McDonnell Douglas MD-81
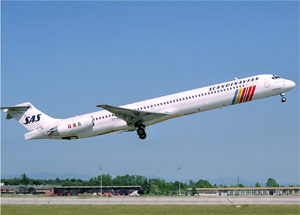
Scandinavian Airlines System Flight 751, OY-KHO
Gottröra, Sweden
December 27, 1991
On December 27, 1991, at approximately 8:51am local time, SAS Flight SK 751, a McDonnell Douglas MD-81, OY-KHO, crash landed in an open field shortly after takeoff from Stockholm/Arlanda airport, Sweden. The fuselage broke into three pieces on impact. All 129 people on board, including 123 passengers and a crew of six survived. One passenger sustained serious back injury. Flight SK 751 arrived at Stockholm/Arlanda at 10:10 pm the previous night and had been parked outdoors overnight. Prior to takeoff, the aircraft was de-iced.
The Swedish Board of Accident Investigation determined that the accident was caused by SAS's inadequate procedures addressing the removal of clear ice from the wings prior to takeoff. As a result, the aircraft took off with clear ice on the wings. During takeoff, the clear ice broke free during rotation and climbout and was ingested into the engines. This resulted in damage to the fan stages of both engines, leading to engine surging and destruction of both engines.
On December 26, 1991, the MD-81 operated by SAS arrived from Zurich and landed at Stockholm/Arlanda airport at 10:09 pm. After landing, the aircraft was parked overnight at gate 2 with approximately 5,622 lbs. (2,550 kg) of fuel remaining in each wing tank. The air temperature at arrival was +33.8° F (+1° C). During the night a ground crew member inspected the aircraft and was required to clear slush from the landing gear in order to perform the landing gear inspection. At approximately 2:00 am, December 27, this crew member noted the presence of ice on the upper surface of the wings.
The aircraft was scheduled for an 8:30 am departure from Stockholm to Copenhagen on the morning of December 27 as Flight SK 751.
On December 27, at 7:30 am, another ground crew member noted frost coverage on the underside of the wings. He checked for ice on the upper side of the left wing and the left engine air inlet. He found no ice but detected slush on the upper side of left wing. At approximately 8:20 am the air temperature had dropped to 32.0° F (0° C).
At 8:30 am, the aircraft was fueled with 3,086 lbs. (1,400 kg) of fuel and was ready for de-icing. After consultation with the captain, a ground crew member ordered de-icing of the underside of the wings due to an earlier detection of frost. There had been no discussions regarding clear ice, since none had been detected during the morning inspection. The ground crew ordered further de-icing after the first spray to assure the removal of slush from the wings. After de-icing, the ground crew did not check for clear ice since none was detected previously.
Ice Detection Tufts
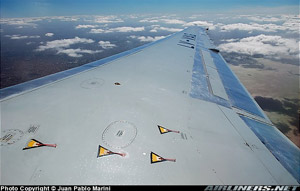
Photo Copyright Juan Pablo Marini - used with permission
A portion of the MD-80 fleet, including this SAS aircraft was equipped with several nylon tufts on the upper surface of the wings, intended to be used as indicators of the presence of clear ice. It was understood that clear ice was difficult to detect visually, and the tufts were intended to enhance that detection capability. Instructions associated with the tufts required that the tufts be "touched" in order to determine the presence of clear ice, and its extent. If the tufts could be freely manipulated, the tufted section of wing was ice free.
The operator of the de-icing spray nozzle reported that during the spraying he saw the movement of one of four upper wing indication tufts. A passenger at a window seat reported no movement of the upper wing indication tufts during the spraying.
The ground crew reported the completion of the de-icing to the captain, and when asked by the captain if "They've got it good and clean under the wings?" he replied "Yes, there was a lot of ice and snow, now it's fine, it's perfect now." The conversation ended with the captain saying, "That sounds fine, thanks."
While the aircraft was being de-iced, the pilots carried on with the routine checks that included the departure procedure from Stockholm/Arlanda airport.
