Concorde
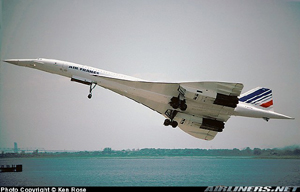
Photo copyright Ken Rose - used with permission
Air France Flight 4590, F-BTSC
Paris, France
July 25, 2000
Air France Flight 4590 was a charter flight from Paris Charles de Gaulle Airport, France, to New York's John F. Kennedy International Airport, New York City. There were 100 passengers and nine crewmembers on board. The fully loaded Concorde began taxing towards runway 26 at approximately 1434 local time. Weather at the time of the accident was clear, and winds light. Takeoff began at approximately 1442 with planned target speeds of V1 of 150kts; VR of 198 kts; and V2 of 220 kts. The takeoff progressed normally until a few seconds after passing through V1. It was learned by investigators that at that point, one of the tires on the left main landing gear (tire No. 2) struck a small piece of sheet metal that had fallen from the No. 3 engine of a DC-10 that had taken off five minutes earlier. The No. 2 tire immediately failed, sending debris into the underside of the airplane and left wheel well. It was determined that the largest tire debris did not penetrate the wing surface but generated a high-pressure surge within the No. 5 fuel tank, resulting in at least three areas of tank surfaces failing outward, and generating a massive fuel leak.
The fuel leak, located forward and inboard of the nos.1 and 2 engine inlets, almost immediately ignited. The takeoff continued, although the ground track began drifting to the left side of runway 26. The pilot rotated the airplane as it passed over the left edge of the runway. After liftoff, engines 1 and 2 began to malfunction, with no 2 being more severe. Within a few seconds following liftoff, the fire warning alarm sounded on No. 2, resulting in it being shut down by the crew. The plane climbed to an altitude of approximately 200 feet, and airspeed of approximately 200 kts, but was unable to accelerate or climb. After about 60 seconds, no 1 engine began to fail, followed by decay in airspeed and the inability to maintain level flight. The airplane stalled and crashed into a hotel approximately 90 seconds from the beginning of the takeoff roll, killing all 109 passengers and crew on board, and four persons on the ground.
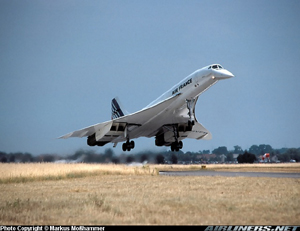
Photo copyright Markus MoBhammer - used with permission
The Concorde
The Concorde was one of only two supersonic transport airplanes to have entered commercial service: the other being the Tupolev Tu-144. The product of a joint development and manufacturing effort by British Aircraft Corporation (BAC) of the United Kingdom, and Aerospatiale of France throughout the 1960s and 1970s, the first aircraft entered service in 1976. The aircraft was designed to fly at cruise speeds of twice the speed of sound, or a Mach number of approximately 2.0, and cruise at altitudes of up to 60,000 feet, substantially higher than conventional subsonic aircraft cruising in the 30,000 to 40,000 foot range. Technical and economic challenges to the Concorde resulted in only 20 aircraft being produced, and it was retired from service in 2003. At the time of the Air France accident in 2000, the Concorde had not experienced a single accident involving a fatality during its nearly 25 years of service.
History of Flight
On July 25, 2000, Concorde registered F-BTSC, operated by Air France as a charter flight, AFR 4590, was scheduled to fly from Paris Charles de Gaulle to New York. There were 100 passengers, six cabin crew members, and three flight crew members on board. The captain in the left seat was the pilot flying (PF) and the first officer was the Pilot Not Flying (PNF). The accident aircraft had been out of service between July 17 and 21 for scheduled A01 checks involving removal of certain main landing gear components, and tire inflation detection system checks. Following this maintenance, four flights were conducted between July 21 and July 24. On July 25, F-BTSC was planned to be a "reserve" aircraft for a regularly scheduled Air France Flight 002, but due to the unavailability of other Concorde aircraft, this aircraft was selected for the charter flight to New York.
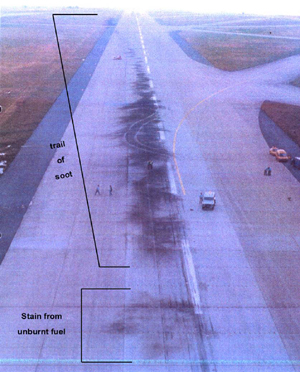
Available records indicated that the aircraft's total weight was 186.9 tons, with 95 of fuel. Based upon these weights and airport conditions, the aircraft takeoff speeds selected were V1 of 150 kts, VR of 198 kts, and V2 of 220 kts. Since this was near maximum weight for the Concorde, the crew requested and was granted permission to use the entire length of runway 26. Winds were generally light at 8 kts, runway conditions dry, and visibility generally clear at 15 km.
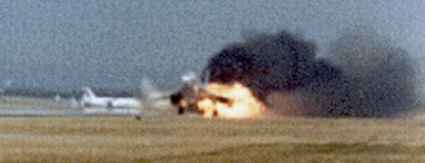
The takeoff began at 14h 42min 31s and progressed normally for most of the takeoff roll. A few seconds after passing through V1, investigators determined that at that point the No. 2 main landing gear tire passed over a piece of metal debris that had fallen from a DC-10 aircraft that had taken off from runway 26 five minutes earlier. The metal debris destroyed No. 2 tire, resulting in segments of the tire striking the underside of the Concorde's left wing. It was concluded by the investigation that the large segment of tire debris found on the runway after the accident did not penetrate the tank, but rather deformed an area of the No. 5 fuel tank, producing a mechanical process within the fuel tank referred to as a "hydrodynamic pressure surge." It was concluded that this pressure surge caused an area of the No. 5 fuel tank lower surface to fail outwards. This tank segment, approximately 32 cm square, completely separated from the wing surface, and was found by investigators lying on runway 26 along with pieces of the failed tire. One of these tire pieces weighed nearly 5 kgs.
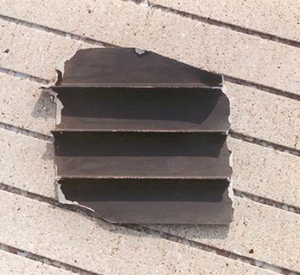
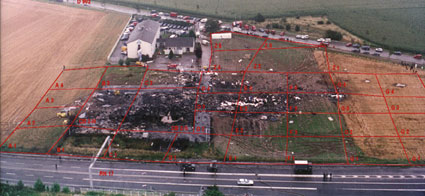
View Larger
The failed area of the lower wing skin of the No. 5 main fuel tank immediately began leaking massive amounts of fuel. The involved area was slightly inboard, and slightly forward of the No. 1 and 2 engine inlets. Leaking fuel almost immediately ignited. It was believed by investigators that electrical arcing from wires within the left main landing gear wheel well was most likely the source of the ignition of the leaking fuel.
