Boeing B-737-800
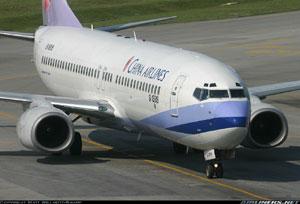
Photo copyright Matthew Taylor - used with permission
China Airlines Flight 120, B18616
Okinawa, Japan
August 20, 2007
On August 20, 2007, a Boeing 737-800 operated by China Airlines departed from Taiwan, Taoyuan International Airport on a regularly scheduled flight to Naha Airport, Okinawa, Japan. Following landing and leading-edge slat retraction, a failed portion of the slat track assembly was pressed through the slat track housing and penetrated the right main fuel tank, causing a fuel leak. At about 10:33 local time, fuel that had been leaking from the right-wing tank during taxi and parking was ignited by hot engine surfaces and/or hot brakes, resulting in the aircraft being engulfed in flames.
There were 165 passengers and crew on board, consisting of eight crewmembers and 157 passengers (including two infants). Everyone on board was evacuated from the aircraft with no casualties.
The aircraft was destroyed by the fire, leaving only part of the airframe intact.
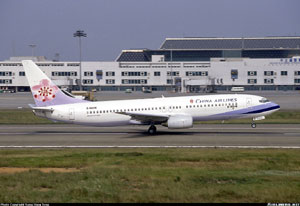
Photo copyright Sung-Yang Tong - used with permission
History of Flight
China Airlines Flight 120, a Boeing 737-800, departed on a regularly scheduled flight from Taiwan Taoyuan International Airport to Naha Airport, Okinawa, Japan. A normal approach and landing at Naha Airport was conducted, including deployment of the high lift system (leading edge slats and trailing edge flaps). The airplane landed uneventfully and began taxiing toward the designated gate. During taxi the slats were retracted. When the slats had fully retracted, fuel started leaking from the right main tank located at the No. 5 slat track housing (slat can). Leaking fuel initially flowed away from the airplane, carried by the airplane movement and engine exhaust. Once the plane stopped at Spot 41, fuel stopped flowing away from the wing and began dripping underneath the airplane in the vicinity of the right engine and brakes. Fuel was also pooling on the tarmac underneath the airplane.
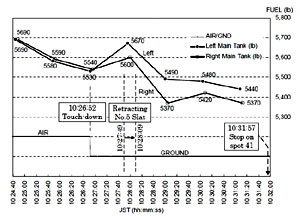
during fuel leak - landing and taxi
View Larger
Between the time of touchdown and parking, a time span of approximately five minutes, approximately 60 pounds of fuel leaked from the breached fuel tank. After stopping at Spot 41 (the designated gate), a significant quantity of fuel pooled beneath the wing. Approximately one minute after coming to a stop at Spot 41, fire broke out on the right side of the airplane. The ground crew alerted the flight crew to the fire. Approximately 35 seconds later, the captain notified the cabin crew of the fire, and evacuation was initiated approximately 30 seconds later.
An animation of the progression of the fire is available below:
Boeing 737 Leading Edge Slats
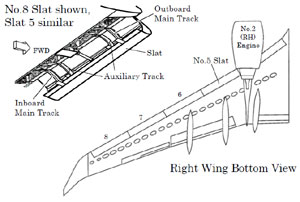
View Larger
The Boeing 737-800 employs leading edge slats, in combination with trailing edge flaps, to modify the lift and drag characteristics of the wing. The high lift system allows the wing to produce more lift and allows operation at slower speeds for takeoff and landing or to take off and land in shorter distances.
The 737-800 has four slats installed on the leading edge of each wing. They are identified sequentially starting at the left outboard slat and increasing in number across the airplane to the right outboard slat. The No. 5 slat is the most inboard slat on the right wing.
Each slat extends on two main and two auxiliary tracks. The two main tracks are guided between two sets of guide rollers installed in the leading edge of the wing in front of the forward spar. Each main track retracts through a hole in the wing forward spar into the slat can, which is formed from thin-walled aluminum and extends into the fuel tank. When the slats are fully retracted, the track assembly is stored inside the slat can. The slat can is inside the fuel tank and is normally immersed in fuel.
