Airbus AS350B3e
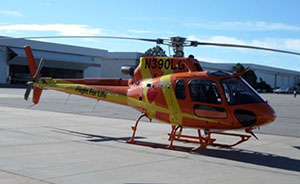
Source: NTSB
Air Methods Corporation, N390LG
Frisco, Colorado
July 3, 2015
On July 3, 2015, about 1339 Mountain Daylight Time, an Airbus Helicopters AS350B3e (marketed as the Airbus H125) crashed at the start of a public relations mission. Immediately after takeoff while climbing, the helicopter began to spin counterclockwise and crashed into a parking lot, impacting a recreational vehicle (RV) adjacent to the heliport. A post-crash fire occurred. Both flight nurses sustained major injuries. The pilot was fatally injured.
The flight was operated under 14 Code of Federal Regulation (CFR) Part 135 on a company flight plan. Visual meteorological conditions prevailed at the time of the accident.
The National Transportation Safety Board (NTSB) determined the probable cause of this accident was Airbus Helicopters’ dual-hydraulic AS350B3e helicopter’s (1) incomplete preflight hydraulic check, which depleted hydraulic pressure in the tail rotor hydraulic circuit, and (2) lack of appropriate alerting to the pilot that hydraulic pressure was not restored before takeoff. The pilot did not perform a hover check, as required by operational procedures, which could have allowed the pilot to verify the helicopter’s controllability. Contributing to the severity of the injuries was the helicopter’s fuel system, which was not crash resistant and facilitated a fuel-fed, post-crash fire.
NTSB Report: CEN15MA290
History of Flight
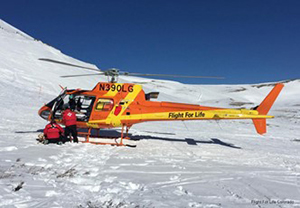
Source: Flight for Life Colorado
On July 3, 2015, at 1339 MDT, an Airbus Helicopter AS350B3e, registered and operated by Air Methods Corporation, took off from the Summit Medical Center Helipad in Frisco, Colorado. The purpose of the flight was to attend a Boy Scout camp on a public relations mission with a crew of one pilot and two flight nurses.
Immediately after takeoff, the pilot experienced loss of control of the helicopter. A flight nurse recalled a rough takeoff with an unusual pitch. Investigators determined that as the pilot continued the takeoff, the helicopter began to spin violently counterclockwise. After reaching around 100 feet in the air, the helicopter began to descend, still spinning. The pilot was unable to regain control and the helicopter crashed into a parking lot adjacent to the helipad, impacting an RV. Almost immediately, fuel began to spill from underneath the helicopter. Approximately three seconds after impact, the fuel ignited, resulting in a post-crash fire. One of the flight nurses was ejected upon impact, sustaining major injuries. The second nurse awoke, pushed the left side door of him and freed himself. He received severe second- and third-degree burns. The pilot sustained fatal blunt force trauma and thermal injuries.
Accident Site
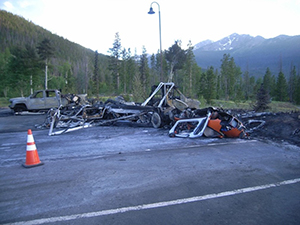
Source: NTSB
The site of the crash was a parking lot adjacent to the helipad, with the helicopter impact point being 360 feet southwest from the pad, according to the NTSB report. After reaching an altitude of approximately 100 feet, the helicopter descended and struck the ground. The helicopter rolled onto its right side, striking an unoccupied RV.
The lack of a crash resistant fuel system led to a post-crash fire, consuming or severely damaging most of the aircraft. This included the main fuselage and tail-boom.
A video of the accident events is below:
Airbus AS350 Information
The Airbus AS350B3e, serial number 7595, was registered to Air Methods Corporation. Preceding the accident, the aircraft was maintained under an FAA-approved aircraft inspection program, and no anomalies were found that would have affected the outcome of the accident on the aircraft. The helicopter was equipped with a Turbomeca Arriel 2D turbo-shaft engine, a three-bladed main rotor system, a two-bladed tail rotor system, a dual hydraulic system for the main rotors, and a single hydraulic system for the tail rotor hydraulic actuator. The single hydraulic system included a hydraulic yaw load compensator for backup hydraulic power if the single system failed. Post-crash, the aircraft endured significant thermal damage with fractured blades, damaged fuselage, and burned control systems due to the fire.