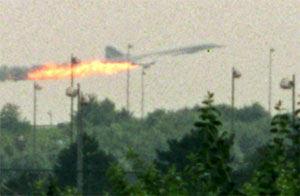
The takeoff was continued, and engines 1 and 2 immediately began to malfunction, with No. 2 being more severe. The takeoff track began to drift to the left, and the pilot rotated as the plane passed over the left-hand edge of the runway, at a speed of approximately 200 kts. The fire warning system for the No. 2 engine sounded a few seconds after liftoff, followed by it being shut down by the crew. Although the crew then attempted to raise the gear, it was believed by investigators that damage to the landing gear system prevented the gear from moving to the stowed position. The plane remained at an airspeed of approximately 200 kts, an altitude of 200 feet, and was unable to accelerate or climb. Approximately 90 seconds from the beginning of the takeoff, the No. 1 engine then failed, resulting in the plane crashing into a hotel, killing all 109 passengers and crew on board, 4 persons on the ground, and injuring six.
See an animation of Flight 4590 flight path and events leading up to the accident:
History of Previous Concorde Tire and Wheel Failures
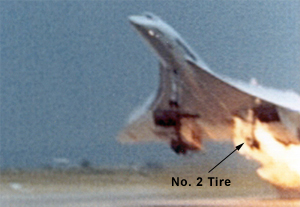
Based upon evidence gathered from the accident site, as well as debris and other evidence from runway 26 following the flight, investigators determined that the sequence of events leading to the accident involved four main conclusions. These four were: (1) a piece of metal debris from an earlier departing DC-10 had been struck by, and failed, the No. 2 tire of Air France Flight 4590; (2) as a result of the No. 2 tire disintegration, tire fragments impacted the lower wing surface; (3) due to being struck by high energy tire fragments, the No. 5 fuel tank experienced a major rupture, leading to a massive fuel leak, ignition and fire; and (4) as a result of a massive in-flight fire, subsequent damage to remaining structure and systems resulted in loss of control of the airplane and the accident.
Although investigators learned that there had been previous tire failures experienced on the Concorde fleet, what was believed to be unusual in this case was the magnitude of the tank damage, and the level of the fuel leak involved. Research was conducted in order to gather information concerning the previous failures, and to better understand the factors leading to these failures. Based upon analysis of available service information, it was learned that there had been 57 previous tire burst/deflation events since the introduction of the Concorde in 1976.
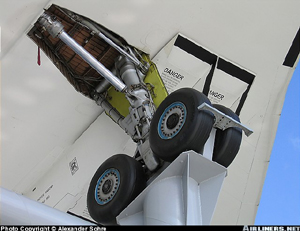
Photo copyright Alexander Sohre - used with permission
Of these events, investigators determined that:
- 12 of these events had structural consequences on the wings and/or the tanks, of which six led to penetration of the tanks.
- 19 of the tire bursts/deflations were caused by foreign objects.
- 22 events occurred during takeoff.
- Only one case of tank penetration by a piece of tire was noted.
- None of the events identified showed any rupture of a tank, a fire, or significant simultaneous loss of power on two engines.
As a result of tire and wheel failures that had been experienced in the late 1970s and early 1980s, several safety initiatives were undertaken in order to improve the reliability of tires and wheels, and to reduce the risks to the airplane when the tire failures occurred. In particular, a concern existed relative to the risks associated with a cascading, double tire failure, leading to wheel failures and risks to fuel tank integrity following disintegration of wheels. These fleet-wide improvements were introduced in the early 1980s by airworthiness directive actions and had been incorporated into the Air France Concorde fleet, including F-BTSC.
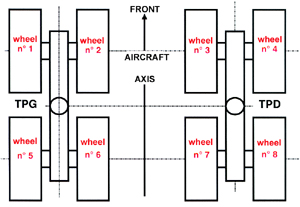
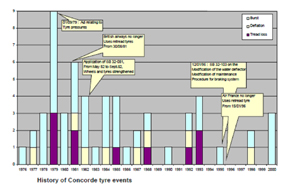
View Larger
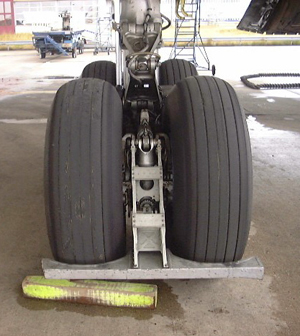
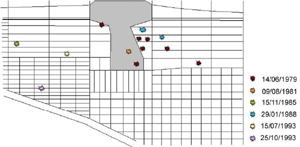
View Larger
Based upon review of previous service experience, investigators concluded that the earlier safety initiatives intended to improve the reliability of the Concorde's tires and wheels had been successful. It was also learned that no failure had occurred similar to what had been experienced on Flight 4590.
Maintenance Performed on the Left Main Landing Gear
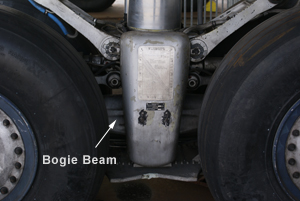
Between July 17 and 21, 2000, investigators learned that Air France had performed a scheduled A01 check in accordance with their approved maintenance program. During this check, the left main landing gear bogie beam was removed and replaced in order to correct an acceptable deferred defect related to the under-inflation detection system.
During the course of examination of wreckage and review of maintenance records, it was discovered by investigators that a part of the bogie assembly had been inadvertently omitted during reassembly of the left main landing gear system. The missing part, a spacer, was not re-installed onto the internal assembly of the bogie beam axis. This spacer is needed in order to properly position inner and outer shear rings that are located at each end of the spacer and serve to properly align the landing gear lateral tracking of the wheels.
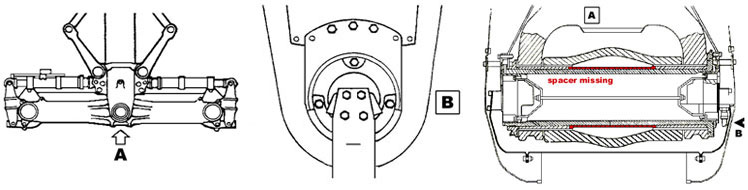
View Larger
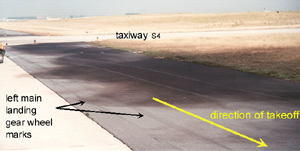
The effects of the missing spacer resulted in review of the potential impact on aircraft performance and takeoff ground trajectories. A detailed analysis was conducted which evaluated the various factors that could have resulted from this omission, and potential for shifting of the shear rings inside the bogie assembly. It had also been learned that there had been four revenue flights conducted following the landing gear removal and reinstallation. These flights were also reviewed for any signs of any takeoff trajectory or controllability problems. None were found.
Following this detailed review of possible effects of the missing landing gear bogie beam spacer, it was generally concluded by investigators that this missing part had no role in the accident. It was also concluded that the moderate trajectory drift to the left, beginning immediately following the #2 tire failure, was primarily a result of loss of thrust on the left side of the airplane, and effects of disturbed airflow in the area of the left wing from the fire.