After engine startup and pushback from the gate, the captain taxied the aircraft to runway 08. Both engine anti-icing systems were 'On' with all systems operating in the normal range. During the two and a half minutes of taxiing, the aircraft average speed was 15 knots, and the captain steered the aircraft to avoid running through taxiway slush. The captain made a normal rolling takeoff. The Auto Throttle System (ATS) which automatically and simultaneously controls the engine throttle levers was engaged.
Automatic Thrust Restoration System (ATR)
As a noise abatement measure, many carriers adopted procedures to use large thrust cutbacks following takeoff. The cutbacks were, in many cases, sufficiently large that an engine failure could result in a descent if thrust were not restored on the operating engine(s). In response to this possibility and addressing FAA and airline concerns about crew workload during a critical phase of flight, some manufacturers developed the ATR system, which would, following a thrust cutback and subsequent engine failure, automatically restore the remaining operating engine(s) to the pre-cutback thrust level. This SAS MD-80 was equipped with a version of this system developed by McDonnell-Douglas... The system was certified in March 1983, and subsequently introduced as standard equipment, irrespective of whether the special takeoff procedure was used. In 1992, the designation of Automatic Thrust Restoration (ATR) was introduced in the FAA approved Airplane Flight Manual and in the McDonnell-Douglas Flight Crew Operating Manual.
The ATR is a Digital Flight Guidance (autopilot) System safety function that monitors engine operation during takeoff and climbout. If an engine failure is sensed by the system, due to the MD-80 autothrottle single-clutch configuration, both the failed and non-failed engine thrust levers are advanced to the corresponding in-flight takeoff (go-around) thrust level in order to attain and maintain required engine-out climb performance. The system is automatically armed when three conditions are met:
- The Flight Director pitch axis is set for takeoff.
- The aircraft's height above the ground is more than 350 feet.
- The current Engine Pressure Ratio (EPR) of both engines is below the go-around thrust EPR.
The system is automatically activated when engine EPR's differ by 0.25 or more at the same time as engine N1 speeds differ by 7% or more in the same direction.
Simultaneous movement of all throttle levers was considered acceptable, as it was assumed that a forward throttle movement on a failed engine would not have a hazardous effect on the airplane. The single clutch system did not foresee the possibility of a multiple engine malfunction. Advancing the throttle levers on a stalled engine, as was the case in this accident, would increase the fuel flow to that engine, and result in increasing turbine temperatures that could result in turbine damage if the engine stall continued.
Accident Sequence
The captain started the rotation at 8:47 am. Three passengers saw ice coming off from the upper side of the wings as the aircraft took off. At the same time, the captain heard an abnormal noise. He could not identify the source of the noise. The sound was recorded by the Cockpit Voice Recorder (CVR) as a low hum.
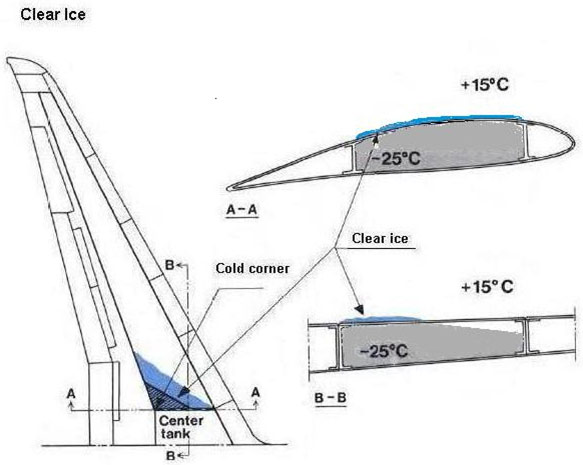
At 25 seconds into the flight and climbing through 1,124 ft (343 m), bangs were heard inside the aircraft followed by vibrations and jerking motions.