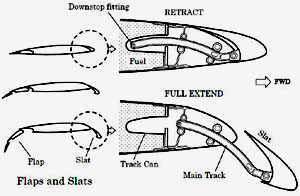
and retraction into slat can
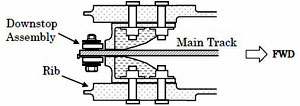
There is a downstop assembly at the aft end of each main track. The downstop assembly comes in contact with another downstop, installed internally on the wing leading edge. When the two downstops contact each other, the slat is fully extended.
The design of the bolt assembly in the downstop requires a washer. The pass-through hole in the downstop is larger than the bolt assembly. If the washer is missing, or if the nut is missing, the entire bolt assembly can pass through the downstop. The track can, which houses the retracted slat, is only large enough to accommodate the retracted slat track. Loose material, such as a disassembled downstop, can potentially be contacted by the slat track and pushed through the wall of the track can, causing a fuel tank breach.
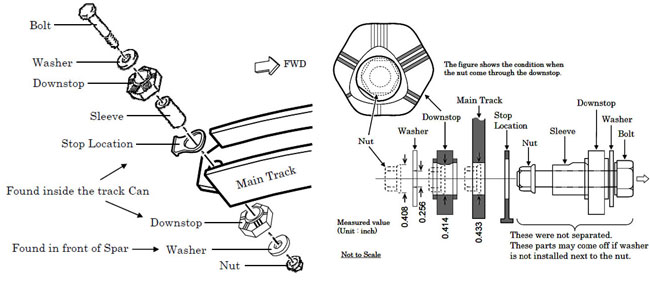
Buildup of downstop assembly and dimensions of components (right)
View Larger
Maintenance History
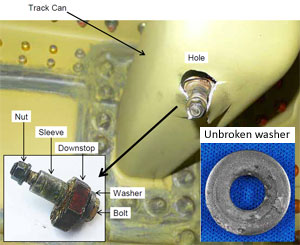
unbroken washer loose from the downstop assembly
View Larger
During the investigation, it was learned that, prior to December 2005, there had been two reported cases of detachment of the downstop assembly nut. In one of these cases, fuel was reported to have leaked from the track can for the number 5 slat. The cause of the fuel leak was determined to have been a hole punctured in the slat can by the nut, that had fallen off the track assembly into the track can, and then pushed through the track can by the slat track. As a result of these two reported incidents, Boeing issued Service Letter 737-SL-57-084, dated December 15, 2005, which recommended removal, inspection, and reinstallation of the bolt assembly, including application of thread locking compound, and tightening the nut with a torque of 50 to 80 inch-pounds.
The investigators determined that during maintenance activity carried out on July 6, 2007, to accomplish this service later, the washer had not been re-installed on the downstop assembly. Without this washer, the downstop assembly was able to fall out of the slat track. The downstop assembly then fell into the slat can, where it was later pushed through the slat can wall, initiating the fuel leak.
Investigators examined the No. 5 slat track can in the wreckage of China Airlines Flight 120. This area was preserved due to the progression of the fire. A complete downstop assembly, minus one washer, was found to have punctured the No. 5 track can. The washer was found loose in the leading edge of the wing. The dimensions of the downstop bolt are smaller than the downstop assembly through which the bolt passes. Without the washer, the bolt can come free from the downstop assembly.
Based on the failure mechanism, the Boeing Company made a change to the design of the downstop assembly following this accident. This change was implemented on new production aircraft of the applicable models beginning in August 2008. Boeing also released a service bulletin that provided operators with instructions to replace the existing downstop hardware with the new design.
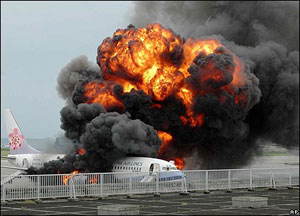
Fuel Auto-ignition
The auto-ignition temperature of a hydrocarbon fuel is the lowest temperature at which it will spontaneously ignite in a normal atmosphere without an external source of ignition or spark. This temperature for auto-ignition can vary depending on pressure and oxygen concentration.
Typically, this material property is tested per the American Society for Testing and Materials (ASTM) test method E659. This test method covers the determination of hot- and cool-flame auto-ignition temperatures of a liquid chemical in air at atmospheric pressure in a uniformly heated vessel. Per the material safety data sheet (MSDS) and ASTM E659, the auto-ignition temperature is 410°F for Jet-A fuel.