DC-10 Thrust Reverser Wear Strip Found on Runway
Immediately following the accident, investigators recovered several items from runway 26. Included in these items were large pieces of tire debris, and a twisted piece of sheet metal that did not appear to belong to the Concorde. After extensive review and analysis of the sheet metal, it was determined that the piece of debris was a thrust reverser wear strip from a GE CF6 turbofan engine. It was also learned that a Continental Airlines DC-10, flight COA 55, had taken off from runway 26 five minutes prior to Flight 4590, and that this airplane was powered by GE engines.
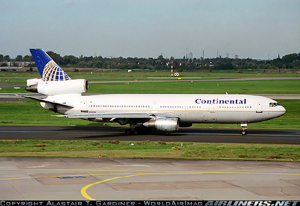
Photo copyright Alastair T. Gardiner (WorldAirImg) - used with permission
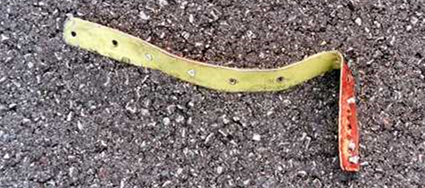
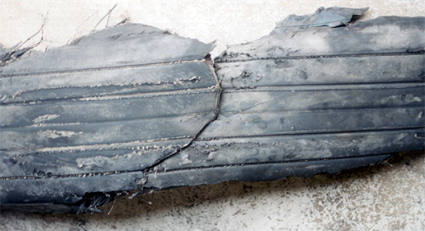
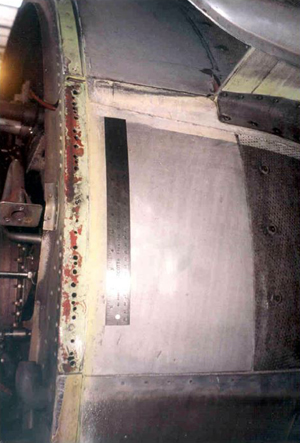
The DC-10 was located at a facility in the U.S. and examined by investigators. The #3 engine, a General Electric CF6-50, was observed to be missing a wear strip in the thrust reverser cowl area. This wear strip forms an air seal inside the thrust reverser cowl duct and is intended to provide a wearing surface during reverser deploy/stow operations. The rivet holes and other features observed on the aircraft matched the wear marks and other characteristics of the piece recovered from the runway. It was concluded by investigators that the piece recovered from runway 26 on July 25 came from the DC-10 being examined in the U.S. It was also concluded that Concorde's #2 tire of Flight 4590 had struck this piece of sheet metal during takeoff and resulted in destruction of the tire.
Maintenance Performed on the DC-10
Maintenance records for the DC-10 identified replacement of the left thrust reverser wear strips on engine #3 during a C check in June 2000, and an additional replacement of the left wear strips at another maintenance facility some time prior to July 25. This second maintenance activity on the DC-10 #3 engine was specifically to replace the thrust reverser wear strip, which was reported at the time as being twisted and sticking out of the cowl.
Maintenance instructions provided by the manufacturer were reviewed for repair or replacement of the wear strips. Detailed examination of the thrust reverser cowl area adjacent to the wear strip revealed 37 drill holes in the base support area of the reverser cowl. Examination of the recovered wear strip revealed 12 holes in the sheet metal part. It was concluded by investigators that a substantial amount of maintenance had been performed in this area prior to July 25. It was also learned that a repair to this area of the DC-10 would have been classified as a "minor repair" which would have permitted some degree of flexibility of steps permitted during the maintenance process. However, it was determined by investigators that the material used in the repair was a titanium/aluminum alloy sheet metal. Wear strip material called out in the instructions provided by the manufacturer indicated the strip be made from stainless steel sheet metal.
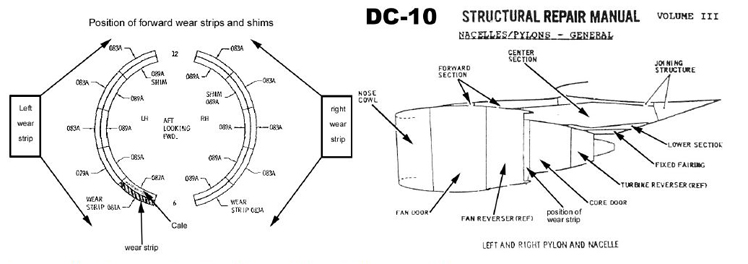
View Larger
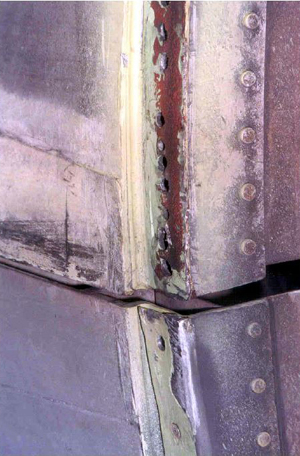
Failure of the #5 Fuel Tank
Examination of debris from the #5 fuel tank bottom recovered from runway 26 led investigators to conclude that a structural failure mechanism occurred on Flight 4590 that had never been experience on civil aircraft. In addition, extensive fire damage to the remainder of the wreckage of the left wing found at the crash site made it impossible to establish the exact location and number of tank openings. However, extensive studies and tank impact testing led to the conclusion that the general scenario of the tank rupture was most likely a result of at least two physical processes occurring simultaneously.
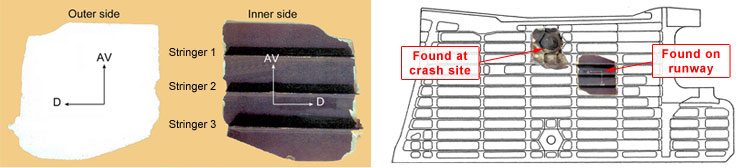
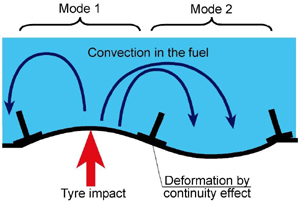
The first process, identified by investigators as the "Continuity Effect," is the behavior of a structural panel that experiences deformation inward from an external force, or in the case of the Concorde accident, the impact forces from the #2 tire failure. The deformation inward is accompanied by an outward rotation in the opposite direction in the panel area immediately adjacent to the inward deflection. The area where these two areas of panel are being deformed, but in opposite directions, is an area of localized highly strained material, and constitutes a "weakened" area of the tank bottom.
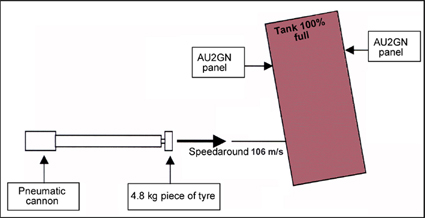
A second physical process believed by investigators to have contributed to the unusual outward failure mechanism observed on the #5 fuel tank structure is referred to as the "Hydrodynamic Pressure Surge." This involves a structural container with a fixed volume, filled with an incompressible fluid such as jet fuel. The container has little or no expansion space available to accommodate a change in volume, or fluid movement. If a surface of the container is suddenly subjected to a deformation that attempts to change the overall container volume, a sudden pressure rise is experienced throughout the container, and weakened areas of the tank structure, such as those formed by the "continuity effect" process, are potential areas of tank failure.