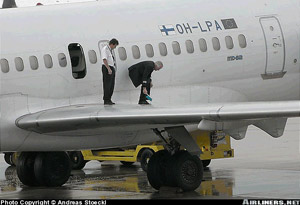
Photo copyright Andreas Stoeckl - used with permission
The pilots isolated the problem to the right engine and a possible compressor stall. The vibrations and the rapid changes in the digital presentation made it difficult for the captain to read the engine instruments. At 43 seconds into the flight and climbing through 2,000 ft (600m), the captain reduced power to the right engine from 1.904 Engine Pressure Ratio (EPR) to 1.870 EPR, but the problems persisted. EPR is the ratio of the outlet pressure to the inlet pressure and is a reference value for engine thrust. The autopilot was not engaged and, according to the flight recorders, throttle control simultaneously changed to an automatic mode, increasing the power settings with altitude. This was indicated discreetly on the instrument panel and went unnoticed by the pilots.
At 64 seconds into the flight, the left engine's first surge was recorded and went unnoticed by the pilots.
At an altitude of 2,616 ft (797 m) an attempt to engage the autopilot failed and activated the voice warning "Autopilot." The warning continued for the rest of the flight.
The right engine failed 51 seconds after the first surge. Two seconds later and 78 seconds into the flight, climbing through 3,206 ft (977 m) at an indicated airspeed of 196 knots, the left engine failed. Within moments, the aircraft reached its maximum flight altitude of 3,318 ft (1011m).
Immediately following the second engine failure, the two Electronic Flight Information System (EFIS) display screens went blank due to loss of both engine-driven generators. The captain made no attempts to recover the EFIS display and for the remainder of the flight relied on a backup altimeter for the altitude information.
After the engine failures, the turbine outlet temperature readings from the engine instruments were over 1,472° F (800° C). This was first noticed by the first officer. Thirteen seconds later, the left engine fire warning came on. The first officer activated the left engine fire extinguishing system. Grey smoke was visible in the forward part of the aircraft. Twenty seconds later the fire warning ceased.
A flight captain traveling in the aft passenger cabin alerted the flight attendant sitting in the cabin rear jump seat that the right engine was surging. Using the intercom, she tried unsuccessfully to contact the aircraft's flight deck. She was finally able to alert the flight deck by passing the message through the flight purser.
A uniformed SAS captain in seat 2C hurried to the cockpit and offered help. He was given the emergency checklist by the first officer and the captain directed him to start the Auxiliary Power Unit (APU). The assisting captain's voice was first recorded two minutes and two seconds into the flight, encouraging the captain to "Look straight ahead."
After the engine failures, the crew prepared for an emergency landing. The captain initiated a glide path and a shallow left turn to a north bound heading. The first officer contacted Stockholm air traffic control and declared an emergency, requesting a clearance to return to Stockholm/Arlanda airport and was cleared to a right turn for landing on Runway 01. The captain, however, continued on the north bound heading.
The flaps were gradually extended by the assisting captain at 1,378 feet (420 m) with an indicated airspeed of 165 knots. Thirty seconds later, at 984 feet, the flaps were fully extended.
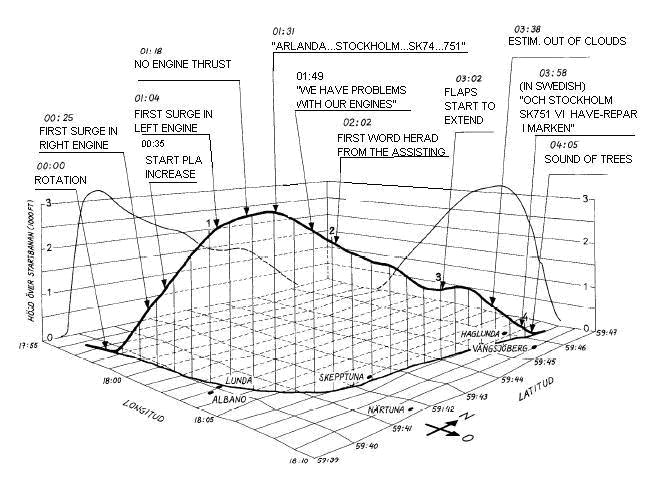
View SAS MD-81 3D Flight Path Animation below:
The aircraft was entirely free from clouds at 980 to 820 ft (300 to 250 m). The captain determined that a large field far to the right of the aircraft could not be reached. He therefore selected a field in the direction of the flight path for the emergency forced landing.
