Airbus 300B4-622R
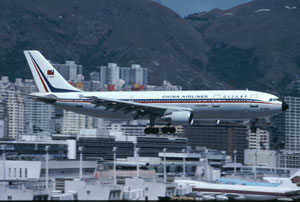
China Airlines Flight 140, B1816
Nagoya, Japan
April 26, 1994
China Airlines Flight 140 from Taipei, Taiwan to Nagoya, Japan executed takeoff climb and cruise phases of flight uneventfully. While the copilot was manually flying the ILS approach to runway 34 at Nagoya, and descending through 1,000 feet, he inadvertently activated the go-around switches (also referred to as the GO lever) on the throttles, activating the auto-throttle go-around mode. This resulted in a thrust increase and a climb above the glide path. The copilot attempted to return to the glide path using forward yoke. Subsequent engagement of the autopilot while in go-around mode caused the trimmable horizontal stabilizer (THS) to drive the stabilizer towards its nose up limit as compensation for the manual control inputs via the yoke.
The first officer continued his effort to maintain approach glide path with forward yoke, commanding the elevator in the airplane nose-down direction (opposite the THS driven by the autopilot system). Passing approximately 510 feet, the captain took control of the aircraft, which was now in an extreme mis-trim condition and applied longitudinal control to the maximum elevator-down limit in opposition to the maximum nose-up stabilizer position. Unable to overcome the greater aerodynamic force of the stabilizer, the crew initiated a go around. On the application of go around thrust, the aircraft rapidly pitched up and airspeed steadily decreased. Correspondingly, airplane angle-of-attack (AOA) increased sharply. The captain was unable to arrest the climb, which continued to approximately 1,700 feet, and AOA increased until the aircraft stalled. Unable to recover from the stall, the aircraft crashed into the landing zone approximately 340 feet east-northeast of the centerline of the approach end of runway 34. Onboard the aircraft were 256 passengers and 15 crew members. All crew members and 249 passengers were killed, and seven passengers were seriously injured. Upon impact the aircraft caught fire and was completely destroyed.
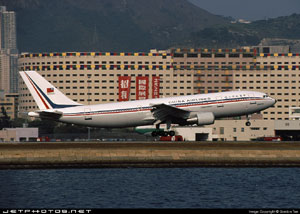
Photo copyright Gordon Tan - used with permission
History of Flight
China Airlines Flight 140 departed from Taipei International Airport, Taiwan on April 26, 1994, towards its destination of Nagoya Airport, Japan (flight plan route). After initial descent and contact with Nagoya Approach Control, the flight was cleared for the Instrument Landing System (ILS) approach to runway 34 (ILS 34 approach) and was switched to the Nagoya tower frequency at approximately 2007 local time. It was nighttime and Nagoya airport weather at the time was reported as winds from 280 degrees at 8 knots, visibility of 20 kilometers, cumulus clouds at 3,000 feet and a temperature of 20 degrees Celsius. During the initial phase of the approach, both autopilot systems (AP1 and AP2) were engaged as well as the auto throttles. After passing the ILS outer marker and receiving landing clearance, the first officer, who was the pilot flying, disengaged the autopilot system and continued the ILS approach manually.
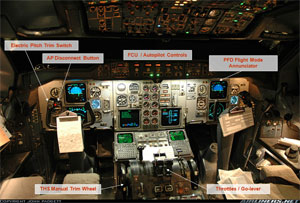
Photo copyright John Padgett - used with permission
View Larger
When passing through approximately 1,000 feet on the approach glidepath, the first officer inadvertently triggered the GO levers placing the auto throttles into go-around mode, which led to an increase in thrust. This increase in thrust caused the aircraft to level off at approximately 1,040 feet for 15 seconds and resulted in the flight path becoming high relative to the ILS glideslope. The captain recognized that the GO lever had been triggered and instructed the first officer to disengage it and correct the flight path down to the desired glide slope. While manually trying to correct the glide path with forward yoke, the first officer engaged the autopilot, causing it to be engaged in the go-around mode as well. As he manually attempted to recapture the glide slope from above by reducing thrust and pushing the yoke forward, he was providing pitch inputs to the elevator that were opposite the autopilot commands to the THS, which was attempting to command pitch up for a go around.
The THS progressively moved from -5.3 degrees to its maximum nose-up limit of approximately -12.3 degress as the aircraft passed through approximately 880 feet. During this period the first officer continued to apply increasing manual nose-down command through forward yoke control which resulted in increasing nose-down elevator movement, opposite the THS movement, masking the out-of-trim condition. The first officer attempted to use the pitch trim control switch to reduce the control force required on the yoke. However, because pitch trim control of the THS is inhibited during autopilot operation, it had no effect. In a normal, trimmed condition the THS and elevator should remain closely aligned. However, because of the opposing autopilot (nose up) commanded THS and manually commanded elevator (nose down) for approximately 30 seconds, the THS and elevator became "mis-trimmed".