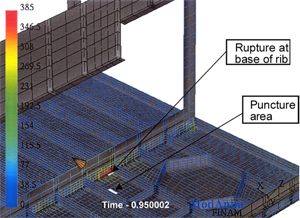
View Larger
Investigators believed that the completely full #5 fuel tank, combined with a sudden deformation of the tank bottom from the tire debris impact, most likely led to weakened area(s) of the tank bottom to fail outward, resulting in the massive fuel leak. It was also recognized by the investigation that the Concorde delta wing structural design, which consisted of relatively thin (less than 2mm minimum thickness) aluminum skin panels, rather than thicker flat aluminum sheets, as is common in conventional large transport wing designs, may have increased vulnerability in the areas weakened by the continuity effect. Although extensive testing was never able to exactly duplicate the precise failure mechanism, the data that was able to be gathered from these tests confirmed the results of theoretical studies.
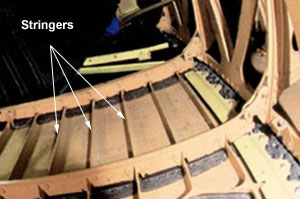
A tank failure animation, including a simplified high-speed video of the two physical properties described above, is available below:
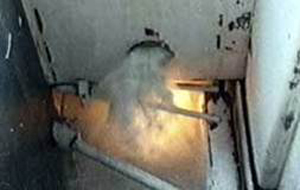
Additional Post-Accident Testing
In addition to fuel tank testing discussed above, additional post-accident testing was conducted in order for investigators to better understand the source of ignition for the leaking fuel, fuel leak propagation paths following the tank failures, and tire failure characteristics. These tests helped determine the likely progression of events during the period that the #2 tire contacted the thrust reverser wear strip, dynamics of the tire failure, and how leaking fuel became ignited underneath the airplane.
Based upon the results of these tests, it was concluded by investigators that the most likely source of ignition of the leaking fuel was due to electrical arcing from damaged wires in the wheel well area, not hot engine parts as was originally suspected. It was also established that, when the Concorde tire was subjected to conditions representative of the actual takeoff weights and speeds, striking a similar piece of sheet metal to the one recovered from runway 26 resulted in tire failures nearly identical to the tire fragments that were collected from the airport.
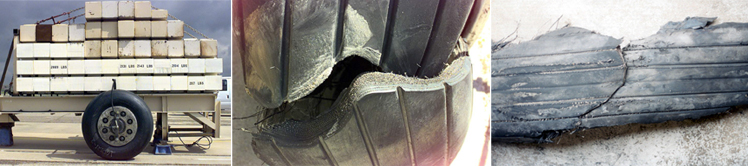
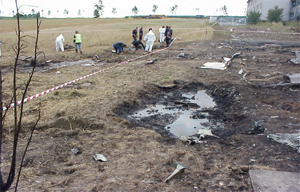
Conclusions
Failure of the Concorde's #2 tire on takeoff was due to striking a small piece of sheet metal that had fallen from a DC-10 that had taken off five minutes earlier. Following contact with sharp sheet metal, as determined by investigators to have occurred in this accident, this tire failure would not be considered to be unusual as there is no industry-wide regulatory requirement for aviation tires to be failure resistant to such threats. However, what was unusual was the extent of damage to the #5 fuel tank that this tire failure resulted in, and that this failure was of a type never experienced before in the history of civil aviation. After extensive analysis and testing, it was believed that this massive tank breach and fuel leak was the result of two complex physical processes occurring nearly simultaneously. These two conditions were (1) the "Continuity Effect," and (2) the "Hydrodynamic Pressure Surge." It was also concluded that this process was very much dependent upon the tank being completely full of an incompressible fluid (i.e., jet fuel), and sudden deformation occurring to the underside of the tank surface from tire debris impact.
Accident Memorial
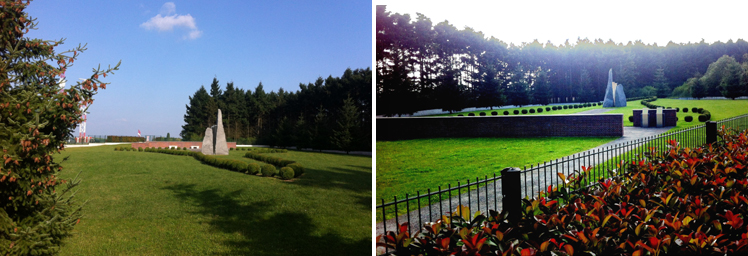
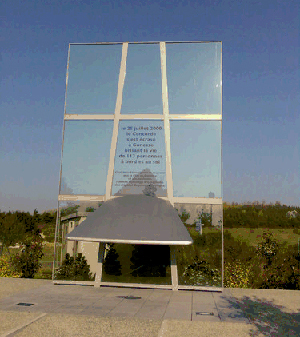
Photo copyright Olivier Ferrante - used with permission
Two independent memorials were created in memory of the victims of this accident.
The first was inaugurated on the sixth anniversary of the accident, on July 25th, 2006. It is located just outside the south perimeter road of the Paris Charles de Gaulle airport, exactly abeam of the position where the Concorde ran over the metal strip on runway 26R.
The memorial consists of 113 low bushes, one for each victim, arranged in the shape of a Concorde with the longitudinal axis aligned with runway 26R. A pathway, with metal plaques at each side inscribed with the names of the victims, leads to a rock and metal monument located in the center.
A second monument was built next to the field where the Concorde crashed, in Gonesse. This monument was funded by the local community through a public subscription. The opening ceremony was held on November 18th, 2006.
The main element of the monument is a rectangular 7-meter-high glass panel, pierced by an oblique steel plank. An inscription in French reads: "On July 25th, 2000, the Concorde crashed in Gonesse, taking the lives of 113 souls on board and on the ground. In sorrow and remembrance, the town of Gonesse and its inhabitants honor the memory of the victims of this catastrophe."
Investigators summarized the findings of the Concorde accident under Section 3.2 of the Accident Report. There were 36 Findings issued, ranging from flight crew qualifications to relevance of the debris that was recovered from the runway and crash site. All of the Findings can be viewed at the following link: Findings of the Accident Report.
3.2 Probable Causes
The accident was due to the following causes:
- High-speed passage of a tyre over a part lost by an aircraft that had taken off five minutes earlier and the destruction of the tyre.
- The ripping out of a large piece of tank in a complex process of transmission of the energy produced by the impact of a piece of tyre at another point on the tank, this transmission associating deformation of the tank skin and the movement of the fuel, with perhaps the contributory effect of other more minor shocks and /or a hydrodynamic pressure surge.
- Ignition of the leaking fuel by an electric arc in the landing gear bay or through contact with the hot parts of the engine with forward propagation of the flame causing a very large fire under the aircraft's wing and severe loss of thrust on engine 2 then engine 1.
In addition, the impossibility of retracting the landing gear probably contributed to the retention and stabilization of the flame throughout the flight.