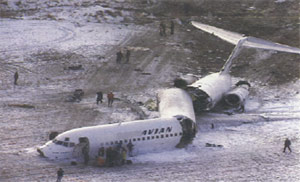
Seventy seconds before ground impact, the first officer is heard on the CVR asking "Shall we get the wheels down?" A reply from the assisting captain was "Yes, gear down, gear down." Seven seconds later the sound of contacts with the trees was recorded on the CVR. According to the flight recorder, at about the same time, the gear was down and locked, and the airspeed had reduced to 121 knots. Upon contact with the trees, a major portion of the right wing tore off, resulting in a bank to the right. The last data recorded one second before impact, registered the aircraft in a 19.7° right bank with an airspeed of 107 knots.
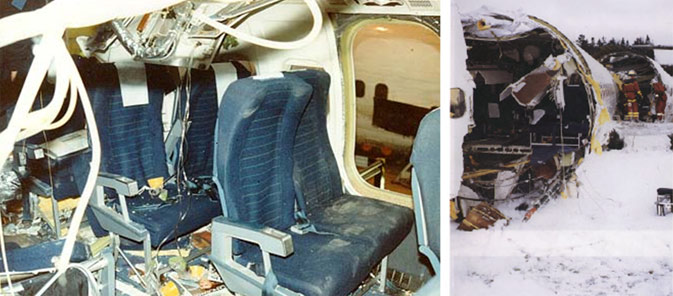
Four minutes and seven seconds after rotation, the aircraft tail struck sloping ground, and came to rest at 361 ft (110 m) from the point of ground impact. The fuselage broke into three major sections. There was no fire. All 129 people on board, including 123 passengers and a crew of six survived. Seven passengers and one crew member sustained serious injuries. Another 81 passengers and three crew members sustained minor injuries. The aircraft was totally destroyed.
View Scandinavian Airlines System (SAS) Flight 751 Accident Animation below:
The Board of Accident Investigation (SHK) of Sweden determined that the cause of this accident was the failure of both engines due to the ingestion of clear ice that came loose from the wings during the take-off roll. The ice caused damage to the engine fan stages, leading to engine surges. The surges lead to the destruction of both engines.
The Board also determined that the SAS's procedures for detection and removal of clear ice prior to take-off were inadequate. A contributing factor to the accident was the ATR system on the aircraft. The activated ATR increased power to both engines during the initial engine surges, leading to the destruction of both engines. According to the Board, SAS was unaware of the onboard ATR system.
The SHK issued 27 findings regarding this accident. The findings dealt variously with the:
- Inadequate procedures for detection and removal of clear ice prior to take-off
- Flight crew emergency procedures
- Inadequate knowledge of the ATR system within SAS
- Adverse and unintended contribution of the ATR system to the engine surges and destruction
- Flight crew response to engine surges
- Cabin safety
Select this link to view the detailed Sweden Accident Board Findings.
The original accident report (in Swedish) is available here: (Swedish Language Report).
The English translations is available here: (English Language Report).
The Board of Accident Investigation (SHK) of Sweden issued 15 recommendations. The subject areas covered include:
- Clear ice detection and removal before flights
- Deactivation of the Auto Throttle System in case of engine surging
- Cabin safety including overhead bins, emergency exits, and cabin attendant jump seat design
- Flight deck emergency procedures for two engine failure due to engine surging
- Instructions for revisions of aircraft operational manual including the emergency procedures to address engine surging and two-engine flame-out
View the detailed Sweden Accident Board Recommendations.
14 CFR 25.803 Emergency Evacuation
14 CFR 25.903 Engines
14 CFR 33.77 Foreign Object Ingestion
14 CFR 91.527 Operating in Icing Conditions
14 CFR 121.629 Operation in Icing Conditions
It is well known that clear ice can form on the upper surfaces of the wings under conditions of high atmospheric humidity or rain in combination with cold temperatures. It is also well known that on the MD-81 series, the risk of ingestion of clear ice into the engine is higher, since the engines are located aft of the wing. The formation of clear ice on the inboard section of the wing (above the aft, inboard portion of the wing fuel tank) can pose an ingestion threat to the engines when this ice is shed from the wing skin. Over the years, the manufacturer had taken a number of steps to inform operators of this threat, including the issuance of service bulletins that provided various means to reduce or mitigate the risks of ice ingestion.
