McDonnell Douglas DC-9
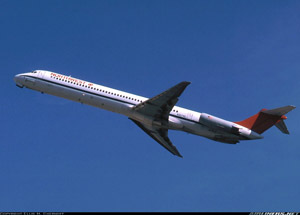
Photo copyright Ellis M. Chernoff - used with permission
Northwest Airlines Flight 255, N312RC
Detroit, Michigan
August 16, 1987
Northwest Airlines, Inc., Flight 255, a McDonnell Douglas DC-9-82, was a regularly scheduled passenger flight en route from the Detroit Metropolitan Wayne County Airport, Romulus, Michigan to Phoenix, Arizona. At approximately 2046 on August 16, 1987, Flight 255 crashed shortly after taking off from runway 3 C. According to witnesses, the airplane began its takeoff rotation about 1,200 to 1,500 feet from the end of the runway and lifted off near the end of the runway. After liftoff, the airplane rolled to the left, rolled to the right, and then collided with obstacles northeast of the runway when the left wing struck a light pole located 2,760 feet beyond the end of the runway. Thereafter, the airplane struck other light poles, the roof of a rental car facility, and then the ground. The airplane broke up as it slid across the ground, and post-impact fires erupted along the wreckage path. Three occupied vehicles on a road adjacent to the airport and numerous vacant vehicles in a rental car parking lot were destroyed. All six crewmembers and 148 passengers were killed; 1 passenger, a 4-year-old child, was seriously injured. On the ground, two persons were killed, one person was seriously injured, and four persons suffered minor injuries.
The National Transportation Safety Board (NTSB) determined that the probable cause of the accident was the flight crew's failure to use the taxi checklist to ensure that the flaps and slats were extended for takeoff. Contributing to the accident was the absence of electrical power to the airplane's takeoff warning system, which failed to warn the flight crew that the airplane was not configured properly for takeoff. The reason for the absence of electrical power could not be determined.
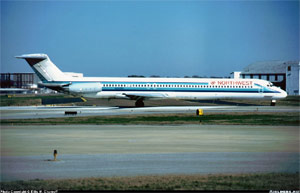
Photo copyright Ellis M. Chernoff - used with permission
Preface
On August 12, 1986, approximately one year prior to flight 255's accident, Northwest Airlines completed its purchase of Republic Airlines. At the time of the accident, and although the former Republic and Northwest personnel and equipment operated under the name of Northwest Airlines, both operated as separate entities with separate operating specifications.
Northwest Airlines did not operate any DC-9 series airplanes, but acquired a fleet of 134 DC-9 series airplanes during the merger. Flight crews remained segregated and operated in accordance with their former company procedures. The flight crew of Flight 255, formerly employed by Republic Airlines, became employees of Northwest Airlines as a result of the merger.
Photos of the accident airplane and sister airplanes in this overview depict various states of livery transition. Some are shown with a simple airline name change, while others can be seen in a more advanced state of transition.
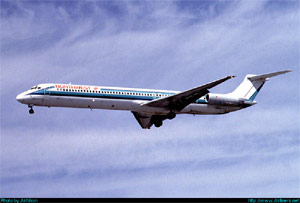
Photo copyright AirNikon Collection - Pima Air Museum - used with permission
History of the Flight
Northwest Airlines Flight 255 was a regularly scheduled passenger flight from Saginaw, Michigan, to Santa Ana, California, with intermediate stops in Detroit, Michigan, and Phoenix, Arizona. On August 16, 1987, the accident flight crew picked up the accident airplane, a McDonnell Douglas DC-9-82, in Minneapolis, Minnesota. The airplane departed Minneapolis as Northwest flight 750 to Saginaw with an intermediate stop at the Detroit Metropolitan Wayne County Airport (Detroit-Metro) in Romulus, Michigan. At about 1853 the airplane departed Saginaw as Flight 255 and made an uneventful flight back to Detroit-Metro.
With 149 passengers and 6 crew members aboard, Flight 255 pushed back from its Detroit-Metro gate at about 2032 for the next flight segment to Phoenix. During push back, the flight crew completed the BEFORE START checklist. After starting both engines, Flight 255 was cleared by the west ground controller to taxi via the ramp, hold short of taxiway Delta, and expect runway 3 Center (3C) for takeoff. About a minute later, the west ground controller cleared Flight 255 to continue taxiing, exit the ramp at taxiway Charlie, taxi to runway 3C, then contact the east ground controller on a new radio frequency. The first officer repeated the taxi clearance, but did not acknowledge the new radio frequency.
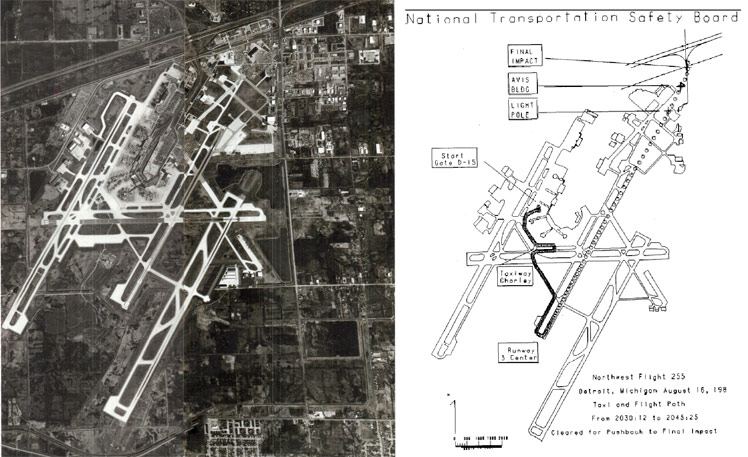
Right: NTSB diagram showing Flight 255's taxi route and takeoff path
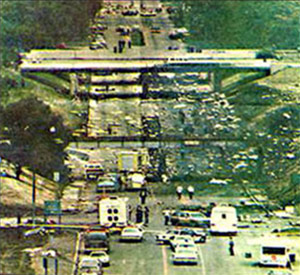
While taxiing, the captain missed the turn at taxiway Charlie. The first officer contacted the west ground controller, who redirected the airplane to taxi to runway 3C and again requested that Flight 255 contact the east ground controller on the new radio frequency. Upon contact with the east ground controller, Flight 255 received a new taxi route to runway 3C, the current altimeter setting, and notification that windshear alerts were in effect.
During taxi to runway 3C, the captain asked the first officer if runway 3C could be used for takeoff because the dispatch package received by the flight crew prior to leaving the gate was based on using either runway 21 Left (21L) or 21 Right (21R). Just prior to Flight 255's push back from the gate, the Detroit-Metro tower supervisor began coordination to change the active runway configuration from runway 21 to runway 3 due to a shift in wind direction. The Automatic Terminal Information Service (ATIS) broadcast, which was recorded approximately six minutes prior to Flight 255's push back, indicated that the ambfient temperature was 88° F and that the wind was from 300° at 17 knots. Using the ATIS information and Northwest's Runway Takeoff Weight Chart Manual, the first officer determined that, for the current ambient temperature and for an 11° takeoff flap setting, the maximum allowable weight to use runway 3C was between 145,100 pounds and 147,500 pounds. Since Flight 255's final takeoff weight was 144,047 pounds, the first officer told the captain that runway 3C could be used for takeoff. Flight 255 completed its taxi to runway 3C and, at about 2044, was cleared for takeoff.
According to information extracted from the Cockpit Voice Recorder (CVR), engine power began increasing at 2044:21. The flight crew could not engage the autothrottle during the early part of the takeoff roll, but engaged it prior to the airplane reaching a speed of 100 knots. The first officer called "100 knots" and approximately 12 seconds later called "rotate." At 2045:05, about 6 seconds after the "rotate" call, the CVR recorded the activation of the stall warning stick shaker. The sounds of the stick shaker continued until the CVR recording ended.
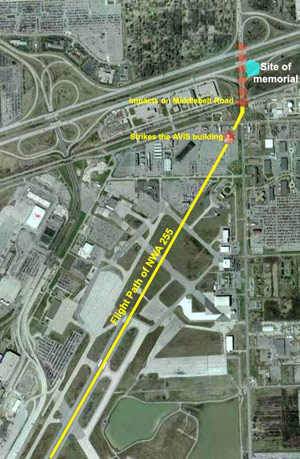
Photo courtesy of DTW Airport Archives
Starting at approximately 2045:09 and over the next eight seconds at about 2.5 second intervals, the aural tone and voice warnings of the supplemental stall recognition system (SSRS) activated. From 2044:01, just prior to takeoff clearance, to 2045:05, when the sounds of the stick shaker commenced, the CVR did not record any sounds of the takeoff warning system (TOWS). Activation of the TOWS during this portion of the takeoff sequence would indicate that the airplane was not properly configured for takeoff.
According to the NTSB report, witnesses indicated that Flight 255's takeoff roll was longer than that normally made by similar airplanes. Witnesses stated that Flight 255 began its rotation about 1,200 to 1,500 feet from the departure end of the runway, rotated to a higher pitch angle than other DC-9s, and that the tail came close to striking the runway.
After Flight 255 became airborne it began rolling left and right. Witnesses estimated that the bank angles during the rolls varied from 15° to 90°. Some witnesses stated that the wings leveled briefly and then banked to the left just before the left wing collided with a light pole in a rental car lot. The collision sheared off a 17-foot section of the outboard left wing.