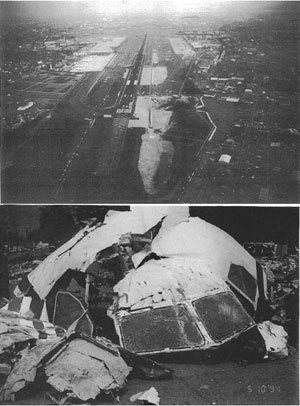
View All Larger
Passing through approximately 700 feet, the autopilot was disengaged but the THS remained at its last commanded position of -12.3 degrees. Also at this time, due to the thrust reduction commanded by the first officer, the airspeed decreased to a low level, resulting in an increasing angle of attack (also termed alpha, or AOA). As a result, the automatic alpha floor function of the aircraft was activated, causing an increase in thrust and a further pitch-up. The alpha floor function of the A300 is an AOA protection feature intended to prevent excessive angles of attack during normal operations. Because of the greater size of the THS relative to the elevator (approximately three times greater in terms of surface area), the available elevator control power or authority was overcome as the aircraft neared 570 feet on the approach. Upon hearing the first officer report that he could not push the nose further down and that the throttles had latched (alpha floor function engaged), the captain took over the controls unaware of the THS position.
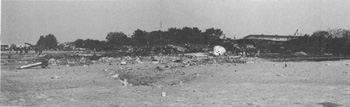
Upon assuming control, the captain initially attempted to continue the approach but was surprised by the strong resistive force to his full nose-down control inputs. He retarded the throttles in an attempt to recapture glide slope. Unable to control the increasing nose-up pitch, which had reached 22 degrees, he called for the GO-lever shortly thereafter in attempt to execute a go around. The increasing thrust added additional nose-up pitch moment and resulted in and uncontrolled steep climb as airspeed continued to decrease and AOA continued to rise. During the attempted go-around, the captain only operated the pitch trim briefly, indicating he was unaware of the mis-trimmed position (extreme nose-up) of the THS. Furthermore, flaps/slats had been retracted two positions (30/40 to 15/15) to the go-around setting, which increased the airplane pitch up and reduced the stall margin. The aircraft continued to climb steeply up to 1,730 feet with AOA rapidly increasing and airspeed decreasing, reaching a maximum pitch angle of approximately 53 degrees until the stall warning and subsequent stall.
Once stalled the aircraft nose lowered to a steep dive and the captain applied full aft yoke in an attempt to recover from the dive; however, the aircraft remained stalled until impact.
An animation of the accident flight path and factors which contributed to the accident are available below:
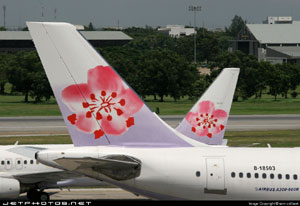
Photo copyright Wim Callaert - used with permission
View Larger
A300 Pitch Control
Critical to this accident are the pitch control surfaces, consisting of the Trimmable Horizontal Stabilizer (THS) and elevator. The greater size of the THS provides much greater control power than that available from the elevator.
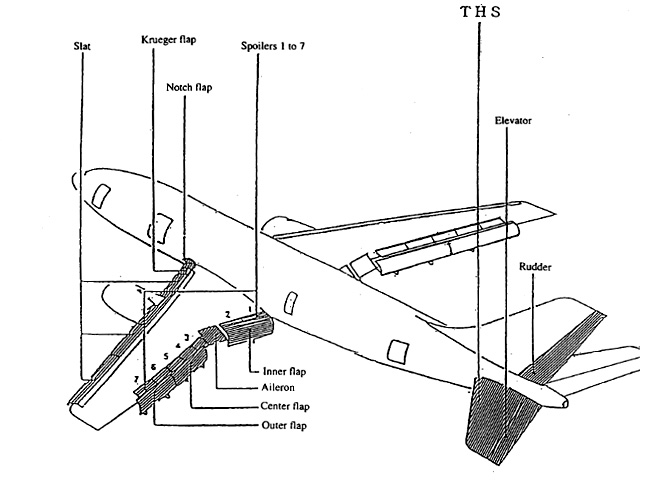
A300 Auto Flight System
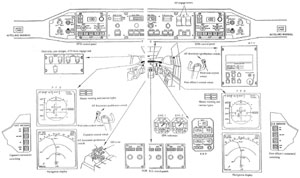
View Larger
The A300 Auto Flight System (AFS) is designed to assist in control of the aircraft in all phases of flight from takeoff through landing. The control surfaces are controlled by a servo system receiving command signals from the Flight Augmentation Computer (FAC), the Flight Controls Computer (FCC), and the Thrust Control Computer (TCC). Key functions provided by each as they relate to this accident are as follows:
Flight Augmentation Computer (FAC) provides yaw damping functions to support rudder control for dutch roll damping, turn coordination, and autopilot assistance in case of engine failure to counter lateral acceleration/yaw during recovery. The FAC also provides pitch trim commands to the THS. Specific pitch trim command functions important to this accident include:
Electric Trim: Pitch control loads may be alleviated using the electric trim switches on each control yoke, which adjusts the position of the THS. Electric trim is available in manual flight or when the autopilot is in the Command Wheel Steering (CWS) mode.