The AS350B3e helicopter is the eighth derivative model of the AS350, first certified in 1977. The accident helicopter was manufactured in 2013 with much of the design remaining from the 1977 certification. Occupant protection regulations for energy absorbing seats and crash-resistant fuel systems (CRFSs) were introduced by the FAA in 1989 and 1994 respectively. None of these safety improvements were required to be implemented in the manufacturing of the new derivatives of the AS350. The manufacturer included energy-absorbing crew seats in later derivatives, though the manufacturer did not implement CRFSs voluntarily prior to this accident, though designs were in development at the manufacturer, which were implemented at a later date.
AS350B3e Single/Dual Hydraulic System
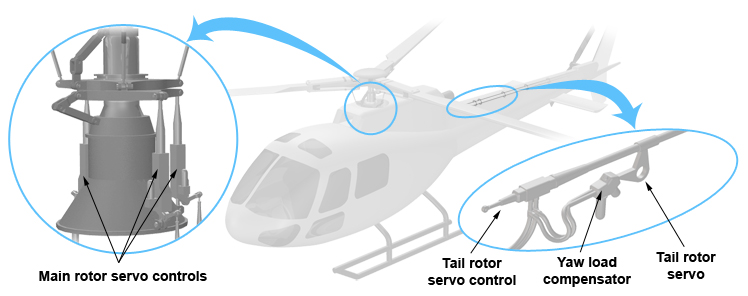
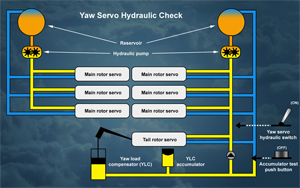
(View Large Image)
The AS350 series has multiple configurations of hydraulics controls systems. The AS350B3e comes equipped with a dual hydraulic system for the main rotor and uses only a single hydraulic system for the tail rotor. The system components consist of the hydraulic systems, a yaw servo, a yaw servo hydraulic switch, a yaw load compensator, yaw load compensator accumulator, and accumulator test button.
According to the preflight expanded checklist, the pilot is to turn off the yaw servo hydraulic switch. This separates the main and tail hydraulic systems and allows the testing of the yaw load compensator and accumulator. Once the pilot turns off the yaw servo hydraulic switch and depresses the accumulator test push button, the hydraulic assistance is removed, and the pilot is to test the pedals. Once this routine is completed, the pilot is to reengage the yaw servo hydraulic switch to "ON," restoring the hydraulic assistance to the pedals. On the accident flight, the pilot failed to reengage the yaw servo hydraulic switch to “ON” and therefore did not repressurize the system.
Operation of the tail rotor controls with hydraulic assist requires a light pedal force, but the force required increases to 30-45 pounds with yaw load compensator pressure. However, with the yaw load compensator and yaw load compensator accumulator depleted, the pedal force to maintain a steady heading would be about 161 pounds, per the NTSB accident report. Without any indication of loss of tail rotor hydraulic pressure, the pilot may not recognize the need for these large pedal forces.
Familiarity of differences between AS350 models and lack of visual feedback to the pilot during preflight checks, other than just the hydraulic system switch position, can contribute to the likelihood of not engaging hydraulic power to the tail rotor controls if all the steps of the preflight checklist are not followed. The accident investigation concluded that the pilot failed to reengage the yaw servo hydraulic switch after performing the preflight hydraulic system check. The lack of hydraulic assistance to the pilot resulted in pedals feeling stuck unless considerable force was used. As a result, the pilot lost control of the helicopter and crashed.
Hover Check
A hover and systems check consists of bringing the helicopter to a stabilized hover before initiating takeoff. The FAA published SAFO 16016, "Helicopter Stabilized Hover Checks Before Departure", dated November 15, 2016, to remind pilots of the safety benefits of performing a hover check.
The Helicopter Flying Handbook (FAA-H-8083-21B) states the following in Chapter 9, section Vertical Takeoff to a Hover: "A vertical takeoff to a hover involves flying the helicopter from the ground vertically to a skid height of two to three feet, while maintaining a constant heading. Once the desired skid height is achieved, the helicopter should remain nearly motionless over a reference point at a constant altitude and on a constant heading." Further, the Helicopter Flying Handbook states, "Very slowly increase the collective until the helicopter becomes light on the skids or wheels. At the same time apply pressure and counter pressure on the pedals to ensure the heading remains constant. Continue to apply pedals as necessary to maintain heading and coordinate the cyclic for a vertical ascent. As the helicopter slowly leaves the ground, check for proper attitude control response and helicopter center of gravity. A slow ascent will allow stopping if responses are outside the normal parameters indicating hung or entangled landing gear, center of gravity problems, or control issues."