Complete Air France Flight 4590 Accident Report
Investigators issued recommendations in three separate areas: Preliminary Recommendations; Recommendations Specific to the Concorde; and General Recommendations. These three areas are:
Preliminary Recommendations
On 16 August 2000 (less than one month following the accident), a joint set of Preliminary Recommendations were issued by both the French BEA, and British AAIB. For clarification, the Concorde accident investigation was headed by the BEA, with support from the AAIB. The jointly issued Preliminary Recommendations concerned two basic areas:
(1) To recommend that the Certificates of Airworthiness for the Concorde be suspended until additional safety measures could be identified and taken; and
(2) To identify and accomplish certain additional safety measures to be taken in order to reduce the risks of further Concorde tank failures and fires.
The recommendations to suspend the Airworthiness Certificates of the Concorde by both the French civil aviation authority (DGAC), and the British civil aviation authority (CAA) were immediately accepted, and individual certificates of all Concorde aircraft were suspended.
View Preliminary Recommendations.
Recommendations Specific to Concorde
Investigators issued four recommendations specific to the Concorde and identified them as related to steps to be taken in order for the airplane to be returned to service. These involved general safety information flow, details of flight data recorders, consistency of flight manual emergency procedures, and specific safety audit programs to be undertaken.
These four recommendations can be viewed at Recommendations Specific to Concorde.
General Recommendations
Investigators identified nine additional recommendations that went beyond specific recommendations for the Concorde. These nine general recommendations concerned areas ranging from improved aviation tire standards, airport runway debris prevention programs, flight simulator improvements, FAA audit of Continental Airlines maintenance programs, among several other recommendations.
View the nine General Recommendations.

Fuel Tank Integrity from Impact Threats
At the time of the development and certification of the Concorde in the 1970s, there were no large transport airplane fuel tank impact structural requirements from the threat posed by tire failure debris. Tire failures from various causes were not uncommon, but large fuel tank breaches/fires were generally not resulting from these failures experienced on aircraft operating in the commercial fleet. However, in 1985, a Boeing 737-200 operated by British Airtours experienced a catastrophic fuel tank breach on takeoff from Manchester, England. This accident became the catalyst for expanding both FAA and JAA requirements for protection from hazardous fuel tank leakages due to both tire debris impact as well as low energy engine debris impact of fuel access covers.
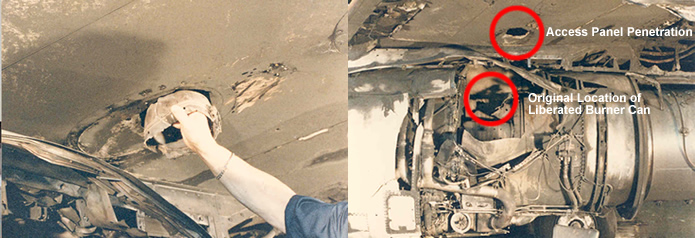
The Manchester 737 accident was the result of an uncontained engine failure on takeoff, where relatively low energy engine fragments penetrated a fuel tank access cover on the underside of the wing near the engine, causing a massive fuel leak and fire. As a result, vulnerable fuel tank access covers were subsequently required to be impact resistant (tire and low energy engine debris) for all aircraft being certified beginning in the late 1980s. In addition, all large transport aircraft operating in commercial service were required to have improved access covers beginning in the early 1990s. The focus of these fuel tank regulatory revisions was fuel tank access covers in vulnerable areas, not the entire wing surface, as it was generally believed at the time that the areas around the access covers were robust, and not subject to penetration and failure from debris. Therefore, protection of the overall tank surface from penetration was not included in the rule revisions (see "Resulting Safety Initiatives" contained within the British Airtours 737 module within this accident library).
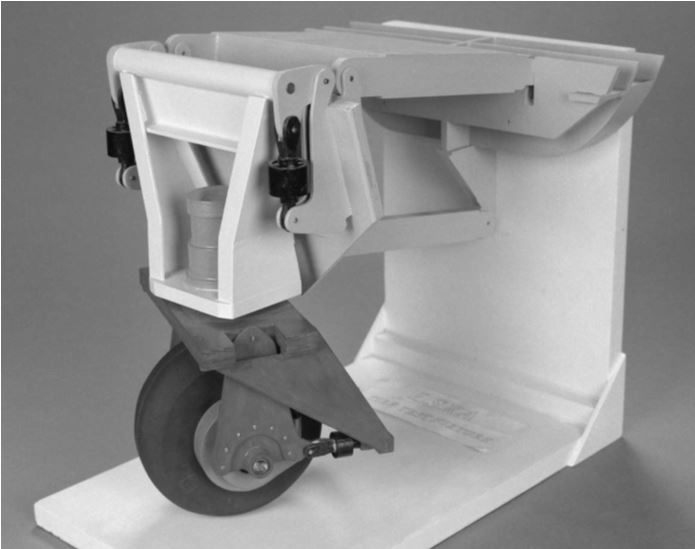
NASA Dryden Flight Research Center
Tire Integrity from Runway Debris
At the time of the Concorde development and certification, aviation tires were required to meet the design, performance, and manufacturing criteria contained in Technical Standard Order (TSO) C-62. The Dunlop tires installed on Flight 4590 met these standards at the time of the accident. However, threats posed by the sheet metal debris believed by investigators to have caused failure of Concorde's #2 tire were not part of criteria contained in TSO C-62. Standards called out in this material generally focus on the speed, weight, and environmental ratings of the tire, and not impact resistance to runway debris. The capability to withstand contact with runway debris (sheet metal, other objects) without failure continues to represent conditions outside of current performance requirements for aviation tires, as detailed in TSO C-62.
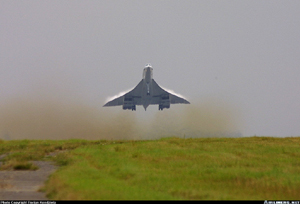
Photo copyright Florian Kondziela - used with permission
Development of the Concorde in the early 1970s was at a time in the evolution of jet powered transport airplane history when significant advances in safety and environmental technologies, and requirements, were occurring. Issues such as takeoff and landing performance, airport noise, engine and fuel system emissions, and sonic booms were among some of the subjects being discussed, and debated, across the international aviation community. In addition, subsonic jet powered commercial aircraft such as the Boeing 727, 737, 747; Douglas DC-9, DC-10; and Lockheed L-1011 were becoming increasingly popular, and had largely replaced piston and early jet powered aircraft of the 1950s and 60s.
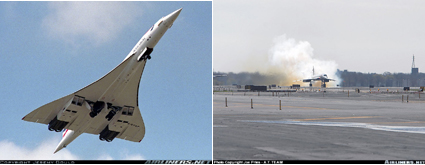
Photo copyright Jeremy Gould - used with permission
Concorde during takeoff roll (right)
Photo copyright Joe Pries A. T. Team - used with permission
This was also a period when significant increases in the number of overall worldwide airport operations were occurring. These rapid increases in aviation traffic had also resulted in specific environmental concerns being raised, especially in the areas of noise and emissions. These concerns were the focus of increasingly demanding regulatory requirements, and a call for continued advances to be made in environmental areas across all large commercial transport airplane types.