After impacting the light pole, Flight 255 continued to roll to the left, continued across the rental car lot, struck a light pole in a second rental car lot, and struck the side wall of the roof of the rental car facility in the second rental car lot. Witnesses stated that the airplane was in a 90° left-wing-down attitude when it struck the roof, and that it continued rolling and was still rolling to the left when the airplane impacted the ground on a road outside the airport boundary.
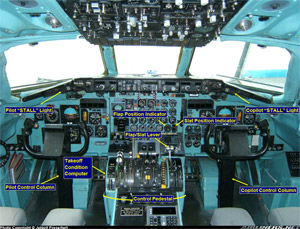
Photo copyright Jakkrit Prasertwit - used with permission
View Larger
The airplane continued to slide across the road, struck a railroad embankment, and disintegrated as it slid along the ground. Fires erupted in the airplane components scattered along the wreckage path. Three occupied vehicles on the road and numerous vacant vehicles in the auto rental parking lot along the airplane's path were destroyed by impact forces and/or fire. All 6 crewmembers and 148 passengers were killed; 1 passenger, a 4-year-old child, was seriously injured. On the ground, two persons were killed, one person was seriously injured, and four persons suffered minor injuries.
DC-9-82 Systems and Components
Airplane Overview
The DC-9-82 is a two-crew, twin-engine transport category airplane powered by two Pratt & Whitney JT8D turbofan engines. The photo to the left shows a typical flight deck, and is annotated to point out the controls and indicators pertinent to this accident. All flight control surfaces are depicted in the accompanying sketch. Ailerons and elevator are positioned by control tabs that are manually operated by the pilot and copilot using the control wheels and control columns. Normally, the rudder is hydraulically powered, but there is a manual reversion mode in which the rudder, like the ailerons and elevator, is positioned by the movement of a control tab.
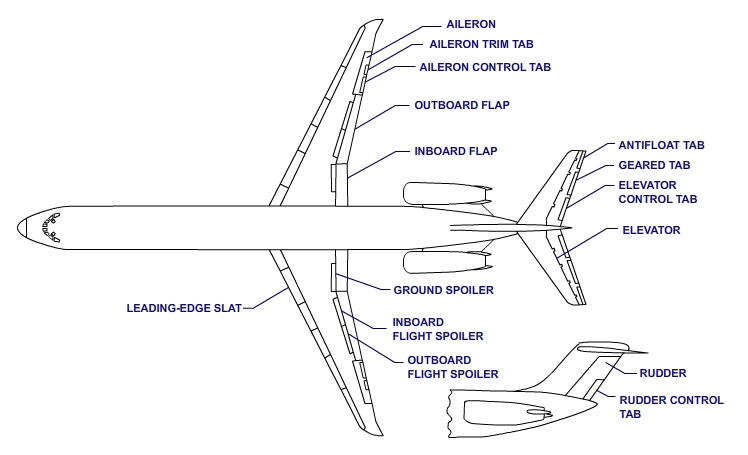
High Lift Devices
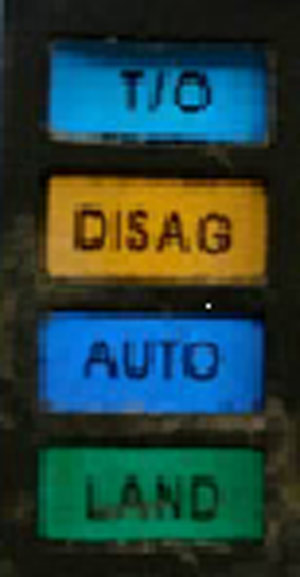
Photo from CIAIAC report on crash of Spanair Flight 5022.
The DC-9-82 wing is equipped with two high lift devices; leading edge slats and trailing edge flaps. When extended, each of these devices increases the wing's ability to produce lift. The increased lift capability allows the airplane, at a given weight, to fly slower while maintaining the required safety margins above stalling speed. Slower speeds result in minimized takeoff and landing distances. The DC-9-82 is required by its operating limitations to takeoff with, at a minimum, the leading edge slats extended.
Leading Edge Slats
The slats are wing lift augmentation devices located on the leading edge of the wing. The flight crew positions the slats in one of three positions by moving the flap/slat lever that is located on the right side of the control pedestal. The slats are positioned to the retracted position when the flap/slat lever is moved to the detent labeled UP/RET. The slats extend to the mid position when the flap/slat lever is moved to a detent that indicates a flap setting from 0° up to but not including 15°. The slats deploy to the fully extended position when the flap/slat lever is moved to a flap setting of 15° or more.
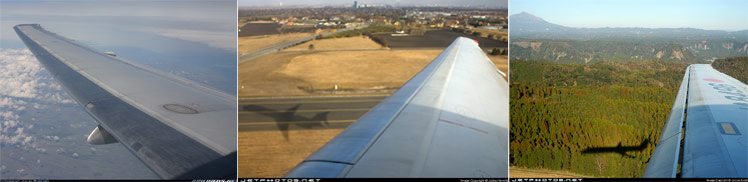
Center: Slats in mid position. Photo copyright Jukka Hemila - used with permission
Slats in extended position. Photo copyright James Scott - used with permission
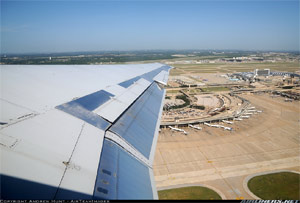
Used with permission - Andrew Hunt - AirteamImages.
Slat position is indicated by four slat advisory lights located forward of the flap/slat lever on the lower center instrument panel. When the flap/slat lever and the slats are configured for takeoff, the blue takeoff (T/O) light will illuminate. The amber disagree (DISAG) light illuminates when the position of the flap/slat lever disagrees with the position of the slats. The autoslat extension (AUTO) light illuminates when the slats are repositioned by the autoslat extension system. The land (LAND) light illuminates when the slats are configured for landing. None of the advisory lights illuminate when the slats are in the retracted position.
Trailing Edge Flaps
The flaps are wing lift augmentation devices located on the trailing edge of the wing. The flap system consists of an inboard and an outboard segment. Flap positions are designated in degrees. The flight crew sets the flaps to one of six fixed-detent positions by movement of the flap/slat lever. If optimized takeoff performance is desired, a movable or "dial-a-flap" detent allows the flight crew to position the flaps anywhere within the takeoff range. The movable detent is positioned by a thumbwheel located on the control pedestal to the right of the flap/slat lever.
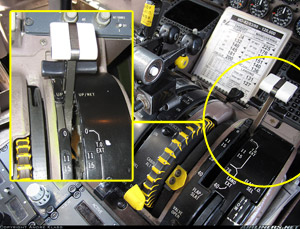
Photo copyright Andre Klass - Used with permission
Flap position is shown on an indicator located forward of the flap/slat lever on the lower center instrument panel. The flap position indicator dial is graduated in degrees of flap travel. The flap position indication corresponds to actual flap position, not flap/slat lever position.
The NTSB investigation concluded that Flight 255's flight crew did not properly configure the airplane for takeoff. Evidence examined by the NTSB indicated that, on takeoff, the flap/slat lever was in the up/retracted (UP/RET) position, the "dial-a-flap" thumbwheel was in the stowed position, the slats were fully retracted, and the flaps were in the full up or 0° position.
Takeoff Condition Computer
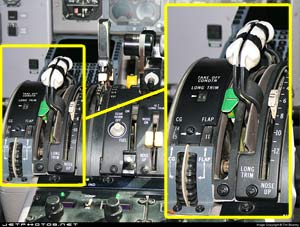
Photo copyright Tim Bowrey - Used with permission
The Takeoff Condition Computer (TCC) mechanically calculates the airplane's horizontal stabilizer trim setting for takeoff. The TCC is located on the left side of the control pedestal. The stabilizer trim setting is determined by entering into the computer the calculated takeoff center of gravity (c.g.) and the desired flap setting. The flight crew enters the two values by rotating thumbwheels until the appropriate c.g. and flap setting appear in their respective readout windows. The flap setting entered into the TCC is used as the reference value by the Takeoff Warning System to determine if the flaps are set for takeoff. The stabilizer setting's numeric value will appear in the takeoff condition longitudinal trim window.
The TCC also positions the longitudinal trim takeoff position ("green band") indicator to the same value contained in the TCC's longitudinal trim window. The flight crew manually sets the stabilizer to the takeoff setting by moving the stabilizer until the longitudinal trim indicator is aligned with the "green band" indicator.
Results of the Investigation: The NTSB's investigation revealed that, based on the airplane's final weight tabulation and the information contained in Northwest's dispatch papers, Flight 255's takeoff weight was 144,047 pounds and the flap and slat settings to be used for takeoff were 11° and mid position, respectively. The position of the TCC flap setting thumbwheel further corroborated the intended 11° takeoff flap setting.
Central Aural Warning System
The central aural warning system (CAWS) provides distinctive aural and vocal annunciations when potentially unsafe operating conditions, unsafe airplane configurations, or system malfunctions exist. Aural annunciations include horn, "C"-chord, chime, and bell sounds. Vocal annunciations are electronically-generated system identification words. The warning sequence begins with a 1-second aural annunciation followed by a 1-second voice message. This sequence is repeated for the duration of the warning period.