In the accident sequence, prior to lift-off, the pilot performed his preflight takeoff checks that included the yaw servo hydraulic test. Per instructions in the Airbus AS350B3e Series Expanded Checklist, the pilot disengaged the yaw servo hydraulic switch to check the hydraulic assistance; however, he failed to return the switch to the "ON" position.
Upon completion of the preflight checklist, the pilot resumed his takeoff sequence and lifted into a climb, appearing to bypass a hover check. During ascent, the helicopter immediately began to spin as shown in the video footage from the landing pad. The combination of unanticipated yaw and taking off perpendicular to the wind's direction contributed to the pilot's inability to counteract the helicopter's torque. These factors lead to the loss of control of the helicopter, which could have been possibly prevented with a hover check.
Tail Rotor Hydraulic System Check
The hydraulic pressure check was moved from a preflight operation to a postflight check. The FAA issued Airworthiness Directive (AD) 2015-22-52 to move the yaw servo hydraulic pressure check to postflight checklists. A superseding AD 2015-22-53 was issued with clarifications on October 30, 2015 and finalized December 1, 2015. These were implemented in order to reduce the likelihood of further similar occurrences.
Indicator Lights Integration
On August 21, 2014, Airbus Helicopters issued Safety Information Notice No. 2776-S-29 to provide information about the preflight hydraulic check for AS350B3 helicopters with a dual hydraulic system in response to two similar accidents in Albuquerque, New Mexico and Temple, Texas. In addition, the manufacturer distributed Service Bulletin (SB) No. AS35067.00.64 on February 25, 2015 to add an indicator light to helicopters as a visual aid for pilots to alert them to the switch being in the "OFF" position. At the time of the accident, the service bulletin was considered non-mandatory and the helicopter was not equipped with the indicator light.
In response this accident and the two prior accidents, the FAA issued Airworthiness Directive (AD) 2018-01-12 to add the hydraulic switch position indicator light.
Incorporating Later FAA Regulations on Early Type Designs (Changed Product Rule)
The helicopter was the eighth derivative model of the AS350, first certified in 1977. The accident helicopter was manufactured in 2013 with much of the design remaining from the 1977 certification. Occupant protection regulations for energy-absorbing seats and CRFSs were introduced by the FAA in 1989 and 1994 respectively.
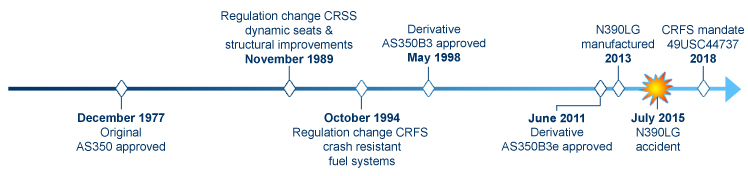
The FAA had published research on rotorcraft post-crash fires. None of these safety improvements were required to be implemented in the manufacturing of the new derivatives of the AS350, and the manufacturer did not implement these safety improvements voluntarily. The regulatory basis for designation of applicable regulations is discussed in the Relevant Regulations / Policy / Background section.
In the years prior to this accident, the FAA began new research on post-crash fires and looked for a means to increase the incorporation of CRFSs into the US fleet. The FAA began the process, tasking the Aviation Rulemaking Advisory Committee (ARAC) in early 2015 and creating the Rotorcraft Occupant Protection Working Group in late 2015. This industry group researched the effectiveness of these later safety regulations and made recommendations on future manufacturing of older type designs and proposed retroactive solutions for installation on the existing fleet.
Conclusion
This accident resulted from issues related to the tail rotor single hydraulic system that required a specific series of pilot preflight actions to assure system safety. Further, the pilot did not perform a hover check that would have presented a condition where there was no tail rotor hydraulic boost, and could have allowed a safe abort to the takeoff. Possibly adding to the pilot's misinformation was the fact that there was no indication of lack of tail rotor hydraulic boost.
The severity of the injuries and death of the pilot were worsened by the lack of retrofit or manufacturing cut-in dates for crash-resistant fuel systems and crash-resistant seats and structures.
The NTSB determined the probable causes of the accident to be:
- Airbus Helicopters' dual-hydraulic AS350 B3e helicopter's (1) preflight hydraulic check, which depleted hydraulic pressure in the tail rotor hydraulic circuit, and (2) lack of salient alerting to the pilot that hydraulic pressure was not restored before takeoff. Such alerting might have cued the pilot to his failure to reset the yaw servo hydraulic switch to its correct position during the preflight hydraulic check, which resulted in a lack of hydraulic boost to the pedal controls, high pedal forces, and a subsequent loss of control after takeoff.