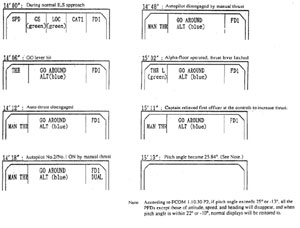
View Larger
- Auto Trim: Auto trim is a function activated by the autopilot which commands the THS based on the command mode of the autopilot.
- Override Function: The pitch trim modes can all be overridden by manual movement of the pitch trim wheel located in the center console of the flight deck. Movement of this wheel is designed to disconnect the pitch trim system and allow pilots to override the THS.
- Flight Envelope Protection /Alpha Floor Protection: This function is intended to protect the aircraft from stall by automatically providing maximum thrust when excessive AOA is detected. When alpha floor is engaged, "THR L" (throttles latched) is indicated on the Flight Mode Annunciator (FMA) on the pilots' primary flight display and the throttle levers move forward towards maximum thrust at a rate of eight degrees per second.
The Thrust Control Computer (TCC) and Auto Throttle System (ATS) provide thrust commands to the engines based on throttle position and/or signals to maintain the thrust limit or a target thrust. The flight crew can override the auto thrust system and control the engines manually by light control pressure on the throttle levers.
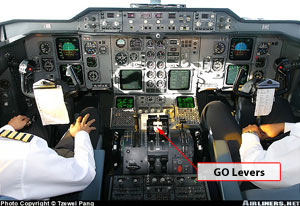
Photo copyright Tzewei Pang - used with permission
View Larger
The Flight Control Computer (FCC) provides the functions of the autopilot/flight director (AP/FD) in a variety of modes (basic, altitude, level change, profile, heading select, navigation, VOR, LOC, takeoff, land, and go-around modes). AP/FD mode is selected by the crew through push buttons located on the Flight Control Unit (FCU) just below the glare shield. Of the several AP/FD modes available, the following are important to this accident:
- Land mode: Land mode is designed to capture ILS glide slope, guiding the aircraft to the runway axis and to flare. Land mode is engaged through the land pushbutton on the FCU with the following conditions met:
- Radio altimeter height greater than 400 feet above ground level
- ILS frequency and runway course selected on ILS control panel
Land mode is disengaged by any of the following:
- Selection of go-around mode
- Pressing the land mode button again
- Selecting another AP/FD mode on the FCU
- Go-around mode: Go-around mode was designed to provide both lateral and longitudinal guidance during the execution of a go-around maneuver. ATS is automatically engaged and longitudinal guidance is provided to maintain the reference speed. This mode is also designed to maintain wings level. Go-around mode is activated by triggering the GO levers on the throttles so long as slats/flaps are extended to at least 15 degrees. Go-around mode may be disengaged by selecting another AP/FD mode except for land mode.
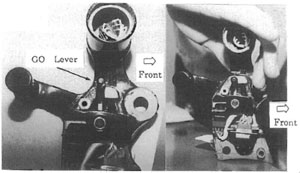
Autopilot Override Function: At the time of this accident, the design of the A300 auto-flight system would disconnect the autopilot if the pilot applied manual pitch inputs to the control wheel greater than 15 kilograms (33 pounds) in all modes except land and go around. In land and go-around modes the system was designed to allow the pilot to override autopilot elevator control. However, this action would not disconnect the autopilot control of the THS regardless of the control force applied. The Flight Crew Operating Manual (FCOM) explained, "This override was conceived in order to protect the pilot against AP abnormal behavior." The FCOM also included the following caution:
"On the longitudinal axis, the autopilot override does not cancel the AP auto-trim orders. So with the AP in CMD, if the pilot counteracts the AP (elevators order) the AP will move the THS (auto-trim order) so as to maintain the A/C on the scheduled flight path. A risk of out of trim is real - and may lead to a hazardous situation in land and go-around mode only."