Electric power for each CAWS warning is provided by one of three power supplies within the CAWS unit. Except for the Supplemental Stall Recognition System (SSRS), there is no redundancy, and the failure of a power supply will result in the loss of its associated warnings. With respect to Flight 255's accident, power supply 2 and power supply 3 are of interest.
CAWS power supply 2 receives power from the left 28V dc bus, and powers the SSRS-1, Takeoff, Landing Gear, Autopilot Disconnect, Cabin Altitude, and Speed Brake warnings. On the accident airplane, CAWS power supply 2 was protected by a 3 amp circuit breaker at location P-40 in the lower electrical power center circuit breaker panel behind the captain's seat. CAWS power supply 3 receives power from the right 28V dc bus, and powers the SSRS-2 and Altitude Alert warnings.
Results of the Investigation: The NTSB recovered the accident airplane's CAWS unit from the wreckage, and noted that, except for a dent in the top left corner of the dust cover, the unit was undamaged. The NTSB examined the unit, verified it operated properly, and tested it on another Northwest Airlines DC-9-82. All takeoff warning functions were tested repeatedly and no discrepancies were found. The stall warning, fire warning, and stabilizer-in-motion horn were also tested repeatedly, and no defects were noted.
P-40 Circuit Breaker
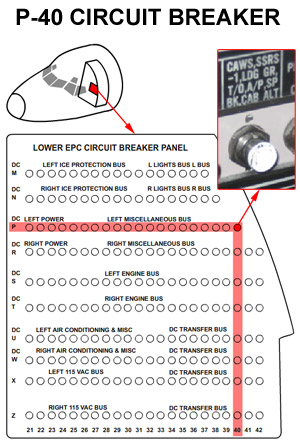
During the NTSB's examination of the wreckage, the P-40 circuit breaker was found broken free of the circuit breaker panel and the electrical bus, but both of its circuit wires remained attached to the remnant of circuit breaker by the terminal hardware. The bus terminal had broken free from the breaker housing and remained attached to the left 28V dc bus. The wiring between the breaker and the CAWS rack was intact and undamaged. The P-40 circuit breaker was taken to the NTSB's materials laboratory for further examination. Results of the examination and testing of 19 additional CAWS circuit breakers removed from Northwest's DC-9-82 fleet revealed that it was possible for the circuit breaker to be closed, but not conduct current.
Because the P-40 circuit breaker was badly damaged during the accident, it was impossible for the NTSB to determine positively its pre-impact condition. The NTSB postulated three possible conditions that would have caused power to be interrupted at the P-40 circuit breaker:
- The circuit breaker was intentionally opened by either the flight crew or maintenance personnel,
- The circuit breaker tripped because of a transient overload and the flight crew did not detect the open circuit breaker, or
- The circuit breaker did not allow current to flow to the CAWS power supply and did not annunciate the condition by tripping.
First, the NTSB considered the possibility that CAWS power supply 2 was disabled by operating the P-40 circuit breaker as a switch and opened intentionally. This might occur if any of the warnings operated by power supply 2 were producing nuisance warnings that annoyed or distracted the flight crew. However, no nuisance warnings were recorded by the CVR during a 30-minute period immediately preceding the crash. Even though there was no evidence that any person had opened or closed the circuit breaker between the time the airplane landed at Saginaw and departed the gate at Detroit-Metro, the NTSB could not rule out this possibility.
The second possibility considered by the NTSB was that the P-40 circuit breaker opened electrically due to an undetermined transient overload condition, and that the crew did not detect the tripped circuit breaker. In this case, there would be no warning that such a condition existed, and the location of the circuit breaker is such that a tripped breaker might not be visually detected, especially in low ambient light conditions. The NTSB considered the possibility that the P-40 circuit breaker might have opened after the flight crew completed the circuit breaker check on the BEFORE START checklist and while the airplane was being taxied for takeoff. Under those circumstances, it would have been very likely that the P-40 circuit breaker's open condition would have gone undetected.
The third possibility examined by the NTSB was that the P-40 circuit breaker, for undetermined reasons, did not allow current to flow even though the breaker appeared mechanically closed to the flight crew. Typically, this anomaly occurs when the breaker is cycled open and is subsequently closed, such as might occur if a crewmember closes a breaker that has tripped open. Investigators believed that, while the breaker is open, foreign objects may lodge between the breaker contacts preventing full closure. Another means by which current could be impeded is the formation of a dielectric film that could build up on the contact surfaces through airborne contaminants flowing into the vented circuit breaker case. When the contacts are closed, the contact point may rest on the surface of the film, preventing current flow.
Results of the Investigation: After completing its examination, the NTSB concluded that the CAWS unit's takeoff warning system was inoperative and, therefore, did not warn the flight crew that the airplane was not configured properly for takeoff. Additionally, the NTSB determined that the failure of the takeoff warning system was caused by the loss of input 28V dc electric power between the airplane's left dc bus and the CAWS unit, and that the interruption of the input power to the CAWS unit occurred at the P-40 circuit breaker. However, the evidence did not permit the NTSB to determine which of the three possible scenarios had interrupted the flow of current and caused the failure of the P-40 circuit breaker to power CAWS power supply 2.
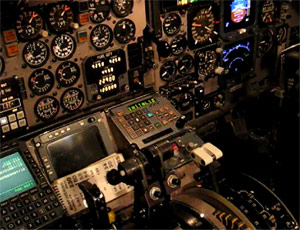
Takeoff Warning System
The Takeoff Warning System (TOWS) identifies the systems or controls that are not properly configured for takeoff. The warning consists of a horn followed by a vocal annunciation of each improperly configured system or control. The takeoff warning system is powered by CAWS power supply 2.
View the MD-82 Takeoff Warning System Animation below.
The two warnings of interest for this accident are the flap warning and the slat warning. The TOWS determines if the airplane's flaps or slats are properly positioned for takeoff by comparing the flap setting entered into the Takeoff Condition Computer (TCC) with the position of the flap/slat lever. On the accident airplane, the flap or slat takeoff warning was designed to activate when the following three conditions are met:
- A disagreement between the flap setting in the TCC and the flap/slat lever position,
- The airplane is on the ground, and
- Either throttle lever position reaches or exceeds 33% of full travel from the idle stop (i.e., full aft).
Results of the Investigation: The NTSB investigation determined that the flight crew had entered the appropriate takeoff flap setting in the TCC but did not extend the flaps and slats prior to starting the takeoff roll. The NTSB's examination of the wreckage found that both throttles were in the full forward position. The NTSB's review of the Cockpit Voice Recorder recording revealed that the recording did not contain any sounds of the TOWS.
Stall Protection System
The stall protection system monitors angle of attack (AOA), the rate of change of AOA, and airplane configuration to provide several warnings to the flight crew. The system consists of two stall warning computers, a stall warning device mounted on each pilot's control column, a supplemental stall recognition system that includes visual and aural alerts for each pilot, an autoslat extension system, and a post stall recovery system. The two stall warning computers are identical, and operate simultaneously, but independently.
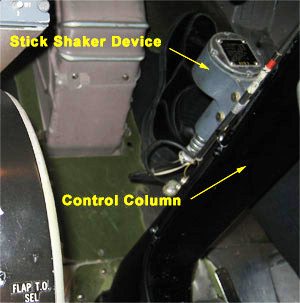
FAA photo taken in an American Airlines DC-9-82 simulator
Stall Warning Device
As the AOA approaches a stall condition, the stall warning device will activate to warn the pilot of an impending stall. An approach-to-stall is detected by either of two independent stall warning computers. Each computer receives AOA, horizontal stabilizer position, flap and slat position information. Either stall warning computer provides pre-stall warning indications by activating the two stall warning devices, commonly known as stick shakers, one on the pilot's control column and one on the copilot's control column. Stall warning activation occurs at a speed of approximately 10% above the stall speed.
Each stick shaker is comprised of an electric motor connected to a deliberately unbalanced flywheel. When actuated, the stick shaker induces forceful, noisy, and unmistakable control column shaking. This shaking is intended to simulate the natural shaking that occurs due to airflow separation as a conventional airplane approaches a stall condition.
Supplemental Stall Recognition System (SSRS)
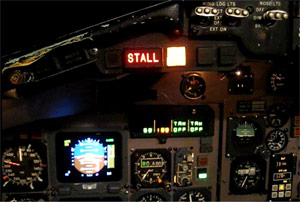
FAA photo taken in an American Airlines DC-9-82 simulator
Each of the two SSRS warnings announces to the flight crew that the stall AOA has been reached and that there is no more safety margin. As the AOA increases to the stall AOA, the SSRS illuminates two "STALL" lights. The lights are located in the glareshield, one light in front of the pilot and one in front of the copilot. In addition to the lights, the SSRS activates a series of aural tones and a voice warning that says the word "stall." The SSRS is active until the stall condition no longer exists. The primary warning is generated by SSRS-2, which is powered by CAWS power supply 3. The redundant warning is generated by SSRS-1, which is powered by CAWS power supply 2.