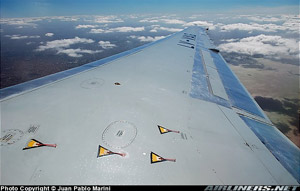
Photo Copyright Juan Pablo Marini - used with permission
SAS was aware of the problem and had equipped the aircraft type with warning triangles and indication tufts to facilitate the discovery of clear ice. The importance of the discovery and removal of the clear ice issue was relayed to all SAS pilots through the Winterization Bulletin. The bulletin clearly stated that it was the responsibility of the captain to check for the presence of snow and ice that could affect the aircraft's performance. The aircraft-type pilot training program, however, did not address the clear ice problem, nor were there any special written instructions for the pilots' action, if the clear ice risk existed.
The SAS Line Maintenance Handbook requires that the wing upper surfaces be checked for clear ice when it is unclear if clear ice has formed on the wing upper surfaces.
The Swedish-language "Line Maintenance De-icing Instructions, Winter 1991/92" for the Arlanda airport requires physical hand contact with the wing upper surface as the only reliable method of clear ice discovery.
However, the SAS Line Maintenance Handbook did not provide clear means on how to check for clear ice, nor did it provide a procedure for reporting clear ice observations. The line maintenance personnel that discovered ice during the evening did not forward the information to the line maintenance personnel responsible for the following morning departure check.
The following key safety issue contributed to this incident:
- The aircraft took off with the presence of clear ice on the upper surfaces of the wings that subsequently broke off during takeoff and was ingested into both engines.
The following safety assumption contributed to this accident:
- The critical surfaces of the aircraft would be free from frost, ice, or snow on takeoff.
- The ATR system would, upon detection of an engine failure during takeoff, advance power on both the operating, and failed engine. It was assumed that this increase in power level on both engines would not represent a hazardous condition
Air Florida Flight 90, Boeing Model 737-200, On January 13, 1982; attempted takeoff with ice and snow on wings and iced engine sensors.
See accident module
Air Ontario Flight 1363, Fokker 28, On March 10, 1989; attempted takeoff with ice and snow on aircraft surfaces, including wings.
See accident module
The following airworthiness directives (ADs) were issued as a result of this accident:
AD 92-10-13 R1 required within 30 days after May 20, 1992, to prevent automatic thrust lever advance on a surging engine during takeoff by revising the Procedure Section of the FAA-approved AFM and adding instructions to: disengage the auto throttles, reduce thrust on affected engine, and shut down the affected engine if surging continues.
AD 2002-21-06 (supersedes AD 2001-06-16 COR & AD-92-03-02) required within 10 days after January 17, 1992 (the effective date of AD 92-03-02) to revise the FAA-approve AFM to include an "ice on wing upper surface" caution statement and installation of inspection aids (i.e., tufts, decal, mount pads, painted symbols, and paint stripes) on the inboard side of the wings' upper surfaces. This latest AD revision also addresses the installation of heater protection panel for airplanes on which an over-the-wing heater blanket system was installed in order to prevent heat damage to the upper surfaces wings.
Airplane Life Cycle:
- Operational
Accident Threat Categories:
- Inclement Weather / Icing
- Lack of System Isolation / Segregation
Groupings:
- Automation
- Loss of Control
Accident Common Themes:
- Organizational Lapses
- Human Error
Organizational Lapses
- Investigators determined SAS was aware of the risks associated with clear ice formation and yet did not clearly address the issues in pilot training sessions and failed to provide adequate procedures for detection and removal of clear ice from the aircraft.
- The aircraft-type pilot training program did not address the clear ice problem, nor were there any special written instructions for the pilots' action, if the clear ice risk existed.
Human Error
- Overnight inspection by a ground crew member detected and noted clear ice on the upper surfaces of the wings. This information was not passed to the crew member responsible for pre-flight inspection, and the airplane was dispatched with ice which had not been cleared during the ground deicing process.