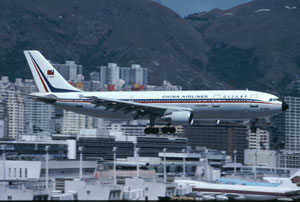
THS-in-motion Flight Crew Awareness/Warning
The design of the A300 provides the following to inform/warn the crew of movement of the THS:
- Visual trim indicators located on the center pedestal which display current position of the THS.
- Manual pitch trim control wheels (one on each side of the pedestal) which contain both position markings and turn according to THS movement.
- THS motion warning which provides an aural warning during periods of use of the electric pitch trim switches located on each control yoke.
As cited in the accident report, both the visual indicators and manual pitch trim wheels are outside the pilot's field-of-view while looking forward along the aircraft's flight path and may be difficult to accurately read in a darkened flight deck as was the case for this nighttime approach. Additionally, by design, the THS aural warning was inhibited during the approach because the autopilot was engaged in a command mode. The accident board concluded that there was inadequate warning or recognition capability for the flight crew to be alerted to the movement of the THS to an abnormal, out-of-trim condition as the flight crew attempted to maintain the approach glide path.
Pitch Effects Due to Thrust
For aircraft with engines below the wing, as is the case with the under-wing mounted engines of the A300, a rapid increase in thrust creates a significant increasing pitch. While the crew was struggling to manually reduce pitch during the approach, the activation of the alpha-floor function, resulting thrust increase, and positive pitch moment further compromised the flight crew's ability to control pitch. As the captain took over control and attempted a go around, the further increase in thrust by the ATS, coupled with the out-of-trim THS, quickly overcame the manual control authority on the elevator and allowed for a severe increase in pitch attitude and accompanying rapid increase in AOA towards stall.
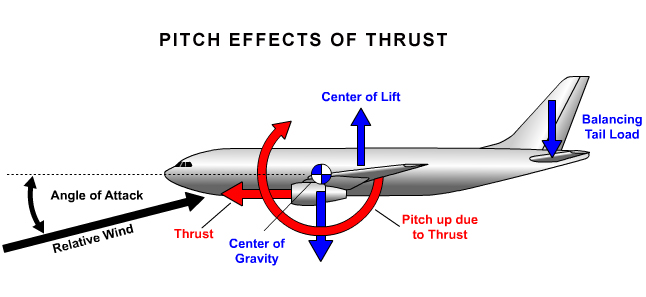
Crew Resource Management
The investigation concluded that effective crew resource management was not practiced by the crew. Areas identified by the investigation involved task sharing, standardization of terms used for instruction, response, confirmation and execution of operations, in order to assure that crews maintain appropriate situational awareness. Further identified by the investigation was the manner in which the captain assumed control of the airplane, and a lack of preflight discussion and agreement as to the situations where it might be appropriate for the captain to assume control.
This and several other accidents involving human errors in using aircraft automation sparked increased focus on consideration of human factors and automation in the design of transport aircraft.
FAA Human Factors Team Report
In 1994 the FAA launched a study to evaluate all flight crew/flight deck automation interfaces of current generation transport category airplanes. The FAA chartered a human factors team to conduct the study. Team members included experts from the FAA, the European Joint Airworthiness Authorities (JAA), and academia. The objective of the study was to examine the contributing factors from the perspective of design; flight crew training and qualifications; operations; and regulatory processes. The FAA also tasked the team to develop recommendations to address any problems identified.
- Pilot/autopilot interactions that create hazardous out-of-trim conditions
- Autopilots that can produce hazardous speed conditions and may attempt maneuvers that would not normally be expected by a pilot; and
- Insufficient wording in the Airplane Flight Manual regarding the capabilities and limitations of the autopilot.
The full text of this team's report issued in 1996 is available at the following link: (FAA Report: Flight crew Interfaces and Modern Flightdeck Systems).
The Aircraft Accident Investigation Commission of the Ministry of Transport of Japan conducted the accident investigation and focused primarily on flight crew error; specifically, continuing to fly the ILS approach with the auto flight system with go-around mode engaged.
The commission found that while manually flying the approach, the first officer inadvertently activated the GO lever on the throttles, causing a thrust increase and placing the flight director in go-around mode. The aircraft's autopilot was subsequently engaged, driving the Trimmable Horizontal Stabilizer (THS) to its full nose-up position against the first officer's nose-down yoke/elevator manual control inputs as he attempted to maintain glide path.
The flight crew, unaware of the conflict between THS and elevator control, continued the approach with a subsequent increase in AOA and eventual triggering of the alpha floor function, increasing thrust and pitch. Shortly after the captain took control in this mis-trimmed condition, a go around was attempted. The increase in thrust caused a rapid pitch-up and further increase in AOA. The flight crew was unable to conduct an effective recovery and the aircraft stalled and crashed.