- Contributing to the accident was the pilot's failure to perform a hover check after liftoff, which would have alerted him to the pedal control anomaly at an altitude that could have allowed him to safely land the helicopter.
- Contributing to the severity of the injuries was the helicopter's fuel system, which was not crash resistant and facilitated a fuel-fed, post-crash fire.
NTSB Report: CEN15MA290
New Recommendations
As a result of this investigation, the NTSB made the following new safety recommendations:
To the Federal Aviation Administration:
Require that existing Airbus Helicopters dual-hydraulic AS350-series helicopters be equipped with a visual and an aural alert for the loss of hydraulic boost to the pedal controls, which would result in increased pedal loads. (A-17-8)
To Airbus Helicopters:
For newly manufactured dual-hydraulic AS350-series helicopters, assess and implement changes to the dual hydraulic system that would both ensure pedal control hydraulic assistance and mitigate the possibility of pilot error during any check of the hydraulic system. (A-17-9) For existing dual-hydraulic AS350-series helicopters, assess and implement changes to the dual hydraulic system that would both ensure pedal control hydraulic assistance and mitigate the possibility of pilot error during any check of the hydraulic system. (A-17-10)
To the Federal Aviation Administration and the European Aviation Safety Agency:
After the actions requested in Safety Recommendation A-17-10, require operators of Airbus Helicopters dual-hydraulic AS350-series helicopters to incorporate changes to the dual hydraulic system to both ensure pedal control hydraulic assistance and mitigate the possibility of pilot error during any check of the hydraulic system. (A-17-11)
To the Association of Critical Care Transport:
In collaboration with the Association of Air Medical Services and the Air Medical Operators Association, establish a working group to develop and distribute guidelines, for those who purchase, lease, or contract for helicopters, regarding the equipment and systems that would enhance the helicopters' crash-worthiness, including, at a minimum, a crash-resistant fuel system and energy-absorbing seats. (A-17-12)
To the Association of Air Medical Services and the Air Medical Operators Association:
Work with the Association of Critical Care Transport to establish a working group to develop and distribute guidelines, for those who purchase, lease, or contract for NTSB Aircraft Accident Report helicopters, regarding the equipment and systems that would enhance the helicopters' crash-worthiness, including, at a minimum, a crash-resistant fuel system and energy-absorbing seats. (A-17-13)
Previously Issued Recommendations
As a result of this accident investigation, the NTSB previously issued the following recommendations:
To the Federal Aviation Administration:
Prioritize Airbus Helicopters’ incorporation of its retrofit kit for crash-resistant fuel systems into AS350B3e and similarly designed variants to accelerate its availability to operators. (A-16-8)
Issue a special airworthiness information bulletin (SAIB) informing all owners and operators of AS350B3e and similarly designed variants of the availability of a crash-resistant fuel system retrofit kit and urging that it be installed as soon as practicable. To encourage helicopter owners and operators to retrofit existing helicopters with a crash-resistant fuel system, the SAIB should also discuss the helicopter accidents cited in this report. (A-16-9)
Issue an SAIB that is periodically updated to inform all helicopter owners and operators about available modifications to improve fuel system crash worthiness and urge that they be installed as soon as practicable. To encourage helicopter owners and operators to retrofit existing helicopters with a crash-resistant fuel system, the SAIB should also discuss the helicopter accidents cited in this report. (A-16-10) at issuance of report.
To the European Aviation Safety Agency:
Incorporate crash-resistant fuel system retrofit kit into AS350B3e and similarly designed variants, prioritize its approval to accelerate its availability to operators. (A-16-11)
Previously Issued Recommendations Reiterated in This Report
The NTSB reiterated a previous recommendation related to crash-resistant flight recorder systems. The complete recommendation can be found in the NTSB report and recommendations.
The letter transmitting the recommendations to the FAA is included at the following link: NTSB Safety Recommendations.
14 CFR Part 21 Certification Procedures for Products and Parts (Part 21) performs multiple functions, including definition of the processes by which aeronautical products are certified. When a manufacturer/modifier applies for a TC or STC, Part 21 establishes the processes that must be followed and the regulations for which compliance must be demonstrated. At TC or STC application, the set of applicable regulations is defined and, in general, remains static for the life of the product.