The primary voice warning produced by SSRS-2 has a limited frequency range, and a flat, almost monotone, pitch. The duration of the SSRS-2 voice warning is approximately 0.37 seconds. The redundant voice warning produced by SSRS-1 is much more dynamic and has a wider frequency range than the SSRS-2 voice warning. The duration of the SSRS-1 voice warning is approximately 0.32 seconds. When both voice warnings operate simultaneously, the effect is perceived as a slight delay between the two warnings. View the Supplemental Stall Recognition System (SSRS) Video to see and hear the SSRS operate during a simulated stall condition.
Autoslat Extension System
The autoslat extension system automatically extends the slats from a mid-position to the fully extended position if several conditions are met. However, the autoslat extension system was deactivated during the accident takeoff because the flap/slat lever was in the up/retract (UP/RET) detent.
Post Stall Recovery System (PSRS)
The PSRS is a device, commonly known as a stick pusher, which abruptly moves the control columns forward in order to pitch the airplane's nose down and reduce the AOA. The PSRS is activated when both stall warning computers detect a stall condition, and the slats are in the fully extended position. Since the slats were in the retracted position during the accident takeoff, the PSRS was deactivated.
Results of the Investigation: The NTSB analysis of the CVR recording showed that the stall warning stick shakers operated continuously from about 8 seconds after the first officer called "rotate" to the end of the CVR recording. The NTSB also performed a sound spectrum analysis of the CVR recording. The results of the analysis revealed that the word "stall" produced a flat, level spectrum signature, and there were no frequency components of the redundant warning from SSRS-1. The NTSB determined from the results of the analysis that the word "stall" was produced only by the primary system, SSRS-2. This determination, along with the lack of a takeoff warning, led the NTSB to conclude that power was not being supplied to CAWS power supply 2.
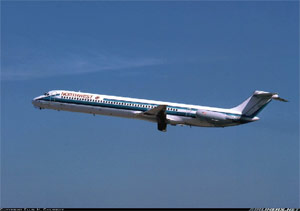
Photo copyright Ellis M. Chernoff - used with permission
DC-9-82 Takeoff Performance
To better understand the flight performance of Flight 255 during the accident takeoff, the NTSB conducted a detailed study. The study was based on time-correlated data from the airplane's digital flight data recorder (DFDR), cockpit voice recorder (CVR), and information derived from those data. The NTSB determined that the airplane's takeoff weight was 144,047 pounds and the intended takeoff flap and slat settings were 11° and mid position, respectively. The position of the TCC flap setting thumbwheel further corroborated the intended 11° takeoff flap setting.
The takeoff speeds on the Northwest takeoff card for the airplane's takeoff weight and intended takeoff configuration were as follows: critical engine failure speed (V1) was 142 knots indicated airspeed (KIAS), rotation speed (VR) was 144 KIAS, and takeoff safety speed (V2) was 153 KIAS. The minimum speeds for flap and slat retraction were 158 KIAS and 198 KIAS, respectively.
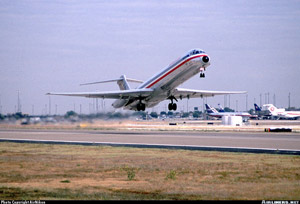
Photo copyright AirNikon Collection - Pima Air Museum - used with permission
The performance study's computations were based on the following data: a takeoff weight of 144,000 pounds; a c.g. of 10% mean aerodynamic chord (MAC); a runway elevation of 631 feet mean sea level (msl); a runway gradient to liftoff of 0.05% down; an altimeter setting of 29.85 inches of mercury (inHg); surface winds from 300° at 14 knots; and 79° F ambient temperature at the time of takeoff.
DFDR data indicated that Flight 255's takeoff was made with the airplane's trailing edge flaps and leading-edge slats retracted. The DFDR data also indicated that both engines were operating at, or above takeoff thrust until all recorded data were lost. A reconstruction of the actual takeoff showed that the airplane's acceleration up to and through VR was in accordance with predicted rates. The CVR recording indicated that first officer called out both V1 and VR, and that these callouts were consistent with the computed values cited above.
According to the DFDR data, the airplane began to rotate at VR. Assuming a proper takeoff configuration, the DC-9-82 normally lifts off at a nose-up pitch angle between 6° and 8°; however, in this case the airplane did not. The airplane continued rotating until the pitch angle reached 11° to 12° and stabilized at that angle. The DC-9-82's tail will strike the ground at a pitch angle of 11.7°. The NTSB noted that there was no evidence of a tail strike during the accident takeoff.
The airplane lifted off the runway at the 11° to 12° pitch angle as it was accelerating through 168 KIAS. The computed flaps and slats retracted stall speed for the airplane was 170 KIAS. The stall warning system's stick shaker activated 0.5 second after liftoff and continued to operate until the end of the CVR recording. The airplane continued to accelerate after liftoff and began to climb. At 4.5 seconds after liftoff, when the airplane was over the departure end of the runway at 10 feet above ground level (AGL), the SSRS aural warning activated. Three more SSRS activations occurred before the initial impact at about 6, 9, and 12 seconds after liftoff. During the 14 seconds between liftoff and initial impact, the DFDR data indicated that the airplane climbed about 45 feet AGL and accelerated to about 186 KIAS.
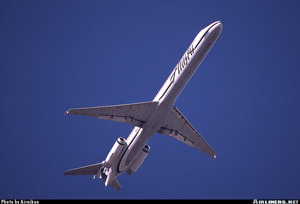
Photo copyright AirNikon Collection - Pima Air Musem - used with permission
Except for momentary nose-down corrections, the pitch angle continued increasing throughout the flight until it reached between 14° and 15°. The programmed angles of attack for stick shaker and SSRS activation were about 11° and 13°, respectively, and, in this case, the angles of attack and the fuselage pitch angles were about the same. Although the airplane was being flown at angles of attack between those that activated the stick shaker and the SSRS, it was still accelerating and climbing. However, the airplane's aerodynamic performance in this area was reduced by two factors: the post liftoff stall induced rolls and the spoiler deflections used to counteract the rolling moments. View the Northwest Airlines Flight 255 Takeoff Animation to see an animation of the effects of high lift devices on takeoff performance.
Upper wing mounted spoiler panels on each wing extend and retract as the pilot's control wheel rotates left or right from the center position. Spoiler panels on the downward moving wing extend to increase the airplane's rolling capability by reducing wing lift, while spoiler panels on the upward moving wing remain retracted. Spoiler deployment begins when the control wheel is rotated approximately 12° left or right. As the control wheel continues to rotate past 12°, spoiler deployment increases. During the last 6 seconds of the flight, the roll oscillations and subsequent spoiler deflections adversely affected the airplane's climb performance by degrading the lift component by as much as 20%.
In the accident takeoff, the stall speed for the clean (i.e., flaps and slats retracted) wing was 170 KIAS. Extending the slats to the mid position would reduce the stall speed to 130 KIAS; extending the flaps to 11° would have reduced the stall speed an additional 6 to 8 KIAS. The reduced stall speeds would have reduced the airplane's liftoff speed, reduced its takeoff ground roll distance, improved its climb capability, increased its climb angle, and improved the roll stability. With this information, the NTSB explored six climb profiles to learn how the DC-9-82 would perform with various takeoff configurations and piloting techniques.
The first profile examined the airplane's performance with the flaps at 11°, the slats at the mid position, and the takeoff performed at programmed speeds contained on Northwest's 144,000-pound takeoff chart. Results of this profile indicated that under these conditions, the airplane would have lifted off 6,520 feet down the runway and cleared the initial impact point by 600 feet.
The fourth profile examined the performance of the airplane with flaps and slats retracted. The airspeeds, pitch, and roll attitudes of the airplane were based on values derived from the DFDR readout of the takeoff roll. This profile placed the airplane at 41 feet AGL at the impact point.
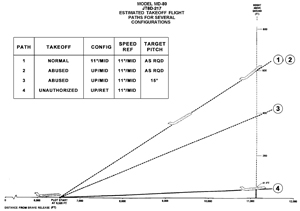
View Larger
The second and third profiles are variations of the first profile, and the fifth and sixth profiles explore variations in piloting techniques after liftoff with flaps and slats retracted. See the NTSB report for full details of these performance profiles.
The NTSB's performance study corroborated physical evidence that Flight 255 was not properly configured for takeoff. DFDR data showed that both engines were operating at or above takeoff power and, that although the acceleration up to and through VR was in accordance with predicted rates, the airplane did not lift off at the predicted pitch attitude. Assuming a proper takeoff configuration, the airplane should have lifted off between a 6° and 8° nose-up pitch attitude. During the accident takeoff, the airplane rotated to an 11° nose-up attitude, stabilized at that attitude, and accelerated to a higher airspeed before liftoff. The liftoff speed provided further evidence that the airplane was not configured properly. With both engines operating at takeoff power, a properly configured airplane typically should have been at V2+10 KIAS (163 KIAS) by the time it climbed through 35 feet AGL. However, the accident airplane did not lift off until it accelerated to about 169 KIAS.
Weather Information
On the day of the accident, sunset at Detroit-Metro was at 2034. At the time of the accident, the moon was below the horizon.