The complete findings are available at the following link: Accident Investigation Commission Causes
The complete accident report is available at the following link: Accident Report
Aircraft Accident Investigation Commission of Japan
The accident investigation commission made several recommendations. Most notable were recommendations in the following areas:
1. To the Taiwanese civil aviation authorities and China Airlines to reinforce their flight crew training program in the following areas:
- Understanding of the design concept and establishment of operational concepts for advanced technology aircraft.
- Improved education and training regarding the Automatic Flight System.
- Review of Crew Resource Management and crew coordination particularly when the first officer is performing as the pilot flying.
2. To the airworthiness authorities of France and Airbus:
- Review and improvement of the A300-600R auto flight system to incorporate the following:
- Autopilot disconnect and override function.
- Out-of-trim protections resulting from prolonged override of the autopilot in the pitch axis.
- Improved warning and flight crew recognition of THS movement.
- Improvement of the Flight Crew Operating Manual descriptions of the A300-600R autopilot manual override, disengagement of go-around mode, and recovery procedures for an out-of-trim condition.
- Review of the auto flight system in the context of flight crew behavior and abilities (human factors) in emergency or abnormal situations.
The complete text of Aircraft accident Investigation Commission's recommendations can be found at the following link: Accident Investigation Commission Recommendations.
National Transportation Safety Board (NTSB)
The NTSB made the following three recommendations to the FAA as a result of this accident:
- Require operators of the Airbus A-300 and A-310 series airplanes to provide immediate and recurrent training to flight crews on the hazard of attempting to counter autopilot commands by manual control forces when the airplane is being flown with the autopilot engaged in the land or go-around mode. (Class 11, Priority Action) (A-94-164)
- Review the logic of the Airbus A-300 and A-310 series automatic flight control systems and require modification as necessary so that the autopilot will disconnect if the pilot applies a specified input to the flight controls or trim system, regardless of the altitude or operating mode of the autopilot. (Class 11, Priority Action) (A-94-165)
- Require modification of Airbus A-300 and A-310 series autopilot systems to ensure that the systems provide a sufficient perceptual alert when the trimmable horizontal stabilizer is in motion, irrespective of the source of the trim command. (Class E, Priority Action) (A-94-166)
The complete text of the NTSB letter to the FAA is available at the following link: NTSB Safety Recommendations.
The following were the relevant certification regulations relating to autopilot and flight director at the time the A300-600R was certified:
14 CFR 25.1329 (Historical) Automatic Pilot System
14 CFR 25.1335 (Historical) Flight Director Systems
Information regarding the function of the automatic flight control system, particularly the flight director mode changes and the autopilot override and supervisory functions, were not clearly understood by aircraft operators and flight crews. As a result of previous incidents involving flight crew manual command against autopilot pitch commands, Airbus had developed a service bulletin (SB A300-22-6021, June 4, 1993) which would alter the flight control computers such that the autopilot would disengage with a control column force of greater than 15 kilograms in go-around mode above 400 feet.
However, the manufacturer's classification of this service bulletin as 'recommended', citing operational benefits and/or passenger comfort, and not having been rendered mandatory by an airworthiness directive, resulted in China Airlines failing to recognize the importance of the change. China Airlines chose to defer incorporating this change to the flight control computers until later maintenance was required. As a result, the accident aircraft had not yet had this recommended change incorporated.
- Long term manual control inputs with the autopilot engaged, resulting in conflicting control inputs and stabilizer mis-trim.
- It was assumed the flight crew would not make long-term or continuous-control inputs while the auto flight system was engaged.
- March 1, 1985 - A300
An A300 descending in the approach phase with autopilot engaged in the command mode reached the selected altitude causing the ALT acquire and subsequently the ALT hold modes to engage. The crew, in an effort to continue the descent, applied nose-down elevator inputs, overriding the autopilot commands. As the aircraft descended below the selected altitude of 4,200 feet, the auto-trim function commanded nose-up movement of the THS as the autopilot attempted to regain the selected altitude. Eventually the THS moved to its full nose-up position with the elevator manually controlled to the full nose-down position. Because of the greater control power of the THS, the aircraft pitched up to 10 degrees nose high. The thrust was briefly reduced by the crew, in a probable attempt to reduce the pitch attitude, but then led to a decrease in airspeed to approximately 119 knots. To correct the loss of airspeed, thrust was subsequently increased, which combined with the mis-trimmed THS, led to a pitch attitude of 24 degrees nose up. As the aircraft climbed, a change in the autopilot mode allowed the auto trim function to command the THS nose down and subsequent manual nose-down pitch commands by the crew disengaged the autopilot and the aircraft was safely recovered.