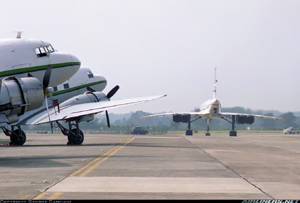
Photo copyright George Canciani - used with permission
With widespread public expectations for continued improvements to be made in environmental areas, the relatively high operational noise levels of the Concorde, and the sonic booms related to supersonic flight, significant design and regulatory challenges existed. As a result of these unique characteristics, special SST design and operational regulations were created in the early 1970s. In some cases, local regulators banned SST operations all together, while other authorities developed unique criteria intended to accommodate the SST airplane and its operation on a limited basis.
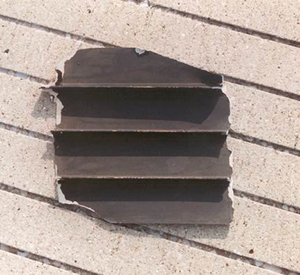
Tire failure leading to massive fuel tank breach
In the first few years of Concorde's service experience, previous tire failures had damaged the Concorde fuel tanks, and in a few cases, penetrations by small debris had led to relatively small fuel leaks. However, there had never been a failure in commercial aviation of this magnitude, involving a large section of the tank bottom completely failing.
Repeated failure of minor engine repair
The sheet metal debris liberated from the DC-10 that had taken off five minutes earlier had been installed in an area that had been repaired multiple times. The repair was found to have been accomplished in a manner inconsistent with manufacturer's recommendations. The sheet metal that the Concorde's #2 tire struck had evidence of multiple drilling operations and was of a material different than called out in the manufacturer's repair instructions.
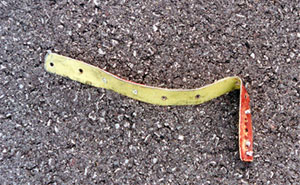
Tire failure threat to fuel tank
Previous Concorde tire failures had occurred, and several safety initiatives had been undertaken in order to reduce the hazards to the aircraft. However, none of the previous failures had resulted in large tank openings and massive fuel leaks such as occurred on Flight 4590. It was not until post-accident testing and analysis revealed details of the Concorde's complex failure mechanism that a full understanding of the tank failure dynamics became known.
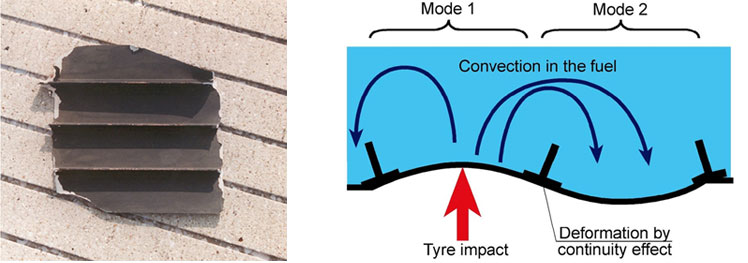
Failure of minor engine repair leading to damage to other aircraft
Liberation of a relatively small part is usually not assumed to result in catastrophic damage to other aircraft, as was found to have been the case in this accident.
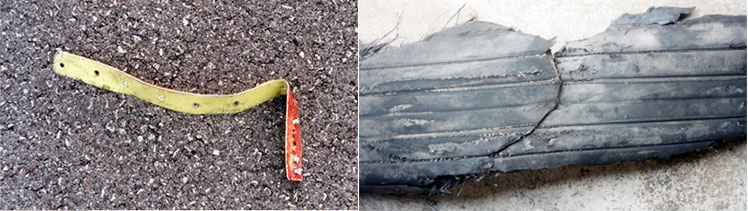
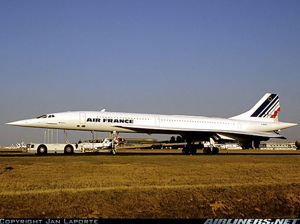
Copyright Jan LaPorte - used with permission
As investigators learned that the chain of events leading up to the crash of Flight 4590 involved failure of the #2 tire, service records of previous tire and wheel failures for the Concorde fleet were collected and analyzed. Fifty-seven cases of tire bursts/deflations were identified. Of these, no cases involving large segments of tank failures, such as observed on Flight 4590 were found. The most serious in-service incident among the six tank penetrations that were recorded occurred on June 14, 1979, involving aircraft F-BVSC on takeoff from Dulles International Airport, near Washington, DC.
It was learned that on this 6/14/79 flight, the #6 tire failed on take-off, liberating large segments of tire debris, and leading to failure of the adjacent #5 tire, due to overload. This then resulted in the aircraft rolling on the #5 and #6 wheels, causing them to fail, liberating debris which impacted the wing. Most of the structural damage resulted from impacts from pieces of #5 wheel rim on the wing, aft of the tires. Penetrations were also observed on fuel tanks #2, #5, and #6. One of the tank penetrations was determined to be the result of a piece of tire debris, the remainder being a result of debris from the #5 wheel, or other small debris from the airplane in the area of the main landing gear. The resulting fuel leakage rate from the three tank penetrations was estimated to be 4 kg/s. The fuel leak rate on Flight 4590 was estimated by investigators to be approximately 60 kg/s. No fire was reported on the 6/14/79 Dulles incident.
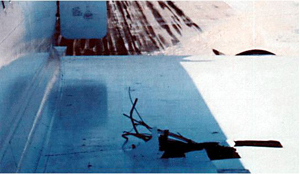
due to penetration from #5 wheel debris
Following the 6/14/79 Dulles incident, extensive review of Concorde tire and wheel service experience was conducted. In order to improve tire and wheel reliabilities, several key safety enhancements were identified and introduced into the Concorde fleet by Airworthiness Directive actions. Included in these improvements were (1) installation of a tire under-inflation pressure detection system; (2) installation of main landing gear tires and wheels with improved structural capability, among several other improvements. Service experience of the Concorde fleet in the years following introduction of these improvements showed significant reduction in the rates of tire and wheel failure occurrences. All of these safety enhancements had been incorporated into the Air France Flight 4590 accident airplane.
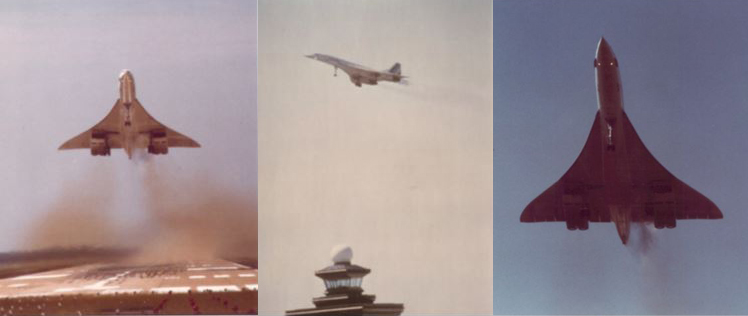
As a result of the 2000 Concorde accident in Paris, both the European Aviation Safety Agency (EASA) and the Federal Aviation Administration (FAA) issued new and/or revised safety requirements intended to address the unique fuel tank failure mechanism experienced on Flight 4590:
European Aviation Safety Agency
EASA issued Certification Specifications for Large Aeroplanes, CS-25, Amendment 14, in 2014 to include:
New:
CS-25.734 "Protection against Wheel and Tyre Failures"
The safe operation of the aeroplane must be preserved in case of damaging effects on systems or structures from:
- tyre debris;
- tyre burst pressure;
- flailing tyre strip; and
- wheel flange debris.