Investigators conducted tests on another 737-800 in order to determine the surface temperatures that would have been present on the accident airplane as the fuel was leaking, leading up to the fire. The following table represents temperatures that were recorded just after engine shutdown, following taxiing operations similar to that of China Airlines Flight 120.
Temperatures Measured for the Boeing 737-800 Engine
Area | Low Temp. (°F) | High Temp. (°F) |
---|---|---|
Exhaust Plug | 194 | 374 |
Outlet Guide Vane | 374 | 482 |
Exhaust Gas | 572 | 644 |
It was believed by the investigators that fuel exposure to these hot areas started the fire.
Fire and Emergency Evacuation
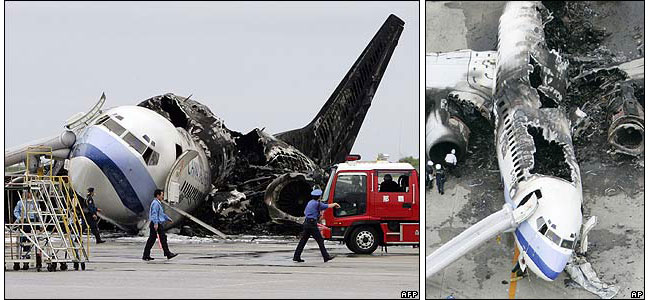
The leaking fuel caught fire a little over one minute after the airplane came to a stop at Spot 41. During this time the ground crew was aware of the leak and of the fuel fire when it started. They immediately contacted the captain, reporting the fire before there was any indication of fire in the cockpit.
One minute after the fire started (two minutes after engine shutdown), the captain instructed the cabin crew to prepare the passengers for evacuation. The passengers were still unaware of the situation, but once the engines had stopped, they were already gathering their personal items and were preparing to exit the airplane. After receiving the evacuation order, the crew informed the passengers that there was a fire, and their exit would be via the aircraft emergency slides. The ground crew, realizing the situation, was at the bottom of the slides to aid in evacuation of passengers. See video of China Airlines Flight 120 emergency evacuation and firefighting progress (Source: Sankei Newspaper, Japan).
All of the aircraft passengers exited the plane within two minutes following the evacuation order, and three minutes after the fire had started. There were no reported injuries or fatalities.
Firefighting operations were stopped, and the fire was declared "out" one hour after it had started. The airplane was completely destroyed.
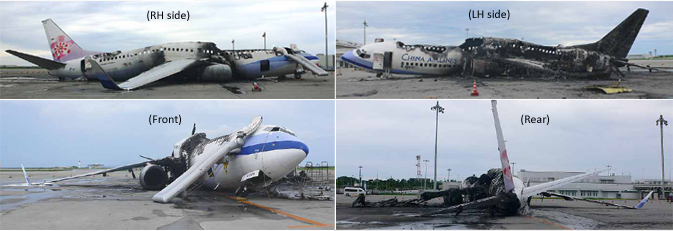
During the fire the right wing drooped and rested on the ground. This occurred approximately six minutes after the fire had started. As a result, the remaining fuel flowed to the wing tip, stopping the leak from the inboard No. 5 slat can area. The extinguishment by ground fire and rescue personnel extinguished the fire, preserving the right wing which housed the No. 5 slat can area. Investigators were thereby able to determine how the downstop assembly had been forced through the slat can wall, initiating the leak.
The accident was investigated by the Japan Transport Safety Board. The findings are contained in Section 3 of the accident report, entitled "Analysis" on pages 50 through 64. Twenty-one findings were issued.
The probable cause of the accident was determined by the safety board to be:
"It is considered highly probable that this accident occurred through the following causal chain: When the Aircraft retracted the slats after landing at Naha Airport, the track can that housed the inboard main track of the No. 5 slat on the right wing was punctured, creating a hole. Fuel leaked out through the hole, reaching the outside of the wing. A fire started when the leaked fuel came into contact with high-temperature areas on the right engine after the Aircraft stopped in its assigned spot, and the Aircraft burned out after several explosions. With regard to the cause of the puncture in the track can, it is certain that the downstop assembly having detached from the aft end of the above-mentioned inboard main track fell off into the track can, and when the slat was retracted, the assembly was pressed by the track against the track can and punctured it. With regard to the cause of the detachment of the downstop assembly, it is considered highly probable that during the maintenance works for preventing the nut from loosening, which the Company carried out on the downstop assembly about one and a half months prior to the accident based on the Service Letter from the manufacturer of the Aircraft, the washer on the nut side of the assembly fell off, following which the downstop on the nut side of the assembly fell off and then the downstop assembly eventually fell off the track. It is considered highly probable that a factor contributing to the detachment of the downstop assembly was the design of the downstop assembly, which was unable to prevent the assembly from falling off if the washer is not installed. With regard to the detachment of the washer, it is considered probable that the following factors contributed to this: Despite the fact that the nut was in a location difficult to access during the maintenance works, neither the manufacturer of the Aircraft nor the Company had paid sufficient attention to this when preparing the Service Letter and Engineering Order job card, respectively. Also, neither the maintenance operator nor the job supervisor reported the difficulty of the job to the one who had ordered the job."