- January 9, 1989 - A300-B4 -- Helsinki, Finland
While on approach and passing approximately 860 feet, the captain inadvertently triggered the GO-levers, placing the auto flight system in go-around mode. The pilot disconnected the auto throttles, reduced the throttles, and pushed forward on the yoke to prevent a pull up causing the autopilot to activate the auto trim system to command nose-up movement of the THS opposite the manually commanded elevator nose-down movement. As the THS reached eight degrees nose down, the captain disengaged the autopilot. As he applied nose-down control inputs, the aircraft leveled at approximately 750 feet. The pilot subsequently selected the auto throttle go-around mode, and the increasing thrust caused the aircraft to pitch up and begin to climb, eventually reaching an altitude of 2,250 feet, pitch attitude of over 35 degrees nose-up, and speed decrease to 94 knots. The captain did not use electrical trim but used the manual trim control wheel in the nose-down direction to eventually recover aircraft to normal flight at 1,540 feet.
- February 11, 1991 - A310 - Moscow, Russia
While on approach with autopilot engaged, the crew was instructed to execute a go-around by air traffic control, passing approximately 1,550 feet with a specified go-around altitude. The crew pre-selected 2,260 feet as the go-around altitude and selected the go-around mode at approximately 1,275 feet. In order to reduce the nose-up attitude commanded by the autopilot as it shifted into go-around mode, the pilot pushed the yoke forward commanding nose-down elevator movement. As a result of these opposing commands, the THS reached its 12-degree nose-up position while the manually controlled elevator reached a nose-down position of 14 degrees. As the aircraft climbed through 1,500 feet, the autopilot shifted to ALT acquire mode while the crew continued to push nose-down on the yoke, leading to a disengagement of the autopilot with the THS in an extreme nose-up position. This, combined with the high thrust commanded for the climb, led to a rapid pitch up to approximately 88 degrees nose high as airspeed decreased to 30 knots and an aircraft stall at approximately 4,300 feet. The aircraft pitched over, descended to approximately 1,400 feet, then began another steep climb, repeating a cycle of stall, descent, and steep climb. On the fourth cycle the aircraft reached an altitude of 11,755 feet. During this period the crew believed the autopilot was still engaged and did not recognize the mis-trimmed position of the THS. The aircraft was recovered after the fourth cycle as the crew reduced thrust in the dive and involuntarily activated electric nose-down trim on the subsequent climb, eventually regaining controlled flight at approximately 8,700 feet.
Human Factors Policy and Regulatory Changes
This and several other accidents involving human error sparked increased focus on consideration of human factors and automation in the design of transport aircraft.
In 1994, the FAA launched a study to evaluate all flight crew/flight deck automation interfaces of current generation transport category airplanes. The FAA chartered a Human Factors Team to conduct the study. Team members included experts from the FAA, the European Joint Airworthiness Authorities (JAA), and academia. The objective of the study was to look beyond the label of "flight crew error," and examine the contributing factors from the perspective of design; flight crew training and qualifications; operations; and regulatory processes. The FAA also tasked the team to develop recommendations to address any problems identified.
With regard to autopilot issues, the Team identified several specific problematic issues, including:
- Pilot/autopilot interactions that create hazardous out-of-trim conditions
- Autopilots that can produce hazardous speed conditions and may attempt maneuvers that would not normally be expected by a pilot; and
- Insufficient wording in the Airplane Flight Manual regarding the capabilities and limitations of the autopilot.
The full text of this team's report issued in 1996 is available at the following link: (FAA Report: Flight crew Interfaces and Modern Flightdeck Systems).
Additionally, the FAA issued two policy documents regarding human factors in aircraft certification:
- ANM-99-2, Guidance for Reviewing Certification Plans to Address Human Factors for Certification of Transport Airplane Flight Decks (ANM-99-01)
- ANM-01-03A, Factors to Consider when Reviewing an Applicant's Proposed Human Factors Methods of Compliance for Flight Deck Certification (ANM-01-03A)
In early 2011, the FAA issued a proposed change to 14 CFR 25.1302, Installed Systems and Equipment for Use by the Flight crew, and accompanying Advisory Circular, AC 25.1302-1 (NPRM 14 CFR25.1302 and AC 25.1302-1, DRAFT) which will amend design requirements in the airworthiness standards for transport category airplanes to minimize the occurrence of design-related flight crew errors and enable a flight crew to detect and manage their errors when they occur.
Auto Flight Systems Policy and Regulatory Changes
This accident, as well as other incidents and accidents that have occurred worldwide involving pilot-autopilot interactions, emphasized to the FAA the need to re-examine the current certification policy relative to autopilot issues. In 1999 the FAA issued policy concerning how the FAA would evaluate various items when certifying automatic pilot installations in transport category airplanes.
The full text of this policy is available at the following link: (ANM-99-01, Improving Flight crew Awareness during Autopilot Operation). This policy memo has since been canceled and replaced with the advisory circular noted below.