On the day of the accident, a surface weather map, prepared by the National Weather Service (NWS) and valid for a local time period around 2000, showed a low-pressure system just north of central Lake Superior with a cold front extending south, then south-southwest through central Wisconsin, southwestern Iowa, northwestern Missouri, and into the Texas Panhandle. There was an instability line about 60 miles to the east and parallel to the front from northwestern Wisconsin into north central Texas. Conditions in the vicinity of Detroit were characterized by light, southerly winds, broken clouds, and haze.
A surface weather observation recorded by the NWS at the Detroit-Metro airport at 2048, shortly after the time of the accident, reported the following:
Scattered cloud cover at 2,500 feet; a ceiling estimated at 4,500 feet with broken cloud cover; an overcast sky at 10,000 feet; visibility of 6 miles in haze; an ambient temperature of 79° F; a dew point of 66 F°; winds from 280° at 12 knots; an altimeter setting of 29.85 inHg; and remarks stating that cumulonimbus clouds were northwest through north of the airport and moving east.
The NTSB reviewed two NWS radar observations that placed the Detroit-Metro airport within an area that was up to 5/10 covered by thunderstorms with very heavy rain showers. About 75 minutes prior to the accident, the cells were reported to be 20 miles west of the airport and moving east-northeast at 20 knots. Approximately 8 minutes after the accident, the cells were reported to be 39 miles northeast of the airport and moving north-northeast at 25 knots. According to the NTSB report, an NWS radar observer stated that there were no thunderstorms in the immediate vicinity of the Detroit-Metro airport at the time of the accident.
At 2045, about the time of the accident, the centerfield anemometer of Detroit-Metro's low level windshear alert system (LLWAS) recorded winds of 300° magnetic at 13 to 15 knots.
According to the NTSB report, the Air Traffic Control (ATC) recording of Detroit-Metro's tower (local) controller east (LC-E) position showed that LLWAS alarms had been received in the tower cab between 2015 and 2030 and had been broadcast by the LC-E controller over his frequency. The recording also showed that, at 2019, Northwest flight 1146 had reported a variation of plus or minus 20 KIAS between 500 and 300 feet AGL while on final approach to runway 21R. ATIS information Golf and information Hotel were transcribed at 2020 and 2028, respectively. Both messages stated, "windshear advisories are in effect." The evidence showed that windshear alerts had occurred at Detroit-Metro and that windshears had been reported near the airport by pilots during a 30-minute period before the accident.
The NTSB investigation showed that Flight 255's stall warning stick shaker had activated immediately after liftoff and that the airplane failed to either match or approach its predicted climb profile. This evidence suggested initially that the airplane encountered a windshear that significantly decreased its performance capability. A loss of an airplane's climb performance can be caused by a strong downdraft or a rapidly decreasing head-wind shear. However, based on the results of its performance study, the NTSB found that Flight 255 did not encounter windshear either during the takeoff roll or after liftoff.
Pre-Takeoff Flight Crew Performance
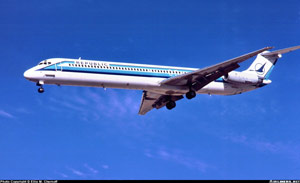
Photo copyright Ellis M. Chernoff - used with permission
The flight crew's performance patterns were examined by the NTSB. The examination included the flight crew's actions during the flight into Detroit and during their departure from the terminal and taxi to the takeoff runway. The NTSB reported that the flight crew's performance showed numerous examples of less than standard performance:
- After landing at Detroit-Metro, the flight crew taxied past the entrance to their assigned gate and had to turn 180° to return to the gate.
- The airplane's weather radar is normally turned off during the AFTER-LANDING checklist which is normally accomplished shortly after clearing the active runway. However, Flight 255's weather radar was still on when the airplane was in proximity of the gate and after a lengthy taxi.
- During the taxi-out at Detroit-Metro, ground control directed the crew to taxi to runway 3C, to change radio frequencies, and to contact ground control on the new radio frequency. The first officer did not change frequencies, and ground control was unable to contact the flight when it taxied past taxiway Charlie.
- The first officer had reiterated the ATC taxi clearance, taxi route, and the takeoff runway assignment to the captain at least twice. The captain did not question either the radio transmission or the first officer's reiteration of the transmission. Although the captain had flown to and from Detroit-Metro many times, he failed to turn off at Charlie and expressed doubt as to where it was located.
In essence, when these deviations are assessed together with the flight crew's flawed checklist performance, the NTSB concluded that their performance was below the standards of an air carrier flight crew.
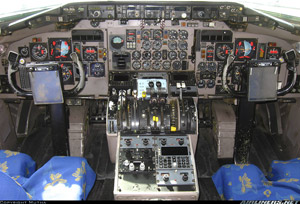
Photo copyright Mutha - used with permission
During its examination, the NTSB commented that it is the captain's responsibility to structure the manner in which his crew will accomplish its duties. While he must be open to information input from his crew, he must set the tone for how this information will be transmitted. In its examination of the performance of Flight 255's captain, the NTSB noted that, except for the BEFORE START CHECKLIST, he did not call for any of the other checklists nor did he point out to the first officer that checklists were not being accomplished in accordance with company procedures. After pushback, the captain initiated three conversations which were not germane to duty requirements, and which diverted the crew's attention from task-related activities. The crew checklists, including the relevant pre-takeoff checklists are available at the following link: (Checklists)
Evidence examined by the NTSB and presented in the accident report indicated that, "the first officer was either given, or assumed he had been given, the duties of leading the crew's task-related activities up to and including the signing of the flight release, a responsibility assigned to the captain by regulation. While it is possible the captain intended to discuss this problem with the first officer, he did not point out to the agent, for the agent's future knowledge, that only the captain is authorized to sign the release. The first officer's assumption of the role of leader placed him in a position of structuring the crew's approach to activities while at the same time trying to satisfy the captain that he was carrying out his subordinate role in a satisfactory manner."
The report further stated, "In the area of checklist initiation, the first officer's assumption of initiation responsibilities greatly increased his work and planning load and relegated the captain's function to that of observer. The evidence also indicated that deference by a captain to a first officer also can inhibit crew effectiveness because the captain cannot presume that the first officer will always assume all of the captain's responsibilities. Flight 255's captain appears to have become dependent upon checklist initiation by the first officer instead of on his own active initiation responsibilities. Therefore, when the first officer became distracted, the captain's passive involvement with checklist initiation did not provide a backup to the first officer's memory."
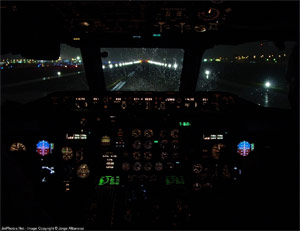
Photo copyright Jorge Albanese - used with permission
View Larger
The NTSB further commented in their report that, "...human performance is subject to considerable change and variation. Factors which can contribute to substandard performance are often subtle, difficult to recognize, and individual in nature. It is for these reasons that standard operating procedures are developed... Routine operating procedures, when applied in a disciplined, standardized manner, provide crewmembers with a firm foundation upon which they can depend for support during those times when they are subject to less than optimum levels of performance. This support is provided when the crew fully recognizes the necessity to function as a coordinated team while applying routine procedures in a disciplined and standardized manner."
The NTSB concluded that, in this accident, it was clearly evident the flight crew did not perform checklist procedures in the manner prescribed in the Northwest Airlines Airplane Pilot's Handbook (APH).
In an article entitled "Give E-Checklists an A+," published in the January 2012 issue of Business & Commercial Aviation magazine, author Patrick R. Veillette, Ph.D., discusses the benefits of using an electronic checklist in lieu of a paper checklist. View Give E-Checklists an A+ to read the article.
Post-Takeoff Flight Crew Performance
Even though the NTSB determined that the flight crew failed to configure the airplane properly for takeoff, the NTSB examined the flight crew's actions after takeoff to see if flight crew could have prevented the accident. The CVR transcript showed that the first officer made the required callouts during the takeoff roll. Therefore, the NTSB concluded that the captain was flying the airplane at the time of the accident.
The NTSB investigation sought to understand what the captain and first officer believed the configuration of the airplane was during the takeoff. Since they both believed that the airplane was configured as required for takeoff before they began the takeoff, the fact that the takeoff warning did not sound in accordance with their expectations would have further reinforced their belief that the flaps were at 11° and that the slats were extended to the mid position.
During the time the flight crew had been in the airplane, evidence indicated that there had been numerous communications concerning windshear and microbursts in proximity to the airport. Also, thunderstorms, which might reinforce the possibilities of windshear or gusts, were in sight north and west of the airport. When the immediate nature and strength of repetition, both verbally and visually, of the possibility of windshear is combined with the reasons for the crew's belief in a properly configured airplane, the NTSB believed that it was reasonable to conclude that the flight crew thought they had encountered a windshear when the stall warnings began after liftoff and focused their attention on escaping from a windshear encounter.
See the NTSB report for the detailed analysis of the flight crews after takeoff performance.
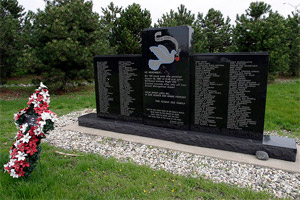
Accident Memorial
On the 7th anniversary of the accident, family members unveiled a memorial for the victims of the accident. The memorial is located at the crash site near highway I-94 and Middlebelt Road
As a result its investigation into the crash of flight 255, the NTSB issued twelve findings. The subject of the findings included flight crew performance, the takeoff warning system, and airplane takeoff performance. Complete text of the findings may be viewed at the following link: Detroit NW255 - NTSB Findings.