The complete accident report can be accessed at the following link: (Accident Report)
The Japan Transport Safety Board made two recommendations:
Preparation of Maintenance Job Instructions
The Japan Transport Safety Board recommends the Federal Aviation Administration of the United States of America to supervise the Boeing Company, the manufacturer of the aircraft, to take the following actions: When preparing maintenance job instructions for airlines such as Service Letters/Bulletins, the scopes of jobs should be clearly defined and the working conditions and environments including accessibilities to job areas should be appropriately evaluated in order to prevent maintenance errors.
Planning and Implementation of Maintenance Jobs
The Japan Transport Safety Board recommends the Civil Aeronautics Administration of Taiwan to supervise China Airlines to take the following actions: When planning and implementing maintenance jobs, the scopes of jobs should be fully ascertained, and the working conditions and environments should be appropriately evaluated. Additionally, the countermeasures to prevent maintenance errors, including the actions taken in 2009 against the recurrence of this accident, should be steadfastly implemented and enhanced.
14 CFR 25.803 Emergency Evacuation
14 CFR 25 Appendix J Emergency Evacuation
14 CFR 25.863 Flammable Fluid Fire Protection
14 CFR 25.901 Powerplant Installation
14 CFR 25.963 Fuel Tanks: General
14 CFR 25.1529 Appendix H Instructions for Continued Airworthiness
The first reported track can puncture was on September 15, 2005. This fuel leak came from the wing leading edge area at the inboard end of the No. 5 leading edge slat. The hole created in this incident was small which caused a low-rate fuel leak. This leak then dripped onto the engine exhaust nozzle but did not cause a fuel fire. The incident was determined to be a result of loose hardware (a nut) falling into the track can and puncturing it during the slat's retraction. However, unlike China Airlines Flight 120, there had been no maintenance actions performed on the No. 5 slat can area that would have contributed to this incident.
When this first incident happened, there was one reported fuel tank puncture, in the entire fleet history of approximately 10 million hours. In this fuel tank puncture the nut had fallen into the track can and punctured it when the slats were retracted. The nut only caused a small leak which dripped on the aircraft engine and did not catch fire. The risk was thought to be low based on the fleet data and the leak being so small.
The China Airlines Flight 120 fire was on August 20, 2007. Five days later on August 25th, the FAA released emergency airworthiness directive (AD) 2007-18-51. This AD required inspection on each main slat track downstop assembly to verify proper installation of the slat track hardware. It also required that a torque between 50 to 80 inch-pounds be applied to the nut. A compliance time of 24 days was given.
After this AD was issued, there were additional reports of parts coming off the main slat track downstop assemblies. In these cases, the parts were found in the bottom of the slat track housing. There was also one case where the track can itself was damaged. Previously there were three reported incidents. Two of these previously reported incidents (including China Airlines Flight 120) had damaged the track can. Based on this new information, AD 2007-18-52 was released. This AD reduced the compliance time to ten days.
Originally, the assumption was made that with one reported incident in over ten million flight hours of operation that this was an isolated event. Based on this assumption, the true scope of the problem was not fully understood. A complete understanding of the issue, and the risks associated with the slat track failure, only occurred after the fire of China Airlines Flight 120.
- A fuel tank breach, caused by a failed downstop assembly being pushed through the No. 5 slat can, which led to a fuel leak and subsequent fire that destroyed the airplane.
- The downstop assembly would not fail such that parts of the downstop could be forced through the slat can wall and create a fuel leak.
- A previous slat can failure and resultant fuel leak was believed to have been an isolated event.