The various CFR parts, the safety standards associated with airplane or rotorcraft design, are amended on a regular basis, generally to increase the level of safety associated with regulatory requirements. As regulations evolve, an original product is not normally required to comply with later amendments to the applicable regulations. However, if a manufacturer/modifier makes an application to change a certified product, with few exceptions, the changed product is required to show compliance to the regulations in effect at the time of application for the changed areas. Various regulations contained in Part 21 define the certification processes, for any aeronautical product, for which compliance must be demonstrated before a TC or STC is issued.
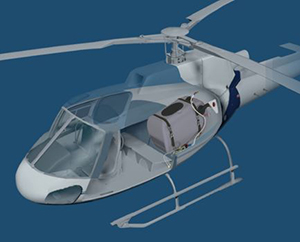
The actual helicopter involved in this accident did not have a CRFS installed. The original certification basis for the AS350 series did not include a requirement for CRFS in 1997. This regulation was added for new type designs in 1994. 14 CFR 21.101 identifies when a type design change (like a later model AS350) would be required to adopt these later safety regulations. The AS350B3e made no changes to the fuel system, and no increase in the certification basis was made.
The requirements for retrofit and forward manufacturing cut-in of CRFSs was studied by the FAA during an industry advisory board, the ARAC Rotorcraft Occupant Protection Working Group (ROPWG). The ROPWG recommended a series of occupant protection regulations, including both CRFSs and CRSS be at least partially implemented. Congress mandated the CRFS requirements for operation in the U.S. airspace. The mandate, codified in 49 U.S.C. 44737 (2018), applies to newly manufactured rotorcraft after April 5, 2020.
Regulatory and guidance material related to this accident, at the appropriate amendment levels, is provided in this section. Links to FAA safety bulletins and the ROPWG reports are also provided.
The manufacturer had not implemented CRFSs voluntarily prior to this accident, though designs were in development at the manufacturer, which were implemented later. Official FAA testing of one of the retrofit designs is shown in the following video.
14 CFR 21.17 Designation of applicable regulations
This regulation was in effect at the time of application for the original type certificate on the Airbus AS350 and established the original certification basis. Follow-on derivative models, including the AS350B3e, used largely the same certification basis except for areas that were substantially different than the original design and required compliance with newer regulatory amendments. Since the original windscreen was not changed as part of the type design, the certification basis for the original equipment manufacturer (OEM) fuel system was not changed for derivative models. At the time of application for the original TC, there were no crash-resistant fuel system requirements applicable for the helicopter.
14 CFR 21.115 Applicable requirements
This regulation was in effect at the time of application for the AS350B3e. This regulation pertains to STCs, but has the same effect as 21.17, in that it establishes the certification basis for the STC. This regulation also invokes the requirements of 21.101 which requires the adoption of the regulations in effect at the time of application that are directly applicable to the changed areas identified in the STC application.
14 CFR 21.101 Designation of applicable regulations
Policy material associated with this regulation explains that 21.101 was adopted to "enhance safety by incorporating the latest requirements into the type certification basis for the changed product to the greatest extent practicable." The original version of this regulation was adopted in 1965. The regulation establishes a means to identify the applicable regulations and their appropriate amendment levels when defining the certification basis of a changed or modified product. The regulation requires the adoption of the regulations in effect at the time of application that are directly applicable to the changed areas identified in the TC amendment application.
14 CFR 27.695 "Power boost and power-operated control system"
14 CFR 27.952 "Fuel system crash resistance"
14 CFR 27.561(b)(3) "with amendments that increased inertial load factors"
14 CFR 27.562 "Emergency landing dynamic conditions"
Advisory Circular 27-1B – Details on methods of compliance for both crash resistant fuel systems and seat certification.
FAA-H-8083-21B - Helicopter Flying Handbook
Title 49 USC 44737 (2018) Helicopter fuel system safety
There were gaps in the communication channels between the manufacturer and operator and their bases.
On August 21, 2014, a year prior to the accident, Airbus Helicopters released Safety Information Notice (SIN) No. 2776-S-29 as a warning to pilots of the preflight hydraulic checks. Airbus warned that if the step to restore hydraulic pressure was omitted, this could lead to pilot difficulty in moving the pedals. According to the pilots of the Frisco base, Air Methods had posted this bulletin in their office before the date of the accident.
