’s power grid. Compared to ground-based services, helicopters provide a more efficient and timely means of performing this type of work. For example, the obligation of the power company to meet the electrical needs of its customers justifies using all available methods, including use of helicopters and longline workers. Here are examples of helicopters supporting the nation’s power grid:
Industry Risk
Conducting helicopter external load operations can place a high workload on the pilot. These flights are often conducted in remote areas with limited resources. The helicopter frequently operates within a flight profile that may make it difficult or impossible to land the helicopter safely in the event of an engine failure or fuel exhaustion.
External load operations are often performed low level, usually less than 300 feet above the ground, and often within the shaded avoid area of the height-velocity (H-V) diagram. Flying within the shaded area of the H-V diagram is not prohibited; however, prolonged flight in this area increases the risk for an unsuccessful autorotation in the event of an engine loss of power. Autorotation landings require a sufficient helicopter energy state as well as pilot reaction time to initiate and complete. If a pilot initiates an emergency autorotation landing within the shaded area of the H-V diagram, it may be impossible to complete the landing without causing damage to the helicopter or injury to the pilot, occupants, or longline workers.
Training Enhancements
Several years prior to this accident, the FAA showed interest in HEC operations that led to a formal study in 1998 of Human Factors Perspective on Human External Loads. The study made several recommendations including modifications to FAA regulations, some of which address emergency training. It is important to establish scenario-based emergency procedure training for specialized operations such as HEC. The aircraft's flight manual emergency procedures are general in nature and may not apply to every scenario that the aircraft may experience. Performing an emergency procedure for one scenario could be catastrophic for a different scenario.
Unique considerations for HEC emergency procedure training should include the equipment used, such as the belly band and harnesses, the HEC distance above ground level, the H-V diagram, communications between the pilot and longline worker during an emergency, and practice of these emergency procedures to verify practical application.
Without specific emergency procedures for HEC release, pilots may develop individual emergency procedures for failures similar to those which occurred in this accident. Scenario-based training may be able to provide operators, pilots, and longline workers with other procedural options for this type of emergency.
Safety Focus
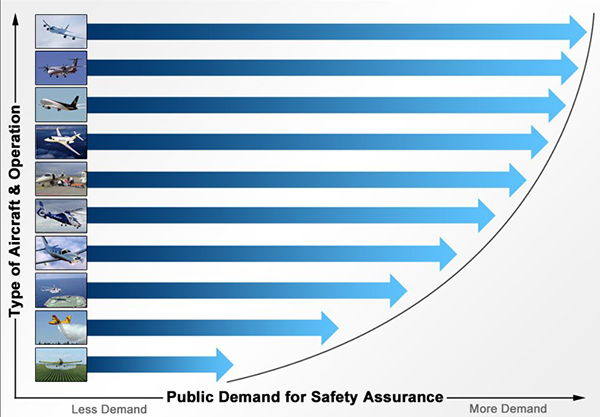
The FAA maintains a safety continuum doctrine. This doctrine seeks to meet the needs of applicants, aircraft owners, and operators while balancing these needs with the public’s demand for services and safety assurance. By constantly seeking to achieve this balance, the FAA can continue to see the safety of aviation grow while allowing capabilities, such as HEC operations, to develop in support of various consumer service and product demands. Thus, the applicable regulations for helicopter powerline maintenance operation is different than for a helicopter operation that is carrying passengers for transportation.
- Improper maintenance procedures – The mechanic did not perform the maintenance on the helicopter's fuel system in compliance with the maintenance manual. This resulted in the fuel start pump’s wire interfering with the fuel float mechanism.
- Inadequate fuel management processes – The operator did not have formal fuel management procedures for external load operations. The pilot used only the fuel gauge to determine when to fuel.
- Fuel low light was not operational – The low-fuel sensor whisker was missing from the fuel quantity sending unit and the float mechanism was not functioning properly. Since there was no independence between the fuel quantity indicating system and the low-fuel warning, the light did not illuminate.
Maintenance personnel comply with current manufacturer’s maintenance instructions.
- The manufacturer’s maintenance instructions for start pump installation and fuel system functional check were not properly followed by maintenance personnel.
Pilots comply with fuel reserve requirements through proper fuel management.
- Per the investigation report, the pilot did not ensure adequate fuel for the flight, and the amount of fuel remaining in the helicopter was consistent with fuel exhaustion.
When an aircraft enters a low-fuel condition, the pilot receives a low-fuel warning.