Revised:
CS-25.963(e) "Fuel Tank Protection"
This AMC sets forth a means of compliance with the provisions of CS-25 dealing with the certification requirements for fuel tanks (including skin and fuel tank access covers) on large aeroplanes. Guidance information is provided for showing compliance with the impact and fire resistance requirements of CS 25.963(e).
To view the revisions in their entirety: CS-25 Amendment 14
This revised rule deleted reference to Fuel Tank Access Covers, which had been the focus of the original rule (reference the 1985 B737-200 accident in Manchester, England), and expanded the area to be protected from expected debris impact to include the entire tank surface.
Federal Aviation Administration
The FAA issued special conditions for the Boeing Model 787, and the Airbus Model A350, both incorporating unique composite wing structure forming the fuel tank surfaces in the areas near the wheels, tires, and engines.
Boeing Model B787
Special Conditions: Boeing Model 787– 8 Airplane; Tire Debris Penetration of Fuel Tank Structure
These special conditions are issued for the Boeing Model 787–8 airplane. This airplane will have novel or unusual design features when compared to the state of technology envisioned in the airworthiness standards for transport category airplanes. These novel or unusual design features include wing fuel tanks constructed of carbon fiber composite materials. For these design features, the applicable airworthiness regulations do not contain adequate or appropriate safety standards. These special conditions contain the additional safety standards that the Administrator considers necessary to establish a level of safety equivalent to that established by the existing standards. Additional special conditions will be issued for other novel or unusual design features of the Boeing Model 787–8 airplanes.
Airbus Model A350
This action proposes special conditions for the Airbus Model A350– 900 series airplanes. These airplanes will have a novel or unusual design feature associated with fuel tanks constructed of carbon fiber reinforced plastic (CFRP) materials located within the tire impact zone, including the wing fuel tanks.
As investigators learned that the #5 tank failure was a result of a single tire failure, in mid-August a decision was made by both the French and UK civil aviation authorities to suspend all revenue flights of the Concorde until a more thorough understanding of the cause of the accident was identified, and corrective actions established and implemented. On August 16, 2000, the French DGAC and British CAA withdrew the Airworthiness Certificates of all Concordes that were in service in both countries. At that time, there were five Concordes operated by Air France (including the accident aircraft), and seven operated by British Airways.
Following a year-long investigation, Airworthiness Directives were issued in Early September 2001 by both the DGAC and CAA that required improvements in three main areas prior to the Concorde returning to service:
Fuel Tank Structural Integrity
It was learned that the outward openings in the #5 fuel tank bottom was the result of it being struck by high-speed, high-energy debris from the #2 tire. The outward openings allowed an extremely high-rate fuel leak to occur. Once ignited, believed by investigators to most likely be from electrical arcing in the wheel well area, the fire resulted in catastrophic damage to the airplane. In order to reduce the flow rate of the fuel in the case of future tank failures, Kevlar liners were installed in tank bottom areas in specific tank locations determined to be most vulnerable to tire debris, or other debris associated with runway operations.

View Larger
Improved Main Landing Gear Tires
Failure of the #2 tire involved liberation of large pieces of tire material: the largest recovered being approximately 4.5 kg. It was believed that in order to minimize the amount of energy being transmitted into the tank bottom surface following tire failure, a tire that "fragmented" into smaller pieces upon failure would help reduce the amount of deformation being experienced by the tank bottom structure. Therefore, a new tire configuration, identified as “Near Zero Growth” (NZG) was developed by Michelin, and was required by authorities to be installed on all 8 main landing gear locations. Testing performed by the tire manufacturer established that the new NZG tire had an improved tire structure that was more resistant to sudden, and complete failure, and that if punctured or cut, would result in the release of smaller pieces of tire tread
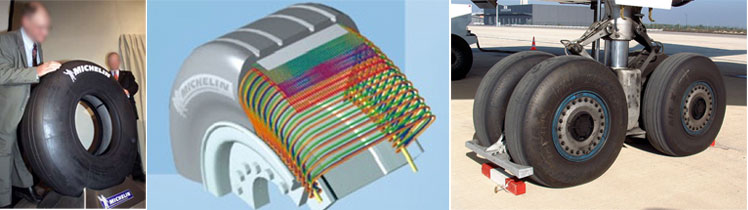
Landing Gear Electrical Harness Protection
Although investigators were not able to precisely determine the origin of ignition of the leaking fuel from the #5 fuel tank, if was generally believed to have been the result of electrical arcing from damaged electrical wires in the wheel well area. In order to reduce the risk of electrical arcing following tire failures, or other causes of harness damage, improvements were made to the wire runs in these areas. Woven stainless steel braiding was added to several areas of the harnesses associated with the landing gear control circuits in the areas adjacent to the main landing gear.
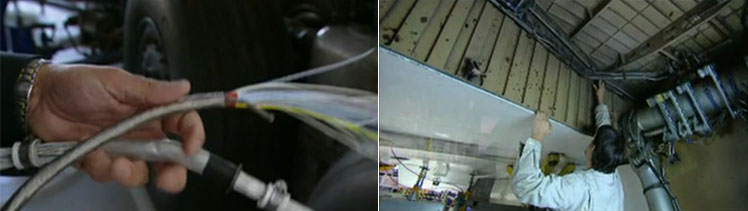
Airworthiness Directive issued by France for the Concorde (French version)
Airworthiness Directive issued by UK for the Concorde
Airplane Life Cycle:
- Design / Manufacturing
- Maintenance / Repair / Alteration
Accident Threat Categories:
- Structural Failure
- Uncontrolled Fire / Smoke
Groupings:
-
N/A
Accident Common Themes:
- Organizational Lapses
- Flawed Assumptions
Flawed Assumptions
Within the first few years of service, the Concorde fleet had experienced a relatively high rate of tire failures, and associated airplane damage. The most serious of these incidents occurred on June 14, 1979, during takeoff from Dulles International Airport. In this incident, a dual tire failure occurred, followed by a wheel failure that resulted in significant damage to the left wing, including debris that penetrated several fuel tanks.