The entire NTSB accident report is available at the following link: Detroit NW255 NTSB Accident Report AAR88-05.
The NTSB issued seven recommendations to the FAA, and one recommendation to all 14 CFR part 121 Air Carriers. The recommendations covered a variety of subjects. Complete text of the recommendations may be viewed at the following link: Detroit NW255 - NTSB Recommendations.
14 CFR 25.111 Takeoff path.
14 CFR 25.113 Takeoff distance and takeoff run.
14 CFR 25.115 Takeoff flight path.
14 CFR 121.189 Airplanes: Turbine engine powered: Takeoff limitations.
14 CFR 121.542 Flight crewmember duties.
The NTSB concluded that the probable cause of this accident was the failure of the flight crew to accomplish the TAXI checklist in accordance with the required procedures. The TAXI checklist was the only checklist of the three pre-takeoff checklists that includes an item to extend the flaps and slats for takeoff. The NTSB sought to determine why flight 255’s first officer did not properly position the flaps and slats for takeoff but could not make a conclusive determination. During its investigation, the NTSB interviewed Northwest flight personnel who indicated that the flap extension procedure had become a very strong habit pattern among DC-9 first officers.
The airplane’s manufacturer recommended extending the flaps as the airplane began taxiing to minimize engine exposure to foreign object damage (FOD). In response to the manufacturer’s recommendation, Republic Airlines, prior to the merger with Northwest Orient Airlines, added “FLAPS” to the taxi checklist. According to the NTSB report, flap extension by the first officer did not require the captain to be notified or to approve the repositioning of the flaps.
The NTSB noted that the habit pattern of extending the flaps as the airplane began to taxi may have caused a lessening of the first officer’s awareness of the omission. By the time the first officer completed copying the ATIS message and analyzing takeoff data, the airplane taxied well beyond the point where he would have routinely extended the flaps. The NTSB postulated that the first officer may have believed that he had extended the flaps since that task was always completed shortly after the airplane began to taxi or by the time the airplane departed the terminal ramps.
Maintain proper flight deck discipline
- Failure to complete pre-takeoff checklists
Configure the airplane for takeoff
- Failure to properly configure the airplane for takeoff
- Failure of the Takeoff Warning System to operate properly
- The flight crew was expected to follow the airline’s prescribed preflight procedures, including the pre-takeoff checklists. The NTSB noted in its accident report that the flight crew failed to execute the TAXI checklist, which calls for the airplane’s flaps and slats to be properly positioned for takeoff.
- The takeoff warning system was expected to notify the flight crew when the airplane was not in the desired takeoff configuration. According to the NTSB report, the fact that the takeoff warning did not activate as the airplane began its takeoff roll reinforced the flight crew’s assumption that the airplane was properly configured.
26 Dec 1968: B-707, Pan American, Elmendorf Air Force Base, AK
Pan American Clipper, N799PA, a Boeing 707-321C, cargo/mail flight bound for Vietnam via Tokyo, Japan, crashed on takeoff from Runway 23, Elmendorf AFB, Anchorage, Alaska, at approximately 0615 on December 26, 1968. The aircraft was destroyed. The accident was fatal to all three crewmembers, who were the only occupants.
The takeoff was made with the flaps in the retracted position. A takeoff aural warning system, which was designed to alert the crew to the fact that the flaps were not in the proper takeoff position, did not activate. The NTSB determined that the probable cause of the accident was an attempted takeoff with the flaps in a retracted position. This resulted from a combination of factors: (a) inadequate cockpit checklist and procedures; (b) a warning system inadequacy associated with cold weather operations; (c) ineffective control practices regarding manufacturer's Service Bulletins; and (d) stresses imposed upon the flight crew by their attempts to meet an air traffic control deadline.
The NTSB report on this accident may be viewed at the following link: NTSB Rpt 1-0045 Pan Am Anchorage 1968.
20 Nov 1974: B-747, Lufthansa, Nairobi, Kenya
Lufthansa Flight 540, a Boeing 747-130, was a regularly scheduled flight from Frankfurt via Nairobi, Kenya, to Johannesburg, South Africa. The airplane crashed shortly after taking off from Jomo Kenyatta International Airport in Nairobi, where 59 of 157 people on board were killed.
While taking off, the flight crew felt vibration or buffeting following lift off. The captain, suspecting wheel imbalance, raised the gear. A lack of acceleration forced the flight crew to lower the nose in order to maintain airspeed. The airplane continued to descend and contacted the ground approximately 3,700 feet past the end of the runway. The aircraft broke up and caught fire before coming to rest about 1,500 feet past the initial point of impact.
The Kenyan Air Accident Investigation Unit determined that the accident was caused by the flight crew initiating a take-off with the leading-edge flaps retracted because the pneumatic system which operates them had not been switched on. Taking off with slats retracted resulted in the aircraft becoming airborne in a partially stalled condition which the pilots did not identify in the short time available to them for recovery. Major contributing factors to the accident were the lack of warning of a critical condition of leading-edge flap position and the failure of the flight crew to complete satisfactorily their checklist items.
One regulatory change and a number of policy changes were made as a result of this accident.
NTSB Safety Recommendation A-88-66 requested the FAA to develop and disseminate guidelines for the design of central aural warning systems. In response to this Safety Recommendation, the FAA developed and released Advisory Circular AC 25.703-1, Takeoff Configuration Warning Systems. This AC provides guidance for the certification of takeoff warning systems installed in transport airplanes. Complete text of AC 25.703-1 may be viewed at the following link: AC 025.703-1
NTSB Safety Recommendation A-88-67 asked the FAA to require that all Parts 121 and 135 operators and principal operations inspectors emphasize the importance of disciplined application of standard operating procedures and, in particular, emphasize rigorous adherence to prescribed checklist procedures. The FAA took three actions in response to this Safety Recommendation:
- On December 30, 1988, the FAA issued Action Notice A8400.2, Normal Checklist Review Parts 121 and 135. This action notice required principle operations inspectors to review the adequacy of checklists and the implementing procedures used by all 14 CFR parts 121 and 135 operators.
- On October 2, 1990, the FAA published Special Federal Aviation Regulation (SFAR) 58, Advanced Qualification Program. The SFAR was intended to improve air carrier training, evaluation, certification, and qualification requirements for appropriate personnel. Additionally, this SFAR addressed cockpit resource management training and line-oriented flight training and evaluation. Complete text of SFAR 58 may be viewed at the following link: FR_55_40262 SFAR 58
- On February 10, 1993, the FAA issued AC 120-51A, a revision to AC 120-51. The revision changed the title of the advisory circular from Cockpit Resource Management Training to Crew Resource Management and added specific observable and measurable markers for in-flight operations, including adherence to checklist and operating procedures. Complete text of AC 120-51A may be viewed at the following link: AC 120-51A
NTSB Safety Recommendation A-88-68 requested the FAA to convene a human performance research group to determine if there is any method of presenting a checklist which produces better user performance. In response to this Safety Recommendation, the FAA contracted with the Volpe National Transportation System Center (TSC) to conduct a study on the use and design of paper checklists. The TSC report, entitled The Use and Design of Flight crew Checklists and Manuals, was published in April 1991. Complete text of the TSC report may be viewed at the following link: VNTSC Rpt DTO-VNTSC-FAA-91-7. The FAA used information from this report to revise the Air Transportation Operations Inspector’s Handbook to provide guidance to principal operations inspectors for evaluation the legibility of checklists, including size and style of print.
In its reply to the FAA response, the NTSB noted that in May 1990 the National Aeronautics and Space Administration (NASA) published a study conducted by the Ames Research Center. The NASA study is entitled Human Factors of Flight-Deck Checklists: The Normal Checklist. Complete text of the NASA study may be viewed at the following link: NASA Ames Rpt CR 177549. The NTSB felt that the FAA’s action alone was not responsive to the safety recommendation. The NTSB believed that examination of the TSC and NASA studies could serve as the foundation for a comprehensive human factors examination and evaluation by experts and result in improved understanding of checklist-induced errors, checklist misuse, checklist design improvements, and enhanced safety of flight operations.
NTSB Safety Recommendation A-88-69 requested the FAA to expedite the issuance of guidance materials for use by Parts 121 and 135 operators in the implementation of team-oriented flight crew training techniques. In response to this Safety Recommendation, the FAA issued two advisory circulars:
- On December 1, 1989, the FAA issued Advisory Circular AC 120-51, Cockpit Resource Management Training. This AC provides guidelines for 14 CFR parts 121 and 135 certificate holders to establish training designed to increase the efficiency with which flight crew members interact in the cockpit by focusing on communication skills, teamwork, task allocation, and decision making. This AC was later revised in response to NTSB Safety Recommendation A-88-67. On February 10, 1993, the revision was issued as AC 120-51A.
- On September 6, 1990, the FAA issued Advisory Circular AC 120-35B, Line Operational Simulations: Line-Oriented Flight Training, Special Purpose Operational Training, and Line Operational Evaluation. This AC provides details on implementing line-oriented flight training for a complete crew under both recurrent training programs and advanced simulation plans, as well as guidelines for implementing other types of operational simulations. Complete text of AC 120-35B may be viewed at the following link: AC120-35B
One airworthiness directive was issued as a result of this accident.