Air Florida Flight 90, Boeing Model 737-200, N62AF
On January 13, 1982, Air Florida Flight 90, a Boeing Model 737-200 series airplane, crashed shortly after takeoff from Washington National Airport, Washington, D.C. The Boeing Model 737-200 experienced difficulty in climbing immediately following rotation and subsequently stalled. The airplane struck the heavily occupied 14th Street Bridge connecting Arlington, Virginia with the District of Columbia, and then crashed into the ice-covered Potomac River. Seventy of the 74 passengers and four of the five crew aboard were killed along with four occupants of vehicles on the bridge. Loss of control was determined to be due to reduction in aerodynamic lift resulting from ice and snow that had accumulated on the airplane's wings during prolonged ground operation at National Airport. Contributing to the airplane's poor takeoff performance was a significant engine thrust shortfall believed to be due to anomalous engine thrust indications on both engines caused by engine pressure ratio (EPR) Pt2 probes which were believed to have been plugged with snow and ice during ground operation.
See accident module
Air Ontario Flight 1363, Fokker 28, C-FONF
On March 10, 1989, Flight 1363, a Fokker 28 airplane operated by Air Ontario, departed Thunder Bay (Ontario) about one hour behind schedule outbound to Dryden and continuing to Winnipeg. In Dryden, the airplane had to be refueled with one engine running, because of an unserviceable APU. Although a layer of 1/8-1/4 inch of snow had accumulated on the wings, no de-icing was done because de-icing with either engine running was prohibited by both Fokker and Air Ontario standard operating procedures. Since no external power unit was available at Dryden, the engines could not be restarted in case of engine shutdown on the ground.
At 12:09 CST the airplane started its take-off roll using the slush-covered runway 29. The Fokker settled back after the first rotation and lifted off for the second time at the 5,700 feet point of the 6,000 feet runway. No altitude was gained, and the aircraft mushed in a nose-high attitude, striking trees. The aircraft crashed and came to rest in a wooded area, 3,156 feet past the runway end and caught fire.
The investigation commission concluded that the Captain, "as the pilot-in-command, must bear responsibility for the decision to land and take off in Dryden on the day in question. However, it is equally clear that the air transportation system failed him by allowing him to be placed in a situation where he did not have all the necessary tools that should have supported him in making the proper decision."
See accident module
Technical Related Lessons:
Environmental conditions, such as ice, rain, birds, turbulence, extreme temperatures, etc., have the potential for multiple airplane system effects. (Threat Category: Lack of System Segregation/Isolation)
- The ingestion of ice into the engines resulted in the eventual failure of both engines. Although not a factor in this accident, the presence of ice on the wings could have also adversely affected airplane performance during takeoff and climbout. Since environmental conditions, by their very nature, have the potential to impact the entire airplane, it is important for each of these threats to have robust airplane capability to withstand these various environmental conditions. It is equally important that the airplane be operated such that extreme environmental conditions, which can exceed any airplane's design capability, be avoided (i.e., severe thunderstorms, high concentrations of birds, severe snowstorms, windshear, etc.).
Clear ice formed on the wings by cold-soaked fuel during ground operations can have significant adverse effects on engine operation when shed into aft-mounted engines during takeoff and flight. (Threat Category: Inclement Weather/Icing)
- The ingestion of ice into the engines resulted in the initial right engine surging, that was further exacerbated by the Automatic Thrust Restoration system increasing power to both engines. The pilot recognized the right engine surging condition and appropriately reduced power. A contributing factor to the engine failures was the engaged onboard Automatic Thrust Restoration system that increased power to both engines during the initial engine surges, contributing to the destruction of both engines.
Common Theme Related Lessons:
The procedures for the detection and removal of ice prior to take-off and during ground checks must be robust and mindful of the formation of clear ice under inclement weather conditions. (Common Theme: Organizational Lapse)
- The SAS Line Maintenance Handbook lacked detailed instructions on how to check for clear ice and did not provide a procedure for reporting clear ice observations. The line maintenance personnel that discovered ice during the evening did not forward the information to the line maintenance personnel responsible for the following morning departure check.