- The low-fuel warning system was inoperative due to improper maintenance.
Hughes 369D, Newark, Delaware, November 25, 1986
The helicopter was being flown on a maintenance check flight. Upon the pilot’s return, the engine lost power from fuel exhaustion. During an autorotative landing, the main rotor blades and tail boom were extensively damaged. The pilot reported the fuel quantity gauge indicated that 120 pounds of fuel were remaining when the engine lost power. An examination of the fuel float arm revealed it was bent and was binding on the internal fuel pump housing.
NTSB accident report: BFO87DHD02
Hughes 369D, Taholah, Washington, April 7, 2003
The pilot of a Hughes 369D helicopter had been engaged in logging operations for about an hour when the engine flamed out and the pilot executed a hard landing on a nearby road. Post-crash examination found no fuel within the fuel tank, and the fuel quantity sending float entangled in the unsecured start pump wiring, preventing the float from registering anything less than about 120 pounds of fuel. The helicopter had undergone a 100-hour inspection just before the accident flight during which the fuel quantity sending unit had been replaced. The maintenance manual contained procedures including a caution to secure the start pump wiring to prevent entanglement with the float, but this caution was addressed only in the start pump replacement procedure of the manual and not included in the fuel quantity sending unit replacement procedures.
NTSB accident report: SEA03LA058
FAA:
- FAA guidance and oversight of HEC operations were revised.
- Special emphasis was placed on the use of FAA-approved HEC cargo hooks, FAA-approved manuals for HEC operations, and qualified crewmembers that pass a knowledge and skill test specific for HEC.
- The FAA issued a revision to 8900.1 to emphasize the requirements of 14 CFR 27.865 for the use of HEC-approved hooks for all HEC operations.
- AC 133-1B CHG 1 – Advisory Circular for Rotorcraft External Load Operations - This AC was updated to include HEC information.
- SAFO 18004 – 04-23-18 – This SAFO serves to alert 14 CFR Part 133 rotorcraft operators, public aircraft operators, and government agencies of the possibility that they are conducting HEC operations with attaching means that do not meet HEC certification requirements.
- SAFO 18013 – 10-23-18 – This SAFO provides updated guidance for the applicability of part 133 as it relates to public aircraft operations (PAO) and supersedes the information conveyed in canceled SAFO 18004, Rotorcraft External Load Attaching Means and Quick Release Devices for HEC, effective of April 23, 2018.
- Following this accident, an FAA Safety Recommendation was made in 2013 and implemented in 2017 to address certification of equipment, training, and operational procedures related to HEC.
- FAA Order 8900.1, Volume 3, Chapter 51 was updated to include specific guidance for FAA inspectors related to 14 CFR Part 133 Class B HEC operations for the Rotorcraft Load Combination Flight Manual (RLCFM). This includes detailed examples for training, briefings, communications, qualifications, and other operational safety considerations.
- Advisory Circular 133-1 was updated in 2017 and 2020 to include specific HEC information.
- SAIB SW-18-15 - Special Airworthiness Information Bulletin SW-18-15 External Load Devices for Human External Cargo – This is an SAIB published on May 30, 2018, to owners and operators of helicopters to bring focus to the airworthiness requirements of 14 CFR Part 27.865 or 29.865 for cargo hooks used to perform human external cargo operations. It highlights how specific FAA approval for cargo hooks or hoists would be conveyed in the flight manuals, type certificate data sheets, or the supplemental type certificates.
Helicopter HEC Industry:
- The helicopter HEC industry best practices and procedures were revised to include fuel management procedures and policies. Equipment compliance to regulatory requirements also became a focus. This led to a change in organizational culture that resulted in additional industry safety initiatives including:
- Thorough job brief, a job analysis to define processes, risks, and responsibilities
- Defining the barriers that are in place to mitigate the risk, e.g., fuel management procedures and responsibilities
- Stop work authority to clearly lay out not only the authorization of stop work authority but the responsibility to speak up if something is off or a mission change is identified
- UPAC, an industry group that includes helicopter operators who conduct HEC operations, created a Safety Guide for Helicopter Operators. Some of the best practices include:
- Risk management procedures similar to air carrier operations (Part 121/135)
- Emphasizing crew resource management to all people involved with helicopter 133 HEC operations
- Specific experience requirements for conducting HEC operations
Operator of Accident Helicopter:
- Revised its external load dispatch procedures to include a formal dispatch release process and focused on maintenance personnel qualifications and proper maintenance procedures
- Implemented new procedures to require an additional "fuel watcher" for fuel management
- Incorporated specific fuel management procedures that included checks and balances along with minimum dispatch fuel quantities and time restrictions to avoid future fuel management failures
- Emphasized the use of manufacturer maintenance procedures and highlighted maintenance issues from this accident
AD 2016-05-09 Fuel Quantity Indicating System
As a result of this accident and other similar accidents, an Airworthiness Directive 2016-05-09 was issued and effective on April 15, 2016. The AD states: “…determine whether the fuel pump wire is wrapped around the left-hand fuel cell fuel inlet hose assembly a minimum of one revolution.” It states the unsafe condition as incorrect routing of the fuel start pump wiring. This condition could result in an erroneous fuel quantity indication in the cockpit and subsequent fuel exhaustion and emergency landing.