On February 25, 2015, four months prior to the accident, Airbus Helicopters issued Service Bulletin No. AS350 67.00.64 for AS350-series helicopters with a dual hydraulic system to incorporate a "HYD2" light on the caution and warning panel that would flash if the yaw servo hydraulic switch was in the "OFF" position. The pilot could use this information to infer that the tail rotor hydraulic circuit was isolated from the hydraulic pressure provided by the lower hydraulic system, which would result in increased pedal loads. This Service Bulletin was not mandated by the FAA at the time of the accident, and the company had not initiated incorporation into their fleet due to a lack of installation kits and the lack of a FAA-approved Rotorcraft Flight Manual Supplement with the kit from the OEM.
In post-crash interviews, both the chief pilot and vice president of safety and risk management shared statements pointing to a lack of communication to the 300 individual bases. The vice president further stated that one of his "major pain points" was that it could sometimes be difficult to communicate the "corporate expectation all the way out into the field on a consistent basis." He added that this situation would not have compromised safety because "everybody out in the field...based on their experience and their professionalism, did a good job."
In the time following the accident, Air Methods accelerated its timeline to complete the installation of MOD No. 07-4622, the HYD2 light, to its entire AS350 fleet. Additionally, Air Methods made the decision to implement a crash-resistant fuel system to its AS350 fleet, along with increased emphasis on differences training for the single and dual hydraulic system AS350s.
- Lack of hover check - No hover check was performed prior to takeoff
- Lack of warning indicator - No clear status indicator or configuration warning was available to the pilot regarding the hydraulic system status to ensure the helicopter was ready for flight
- No crash-resistant fuel system - No crash-resistant fuel system was available or required. However, a CRFS would have decreased the likelihood of a post-crash fire and potentially increased survivability
Pilots thoroughly complete all preflight and postflight checklists without error.
- The pilot did not reengage the yaw servo hydraulic switch as instructed in the expanded preflight checklist, therefore not restoring the tail rotor hydraulic system. The pilot was unable to regain control of the aircraft due to a significant increase in pressure needed to control the pedals.
Instrumentation for a hydraulic system includes visual and/or aural warnings when the aircraft is not in a flight configuration during a preflight check.
- A notable warning of the incorrect position of the yaw servo switch was not present in this accident.
Hover checks will be performed prior to flight.
- Prior to take-off, the pilot did not perform a preflight hover check and instead immediately began to climb. Without the hover check, the pilot did not notice the increased pressure in his pedals and lack of control of the helicopter, resulting in an uncontrollable spin.
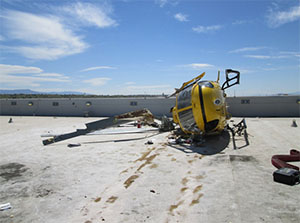
Source: NTSB
Airbus Helicopters AS350B3e, 04/09/2014 in Albuquerque, New Mexico
This AS350B3e accident occurred in Albuquerque, New Mexico on April 9, 2014, with the aircraft taking off from a hospital rooftop. The pilot attempted to turn left to clear the platform and hospital, but lost control and kept spinning. According to the NTSB report, the pilot ensured that he had completed the preflight hydraulic check and did not note anything abnormal with the pedals. Despite this, during takeoff, the pilot attempted to turn left, however the helicopter kept turning. The pilot attempted to use the right pedal to stop the spin, but noticed the pedal felt jammed. During inspection of the crash, suspicion pointed toward lack of reengagement of the yaw servo hydraulic switch, though that could not be determined based on available information.
NTSB Accident Report: CEN14FA193
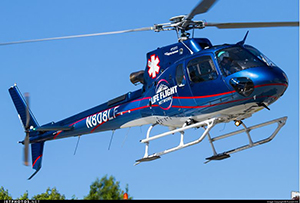
Source: Russel Hill
Airbus Helicopters AS350B3e, 06/26/2014 in Temple, Texas
This helicopter was operated by Air Methods under 14 CFR Part 91. Like the Albuquerque accident, the pilot reported the pedals being locked in the neutral position immediately after takeoff, not allowing him to correct the helicopter's rotation. In response, the pilot executed a precautionary hovering autorotation after he could not regain control. No injuries were reported, and the helicopter sustained only minor damage. Examination of the accident by the NTSB revealed that the pilot failed to reengage the yaw servo hydraulic switch, which resulted in complete lack of hydraulic boost to the tail rotor system and increased the load required to move the control pedals.
NTSB Accident Report: CEN14IA329
Air Methods Changes
- Accelerated timeline to complete installation of MOD No, 07-4622, the HYD2 light, on dual hydraulic AS350 helicopters.
- Working collaboratively on a crash-resistant fuel tank solution, while committing to retrofit all AS350 and EC130 fleet with crash-resistant fuel tanks following STC approval.