The FAA also undertook a rulemaking effort to update its regulations and certification guidance regarding Flight Guidance Systems. The full text of the current regulation and associated advisory circular are available at the following links:
- 14 CFR 25.1329, Flight Guidance Systems
- AC25.1329-1B, Approval of Flight Guidance Systems
Changes to Stall Recovery Technique Training
This and other past accidents and incidents, have led to an FAA-industry collaborative review of stall recovery techniques and training. Previous stall recovery training emphasized increasing thrust and minimizing altitude loss during recovery. The emphasis is now on reduction of Angle of Attack (AOA) as the most important aspect of stall recovery. As a result of this accident, and other accidents and incidents involving stall and loss of control (LOC), it is now recommended that pilot training and evaluation emphasize as the first steps in stall recovery in any aircraft: the disconnection of the autopilot and autothrottle, followed by application of nose-down pitch control to reduce AOA until the stall warning is eliminated. Nose down pitch trim should be used as needed, wings should be leveled, and thrust should carefully be applied as needed for recovery, noting that maximum power is not always required and should not be the first step in the stall recovery. Additionally, speed brakes/spoilers should be checked for retraction as the plane is returned to the desired flight path. (FAA AC 120-109: Stall and Stick Pusher Training, Flight Safety Foundation: Rebuilding Stall Defenses, Airbus Telex: Stall Recovery Procedure, Transport Canada: Training and Checking Practices for Stall Recovery
The French Direction Generale de l'Aviation Civile (DGAC) issued airworthiness directive (AD) CN94-185-165(B) (EASA_AD_F-1994-185-165R2) on August 17, 1994, requiring flight manual revisions and modification of the flight control computers (FCC) to prevent abnormal out-of-trimmed conditions arising from prolonged override of the autopilot commands in the pitch axis via the control yoke. In December 1994 Airbus re-categorized previously issued service bulletin A300-185-165(B) from "recommended" to "mandatory" in accordance with this AD.
The FAA issued AD 94-21-07 on November 2, 1994, requiring:
- Within 10 days, revision of the limitations section of the AFM to emphasize the hazards of manual control overriding the autopilot commands.
- And, within 60 days, required modification of the FCCs in accordance with Airbus Service Bulletin (SB) A300-185-165(B) that allowed the autopilot to disconnect at 15 kilograms (33 pounds) in the land or go-around modes.
This AD was later superseded by AD 98-17-09.
Airplane Life Cycle:
- Design / Manufacturing
- Operational
Accident Threat Categories:
- Incorrect Piloting Technique
- Crew Resource Management
- Flight Deck Layout / Avionics Confusion
Groupings:
- Loss of Control
- Approach and Landing
- Automation
Accident Common Themes:
- Human Error
- Organizational Lapses
Organizational Lapses
There had been previous, similar A300 incidents in which flight crew had made manual control inputs against the auto flight system resulting in a trimmable horizontal stabilizer becoming out of trim. While Airbus had provided operators with a summary of these incidents, the accident report concluded that they did not present sufficient technical and background details for operators to fully understand this hazardous condition. In response to these previous incidents, Airbus had developed a modification to the auto-flight system which would cause the autopilot to disengage if 15 kilograms (approx. 33 pounds) was applied to the yoke, and they issued a service bulletin (SB A300-22-6021) in 1993. However, the service bulletin was categorized as "recommended". Because the service bulletin was not mandated by an AD, China Airlines judged the changes not to be urgent, and elected to defer the SB implementation to a time when the flight control computers needed repair. As a result, the accident aircraft had not yet had this change to the auto flight system incorporated.
Human Error
During an ILS approach, the first officer (pilot flying) inadvertently activated the GO Lever on the aircraft throttles. He later engaged the autopilot, which placed the automation in the go-around mode, and the airplane went above glide path. However, the pilot flying continued to try to correct with nose-down elevator and manually reacquire the glide slope. He left the autopilot connected and continued to apply increasing nose-down elevator commands, counter to the auto flight system's increasing nose-up commands to the THS. The position of the THS was consistent with the go-around mode, that is, a nose-up command. The crew did not recognize this increasingly mis-trimmed condition, and when the captain took the controls in an attempt to salvage the approach, he was surprised by the large, nose-up control force. Recognizing that a safe landing could not be performed, the captain attempted a go around and advanced the throttles. The increasing thrust effects (pitch up) combined with the mis-trimmed THS (in the nose-up direction) overcame the available elevator control authority and led to a severe pitch up of the aircraft. This pitch up resulted in rapidly decreasing airspeed and an increasing AOA until the aircraft stalled.