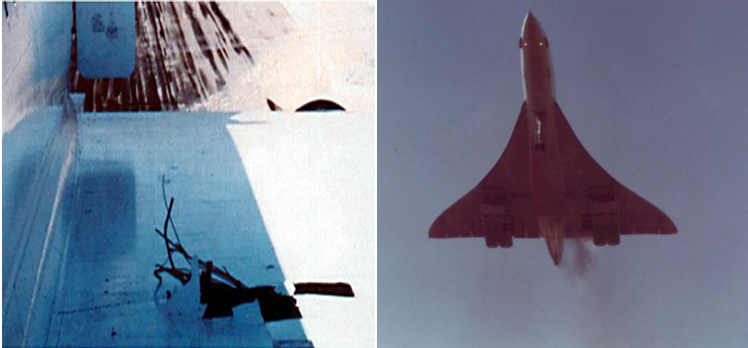
Photo of fuel leaking from Concorde's left wing on take-off from Dulles International Airport, June 14, 1979 (right)
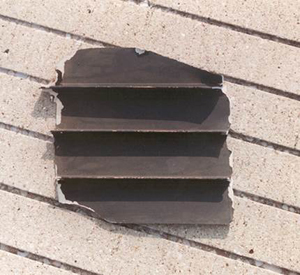
on July 25, 2000
Of the 57 tire failure/deflation events that the investigators studied, the Dulles incident was the only one where a piece of tire tread was found to have penetrated a fuel tank. In the early 1980s, several safety enhancements were implemented into the Concorde fleet intended to improve tire reliabilities and reduce the risk of wheel failure. In the nearly 20 years that followed, substantial improvements in the rates of tire failures were observed.
As a result of substantial improvements in tire reliabilities, it was generally assumed that the risks associated with tire failures had been adequately mitigated. A tank failure similar to that of Flight 4590 had never been observed in civil aviation, involving a piece of tire debris causing large fuel tank openings, and a massive fuel leak.
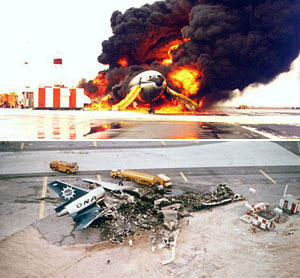
Overseas National Airways Flight 032, DC-10-30
Location: John F. Kennedy International Airport, New York
Date: November 12, 1975
At approximately 1310 Eastern Standard Time on November 12, 1975, Overseas National Airways (ONA) Flight 032, a McDonnell Douglas Model DC-10-30 airplane, crashed while attempting to take off from John F. Kennedy (JFK) International Airport, New York. During takeoff roll on runway 13R, the airplane struck a flock of sea gulls, causing the crew to perform a rejected takeoff. The number 3 engine and several tires and wheels disintegrated, and the landing gear collapsed. A resulting fuel leak led to an extensive ground fire which destroyed the airplane. Of the 128 passengers and 11 crewmembers on board, two people were seriously injured and 30 were slightly injured.
See accident module
British Airtours Flight KT28M, Boeing Model 737-236, G-BGJL
Location: Manchester International Airport, UK
Date: August 22, 1985
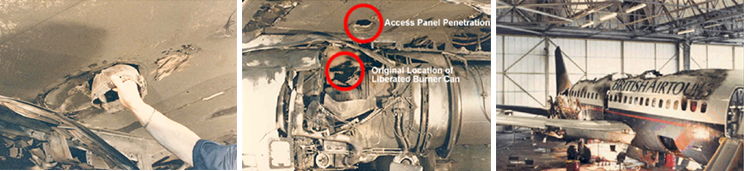
On August 22, 1985, British Airtours Flight KT28M, a Boeing Model 737-200 series airplane, was taking off from Runway 24 at Manchester International Airport, Manchester, UK, when the left engine experienced an engine failure. The flight crew aborted the takeoff and thinking the airplane had suffered from a tire burst, taxied the airplane clear of runway 24. In fact, a piece of the left engine combustor had penetrated a fuel-tank access panel, causing an uncontrollable fuel spill. The captain called for an evacuation; however, the fuel ignited and, accelerated by the adverse positioning of the airplane relative to the wind, the airplane was burned severely. Fifty-five passengers perished as a result. The British Civil Aviation Authority (CAA) determined the cause of the accident (fuel spill/ensuing fire) was an engine failure caused by faulty repairs; fragments from that engine failure penetrating a fuel-tank access door insufficiently constructed to withstand the impact from the failed engine pieces.
See accident module
Technical Related Lessons
Fuel tanks located in areas where tire failures are expected to occur should be capable of withstanding tire debris impact without resulting in hazardous fuel leakage. This should include protection from tank penetration, rupture, or the effects of deformation. (Threat Category: Structural Failure)
- Following introduction into service in 1976, the Concorde fleet began to experience a relatively high rate of tire failure events, and in some cases, resulting fuel tank damage. This damage included some instances of fuel tank penetration from debris, and several fuel leak events were reported. However, no fires were experienced, no massive fuel leaks were reported, and no engine thrust losses occurred.
-
In order to improve tire reliabilities, several safety initiatives were implemented into the Concorde fleet in the 1980s. Service records indicated that the rates of tire failures substantially improved throughout the late 1980s and 1990s, suggesting that the steps taken to reduce the risk of tire failures were having a positive effect. Although the rates of failures had improved, failures were still occurring.
-
Tire failures can occur for many reasons, including failures caused by runway debris as experience by Air France Flight 4590. Also, fuel tank breaches, even relatively minor breaches, pose a significant threat to the airplane. Therefore, fuel tanks in areas where tire failure debris impacts are expected to occur should be robust and have the capability to withstand impact from tire debris without resulting in penetration, or rupture caused by deformation.
Fuel tank breaches, especially those resulting in massive fuel leaks, represent a very significant risk of catastrophic, uncontrolled fire. (Threat Category: Uncontrolled Fire/Smoke)
- Service experience of many aircraft types where uncontrolled, unrestricted loss of fuel has occurred has identified numerous cases where catastrophic fires have resulted. In some cases, specific areas of the airplane, such as engine fire zones, are designed to direct leaking fuel into drainage paths, or areas where a safe discharge overboard has been established. However, leakage from the entire fuel tank area is not able to be shown to discharge in a predictable manner, and ignition sources from hot surfaces such as airplane brakes, or engine tail pipes, are nearly always present. Therefore, tank breaches, even relatively small breaches that are not able to be controlled, have the potential to eventually communicate with ignition sources, and an uncontrolled fire can result. Either in-flight fires such as occurred on Flight 4590, or ground fires, can quickly consume airplane systems or structures, resulting in a catastrophic outcome.
Common Theme Related Lessons
A repair should be accomplished with the expectation that the repaired part or system will provide a reasonable degree of capability and reliability. If it is determined that a repair procedure does not provide the desired level of reliability, then additional measures should be employed intended to achieve acceptable reliability, including consultation with manufacturers' maintenance instructions. (Common Theme Category: Organizational Lapse)
- Review of maintenance records for the DC-10 that took off five minutes ahead of Flight 4590 showed that the #3 engine thrust reverser wear strip had been replaced in June 2000, and again in July 2000. The reason for the second wear strip replacement was determined to be that the wear strip installed in June, upon airplane inspection, was observed to have been twisted, and was extending out from the reverser cowl. Examination of the DC-10 reverser found 37 holes had been drilled into the base material of the reverser, while the strip that was found on the runway contained 12 holes. It was concluded by investigators that there had been repeated work done to this area of the reverser, and a significant amount of drilling and wear strip replacement appeared to have taken place. Also, it was concluded by investigators that manufacturer's maintenance instructions for this area differed from the maintenance that had actually been performed.