- Non-mandatory service information notices and service bulletins are now reviewed by the director of operations and distributed for further review, analysis, and implementation.
- Increased emphasis on differences training for pilots flying both single and dual hydraulic AS350 helicopters.
Aviation Rulemaking Advisory Committee (Industry and FAA)
- Rotorcraft Occupant Protection Working Group (ROPWG), Final Report 2018-03-15, Crash-Resistant Fuel System (CRFS)
- This report contains the ROPWG recommendations for incorporating CRFS regulations into newly manufactured rotorcraft that were certified before these regulations went into effect (legacy helicopters). These recommendations supersede the interim ROPWG proposals submitted on May 11, 2017.
Congressional Mandate
- As a direct result of this accident, and using the ROPWG recommendations, U.S. Congress mandated CRFS requirements through an operational requirement in U.S. airspace to include new manufacturing rotorcraft meet these ROPWG partial list of regulations.
- Codified by H.R. 302 – FAA Reauthorization Act of 2018, Section 317, Helicopter Fuel System Safety
- 49 USC 44737 (2018) Helicopter Fuel System Safety
FAA SAIBs and SAFO
- SAFO 16016, "Helicopter Stabilized Hover Checks Before Departure"
- SAIB: SW-17-23R2 (Fuel System) - SAIB advises registered owners and operators of certain Airbus Helicopters of FAA-approved STCs to install crash-resistant fuel systems that comply with the latest safety standards. This includes the Airbus AS350B3e.
- SW- 17-23R2 serves as a reminder of recommendation to add CRFSs
- SAIB: SW-17-31R2 (Fuel System) - notifies all registered helicopter owners and operators of helicopters that are either 1) fully compliant with the CRFS safety standards of 14 CFR Part 27 through Amendment 27-30 or Part 29 through Amendment 29-35 or 2) compliant with the requirements listed in 49 USC § 44737 (2018). The statutory requirement of 49 USC 44737 (2018) was established by the FAA Reauthorization Act of 2018 (H.R. 302, Pub.L. 115-254), Section 317, HELICOPTER FUEL SYSTEM SAFETY
- SAFO 19006, Crash Resistant Fuel System (CRFS) Safety Standards - seeks to inform registered owners and operators of helicopters about compliance standards for CRFSs
Emergency AD 2015-22-52 (superseded by 2015-22-53)
This AD was issued on 10/28/2015, prompted by the incident in Temple, Texas, and the accidents in Albuquerque, New Mexico and Frisco, Colorado. The yaw servo hydraulic check would be removed from preflight procedures and moved instead to postflight procedures. This was done to avoid takeoff without hydraulic pressure in the tail rotor hydraulic circuit, which could cause tail rotor control loss and, ultimately, complete control loss of the helicopter.
View: Emergency AD 2015-22-52
Emergency AD 2015-22-53
This AD was issued 10/30/2015, superseding AD 2015-22-52, to further clarify the requirements of the superseded AD. AD 2015-22-53 corrected terminology from the "collective switch" to the "ACCU TST" switch when referring to the yaw load compensator check. In addition, a method of recording compliance was omitted.
View: Emergency AD 2015-22-53
AD 2018-01-12 (which supersedes 2015-22-53)
This AD was issued on 2/20/2018, retaining the requirements of AD 2015-22-53 and also requiring installation of a timer relay for the yaw servo hydraulic switch, installing an additional light on the caution and warning panel, and replacing the bistable ACCU TST button with a monostable button. The requirements are intended to prevent takeoff without hydraulic pressure in the tail rotor (T/R) hydraulic system.
View: AD 2018-01-12 R1
Rotorcraft Life Cycle:
- Design / Manufacturing
Accident Threats:
- Loss of Control - Inflight (LOC-I)
- Fire / Smoke (POST-IMPACT) (F-POST)
Industries:
- Helicopter Air Ambulance
Accident Common Themes:
- Organizational Lapses
- Human Error
- Unintended Effects
Human Error
The failure of the pilot to follow the preflight procedure to return the yaw servo hydraulic switch to the "ON" position resulted in high control loads, eventually resulting in the loss of control of the helicopter.
A preflight hover check was not accomplished. Had the check been performed, the likelihood of the pilot recognizing the lost hydraulic assistance would have increased and could have led to a safe landing.
Organizational Lapses
Following issuance of OEM service bulletins which address shortcomings of the hydraulic test circuit and visual cues for status of that system, the operator was slow to distribute the OEM service bulletin to its bases. A lack of immediate communications regarding critical service bulletins and service announcements, as well as lack of adequate installation kits and parts from the OEM, can lead to delay in important design and safety improvements by an operator.