Rotorcraft Life Cycle
- Operation
- Maintenance/Repair/Alteration
Accident Threats
- External Load Related Occurrences
- Fuel Related
- Low Altitude Operations
- System / Component Failure or Malfunction (non-powerplant) (SCF–NP)
- System / Component Failure or Malfunction (powerplant) (SCF–PP)
Industries
- External Load
- Utilities Patrol / Construction
Accident Common Themes
- Organizational Lapses
- Human Error
- Flawed Assumptions
- Pre-existing Failures
Organizational Lapses
Operator: The manufacturer published a service bulletin to ensure the start pump wiring was wrapped around or secured to the fuel inlet hose and to perform specific inspections ensuring proper start pump wire routing and fuel quantity sending unit operation.
The operator lacked adequate training and oversight of maintenance procedures and personnel. Due to this shortfall, the mechanic did not address the aircraft manufacturer’s published service bulletin. Investigators determined that the operator did not comply with the service bulletin, nor were they required to do so by the FAA at the time of this accident.
Additionally, the operator did not have a formal fuel management program for pilots and maintenance personnel. This led to individuals creating their own procedures.
FAA: There were no applicable operational regulations or FAA policy requirements at the time of this accident for the external load operators when conducting 14 CFR Part 133 Class B HEC operations.
Human Error
Mechanic: The mechanic did not accomplish all the methods, techniques, and practices prescribed in the current manufacturer's maintenance manual about this make and model of helicopter to perform the work properly.
Pilot: The pilot was unaware of the exact fuel quantity onboard. The pilot believed he had more fuel than was present on the aircraft and relied on the fuel gauge for fuel management.
Flawed Assumptions
The operator assumed that the mechanic would follow all the manufacturer's maintenance procedures. Additionally, the operator assumed the pilot's fuel management procedures ensured adequate fuel reserves for the operations conducted.
Pre-existing Failures
The start pump wiring can interfere with the float arm of the fuel quantity sending unit if installed incorrectly on this model helicopter. The manufacturer had published Mandatory Service Bulletin DN-150 in September 1987 to address this subject. Coupled with maintenance procedural errors and fuel management errors, preexisting failure may lead to an accident.
Hughes 369D, Pylesville, Maryland, April 25, 2020
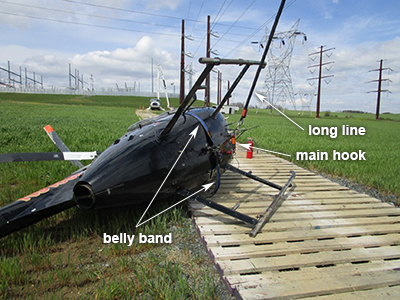
The commercial helicopter pilot was attempting to move a conductor wire with a longline while it remained in contact with the ground as a Class C rotorcraft-load combination (RLC) operation. The engine then experienced a total loss of engine power. In the autorotation, the pilot was only able to release one of two mechanisms that secured the longline to the helicopter. The pilot reported that the loss of engine power occurred about 150 feet above ground level and that he immediately pulled the belly band release lever, one of two levers needed to release the longline. The pilot stated that he did not have sufficient time to pull the second lever on the cyclic control to release the longline. Probable cause was determined to be the loss of engine power due to fuel starvation from the attitude of the helicopter while it was maneuvered to move a conductor wire. Contributing to the accident was the helicopter’s inappropriate configuration for the type of operation being conducted, which impeded the pilot's ability to release the long line and perform a successful emergency landing.