- A small fuel leak associated with a fuel tank breach does not pose a significant fire hazard.
Prior to the accident there were two reported incidents of slat can damage and/or fuel leaks involving slat track hardware coming loose. One of these incidents included fuel leakage from the No. 5 slat. The fuel leak was caused by a loose nut that had fallen into the track can. The nut remained loose in the track can for an undetermined length of time. Eventually the main track pushed the nut through the track can wall, puncturing the fuel tank. The leak was small and did not lead to an aircraft fire.
After AD 2007-18-51 was released, additional incidents of parts coming off the main slat track downstop assemblies were discovered. This led to a superseding of the original AD and a reduction in the compliance time from 24 days to ten days in AD 2007-18-52.
Boeing 737
Slat Track Hardware
AD 2007-18-51 This emergency AD, issued on August 25, 2007, required all U.S. operators of Boeing 737-600/700/700C/800/900/900ER to perform a detailed inspection to verify proper installation of the slat track hardware (the bolt, washers, downstops, sleeve, stop location and nut) and the inside of the slat can. The compliance time was within 24 days after receipt of the AD.
AD 2007-18-52 This AD superseded AD 2007-18-51 and was issued on August 28, 2007. The compliance time was reduced to ten days from the receipt of the AD based on additional reports of parts coming off the main slat track downstop assemblies. AD 2007-18-52 required a detailed inspection or a bore scope inspection of each main slat track downstop assembly to verify proper installation of the slat track hardware and the inside of the slat can.
AD 2011-06-05 This AD, issued on April 26, 2011, supersedes AD 2007-18-52, Amendment 39-15197. The AD applies to all Model 737-600/700/700C/ 800/900/900ER series airplanes. This AD includes a requirement for replacing the hardware of the downstop assembly with new hardware, doing a detailed inspection or a borescope inspection of the slat cans on each wing and the lower rail of the slat main tracks for debris, replacing the bolts of the aft side guide with new bolts, and removing any debris found in the slat can.
Fuel Drainage Paths
AD 2013-08-18 This AD, effective June 5, 2013, is for certain Boeing Model 737-600/700/700C/ 800/900/900ER series airplanes. This AD required modifying the fluid drain path in the wing leading edge area, forward of the wing front spar, and doing all applicable related investigative and corrective actions; and installing new seal disks on the latches in the fuel shutoff valve access door.
Boeing 757
Slat Track Hardware
AD 2010-23-13 This AD required changing the lower, fixed leading edge panel assemblies immediately outboard of the nacelles at slats 4 and 7.
Fuel Drainage Paths
AD 2013-03-20 This AD required a detailed inspection of the inboard and outboard main slat track downstop assemblies and a torque application to the main track downstop assembly nuts of slat numbers 1 through 10, excluding the outboard track of slats 1 and 10; a detailed inspection of all slat track housings for foreign object debris (FOD) and visible damage; and corrective actions, if necessary.
Boeing 767
Slat Track Hardware
AD 2011-03-15 This AD required a detailed inspection for correct main track downstop assembly, thread protrusion, and damaged and missing parts of the main track downstop assemblies of the outboard slats and related investigative and corrective actions if necessary. This AD also required a detailed inspection for foreign objects, debris and damage to the wall of the track housing of the outboard slats, and corrective actions, if necessary.
AD 2011-12-11 This AD, which supersedes AD 2001-03-15, required replacing the drain tube assemblies. For certain airplanes, this new AD also requires installing an additional electrostatic bond path for the number 5 and 8 inboard slat track drain tube assemblies. For certain other airplanes, this new AD also requires reworking the bonding jumper assembly. This new AD also revises the applicability to include additional airplanes.
Fuel Drainage Paths
AD 2012-21-02 This AD applies certain Boeing Model 767-200/300/300F/400ER series airplanes. This AD requires modification of the fluid drain path in the leading-edge area of the wing.
Boeing 777
Slat Track Hardware
AD 2010-14-13 This AD requires inspecting the bolt, nut, and downstop of the slat track assembly to determine if the bolt, nut, or stops are missing and to determine if the thread protrusion of the bolt from the nut is within specified limits and parts are correctly installed and related investigative and corrective actions if necessary. For certain airplanes, this AD also requires inspecting the slat cans at the outboard slat number 3 and 12 outboard main track locations for holes and wear damage, and corrective actions if necessary; and replacing the downstop hardware for the outboard slats number 3 and 12 outboard and inboard main track locations.