NTSB Safety Recommendation A-88-65 requested the FAA require the modification of the DC-9-80 series airplanes to illuminate the existing central aural warning system (CAWS) fail light on the overhead annunciator panel in the event of CAWS input circuit power loss. The original airplane design illuminated the CAWS fail light only in the event of CAWS power supply malfunction, but not loss of input circuit power. On March 8, 1990, and in response to this Safety Recommendation, the FAA issued Airworthiness Directive AD 90-04-05 to prevent takeoff of DC-9-80 and MD-88 series airplanes while in an unsafe configuration for takeoff, due to flight crew deactivation of the takeoff warning system in order to eliminate nuisance warnings of the takeoff warning system during single-engine taxi operations. The AD required a design change such that both throttle levers must be advanced simultaneously to activate the takeoff warning rather than just one throttle lever. Complete text of AD 90-04-05 may be viewed at the following link: AD-90-04-05
As a result of this accident, the FAA convened a special FAA team on September 23, 1987, to study takeoff warning systems. The team’s final report was published on April 29, 1988. Complete text of the FAA report may be viewed at the following link: Review of Takeoff Configuration Warning Systems on Large Jet Transports. The FAA team determined that the problem was not whether or not the CAWS fail light illuminates when the CAWS is intentionally deactivated, but rather the nuisance warnings addressed by AD 90-04-05. The FAA determined that this AD significantly enhanced safety by eliminating the cause of constant nuisance warnings and removing the incentive for flight crews to pull the circuit breaker to interrupt power to the CAWS. The NTSB accepted issuance of AD 90-04-05 as acceptable closing action for Safety Recommendation A-88-65.
Airplane Life Cycle:
- Design / Manufacturing
- Operational
- Maintenance / Repair / Alteration
Accident Threat Categories:
- Flight Deck Layout / Avionics Confusion
- Incorrect Piloting Technique
- Lack of System Isolation / Segregation
- Landing / Takeoff Excursions
Groupings:
- Automation
- Loss of Control
Accident Common Themes:
- Human Error
Human Error
The flight crew did not properly configure the airplane for takeoff. The flight crew was distracted during taxi and did not complete the checklist that would have assured proper setting of the flaps and slats. As a result, the flaps and slats remained in their retracted positions during takeoff, creating an airplane performance deficiency which led to the crash. The NTSB concluded that the distractions during taxi prevented the completion of the appropriate checklists and were indicative of a lack of proper crew coordination and adherence to company procedures.
Accidents – Takeoff Configuration
26 Dec 1968: B-707, Pan American, Elmendorf Air Force Base, AK
Pan American Clipper, N799PA, a Boeing 707-321C, cargo/mail flight bound for Vietnam via Tokyo, Japan, crashed on takeoff from Runway 23, Elmendorf AFB, Anchorage, Alaska, at approximately 0615 on December 26, 1968. The aircraft was destroyed. The accident was fatal to all three crewmembers, who were the only occupants.
The takeoff was made with the flaps in the retracted position. A takeoff aural warning system, which was designed to alert the crew to the fact that the flaps were not in the proper takeoff position, did not activate. The NTSB determined that the probable cause of the accident was an attempted takeoff with the flaps in a retracted position. This resulted from a combination of factors: (a) inadequate cockpit checklist and procedures; (b) a warning system inadequacy associated with cold weather operations; (c) ineffective control practices regarding manufacturer's Service Bulletins; and (d) stresses imposed upon the flight crew by their attempts to meet an air traffic control deadline.
The NTSB report on this accident may be viewed at the following link: NTSB Rpt 1-0045 Pan Am Anchorage 1968
20 Nov 1974: B-747, Lufthansa, Nairobi, Kenya
Lufthansa Flight 540, a Boeing 747-130, was a regularly scheduled flight from Frankfurt via Nairobi, Kenya, to Johannesburg, South Africa. The airplane crashed shortly after taking off from Jomo Kenyatta International Airport in Nairobi, where 59 of 157 people on board were killed.
While taking off, the flight crew felt vibration or buffeting following lift off. The captain, suspecting wheel imbalance, raised the gear. A lack of acceleration forced the flight crew to lower the nose in order to maintain airspeed. The airplane continued to descend and contacted the ground approximately 3,700 feet past the end of the runway. The aircraft broke up and caught fire before coming to rest about 1,500 feet past the initial point of impact.
The Kenyan Air Accident Investigation Unit determined that the accident was caused by the flight crew initiating a take-off with the leading-edge flaps retracted because the pneumatic system which operates them had not been switched on. Taking off with slats retracted resulted in the aircraft becoming airborne in a partially stalled condition which the pilots did not identify in the short time available to them for recovery. Major contributing factors to the accident were the lack of warning of a critical condition of leading-edge flap position and the failure of the flight crew to complete satisfactorily their checklist items.
31 Aug 1988: B-727, Delta, Dallas-Ft. Worth, TX
About 0901 central daylight time, Delta Air Lines, Inc., Flight 1141, crashed shortly after lifting off from runway 18L at the Dallas-Fort Worth International Airport, Texas. The airplane, a Boeing 727-232, was a regularly scheduled passenger flight and was en route to Salt Lake City, Utah, with 101 passengers and 7 crewmembers. The flight crew reported that the takeoff roll appeared to be normal in all respects, with no warning lights, audible warnings, or unusual engine instrument conditions. The captain stated that the rotation was initially normal, but as the main gear wheels left the ground he heard “two explosions." He said it felt as though the airplane was experiencing "reverse thrust." The captain stated that the airplane began to "roll violently."
The airplane struck the instrument landing system (ILS) localizer antenna array approximately 1,000 feet beyond the end of runway 18L and came to rest about 3,200 feet beyond the departure end of the runway. The flight was airborne approximately 22 seconds from liftoff to the first ground impact near the ILS localizer antenna. The airplane was destroyed by impact forces and the post-crash fire. Of the persons on board flight 1141, 12 passengers and 2 crewmembers were killed, 21 passengers and 5 crewmembers were seriously injured, and 68 passengers sustained minor or no injuries.
The NTSB determined that the probable causes of this accident were (1) the Captain and First Officer's inadequate cockpit discipline which resulted in the flight crew's attempt to takeoff without the wing flaps and slats properly configured; and (2) the failure of the takeoff configuration warning system to alert the crew that the airplane was not properly configured for the takeoff. Contributing to the accident was Delta's slow implementation of necessary modifications to its operating procedures, manuals, checklists, training, and crew checking programs which was necessitated by significant changes in the airline following rapid growth and merger. Also contributing to the accident was the lack of sufficiently aggressive action by the FAA to have known deficiencies corrected by Delta and the lack of sufficient accountability within the FAA's air carrier inspection process.
The NTSB report on this accident may be viewed at the following link: DFW DL1141 NTSB Accident Report AAR89-04
31 Aug 1999: B-737, LAPA, Buenos Aires, Argentina
LAPA Flight 3142, a Boeing 737-204C, was a scheduled Buenos Aires to Córdoba flight operated by the Argentine airline Líneas Aéreas Privadas Argentinas (LAPA). The airplane crashed at 2054 local time while attempting to take off from Aeroparque Jorge Newbery after it failed to get airborne. The crash resulted in 67 fatalities, 65 of whom were occupants of the aircraft.
The Junta de Investigaciones de Accidentes de Aviación Civil (JIAAC) reported that, as the aircraft started the takeoff run, a warning sounded in the cockpit, indicating that the aircraft was not correctly configured for the takeoff. The crew continued the run, not realizing that the flaps were not in the required takeoff position and were, instead, fully retracted, thus preventing the aircraft from lifting off. The jet overshot the runway, breaking through the airport's perimeter fence, crossed a road, hitting an automobile, and finally collided with road-construction machinery and a highway median. Fuel spilling over the hot engines and gas leaking from a damaged gas regulation station resulted in a fire that totally destroyed the aircraft. The JIAAC determined that the pilots failed to configure the aircraft correctly for take-off and were allowed to fly without a license by the company.
05 Sep 2005: B-737, Mandala, Medan, Indonesia
At 0315 UTC a Mandala Airlines B737-200, operating as flight number MDL 091, crashed during takeoff from Polonia Airport, Medan, North Sumatera. The initial phase of the takeoff from runway 23 was normal. Following liftoff, the airplane was unable to climb away and settled back onto the runway. It then overran the departure end of the runway and hit several approach lights and continued to travel through a grass area and over a small river. It subsequently impacted several buildings and vehicles before coming to rest on a public road about 1,800 feet from the end of runway 23.
The Indonesian National Transportation Safety Committee determined that the probable causes for this accident were: (1) the aircraft attempted a takeoff with an improper take off configuration namely with retracted flaps and slats causing the aircraft failed to lift off, (2) improper checklist procedure execution by the flight crew which led to a failure to identify the flap in retract position, and (3) the aircraft’s takeoff warning horn was not heard on the cockpit area microphone (CAM) channel of the CVR. It is possible that the takeoff configuration warning horn was not sounding.