United Airlines Flight 227, Boeing Model 727-22, November 11, 1965
United Airlines Flight 227, a Boeing 727, crashed during an attempted landing at Salt Lake City Airport. The captain failed to recognize and arrest an excessive sink rate on final approach, resulting in a touchdown 335 feet short of the runway. The main landing gear sheared off, causing a breach in the fuselage. The airplane caught fire while sliding down and off the right side of the runway. Failure of the main landing gear ruptured fuel lines and generator leads, causing the fire. The entire roof and cabin area forward of the fuselage breach was consumed by fire. Of the 85 passengers aboard, there were 43 fatalities. All six crew members survived. The Civil Aeronautics Board (CAB) determined that the accident was survivable - none of the passengers sustained any traumatic injuries that would have precluded their escape. The 43 fatalities were attributed to the fire caused by the broken fuel line. The CAB also established that similar future events could not be ruled out, and that the airplane should be designed to have a higher degree of survivability in these types of events.
See accident module
Air France Flight 072, Boeing 747-428B, September 13, 1993
Air France Flight 072, a flight from Los Angeles, California to Tahiti, was assigned the VOR DME approach to runway 22 at Faa'a International Airport. It was night and the weather conditions were clear. The airplane was on a stabilized approach in the landing configuration with the autopilot disconnected and auto throttles engaged. At the missed approach point, the automatic flight system initiated a go-around. The pilot of the aircraft physically held the throttles back with his hand, countermanding the automatic flight system, and continued the approach. During landing the thrust lever for the left outboard engine slipped out of the pilot's hand and commanded by the automatic flight systems, increased to full forward thrust. During the landing rollout, the thrust asymmetry generated with multiple engines in reverse thrust and one engine at forward takeoff thrust caused the airplane to veer to the right and depart the runway on the right-hand side, near the end, coming to rest in a lagoon adjacent to the runway. All passengers were successfully evacuated with only four minor injuries.
See accident module
American Airlines Flight 1420, MD-82, June 1, 1999
Shortly before midnight on the evening of June 1, 1999, American Airlines Flight 1420 crashed after it overran the end of runway 4R during landing at Little Rock National Airport in Little Rock, Arkansas. After departing the end of the runway, the airplane struck supporting structure for the instrument landing system localizer array located 411 feet beyond the end of the runway, continued through a chain link fence and over a rock embankment into a flood plain, where it came to rest after colliding with the runway 22L approach lighting support structure. The captain and ten passengers were killed. The first officer, flight attendants and 105 passengers received serious or minor injuries, and 24 passengers were not injured. The airplane was destroyed by impact forces and a post-crash fire.
The National Transportation Safety Board (NTSB) determined that the probable causes of this accident were "the flight crew's failure to discontinue the approach when severe thunderstorms and their associated hazards to flight operations had moved into the airport area and the crew's failure to ensure that the spoilers had extended after touchdown. Contributing to the accident were the flight crew's (1) impaired performance resulting from fatigue and the situational stress associated with the intent to land under the circumstances, (2) continuation of the approach to a landing when the company's maximum crosswind component was exceeded, and (3) use of reverse thrust greater than 1.3 engine pressure ratio after landing."
See accident module
Technical Related Lessons
If continuous or protracted manual override of an automatic flight control system becomes necessary, it should be accompanied by manual disengagement of the system. (Threat Category: Incorrect Piloting Technique)
- Early in the accident sequence, the auto throttles were inadvertently engaged, resulting in a thrust increase, and a change in flight path that deviated above the ILS glide slope. Later in the accident sequence, the autopilot was also engaged, and as the auto throttle was in go-around mode, the autopilot also engaged in go-around mode, and commanded a pitch increase commensurate with a go-around. Subsequent manual control inputs in opposition to autoflight system control inputs resulted in a severe mistrim condition and a loss of control. At the time of the accident, the A300 Flight Crew Operating Manual stated, "If any abnormal behavior is suspected when AP is in CMD, disconnect the autopilot immediately. CAUTION: Do not attempt to modify the aircraft path by acting on the flight controls, if AP is not disconnected."
Common Theme Related Lessons
The consequences of manually overriding an automatic flight control system, and the associated effects on airplane control and flight path stability, should be fully understood by the flight crew. (Common Theme: Human Error)
- At the time of this accident, in all modes except land and go-around modes, the autopilot on the A300 would disconnect with manual application of a 15 kilogram to the control column. In the landing modes, there was no provision for an automatic disconnect following manual application of column force, regardless of the manual forces applied. The investigation concluded that the flight crew did not adequately understand the autopilot design provisions regarding automatic disconnections, or the effects of manual control inputs while the auto flight systems remained engaged. The investigators believed that had the flight crew fully understood the effects, the autopilot would have been manually disengaged and the approach or go-around continued manually, thus avoiding the accident.