NTSB accident report: ERA20LA160
Bell UH 1H, Bethel, Alaska, June 6, 2019
The pilot reported that before departure he was told the helicopter was topped off with fuel for the multi-stop flight. He added that he did not verify the fuel quantity. About three miles from the destination airport, the engine lost power. The cause of the accident was determined to be the pilot's improper fuel planning, which resulted in fuel exhaustion and a total loss of engine power. Contributing to the accident were the inoperative fuel gauge, which was not accurately calibrated, and the pilot's reliance on the gauge.
NTSB accident report: GAA19CA344
Continental Copters OMCAT MK5A, Le Sueur, Minnesota, July 28, 2018
About 50 minutes into the flight, the engine lost power. The pilot performed an autorotation to a field, during which the helicopter impacted terrain and sustained substantial damage. Post-accident examination revealed no useable fuel aboard and the fuel gauge indicated a little over one quarter tank of fuel. The fuel transmitter was of the resistive type and was found to be corroded. The transmitter was tested using an Ohm meter, and the resistive values were uncorrelated to float position.
NTSB accident report: CEN18LA300
MD Helicopter 600N, Smethport, Pennsylvania, April 8, 2018
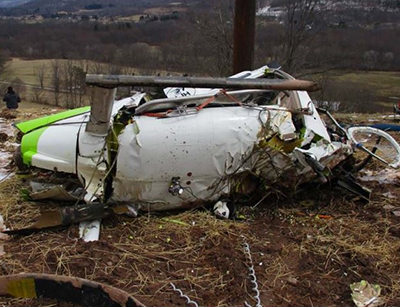
The pilot of the helicopter was conducting a power line construction flight. A static line fell between the structures and over the left front skid of the helicopter, which created a pivot point over which the helicopter rolled inverted. The pilot's failure to maintain adequate clearance during power line construction work, which resulted in the helicopter's main rotor striking and becoming entangled with a wire and a subsequent dynamic rollover and collision with terrain. Contributing to the accident was the pilot's and linemen's decision to continue work without a secondary safety device installed, which was contrary to standard operating procedures. During the investigation, FAA inspectors determined the company's Rotorcraft Load Combination Flight Manual had inadequate procedures and training for human external cargo.
NTSB accident report: ERA18FA122
Technical Related Lessons
To avoid inflight fuel management errors, the flight crew should have more than one method to monitor remaining onboard fuel. (Threat Category: Fuel Related)
- Accurate fuel management only exists if the flight crew knows exactly how much fuel is on board. Relying only on one method, such as the fuel gauge, can lead to fuel management errors, especially if that one method is inaccurate.
- Best practices advise that having at least two methods to monitor fuel helps alert the flight crew to a possible fuel management error if they do not match. Among options, one effective fuel management process includes the flight crew measuring how much fuel was onboard at the start of the flight, determining how much flight time elapsed, then calculating how much fuel remains based on fuel burn. If any of these steps use inaccurate information, fuel management errors occur.
- In this accident, the fuel gauge was inaccurate and the low-fuel warning system was inoperable because its function was not independent from the primary fuel quantity indicating system. Thus, the fuel indications to the pilot did not accurately display the correct quantity of fuel. Without a second method to determine fuel quantity, the pilot did not have correct information.
Operators should ensure all applicable maintenance procedures for the make and model of aircraft are followed, especially for critical fuel or powerplant systems. (Threat Category: System / Component Failure or Malfunction (powerplant) (SCF–PP))
- Operators should ensure that maintenance personnel are trained for the specific make and model and follow the manufacturer’s most current technical data and applicable procedures.
- In this accident, the fuel start pump wire was not properly secured. In addition, the low fuel warning system was not tested per the manufacturer’s instructions. This led to inaccurate fuel quantity and no low-fuel caution light indications to the pilot.
- If the mechanic had followed all maintenance procedures specific for this make and model of aircraft, it is highly probable that the fuel pump installation and associated maintenance procedures would have been completed correctly and there would not have been any fuel indication errors to the pilot.
Common Theme Lessons
To reduce the risk of fuel exhaustion, there should be an effective and formal fuel management process in place that is used companywide. (Common Theme: Organizational Lapses)
- A formal fuel management process should address preflight planning, preflight fueling, inflight fuel management, risk mitigations, and specific company procedures to address high workload distractions, minimum dispatch fuel quantities, etc. along with actions to prevent fuel exhaustion and fuel starvation.
- Investigators determined that a formal companywide fuel management process did not exist for this company at the time of the accident.
- The pilot's inflight fuel management errors due to an inaccurate fuel gauge were not mitigated and ultimately led to fuel exhaustion.