Airplane Life Cycle:
- Design / Manufacturing
- Maintenance / Repair / Alteration
Accident Threat Categories:
- Uncontrolled Fire / Smoke
- Cabin Safety / Hazardous Cargo
- Lack of System Isolation / Segregation
Groupings:
- Approach and Landing
Accident Common Themes:
- Human Error
- Flawed Assumptions
- Unintended Effects
Human Error
As a result of service letter related maintenance activity, a slat downstop was incorrectly reassembled. The assembly error led to the failure of the downstop assembly and its migration out of the slat track. The downstop fell out of the slat track and into the slat can where it was eventually pushed through the wall of the slat can. The reassembly error, which omitted the reinstallation of a washer, led to the fuel tank breach and fire.
Flawed Assumptions
Prior to this accident, there had been at least two reported incidents involving failures of the downstop assembly, one of the failures resulted in a minor fuel leak. The investigation believed that at the time of the failure reporting, the one reported fuel leak was an isolated event. Following the accident, a number of other events were reported that had been previously unreported, leading to the conclusion that the early fuel leak was not an isolated event and that the threat to the airplane fleet was larger than had originally been believed.
Unintended Effects
Prior to the accident there had been two reports of nuts falling off of downstop assemblies within the 737 fleet that lead to downstop failures. As a result of the nut failures, a service letter was issued. The letter recommended disassembly, inspection and reassembly of the downstop, paying particular attention to the proper reinstallation of the nut securing the downstop hardware to the downstop bolt. On the accident airplane, during downstop reassembly following inspection, a washer was omitted, initiating the accident sequence of events. The recommended actions mitigated a problem that had been discovered on multiple 737 aircraft, but due to the misassembly of the slat downstop following these inspections, another error was experienced which resulted in the loss of Flight 120.
The accidents listed below all involved fuel tank breaches, or fuel line failures, followed by a landing or rejected takeoff. While this listing is not comprehensive, the accidents below have been selected in order to underscore the ground fire hazards associated with fuel tank breaches or fuel line failures with massive, unrestricted fuel leakage in the vicinity of ignition sources such as engine tailpipes or hot brakes.
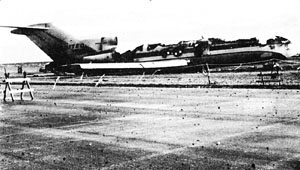
United Airlines Flight 227, Salt Lake City Municipal Airport, Salt Lake City, Utah, November 11, 1965, Boeing 727-200
During an attempted landing at Salt Lake Municipal Airport, the pilot was unable to arrest an excessive sink rate during the approach. The airplane touched down with a very high vertical speed approximately 335 feet short of the runway. The main landing gear failed, severing fuel lines and electrical cables within the fuselage, which resulted in a massive fuel leak and fire. Of the 91 passengers and crew on board, there were 43 fatalities, which were all determined to be due to the effects of the fire.
See accident module
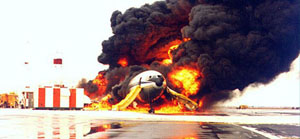
Overseas National Airlines Flight 32, John F. Kennedy International Airport, New York, November 12, 1975, McDonnell-Douglas DC-10-30
During takeoff roll, the right engine experienced an uncontained failure resulting in a fuel-fed fire in the engine. The takeoff was aborted but the airplane overran the runway and burned, largely due to pooled fuel around the airplane. All passengers and crew successfully evacuated the airplane and there were no fatalities.
See accident module
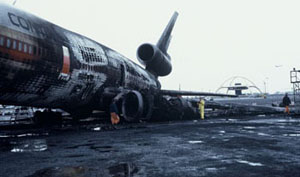
and resulting ground fire
Continental Airlines Flight 603, Los Angeles International Airport, Los Angeles, California, March 1, 1978, McDonnell Douglas DC-10-10
During the takeoff roll, three main landing gear tires on Flight 603 failed, prompting the captain to initiate a takeoff abort. The speed that Flight 603 had reached at the time of the tire failures was very near V1. A combination of the wet runway and multiple tire failures resulted in the airplane sliding off the end of the runway, causing failure of the main landing gear, tank penetration, and a fuel leak from the left side of the airplane. The leaking fuel was ignited by hot surfaces from the engines, brakes, or other areas of the aircraft. The resulting fire consumed much of the airplane. Of the 184 passengers and 14 crew, there were two fatalities, and several serious injuries.