Robinson R22B, Helicopter Services, Inc., N281RG, Houston, Texas, September 10, 2012
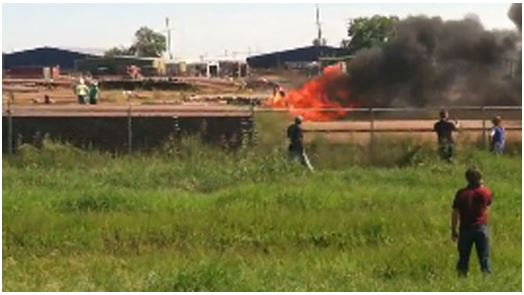
Source: Robinson Helicopter
On September 10, 2012, a Robinson R22B helicopter, N281RG, suffered substantial damage when it impacted terrain during a low-altitude maneuvering flight in Houston, Texas. The helicopter had departed Baytown Airport in Baytown, Texas at approximately 1500. A post-crash fire ensued. Both occupants were fatally injured.
The lack of fuel system crash resistance increased the risk of post-crash fire. In this accident, most likely non-survivable, the helicopter did not have a crash-resistant fuel system, nor was one required.
Eurocopter AS350B2, Helicopters, Incorporated, N250FB, Seattle, Washington, March 18, 2014
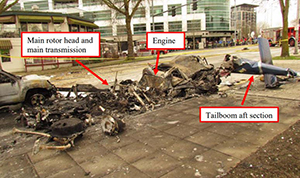
Source: NTSB
View Larger
The pilot was repositioning the helicopter from a rooftop helipad where it had just been refueled to a nearby airport. Video footage revealed that the helicopter lifted off of the helipad and simultaneously started to yaw to the left, consistent with a loss of tail rotor control. The helicopter completed one 360-degree rotation about the yaw (vertical) axis in a near level attitude while climbing. As it continued to rotate (spin) to the left, the helicopter deviated from a level attitude, pitching nose down and banking right, consistent with a loss of main rotor control. The helicopter moved away from the helipad, lost altitude, and impacted the street below. A post-crash fire erupted that consumed most of the fuselage and the forward section of the tail boom.
The NTSB determined the probable cause to be loss of hydraulic boost to the tail rotor system at takeoff, though the reason for the loss of hydraulic boost to the main and tail rotor controls could not be determined because of fire damage to hydraulic system components and the lack of a flight recording device.
NTSB Accident Report: WPR14FA137
Technical Related Lessons
Preflight check procedures that intentionally remove a critical flight system must have strong provisions to alert the pilot that the aircraft is restored for flight. These provisions include annunciations, such as visual and/or aural indications, in addition to the preflight check. (Threat Category: Loss of Control LOC-I)
- The preflight testing of the tail rotor hydraulic system circuit involves shutting off hydraulic power, then relieving the system pressure, and finally, reengagement of the yaw servo hydraulic switch. This system did not include any feedback to inform the pilot that hydraulic power had been removed from, or reengaged to, the tail rotor yaw control circuit.
- The accident pilot was put at higher risk for mistakes and accidents due to the lack of indication of hydraulic power for the critical yaw control system.
The risk of post-crash fires from fuel leaks in survivable crashes can be reduced through installation and utilization of crash-resistant fuel systems (CRFSs). CRFS design requirements increase safety in the event of a survivable crash by either decreasing the likelihood or delaying the onset of post-crash fires. (Threat Category: Fire/ Smoke Post-impact)
- The accident aircraft did not incorporate CRFS technology, nor was it required by date of application.
- Special Airworthiness Information Bulletin (SAIB) SW-17-31R2, Fuel System, notifies all registered owners and operators of helicopters, which are either fully compliant with the CRFS safety standards or compliant with the 2018 statutory requirement, to incorporate a CRFS design. The statute 49 USC 44737 (2018), effective April 5, 2020, applies to newly manufactured rotorcraft. In addition, the SAIB recommends that owners and operators pursue installation of fuel systems that improve the fuel system crash resistance capability of their helicopters.
Common Theme Related Lessons
Hover checks should be completed to ensure the helicopter is controllable. (Common Theme: Human Error)
- The AS350 rotorcraft flight manual (RFM) normal procedures section includes a hover check requirement to ensure controllability.
- In this accident, the lack of a hover check resulted in takeoff without hydraulic boost to the tail rotor control, resulting in extremely high pedal forces. A hover check likely would have provided the pilot an indication that the aircraft was not safe for flight.