The Indonesian National Transportation Safety Committee report on this accident may be viewed at the following link: Final_Report_Mandala_PK-RIM 5Sep05
20 Aug 2008: MD-80, Spanair, Madrid, Spain
At 1424 local time, Spanair Airlines flight 5022, a McDonnell Douglas DC-9-82, crashed on takeoff from Madrid’s Madrid-Barajas Airport. Of the 172 occupants on the airplane, 154 were killed. The accident investigation determined from CVR information, DFDR data, and physical evidence that the flaps and slats were not positioned properly for takeoff. Spain’s Civil Aviation Accident and Incident Investigation Commission’s (CIAIAC) investigation determined that the flaps and slats were in the up and retracted positions, respectively.
The CIAIAC determined that the accident occurred because the flight crew lost control of the airplane as a consequence of entering a stall immediately after takeoff due to an improper airplane configuration involving the non-deployment of flaps and slats following a series of mistakes and omissions, along with the absence of the improper takeoff configuration warning.
The CIAIAC determined that factors contributing to the accident included an absence of an improper takeoff warning resulting from the failure of the Takeoff Warning System to operate, which thus did not warn the flight crew that the airplane’s takeoff configuration was not appropriate. The reason for the failure of the Takeoff Warning System to function was not reliably established. Also contributing to the accident was improper crew resource management, which did not prevent the deviation from procedures in the presence of unscheduled interruptions to flight preparations.
The Spanish CIAIAC report on this accident may be viewed at the following link: Final CIAIAC Rpt Spanair 5022
Incident – Takeoff Configuration
05 Jun 2007: MD-80, MAP Jet, Lanzarote, Canary Islands, Spain
At 1045 local time, a MAP Airlines DC-9-83 took off from the Lanzarote Airport in the Canary Islands. The first officer (i.e., copilot) was the pilot flying for this takeoff. After rotation, which occurred at an approximate speed of 145 knots, the stall warning (i.e., stick shaker) activated and the airplane started a roll oscillation to bank angles of 63° to the right and 60° to the left. The captain retracted the landing gear shortly after liftoff while the airplane was experiencing roll oscillations. Roll oscillations continued until the airplane reached a speed in excess of 200 knots. The airplane climbed to an altitude of 5,000 feet where the flight crew decided to return to Lanzarote. The flight crew did not declare an emergency. The airplane returned to the airport and made an uneventful landing.
Spain’s Civil Aviation Accident and Incident Investigation Commission's (CIAIAC) analysis of the incident data showed that the airplane conducted the takeoff maneuver with slats retracted and the flaps in the UP (0°) position. A procedural omission by the flight crew resulted in the flight crew not selecting the proper slat and flap positions for takeoff. In addition to this error was the lack of protection offered by the Takeoff Warning System, which the crew did not check prior to engine start as required by the MAP checklist. In addition, the Takeoff Warning System was disabled by an open K-33 circuit breaker (Left ground control relay), which was not reset as required by maintenance practices, and was not checked by the flight crew as required prior to engine start. The open K-33 circuit breaker placed some of the airplane systems in the flight mode even though the airplane was still on the ground.
The Spanish CIAIAC report on this incident may be viewed at the following link: CIAIAC Report IN-022-2007
Accidents – Sterile Cockpit
11 Sep 1974: DC-9-31, Eastern, Charleston, NC
At about 0734 eastern daylight time, Eastern Air Lines Flight 212, a DC-9-31, crashed 3.3 statute miles short of runway 36 at Douglas Municipal Airport in Charleston, North Carolina. The flight was conducting a non-precision instrument approach in visibility restricted by patchy dense ground fog. Of the 82 persons aboard the aircraft, 11 survived the accident. One survivor died of injuries 29 days after the accident. The aircraft was destroyed by impact and fire.
The NTSB determined that the probable cause of the accident was the flight crew's lack of altitude awareness at critical points during the approach due to poor cockpit discipline in that the crew did not follow the prescribed instrument approach procedure.
The NTSB report on this accident may be viewed at the following link: Charleston EA212 NTSB Accident Report AAR75-09
01 Jun 1999: DC-9-82, American, Little Rock, AR
At 2350:44 central daylight time, American Airlines Flight 1420, a McDonnell Douglas DC-9-82, crashed after it overran the end of runway 4R during landing at Little Rock National Airport in Little Rock, Arkansas. Flight 1420 departed from Dallas/Fort Worth International Airport, Texas, about 2240 with 2 flight crewmembers, 4 flight attendants, and 139 passengers aboard and touched down in Little Rock at 2350:20. After departing the end of the runway, the airplane struck several tubes extending outward from the left edge of the instrument landing system localizer array, located 411 feet beyond the end of the runway; passed through a chain link security fence and over a rock embankment to a flood plain, located approximately 15 feet below the runway elevation; and collided with the structure supporting the runway 22L approach lighting system. The captain and 10 passengers were killed; the first officer, the flight attendants, and 105 passengers received serious or minor injuries; and 24 passengers were not injured. The airplane was destroyed by impact forces and a post-crash fire.
The NTSB determined that the probable causes of this accident were the flight crew’s failure to discontinue the approach when severe thunderstorms and their associated hazards to flight operations had moved into the airport area and the crew’s failure to ensure that the spoilers had extended after touchdown. Contributing to the accident were the flight crew’s (1) impaired performance resulting from fatigue and the situational stress associated with the intent to land under the circumstances, (2) continuation of the approach to a landing when the company’s maximum crosswind component was exceeded, and (3) use of reverse thrust greater than 1.3 engine pressure ratio after landing.
The NTSB report on this accident may be viewed at the following link: Little Rock AA1420 NTSB Accident Report AAR01-02
See accident module
27 Aug 2006: CL600, Comair, Lexington, KY
About 0606:35 eastern daylight time, Comair flight 5191, a Bombardier CL-600-2B19, crashed during takeoff from Blue Grass Airport, Lexington, Kentucky. The flight crew was instructed to take off from runway 22, but instead lined up the airplane on runway 26 and began the takeoff roll. The airplane ran off the end of the runway and impacted the airport perimeter fence, trees, and terrain. The captain, flight attendant, and 47 passengers were killed, and the first officer received serious injuries. The airplane was destroyed by impact forces and post-crash fire. The flight was en route to Hartsfield-Jackson Atlanta International Airport, Atlanta, Georgia. Night visual meteorological conditions prevailed at the time of the accident.
The NTSB determined that the probable cause of this accident was the flight crewmembers’ failure to use available cues and aids to identify the airplane’s location on the airport surface during taxi and their failure to cross-check and verify that the airplane was on the correct runway before takeoff. Contributing to the accident were the flight crew’s non-pertinent conversation during taxi, which resulted in a loss of positional awareness, and the Federal Aviation Administration’s failure to require that all runway crossings be authorized only by specific air traffic control clearances.
The NTSB report on this accident may be viewed at the following link: Lexington Comair 1591 NTSB Accident Report AAR07-05
See accident module
Technical Related Lessons
Satisfactory takeoff performance is predicated on appropriate aircraft configuration and associated speed schedules. High lift devices (flaps/slats) are critical for achieving this satisfactory performance, and if improperly configured, result in a potentially catastrophic degradation in safety margins. (Threat Category: Landing/Takeoff Excursions)
- Transport airplanes are designed and certificated to operate with safety margins during critical flight phases such as takeoff. A properly configured airplane can perform a safe takeoff in part because the safety margins provide an adequate speed margin above stall, appropriate flight performance, and satisfactory handling characteristics. Safety margins are present only if the flight crews properly configure the airplane for each phase of flight. For takeoff, the high-lift devices must be extended to the appropriate positions. When high-lift devices are not properly configured for a takeoff, safety margins are reduced to near zero.
Safety critical features intended to protect against specific, potentially catastrophic, failure conditions must be arranged and isolated such that failure of the safety feature is annunciated and provides flight crew awareness that the feature is no longer able to perform its function. (Threat Category: Lack of System Isolation / Segregation)
- In this accident, the crew failed to deploy the high lift devices to the proper settings. The NTSB determined that the configuration warning system, which should have provided annunciation to the crew that the airplane was misconfigured, did not function, Proper functioning of the configuration warning system would have warned the crew in time to prevent the takeoff attempt, and/or to properly configure the airplane. The NTSB was not able to determine the nature of the configuration warning failure but concluded that the system was not powered. The crew was apparently unaware that the system was not operational, and therefore had no backup means available to verify that the airplane configuration was correct.
Common Theme Related Lessons
During high workload phases such as preparation for takeoff, takeoff, preparation for landing, or landing, flight crews should maintain a sterile cockpit environment in order to avoid distractions that can lead to operational errors. (Common Theme: Human Error)
- Maintaining a "sterile cockpit" environment reduces fight crew distractions, and enhances adherence to operational procedures, including completion of checklists that are essential for safe operations. The NTSB reported that the flight crew engaged in extraneous conversation during taxi, violating the sterile cockpit environment, and were sufficiently distracted that they missed a taxiway, did not respond properly to ATC taxi instructions, and did not complete the Taxi Checklist, during which the high-lift devices would have been properly configured. Additionally, the flight crew did not complete the Before Takeoff Checklist. Failure to complete the Taxi and Before Takeoff checklists eliminated the second layer of protection that ensures the safety margins are provided for takeoff.