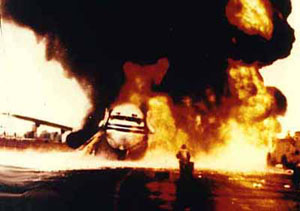
Pacific Western Flight 501, Calgary International Airport, Canada, March 22, 1984, Boeing Model 737-275
At approximately 70 knots during the takeoff roll, the compressor section of the left engine failed. Debris from the failed engine exited the engine case and penetrated the airplane, including the left-wing main fuel tank. The flight crew aborted the takeoff and stopped the airplane on a taxiway adjacent to the runway. Leaking fuel from the left wing immediately ignited and engulfed the left side of the airplane in flames. All passengers and crew successfully evacuated the burning airplane, although there were several serious injuries.
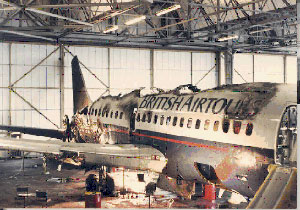
British Air Tours Flight KT28M, Manchester International Airport, United Kingdom, August 22, 1985, Boeing Model 737-236
During takeoff roll, debris from an uncontained engine failure struck and penetrated the left-wing fuel tank access panel. Failure of this panel resulted in a massive fuel leak which was ignited by the left engine. A successful RTO was conducted, and the airplane exited the runway and parked on a taxiway. Once parked, the fire spread to the airplane where it was totally destroyed. Fifty-five passengers died in the fire.
See accident module
Technical Related Lessons
Unrestricted fuel leaks during ground operation (taxi, takeoff, and landing), particularly those resulting from a fuel tank breach, pose an extreme hazard to the aircraft and occupants. (Threat Category: Uncontrolled Fire)
-
Following landing and during taxi, investigators concluded that the fuel leak began as a result of slat retraction. During taxi the fuel was dispersed away from the airplane due to the engine exhaust. Once the airplane was stationary at the gate, and engines shutdown, fuel was able to collect underneath the airplane and poured onto the hot engine tailpipe and/or the hot brakes. The leaking fuel ignited, and the fire consumed the airplane.
Expedited initiation of emergency evacuation, in cases where a fuel tank breach has occurred, is critical to achieving a successful passenger evacuation. (Threat Category: Cabin Safety/Hazardous Cargo)
-
Ground personnel witnessed the initiation of the fire and immediately notified the flight crew that a fire was progressing underneath the airplane. The captain ordered an evacuation less than one minute from the start of the fire, which progressed as soon as his order was given. The airplane was evacuated in approximately two minutes with no injuries to passengers or crew. The successful evacuation was the result of an expedited order, followed by an organized, timely execution of the evacuation process.
Airplane designs, and associated maintenance procedures, should be sufficiently robust in order to reduce the risks associated with expected human errors in manufacturing, assembly, or prescribed maintenance. (Threat Category: Lack of System Isolation/Segregation)
-
In this accident, investigators concluded that a single washer was omitted during reassembly of the slat downstop following maintenance in that area of the leading-edge slat. The washer is intended to prevent the downstop assembly from migrating out of the slat track. The dimensions of the downstop bolt are smaller than the downstop assembly through which the bolt passes. Without the washer, the bolt can come free from the downstop assembly and fall out of the slat track. At some point following maintenance, as a result of the missing washer, the downstop assembly migrated out of the slat track and fell into the slat can, where it was subsequently pushed through the bottom of the slat can, breaching the fuel tank. This single maintenance error led to a potentially catastrophic ground fire.
Common Theme Related Lessons
Proper execution of maintenance activities, including disassembly, inspection, and reassembly, is critical in order to preserve safe airplane operation. (Common Theme: Human Error)
-
Approximately one month prior to the accident, maintenance had been performed on the No. 5 slat can as part of compliance with a Boeing Service Letter. The investigation determined that during reassembly of the slat downstop, a washer was not reinstalled. Without the washer, the downstop assembly was eventually able to fall out of the slat track. The downstop assembly fell into the slat can where it was pushed through the wall of the slat can, creating a fuel tank breach and subsequently a fire.